- お役立ち記事
- How to effectively proceed with FMEA and design reviews, and practical points to prevent quality problems.
How to effectively proceed with FMEA and design reviews, and practical points to prevent quality problems.
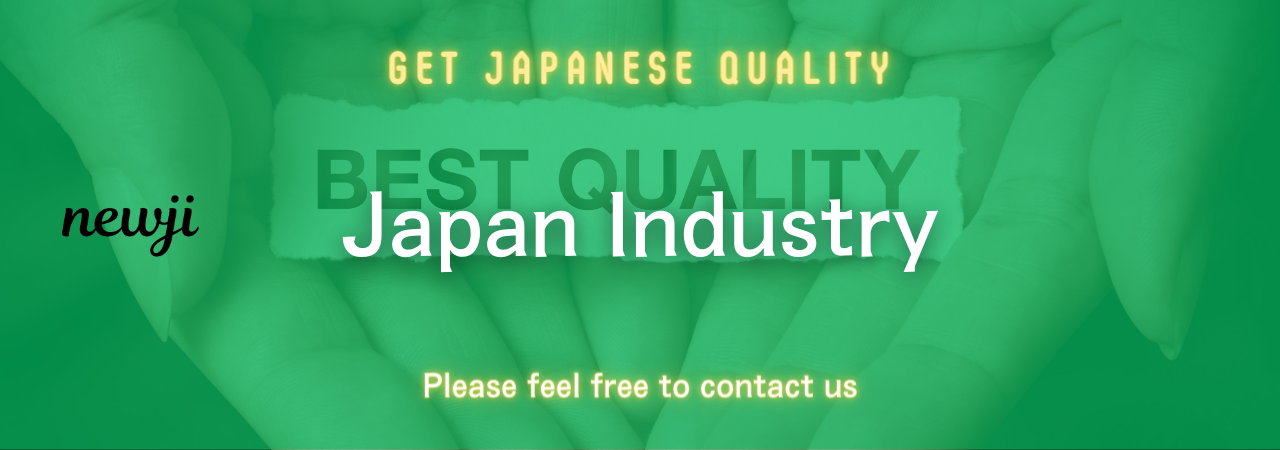
目次
Understanding FMEA and Design Reviews
Failure Mode and Effects Analysis (FMEA) and design reviews are essential tools in product development and manufacturing processes.
They play a critical role in identifying potential failures, assessing risks, and ensuring product quality.
By effectively implementing FMEA and conducting thorough design reviews, companies can prevent quality problems and ensure customer satisfaction.
FMEA is a systematic approach used to identify potential failure modes, evaluate their effects, and prioritize actions to mitigate these risks.
It helps to uncover potential issues early in the product development cycle, thereby reducing the likelihood of costly recalls or customer complaints.
Design reviews, on the other hand, involve scrutinizing a product’s design to ensure it meets the intended requirements and standards.
Both processes are vital for maintaining high-quality standards and minimizing defects.
Steps to Conduct an Effective FMEA
Implementing an effective FMEA requires a structured and comprehensive approach.
The following steps outline how to proceed with this crucial analysis:
1. Assemble a Cross-Functional Team
Gather a team comprising members from various departments, such as engineering, quality assurance, manufacturing, and customer service.
This diversity brings different perspectives, ensuring a comprehensive analysis.
Each member provides unique insights into how a potential failure could impact their area of expertise.
2. Define the Scope and Identify Failure Modes
Clearly define the scope of the FMEA and focus on specific processes or components.
Identify all possible failure modes—ways in which a component, system, or process could fail.
For example, if analyzing a car engine, consider failure modes like overheating, oil leaks, or component wear and tear.
3. Analyze the Effects and Causes
Evaluate the potential effects of each failure mode on the end product.
Ask questions like: How does this failure impact the user?
What safety issues could arise?
Determine the root causes of these failure modes to help design effective countermeasures.
4. Calculate the Risk Priority Number (RPN)
Assign scores to each failure mode based on its severity, occurrence, and detection.
Multiply these scores to calculate the Risk Priority Number (RPN).
