- お役立ち記事
- How to effectively implement poka-yoke that team leaders in equipment maintenance departments should know
How to effectively implement poka-yoke that team leaders in equipment maintenance departments should know
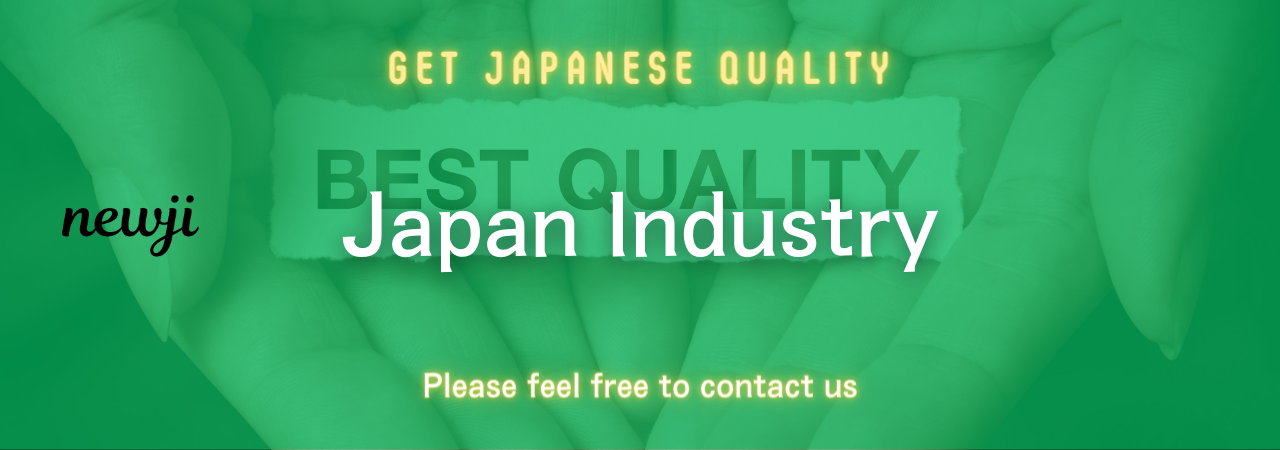
目次
Understanding Poka-Yoke
Poka-Yoke is a Japanese term that translates to “mistake-proofing” or “error prevention.”
It is a concept used to prevent errors in the manufacturing process.
Originally developed by Shigeo Shingo, a Japanese engineer, it focuses on designing processes and equipment in a way that mistakes are minimized, if not entirely eliminated.
In today’s competitive environment, operational efficiency has become paramount, and Poka-Yoke provides a practical solution for teams in equipment maintenance departments.
The Importance of Poka-Yoke in Maintenance
Implementing Poka-Yoke in equipment maintenance can dramatically reduce the number of errors that occur in day-to-day operations.
Mistakes in maintenance can lead to costly downtime, inefficient processes, and safety hazards.
Using Poka-Yoke can enhance productivity and ensure a higher standard of safety and quality.
Maintenance departments are critical to any manufacturing operation, and understanding how to implement Poka-Yoke effectively can lead to substantial improvements in performance and reliability.
Principles of Poka-Yoke
Poka-Yoke strategies are based on simple principles aiming to make errors impossible or to immediately detect them when they occur.
Error prevention is achieved through either of two approaches:
1. Control: the process is stopped automatically if an error is detected.
2. Warning: alerts are provided when errors are detected so corrective actions can be taken.
Control Methods
Control methods are typically seen as hard Poka-Yokes, directly preventing mistakes by designing processes or equipment that make errors impossible.
For example, using a machine that physically won’t start if parts are incorrectly loaded is a straightforward control method.
Warning Methods
Warning methods, or soft Poka-Yokes, involve signaling to workers when something goes wrong.
This could include warning lights, sounds, or messages that alert team members of the potential issue, allowing for quick corrections without halting production.
Steps to Implement Poka-Yoke
Implementing Poka-Yoke requires both strategic planning and practical execution.
Here are key steps team leaders should consider:
1. Identify the Problematic Areas
Start by analyzing the maintenance processes to identify areas where errors are prone.
Look for repetitive mistakes, common failure points, and sections of the operation prone to human error.
