- お役立ち記事
- How to deal with raw material price fluctuation risks faced by purchasing departments
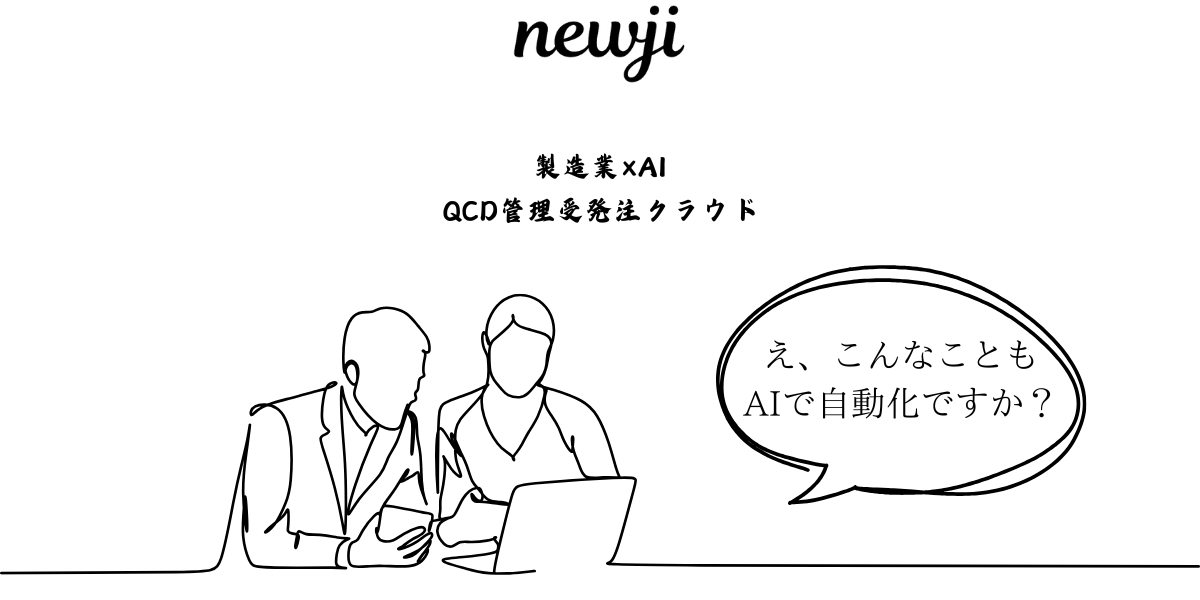
How to deal with raw material price fluctuation risks faced by purchasing departments
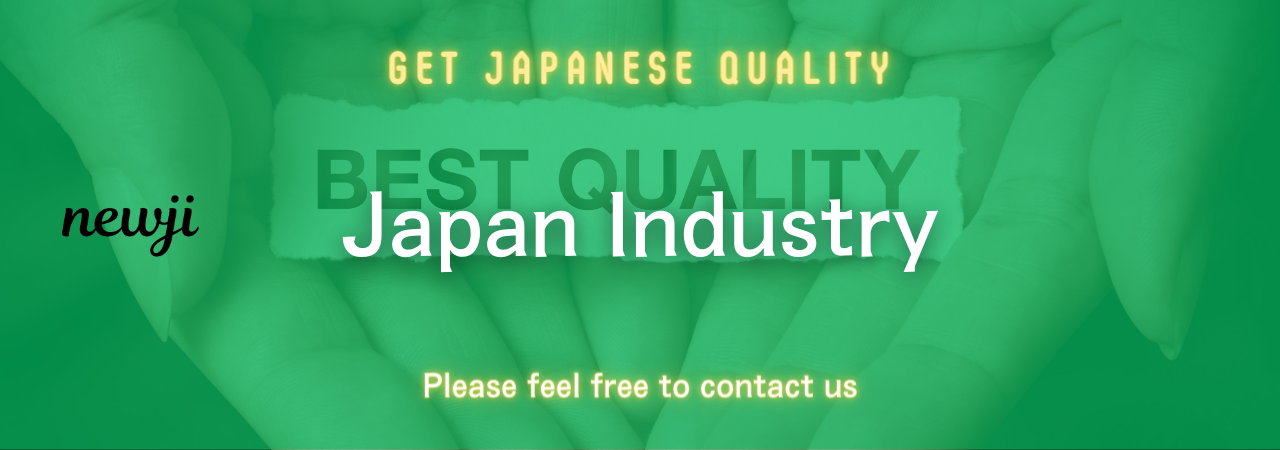
目次
Understanding Raw Material Price Fluctuations
Raw material price fluctuation is a significant challenge that purchasing departments face regularly.
These fluctuations can affect the cost of goods sold, profit margins, and overall business operations.
By understanding the causes and implications of these fluctuations, companies can better prepare and mitigate risks.
Several factors can contribute to raw material price changes.
These include supply chain disruptions, geopolitical events, natural disasters, and changes in consumer demand.
