- お役立ち記事
- How to develop and implement procurement strategies in the manufacturing industry
How to develop and implement procurement strategies in the manufacturing industry
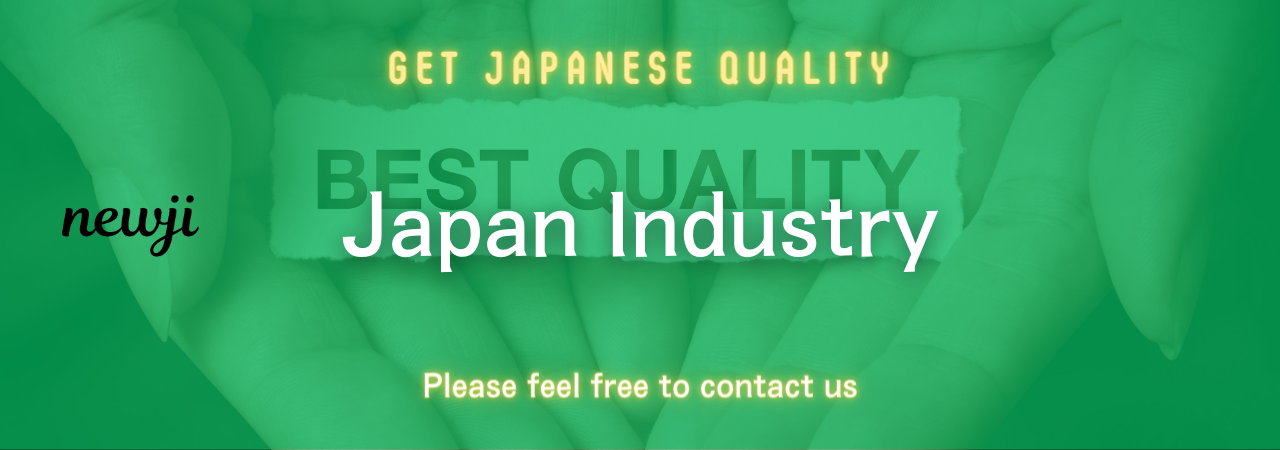
Procurement strategies play a crucial role in the manufacturing industry.
They help in cost reduction, improving product quality, and ensuring timely delivery of materials.
Developing and implementing effective procurement strategies requires a systematic approach.
In this article, we’ll delve into the necessary steps and best practices for successful procurement in the manufacturing sector.
目次
Understanding Procurement in Manufacturing
Procurement involves sourcing and acquiring the raw materials and components needed for production.
In the manufacturing industry, this process is pivotal as it directly impacts production schedules, costs, and product quality.
To develop a robust procurement strategy, you first need to understand the key aspects of procurement.
Key Components of Procurement
Procurement in manufacturing encompasses several components:
– **Supplier Selection**: Identifying and selecting suppliers who can meet your requirements.
– **Cost Management**: Negotiating prices and ensuring cost-effectiveness.
– **Quality Assurance**: Ensuring that materials meet quality standards.
– **Risk Management**: Identifying and mitigating risks associated with supply chain disruptions.
Understanding these components helps lay the foundation for an effective procurement strategy.
Steps to Develop Procurement Strategies
Developing a procurement strategy involves a series of steps.
Each step should be carried out meticulously to ensure the strategy’s success.
1. Analyze Your Needs
Begin by analyzing your production needs.
Identify the materials, components, and services required for manufacturing.
Understanding your needs helps in creating a procurement plan that aligns with your production goals.
2. Market Research
Conduct thorough market research to identify potential suppliers.
Assess the market conditions, pricing trends, and supply chain dynamics.
Market research provides insights that are crucial for negotiating contracts and relationships with suppliers.
3. Supplier Evaluation and Selection
Evaluate potential suppliers based on their reliability, quality, and cost.
It’s important to consider factors such as supplier reputation, delivery times, and financial stability.
Select suppliers who can consistently meet your demands and maintain quality standards.
4. Cost Analysis
Perform a cost analysis to understand the total cost of ownership.
