- お役立ち記事
- How to effectively conduct why-why analysis and key points to prevent recurrence
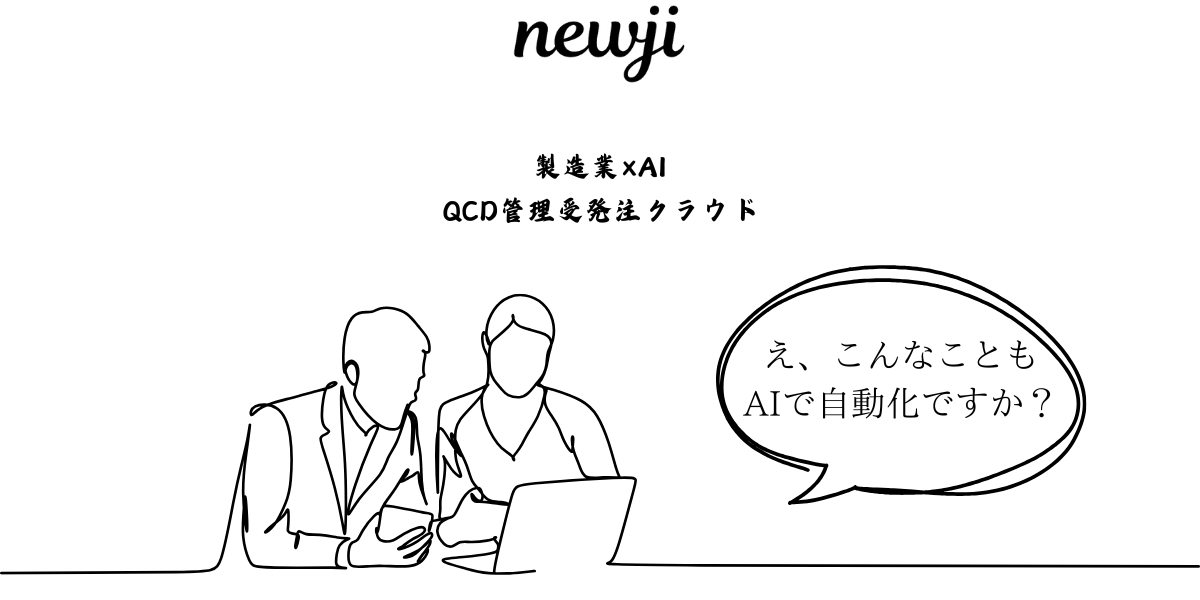
How to effectively conduct why-why analysis and key points to prevent recurrence
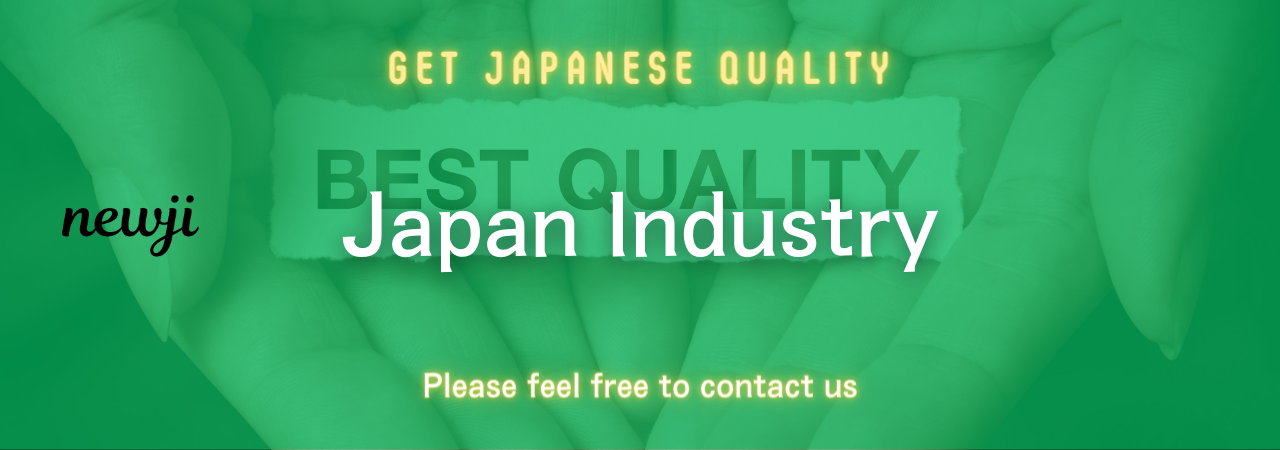
目次
Understanding Why-Why Analysis
Why-why analysis is a powerful problem-solving method used to identify the root cause of an issue.
This technique involves asking “why” repeatedly, typically five times, to delve deeper into the cause-and-effect relationships underlying a particular problem.
By doing this, you can trace the origin of a problem, understand its nature, and develop strategies to prevent it from happening again.
