- お役立ち記事
- How to deal with the “number” and “time” barriers of reliability testing
月間76,176名の
製造業ご担当者様が閲覧しています*
*2025年3月31日現在のGoogle Analyticsのデータより
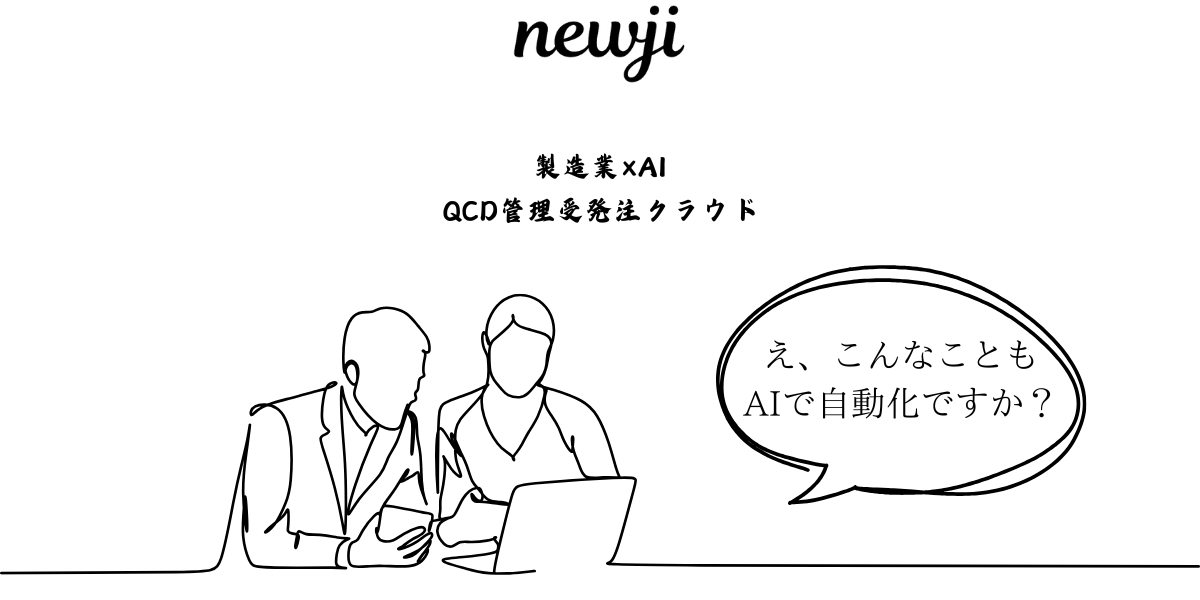
How to deal with the “number” and “time” barriers of reliability testing
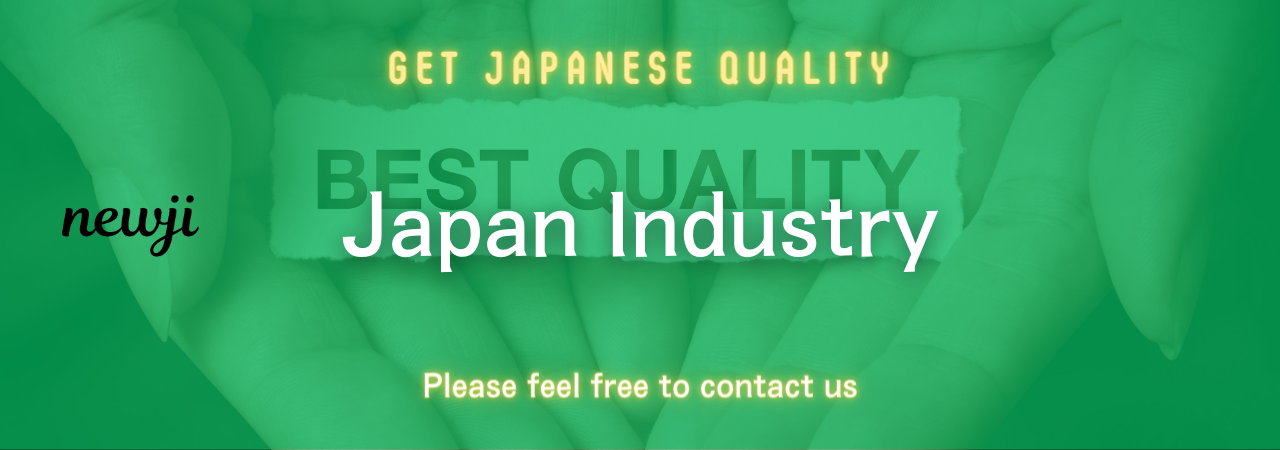
目次
Understanding Reliability Testing
Reliability testing is a crucial process in product development and quality assurance.
It ensures a product will perform consistently under specified conditions for a certain period of time.
This testing helps identify potential failures and defects, which can save companies time and money by addressing issues before products reach the market.
However, two significant barriers to effective reliability testing are the “number” and “time” barriers.
