- お役立ち記事
- How to effectively proceed with fracture surface analysis (fractography) and practice in investigating the cause of damage
月間77,185名の
製造業ご担当者様が閲覧しています*
*2025年2月28日現在のGoogle Analyticsのデータより
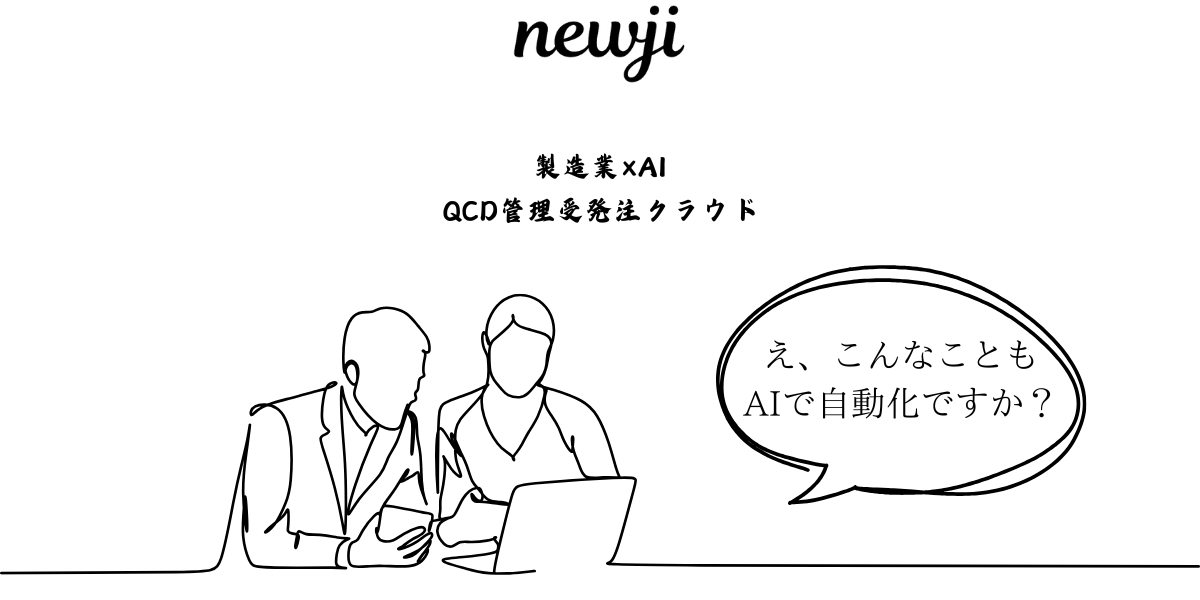
How to effectively proceed with fracture surface analysis (fractography) and practice in investigating the cause of damage
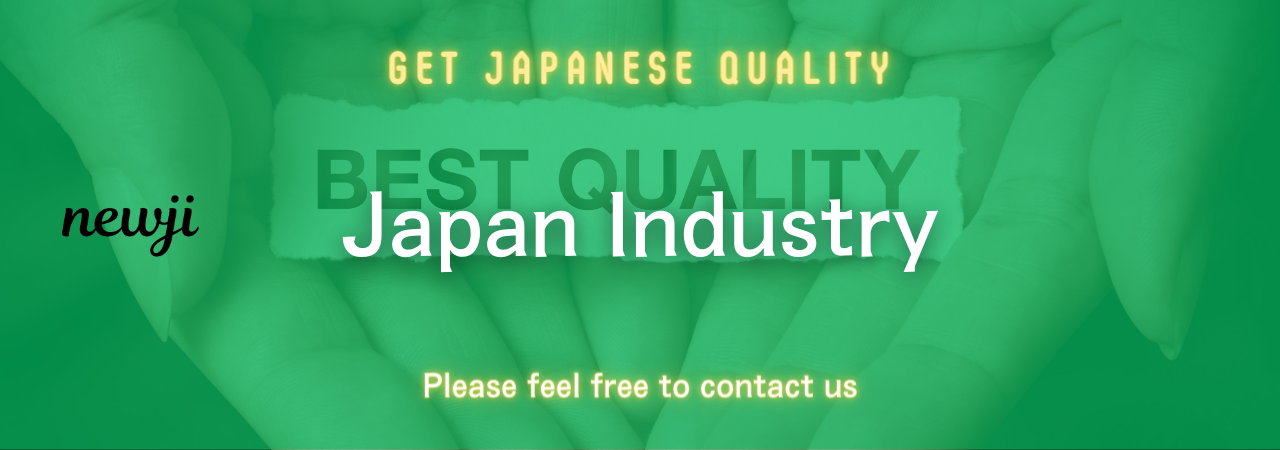
目次
Understanding Fracture Surface Analysis
Fracture surface analysis, also known as fractography, is a crucial tool in the field of materials science and engineering.
When a material fails or breaks, examining the fracture surface can provide valuable information about the failure process and its causes.
Fractography involves analyzing the patterns, textures, and features of the fracture surface to identify stress factors, environmental conditions, and other influences that contributed to the failure.
To begin with, understanding the type of fracture is essential.
Fractures can be broadly classified into ductile and brittle fractures.
Ductile fractures, often characterized by significant plastic deformation, display a rough and fibrous fracture surface.
Conversely, brittle fractures, which occur with minimal plastic deformation, present smooth and bright surfaces with a more granular texture.
