- お役立ち記事
- How to effectively proceed with DR based on FMEA and prevent quality troubles
月間76,176名の
製造業ご担当者様が閲覧しています*
*2025年3月31日現在のGoogle Analyticsのデータより
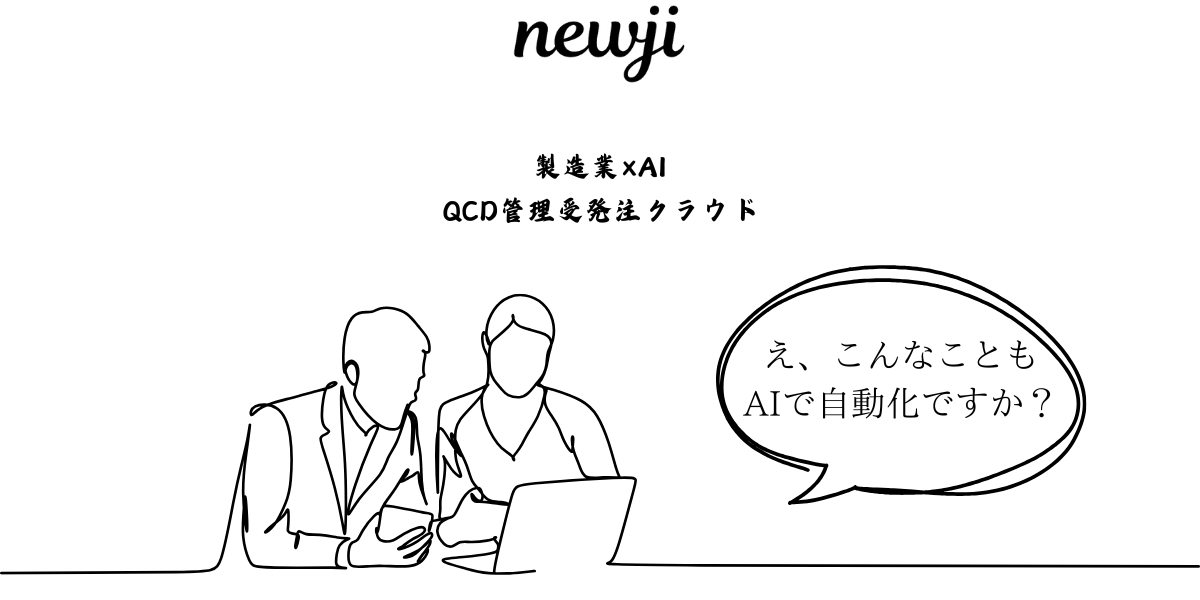
How to effectively proceed with DR based on FMEA and prevent quality troubles
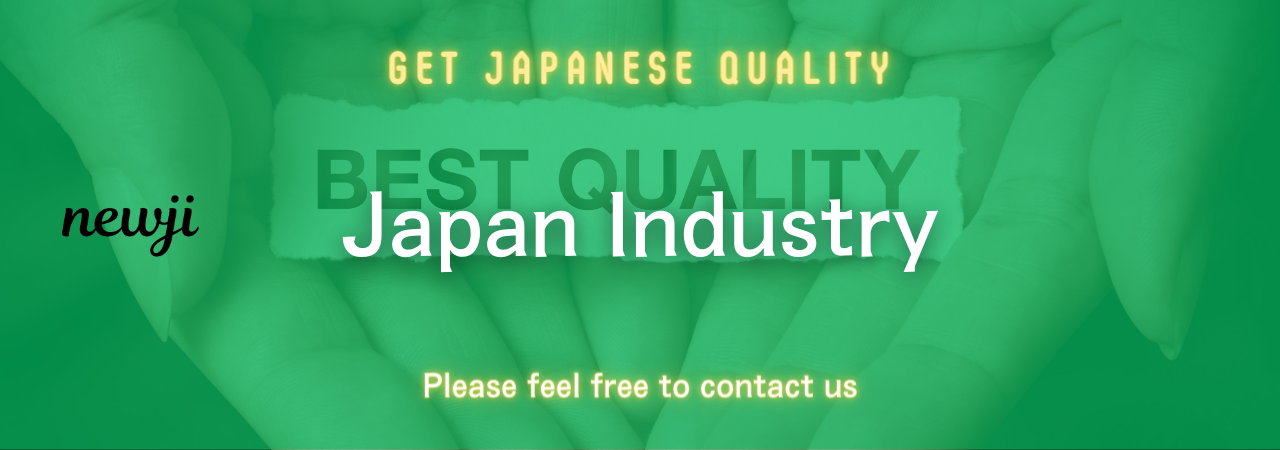
目次
Understanding FMEA and Its Importance
Failure Mode and Effects Analysis, commonly known as FMEA, is a systematic, step-by-step approach used for identifying potential failure modes, assessing their impact, and prioritizing actions to mitigate the risks associated with these failures.
The main objective is to improve the reliability and quality of a product or process by recognizing failure points before they cause significant impacts.
With the implementation of Design Review (DR) methods through FMEA, organizations can effectively preempt quality issues and enhance customer satisfaction.
FMEA is essential as it helps identify and rectify potential failures before they occur, thus ensuring smooth operations.