The “Number” Barrier in Reliability Testing
The “number” barrier refers to the challenge of determining how many samples of a product are needed to obtain statistically significant reliability test results.
Testing too few products can result in data that does not accurately represent the entire production batch, leading to misguided conclusions or missed defects.
On the other hand, testing too many products can be costly and inefficient.
Statistical methods, such as the Weibull distribution, help overcome the number barrier by modeling life data to predict failures and their probabilities.
These methods allow engineers to calculate the minimum sample size needed to achieve a certain confidence level about a product’s reliability.
Employing advanced analytical techniques also aid in optimizing sample sizes.
For instance, the use of Design of Experiments (DOE) can reduce the number of tests needed by studying multiple variables simultaneously.
This technique ensures robust data collection with fewer samples, ultimately balancing cost and accuracy.
The “Time” Barrier in Reliability Testing
Time is another crucial barrier in reliability testing since real-world use conditions often require long-term testing.
Waiting for products to naturally reach end-of-life to capture accurate reliability data is impractical due to time constraints.
To address the time barrier, accelerated life testing (ALT) is utilized.
This method speeds up the life cycle of a product by subjecting it to higher-than-normal levels of stress, such as increased temperature, pressure, or load.
The data collected from ALT can then be extrapolated back to normal use conditions using mathematical models.
This approach significantly shortens the testing time while providing insights into potential long-term reliability issues.
Environmental chambers are also employed to simulate extreme conditions quickly, providing valuable data over a condensed period.
These chambers help predict how products will perform over time in varying environmental conditions, such as humidity and temperature fluctuations.
Strategies to Overcome Barriers
There are several strategies that manufacturers and testing professionals can implement to cope with the challenges posed by the number and time barriers in reliability testing.
Increasing collaboration across different teams within an organization ensures a comprehensive approach to reliability testing.
Design engineers, quality assurance professionals, and statisticians all bring unique perspectives and expertise that can enhance testing efforts.
Working together allows these teams to devise optimized testing plans that effectively balance time, cost, and accuracy.
Investing in predictive maintenance technologies can also aid in overcoming these barriers.
By collecting and analyzing real-time data from products in the field, companies can predict when a product is likely to fail and plan maintenance accordingly.
This not only enhances reliability but provides valuable feedback for improving future product designs.
Lastly, incorporating automation in testing processes can expedite reliability testing and improve data accuracy.
Automated testing reduces human error, ensuring consistency, while freeing up resources to focus on more complex analysis and decision-making tasks.
Real-World Applications
Various industries, such as automotive, electronics, and medical device manufacturing, depend heavily on reliability testing due to the high stakes involved.
Failures in these sectors can result in significant financial loss, regulatory non-compliance, or even endanger human lives.
Automakers, for example, employ reliability testing to ensure their vehicles achieve a high safety standard and meet consumer expectations.
By conducting tests like fatigue testing on vehicle components, manufacturers can prevent system failures, thus improving customer satisfaction and brand reputation.
Similarly, in the electronics industry, reliability testing ensures devices can withstand daily wear and tear.
It’s crucial to test for resistance to shock, vibration, and varied temperatures to meet consumer demands for durable and long-lasting products.
In healthcare, medical devices undergo rigorous reliability testing to ensure they function effectively and safely in clinical settings.
This is vital as any failure could compromise patient safety and lead to severe consequences.
Conclusion
Reliability testing is critical in predicting product performance and identifying failure modes before reaching consumers.
Overcoming the “number” and “time” barriers requires strategic planning, research, and collaboration among various stakeholders involved in product development and testing processes.
By leveraging statistical methods, utilizing accelerated testing techniques, and embracing technological advancements, companies can enhance their reliability testing processes.
Doing so helps ensure that products remain reliable, meet industry standards, and exceed consumer expectations, ultimately leading to a successful market presence.
資料ダウンロード
QCD管理受発注クラウド「newji」は、受発注部門で必要なQCD管理全てを備えた、現場特化型兼クラウド型の今世紀最高の受発注管理システムとなります。
ユーザー登録
受発注業務の効率化だけでなく、システムを導入することで、コスト削減や製品・資材のステータス可視化のほか、属人化していた受発注情報の共有化による内部不正防止や統制にも役立ちます。
NEWJI DX
製造業に特化したデジタルトランスフォーメーション(DX)の実現を目指す請負開発型のコンサルティングサービスです。AI、iPaaS、および先端の技術を駆使して、製造プロセスの効率化、業務効率化、チームワーク強化、コスト削減、品質向上を実現します。このサービスは、製造業の課題を深く理解し、それに対する最適なデジタルソリューションを提供することで、企業が持続的な成長とイノベーションを達成できるようサポートします。
製造業ニュース解説
製造業、主に購買・調達部門にお勤めの方々に向けた情報を配信しております。
新任の方やベテランの方、管理職を対象とした幅広いコンテンツをご用意しております。
お問い合わせ
コストダウンが利益に直結する術だと理解していても、なかなか前に進めることができない状況。そんな時は、newjiのコストダウン自動化機能で大きく利益貢献しよう!
(β版非公開)