This includes the purchase price, transportation costs, storage costs, and any other associated costs.
A detailed cost analysis helps in budget planning and cost control.
5. Risk Assessment
Identify potential risks in your supply chain.
These could include supplier insolvency, geopolitical issues, or natural disasters.
Develop risk mitigation strategies to ensure supply chain continuity in case of disruptions.
6. Develop Procurement Policies
Establish procurement policies that outline procedures for purchasing, supplier management, and contract negotiations.
These policies should align with your overall business objectives and compliance requirements.
7. Create a Procurement Plan
Draft a detailed procurement plan that includes timelines, budgets, and responsibilities.
This plan serves as a roadmap for implementing your procurement strategy.
Ensure that all relevant stakeholders are on board with the plan.
8. Implement and Monitor
Implement the procurement strategy according to the plan.
Monitor the procurement processes closely to ensure they are running smoothly.
Regular monitoring helps in identifying any issues early and making necessary adjustments.
Best Practices for Implementing Procurement Strategies
Effective implementation of procurement strategies requires adherence to best practices.
Here are some key practices to consider:
Build Strong Supplier Relationships
Cultivate strong relationships with your suppliers.
Regular communication, transparency, and mutual trust are essential for maintaining good supplier relationships.
Strong relationships can lead to better negotiation outcomes and smoother supply chain operations.
Use Technology
Leverage technology to streamline procurement processes.
Procurement software can help with supplier management, order tracking, and data analysis.
Technology enhances efficiency and provides valuable insights for decision-making.
Continuous Improvement
Adopt a culture of continuous improvement.
Regularly review and analyze your procurement processes to identify areas for improvement.
Encourage feedback from your team and suppliers to enhance efficiency and effectiveness.
Training and Development
Invest in training and development for your procurement team.
Ensure they are well-versed in the latest procurement trends, technologies, and best practices.
A knowledgeable team is better equipped to handle procurement challenges.
Sustainability and Ethics
Incorporate sustainability and ethics into your procurement strategy.
Select suppliers who adhere to environmental standards and ethical practices.
Sustainable and ethical procurement not only benefits society but also enhances your brand reputation.
Conclusion
Developing and implementing procurement strategies in the manufacturing industry is a complex process.
It requires careful planning, market research, supplier selection, and continuous monitoring.
By following the steps outlined in this article and adhering to best practices, manufacturers can develop effective procurement strategies that drive cost savings, improve product quality, and ensure timely delivery of materials.
In essence, a well-developed procurement strategy is a cornerstone of success in the manufacturing industry.
Whether you are a small manufacturer or a large enterprise, the principles of effective procurement remain the same.
Strategic procurement enhances operational efficiency and supports sustainable business growth.
資料ダウンロード
QCD調達購買管理クラウド「newji」は、調達購買部門で必要なQCD管理全てを備えた、現場特化型兼クラウド型の今世紀最高の購買管理システムとなります。
ユーザー登録
調達購買業務の効率化だけでなく、システムを導入することで、コスト削減や製品・資材のステータス可視化のほか、属人化していた購買情報の共有化による内部不正防止や統制にも役立ちます。
NEWJI DX
製造業に特化したデジタルトランスフォーメーション(DX)の実現を目指す請負開発型のコンサルティングサービスです。AI、iPaaS、および先端の技術を駆使して、製造プロセスの効率化、業務効率化、チームワーク強化、コスト削減、品質向上を実現します。このサービスは、製造業の課題を深く理解し、それに対する最適なデジタルソリューションを提供することで、企業が持続的な成長とイノベーションを達成できるようサポートします。
オンライン講座
製造業、主に購買・調達部門にお勤めの方々に向けた情報を配信しております。
新任の方やベテランの方、管理職を対象とした幅広いコンテンツをご用意しております。
お問い合わせ
コストダウンが利益に直結する術だと理解していても、なかなか前に進めることができない状況。そんな時は、newjiのコストダウン自動化機能で大きく利益貢献しよう!
(Β版非公開)