This analysis method is employed across various sectors such as manufacturing, engineering, and healthcare, making it a versatile tool in avoiding costly failures and downtime.
By systematically assessing potential failures, FMEA aids in developing strategies to either eliminate or minimize risks, ensuring that quality standards are met.
Key Steps in Implementing FMEA
1. Assemble the FMEA Team
Forming a diverse team is the first step in conducting an FMEA.
The team should include expertise from different fields, as these individuals will bring a wide range of perspectives and insights into the analysis process.
The team usually consists of members from design, manufacturing, testing, quality assurance, and even end-user representatives.
Their varied expertise and insights will drive the identification of potential failure modes effectively.
2. Define the Scope of Analysis
Before delving into the FMEA process, it is imperative to clearly define the scope of the analysis.
This involves pinpointing which parts or processes will be reviewed.
Defining the scope ensures that the team focuses only on relevant aspects of the product or process, optimizing time and resources.
3. Identify Potential Failure Modes
The team should brainstorm all possible failure modes for each component or step in the process.
A failure mode can be anything ranging from a component breakdown to a user error.
It’s crucial to be as exhaustive as possible at this stage because even seemingly insignificant failures can lead to quality issues if not addressed.
4. Determine the Effects of Failures
Once potential failure modes are identified, the next step is to analyze their effects.
The impact of each failure mode must be evaluated in terms of severity, occurrence, and detection.
The severity describes how serious the effect of failure is on the product or process.
Understanding the potential effects is crucial for prioritizing which aspects need immediate focus.
5. Prioritize Potential Failures
It is crucial to prioritize the identified potential failures based on the Risk Priority Number (RPN).
RPN is derived by multiplying the ratings of severity, occurrence, and detection of each failure mode.
Higher RPN scores indicate high-priority failure modes that require immediate attention.
By focusing on these high-risk areas, the organization can allocate resources more effectively and implement corrective actions where they are most needed.
Design Review (DR) in the Context of FMEA
Design Review, or DR, is an integral part of the FMEA process that ensures design objectives are met while maintaining high-quality standards.
Effective DR helps verify whether the product design is capable of withstanding the identified risks, thus preventing quality issues before they arise.
Ensuring DR Effectiveness
One of the key factors in effective DR is the involvement of cross-functional teams in the process.
This ensures a comprehensive evaluation of the design by incorporating diverse perspectives.
Involving team members from various disciplines helps uncover potential issues that might have been overlooked by a single focus group.
Regular DR sessions should be scheduled at various stages of the design process.
These scheduled sessions allow for continuous assessment and improvements, aligning the product design with customer expectations and industry standards.
By adopting a systematic approach towards DR within the FMEA framework, organizations can proactively design products that minimize failure risks and reach optimal performance levels.
Preventing Quality Troubles Through FMEA and DR
The combined implementation of FMEA and DR ensures that quality troubles are effectively managed.
This collaboration allows organizations to preemptively identify and eliminate potential sources of quality deviation.
Documenting and Monitoring
One of the critical components in preventing quality troubles is the thorough documentation of all findings and actions taken during the FMEA process.
Each change and observation should be meticulously recorded to track the improvements made and to form a reference point for future analyses.
Monitoring the implementation of corrective actions also allows for the validation of their effectiveness, ensuring that quality standards are consistently met.
Continuous Improvement Culture
Promoting a culture of continuous improvement is essential to prevent quality troubles.
Continuous feedback loops, regular training, and open communication channels encourage team members to actively engage in identifying areas for improvement.
By maintaining this culture, the organization ensures that quality is not just a goal but an ongoing practice.
Employing FMEA, with its systematic approach to identifying and addressing potential failures, coupled with effective Design Review processes, equips organizations with the insights needed to foster high-quality standards and prevent future quality issues.
As a result, organizations that embrace these methods see significant improvements in product and process reliability, ultimately enhancing their competitive edge and customer satisfaction.
資料ダウンロード
QCD管理受発注クラウド「newji」は、受発注部門で必要なQCD管理全てを備えた、現場特化型兼クラウド型の今世紀最高の受発注管理システムとなります。
ユーザー登録
受発注業務の効率化だけでなく、システムを導入することで、コスト削減や製品・資材のステータス可視化のほか、属人化していた受発注情報の共有化による内部不正防止や統制にも役立ちます。
NEWJI DX
製造業に特化したデジタルトランスフォーメーション(DX)の実現を目指す請負開発型のコンサルティングサービスです。AI、iPaaS、および先端の技術を駆使して、製造プロセスの効率化、業務効率化、チームワーク強化、コスト削減、品質向上を実現します。このサービスは、製造業の課題を深く理解し、それに対する最適なデジタルソリューションを提供することで、企業が持続的な成長とイノベーションを達成できるようサポートします。
製造業ニュース解説
製造業、主に購買・調達部門にお勤めの方々に向けた情報を配信しております。
新任の方やベテランの方、管理職を対象とした幅広いコンテンツをご用意しております。
お問い合わせ
コストダウンが利益に直結する術だと理解していても、なかなか前に進めることができない状況。そんな時は、newjiのコストダウン自動化機能で大きく利益貢献しよう!
(β版非公開)