Additionally, economic policies, monetary fluctuations, and seasonal variations play a role.
Recognizing these factors helps anticipate changes and formulate strategies to cope with potential risks.
Strategies for Managing Price Fluctuation Risks
To effectively manage the risks associated with raw material price volatility, purchasing departments can implement robust strategies.
1. Diversifying Suppliers
One effective approach is to diversify the supplier base.
Relying on a single supplier can increase the risk of price spikes if that supplier experiences disruptions.
By having multiple suppliers, companies can negotiate better prices and ensure a steady supply, even in the face of market volatility.
2. Long-term Contracts and Agreements
Entering into long-term contracts with suppliers can offer price stability.
These agreements often include predetermined pricing, ensuring that companies are less affected by sudden market changes.
However, it’s essential to carefully assess these contracts to avoid overpaying when market prices decline.
3. Hedging Strategies
Hedging can be a powerful tool to manage price risks.
Financial instruments like futures contracts allow companies to lock in prices for future procurement.
This strategy provides certainty and helps in shielding against adverse price movements.
4. Inventory Management
Effective inventory management is crucial in dealing with price fluctuations.
By maintaining optimal inventory levels, companies can purchase raw materials when prices are favorable and avoid rushed buying during price hikes.
This approach requires accurate demand forecasting and storage capacity planning.
5. Cost Pass-Through
In some cases, businesses can pass on increased raw material costs to customers.
This strategy involves adjusting the pricing of end products to reflect higher input costs.
While this may not always be feasible in highly competitive markets, it remains a viable option in certain industries.
The Role of Technology in Risk Management
Technology plays a pivotal role in managing raw material price fluctuation risks.
By leveraging advanced tools, companies can enhance their decision-making processes and minimize potential impacts.
1. Data Analytics and Predictive Modeling
Data analytics enables businesses to gain insights into market trends and anticipate price movements.
Predictive modeling tools can forecast future price changes based on historical data, allowing purchasing departments to make informed decisions about timing and sourcing.
2. Automation and Real-time Monitoring
Automation tools facilitate real-time monitoring of market conditions and supply chain dynamics.
With instant alerts on price changes and supply disruptions, purchasing departments can swiftly respond and adapt their strategies accordingly.
3. Blockchain for Transparency and Traceability
Blockchain technology enhances transparency and traceability in supply chains.
By recording transactions and supply chain movements on a secure ledger, companies can track raw material sources and ensure compliance with ethical standards.
This also aids in verifying claims related to sustainable and fair trade practices.
Fostering Collaboration Across Departments
Managing raw material price fluctuation risks is not solely the responsibility of the purchasing department.
It requires collaboration across various departments to develop a comprehensive risk management approach.
1. Finance and Budgeting
The finance department plays a crucial role in budgeting and allocating funds for raw material procurement.
By working closely with purchasing departments, finance can ensure that budgets are aligned with market conditions and risk management strategies.
2. Operations and Production
The operations team must coordinate with purchasing to ensure that production schedules align with raw material availability.
Adjusting production timelines based on material costs can help optimize overall profitability.
3. Sales and Marketing
Sales and marketing teams need to be informed about cost adjustments in raw materials.
This knowledge enables them to develop pricing strategies and communicate value propositions to customers effectively.
Conclusion
Managing the risks associated with raw material price fluctuations is an ongoing challenge for purchasing departments.
By employing a combination of strategic approaches, technological tools, and cross-departmental collaboration, companies can effectively navigate these fluctuations.
Ultimately, this leads to greater resilience, sustained profitability, and a competitive edge in the market. \
Proactively addressing these challenges ensures that businesses remain adaptable and robust in an ever-changing economic landscape.
資料ダウンロード
QCD調達購買管理クラウド「newji」は、調達購買部門で必要なQCD管理全てを備えた、現場特化型兼クラウド型の今世紀最高の購買管理システムとなります。
ユーザー登録
調達購買業務の効率化だけでなく、システムを導入することで、コスト削減や製品・資材のステータス可視化のほか、属人化していた購買情報の共有化による内部不正防止や統制にも役立ちます。
NEWJI DX
製造業に特化したデジタルトランスフォーメーション(DX)の実現を目指す請負開発型のコンサルティングサービスです。AI、iPaaS、および先端の技術を駆使して、製造プロセスの効率化、業務効率化、チームワーク強化、コスト削減、品質向上を実現します。このサービスは、製造業の課題を深く理解し、それに対する最適なデジタルソリューションを提供することで、企業が持続的な成長とイノベーションを達成できるようサポートします。
オンライン講座
製造業、主に購買・調達部門にお勤めの方々に向けた情報を配信しております。
新任の方やベテランの方、管理職を対象とした幅広いコンテンツをご用意しております。
お問い合わせ
コストダウンが利益に直結する術だと理解していても、なかなか前に進めることができない状況。そんな時は、newjiのコストダウン自動化機能で大きく利益貢献しよう!
(Β版非公開)