Identifying whether the fracture is ductile or brittle is the first step in effective fracture analysis.
The Process of Fracture Surface Analysis
Effective fracture surface analysis involves a systematic approach to examining and documenting the fracture surface.
This ensures that all pertinent details of the fracture surface are captured and subjected to detailed scrutiny.
The process typically begins with the collection and preservation of fracture samples, followed by visual inspections, microscopic examinations, and advanced analytical techniques.
1. Sample Collection and Preservation
Sample collection is the foundational step in fracture surface analysis.
It is crucial to handle samples with care to avoid altering or contaminating the fracture surface.
Samples should be collected from the failure site as soon as possible and preserved in a manner that maintains their original condition.
Proper labeling and documentation of the sample location, orientation, and environmental conditions at the time of failure are essential for accurate analysis.
2. Visual Inspection
Once the samples are collected, a detailed visual inspection should be performed.
This requires a careful examination of the fracture surface with the naked eye or using a magnifying glass.
Look for patterns, discoloration, and unusual features that may hint at the failure mode.
In some cases, a stereomicroscope can be used to gain an enhanced view of surface features.
3. Microscopic Examination
Microscopic examination is a critical component of fracture surface analysis.
Scanning Electron Microscopy (SEM) is one of the most widely used techniques for this purpose.
SEM provides high-resolution images of the fracture surface, allowing for detailed observation of micro features that are not visible to the naked eye.
Key characteristics such as dimples, striations, and river patterns can be identified using SEM to help determine the failure mode.
4. Advanced Analytical Techniques
In addition to SEM, other advanced analytical techniques can provide further insights into the nature of the fracture.
Energy Dispersive X-ray Spectroscopy (EDX) is often used in conjunction with SEM to analyze the chemical composition of the fracture surface.
This helps to identify any foreign materials, contaminants, or elemental deficiencies that may have contributed to the failure.
Other techniques such as X-ray Diffraction (XRD) and Fourier Transform Infrared Spectroscopy (FTIR) may also be utilized depending on the material and failure conditions.
Investigating Cause of Damage
Effective fracture analysis goes beyond mere observation of the fracture surface.
It requires a deep investigation into the root cause of the damage.
Several factors can influence the fracture of a material, including material properties, design flaws, manufacturing defects, and environmental conditions.
Understanding Material Properties
Every material has inherent properties that dictate its performance under stress.
Understanding these properties is fundamental to determining why a fracture occurred.
Properties such as tensile strength, toughness, ductility, and hardness influence how a material behaves under load.
By considering the expected properties against those observed in practice, potential discrepancies or weaknesses can be identified.
Design and Manufacturing Defects
Design and manufacturing defects are common contributors to material failures.
Design defects may arise from inadequate consideration of load paths, stress concentrations, or material compatibility.
Manufacturing defects, on the other hand, could include improper heat treatment, machining errors, or inclusion of foreign materials.
Thorough investigations of these potential defects should be conducted in parallel with fracture analysis.
Environmental Considerations
Environmental factors, such as temperature, humidity, and chemical exposure, can dramatically influence material behavior.
Certain environments may accelerate corrosion or cause unexpected stress on materials.
Therefore, a full appraisal of the service environment is crucial to understanding and preventing similar failures in the future.
Practice in Investigating the Cause of Damage
Combining fracture surface analysis with a root cause investigation provides the most comprehensive understanding of material failures.
This practice involves not only understanding the science behind fractures but also applying systematic investigative techniques.
Conducting simulations or recreations of the failure circumstances can provide additional insights.
Software tools and physical tests can replicate the conditions to determine their impact on the material.
Collaboration with cross-disciplinary teams also enriches the analysis, bringing together materials experts, engineers, and environmental scientists.
Moreover, maintaining a detailed archive of historical data on material behavior and previously encountered failures can be invaluable.
Such records can highlight recurring issues and solutions that can be applied to future cases.
With thorough and effective fracture surface analysis and practice in cause investigation, industries can mitigate future failures, enhance product reliability, and ensure the safety of their applications.
In doing so, they not only safeguard their interests but also contribute to the advancement of materials science and engineering as a whole.
資料ダウンロード
QCD管理受発注クラウド「newji」は、受発注部門で必要なQCD管理全てを備えた、現場特化型兼クラウド型の今世紀最高の受発注管理システムとなります。
ユーザー登録
受発注業務の効率化だけでなく、システムを導入することで、コスト削減や製品・資材のステータス可視化のほか、属人化していた受発注情報の共有化による内部不正防止や統制にも役立ちます。
NEWJI DX
製造業に特化したデジタルトランスフォーメーション(DX)の実現を目指す請負開発型のコンサルティングサービスです。AI、iPaaS、および先端の技術を駆使して、製造プロセスの効率化、業務効率化、チームワーク強化、コスト削減、品質向上を実現します。このサービスは、製造業の課題を深く理解し、それに対する最適なデジタルソリューションを提供することで、企業が持続的な成長とイノベーションを達成できるようサポートします。
製造業ニュース解説
製造業、主に購買・調達部門にお勤めの方々に向けた情報を配信しております。
新任の方やベテランの方、管理職を対象とした幅広いコンテンツをご用意しております。
お問い合わせ
コストダウンが利益に直結する術だと理解していても、なかなか前に進めることができない状況。そんな時は、newjiのコストダウン自動化機能で大きく利益貢献しよう!
(β版非公開)