Understanding these patterns helps prioritize where Poka-Yoke techniques could be most beneficial.
2. Brainstorm Possible Solutions
Once the problematic areas are identified, employ creativity and innovation to brainstorm potential error-proofing solutions.
Involve the maintenance team in this process, as they are familiar with day-to-day operations and can offer valuable insights and practical ideas.
3. Design and Test Solutions
Design simple and easily implemented solutions based on the brainstormed ideas.
It’s crucial to test these solutions on a small scale to ensure they are effective without causing disruptions to the existing processes.
Feedback is essential here, so encourage team members to suggest improvements and modifications.
4. Implement and Monitor
After successful testing, roll out the Poka-Yoke solutions on a larger scale.
Continually monitor the processes to gauge the effectiveness of the implemented strategies.
It’s important to keep communication open among team members to promptly address any issues or unexpected outcomes.
5. Continuous Improvement
Poka-Yoke implementation is not a one-time activity but an ongoing effort.
Regularly review and refine processes to adapt to changing operations or new equipment.
Encouraging a culture of continuous improvement will help the department stay efficient, adapt to challenges more dynamically, and encourage team members to look for ways to further minimize errors.
Real-life Examples of Poka-Yoke
To better understand Poka-Yoke in action, consider these practical examples often seen in manufacturing and maintenance settings:
Color-Coded Tools
In many maintenance departments, tools are color-coded to match specific tasks or departments.
This simple method prevents using the wrong tools for a job and streamlines the work process.
Customized Jigs and Fixtures
Using specialized jigs and fixtures that only allow assembly if parts are aligned correctly is another effective example.
This approach eliminates errors in component alignment and assembly.
Error-proof Product Design
Designing products with unique shapes or sizes so they fit only in the correct position prevents improper assembly or installation.
For instance, incorporating asymmetrical features in components ensures they can only be installed in one orientation.
The Benefits of Poka-Yoke
The adoption of Poka-Yoke techniques can provide numerous advantages for equipment maintenance departments:
1. **Reduced Error Rates:** By preventing mistakes before they happen or catching them early in the process, the error rate is significantly reduced.
2. **Improved Safety:** Safety is enhanced as the likelihood of maintenance-related accidents due to errors decreases.
3. **Increased Productivity:** By reducing downtime caused by errors, overall productivity within the department is enhanced.
4. **Cost Savings:** Lower error rates and improved efficiency translate into cost savings over time.
5. **Enhanced Quality:** Products and services provided by your operation are consistently at a higher quality due to reduced errors in maintenance processes.
Conclusion
Poka-Yoke is a powerful tool for team leaders in equipment maintenance departments seeking to improve efficiency and reduce errors.
By understanding its principles and following a structured implementation plan, maintenance teams can foster environments of reliability and excellence.
Through the use of control and warning methods, ongoing monitoring, and commitment to continuous improvement, Poka-Yoke can transform maintenance operations into smooth and error-free processes.
資料ダウンロード
QCD調達購買管理クラウド「newji」は、調達購買部門で必要なQCD管理全てを備えた、現場特化型兼クラウド型の今世紀最高の購買管理システムとなります。
ユーザー登録
調達購買業務の効率化だけでなく、システムを導入することで、コスト削減や製品・資材のステータス可視化のほか、属人化していた購買情報の共有化による内部不正防止や統制にも役立ちます。
NEWJI DX
製造業に特化したデジタルトランスフォーメーション(DX)の実現を目指す請負開発型のコンサルティングサービスです。AI、iPaaS、および先端の技術を駆使して、製造プロセスの効率化、業務効率化、チームワーク強化、コスト削減、品質向上を実現します。このサービスは、製造業の課題を深く理解し、それに対する最適なデジタルソリューションを提供することで、企業が持続的な成長とイノベーションを達成できるようサポートします。
オンライン講座
製造業、主に購買・調達部門にお勤めの方々に向けた情報を配信しております。
新任の方やベテランの方、管理職を対象とした幅広いコンテンツをご用意しております。
お問い合わせ
コストダウンが利益に直結する術だと理解していても、なかなか前に進めることができない状況。そんな時は、newjiのコストダウン自動化機能で大きく利益貢献しよう!
(Β版非公開)