The core principle of why-why analysis is to transform a superficial understanding of a problem into a comprehensive insight.
Many organizations use this method due to its simplicity and effectiveness, making it accessible for anyone from frontline employees to senior managers.
Essentially, it helps in preventing future occurrences by addressing the root cause rather than just the symptoms.
Steps to Conduct Why-Why Analysis Effectively
Conducting a why-why analysis involves several steps.
Implementing these steps correctly ensures a thorough investigation and accurate identification of the root cause.
1. Clearly Define the Problem
Begin by clearly stating the problem you need to solve.
A well-defined problem sets the stage for a focused analysis.
Ensure that the problem statement is specific, measurable, and pertains to a single issue.
Instead of saying “production is slow,” specify the issue by saying “production time has increased by 20% in the past month.”
2. Assemble the Right Team
Gather a team with diverse expertise relevant to the problem area.
Having different perspectives can enrich the discussion and lead to more comprehensive answers.
Ensure that the team includes individuals who are directly involved with the process or issue being analyzed, as they can provide valuable insights.
3. Start the Inquiry Process
With the problem defined, start asking why it occurred.
After each answer, ask another why, and continue this process until you reach a root cause that is actionable.
The trick is to remain objective and refrain from assigning blame.
For instance, if an equipment breakdown caused production delays, ask why the equipment broke down.
Keep questioning until you arrive at a manageable and preventable issue.
4. Validate the Root Cause
Once you believe you’ve found the root cause, validate it through data collection and analysis.
Check to see if the cause you’ve identified is genuinely at the heart of the problem.
Validation ensures that you are addressing the correct issue and not merely a symptom.
5. Develop and Implement Solutions
After verifying the root cause, brainstorm potential solutions.
Choose the solution that is most feasible and has the greatest potential for preventing recurrence.
Ensure that the solution is implemented with the necessary resources and support.
This step might involve revising procedures, improving training, or investing in new technologies.
6. Monitor the Results
Continuously monitor the situation to check if the implemented solution is effective.
Adjust the approach if necessary.
Monitoring helps in understanding if the solution is sustainable in the long run.
Key Points to Prevent Recurrence
Preventing the recurrence of a problem is crucial to maintaining efficient operations.
Here are key points to ensure the issue does not recur:
1. Comprehensive Documentation
Document the entire process of the why-why analysis, from the problem statement to the solutions implemented.
Good documentation helps in creating a knowledge base for the organization, which can be referred to in future problem-solving efforts.
2. Foster a Culture of Problem-Solving
Encourage a culture that promotes proactive approaches to problem-solving.
Empower employees to participate in why-why analyses and support them in identifying and solving issues.
Training sessions on root cause analysis can enhance the problem-solving capabilities of your team.
3. Evaluate and Improve Continuously
Regularly review and assess the effectiveness of solutions and prevention strategies.
Improvements should be integrated into regular operations based on feedback and monitoring results.
A continuous evaluation approach will allow you to tweak the processes as necessary.
4. Implement Systematic Checks
Introduce systematic checks and balances as part of your processes.
These can include regular audits, maintenance schedules, and other preemptive measures to avoid recurrences.
Systematic checks ensure that issues are identified before they develop into serious problems.
Conclusion
Why-why analysis is an effective method to identify root causes and implement solutions that prevent recurrences.
By following a structured approach, including clear problem definitions, thorough investigations, validations, and continuous monitoring, organizations can reap the benefits of this technique.
It ultimately leads to improved efficiency, reduced risk of future issues, and a stronger, more resilient operational framework.
Empower your team through training and support to integrate why-why analysis effectively, fostering a workplace culture that values problem resolution and continuous improvement.
資料ダウンロード
QCD調達購買管理クラウド「newji」は、調達購買部門で必要なQCD管理全てを備えた、現場特化型兼クラウド型の今世紀最高の購買管理システムとなります。
ユーザー登録
調達購買業務の効率化だけでなく、システムを導入することで、コスト削減や製品・資材のステータス可視化のほか、属人化していた購買情報の共有化による内部不正防止や統制にも役立ちます。
NEWJI DX
製造業に特化したデジタルトランスフォーメーション(DX)の実現を目指す請負開発型のコンサルティングサービスです。AI、iPaaS、および先端の技術を駆使して、製造プロセスの効率化、業務効率化、チームワーク強化、コスト削減、品質向上を実現します。このサービスは、製造業の課題を深く理解し、それに対する最適なデジタルソリューションを提供することで、企業が持続的な成長とイノベーションを達成できるようサポートします。
オンライン講座
製造業、主に購買・調達部門にお勤めの方々に向けた情報を配信しております。
新任の方やベテランの方、管理職を対象とした幅広いコンテンツをご用意しております。
お問い合わせ
コストダウンが利益に直結する術だと理解していても、なかなか前に進めることができない状況。そんな時は、newjiのコストダウン自動化機能で大きく利益貢献しよう!
(Β版非公開)