Prioritize failure modes with the highest RPN for immediate action.
5. Develop and Implement Action Plans
Create action plans to address high-priority failure modes.
Implement corrective measures and monitor their effectiveness.
This might involve design changes, process alterations, or additional testing.
Strategies for Successful Design Reviews
To ensure the success of design reviews, follow these strategic approaches:
1. Set Clear Objectives
Before starting the review, establish clear objectives.
Determine what you aim to achieve with the review process—whether it’s to identify design flaws, ensure compliance with standards, or verify functionality.
2. Involve the Right Stakeholders
Involve stakeholders who have an in-depth understanding of the product and its requirements.
This includes engineers, designers, quality assurance specialists, and customers if necessary.
Their feedback and expertise are crucial for a comprehensive review.
3. Conduct Multiple Review Stages
Design reviews should occur at various stages of the product’s lifecycle, from initial concept to final prototype.
Each stage serves as a checkpoint to ensure the design meets evolving requirements and standards.
4. Document the Process
Thoroughly document each stage of the design review process.
Record observations, suggestions, and decisions made during the review.
This documentation not only provides a reference for future projects but also ensures accountability and traceability.
5. Focus on Continuous Improvement
Design reviews should not be seen as a one-time activity.
Instead, use the insights gained to continuously improve the product design and development process.
Implement feedback loops to ensure the product evolves and adapts to changing needs and technologies.
Preventing Quality Problems Through Proactive Measures
By effectively integrating FMEA and design reviews into product development and manufacturing processes, organizations can prevent quality problems and enhance product reliability.
1. Embrace a Proactive Quality Culture
Cultivating a proactive quality culture is crucial for preventing defects and enhancing overall quality.
Encourage employees at all levels to take ownership of quality and actively participate in identifying and resolving potential issues.
2. Leverage Technology and Data
Utilize advanced technologies, such as predictive analytics and simulations, to anticipate potential failure modes and product performance.
Analyze data from previous projects to gain insights into common issues and how to prevent them.
3. Invest in Training and Development
Equip employees with the necessary skills and knowledge to conduct effective FMEAs and design reviews.
Invest in ongoing training and development to keep the workforce updated on the latest industry standards and best practices.
4. Collaborate with Suppliers
Work closely with suppliers to ensure that components meet quality standards and requirements.
Collaborate on risk assessments and design reviews to identify potential supply chain issues before they impact the final product.
5. Monitor and Evaluate Results
Continuously monitor the effectiveness of implemented changes and measure their impact on product quality.
Use key performance indicators (KPIs) to evaluate success and identify areas for further improvement.
By taking these proactive measures, organizations can significantly reduce the risk of quality problems and enhance their reputation for delivering reliable, high-quality products.
This ultimately leads to increased customer satisfaction and long-term success in the marketplace.
資料ダウンロード
QCD調達購買管理クラウド「newji」は、調達購買部門で必要なQCD管理全てを備えた、現場特化型兼クラウド型の今世紀最高の購買管理システムとなります。
ユーザー登録
調達購買業務の効率化だけでなく、システムを導入することで、コスト削減や製品・資材のステータス可視化のほか、属人化していた購買情報の共有化による内部不正防止や統制にも役立ちます。
NEWJI DX
製造業に特化したデジタルトランスフォーメーション(DX)の実現を目指す請負開発型のコンサルティングサービスです。AI、iPaaS、および先端の技術を駆使して、製造プロセスの効率化、業務効率化、チームワーク強化、コスト削減、品質向上を実現します。このサービスは、製造業の課題を深く理解し、それに対する最適なデジタルソリューションを提供することで、企業が持続的な成長とイノベーションを達成できるようサポートします。
オンライン講座
製造業、主に購買・調達部門にお勤めの方々に向けた情報を配信しております。
新任の方やベテランの方、管理職を対象とした幅広いコンテンツをご用意しております。
お問い合わせ
コストダウンが利益に直結する術だと理解していても、なかなか前に進めることができない状況。そんな時は、newjiのコストダウン自動化機能で大きく利益貢献しよう!
(Β版非公開)