- お役立ち記事
- How to effectively utilize CAE and points to use in design practice
月間77,185名の
製造業ご担当者様が閲覧しています*
*2025年2月28日現在のGoogle Analyticsのデータより
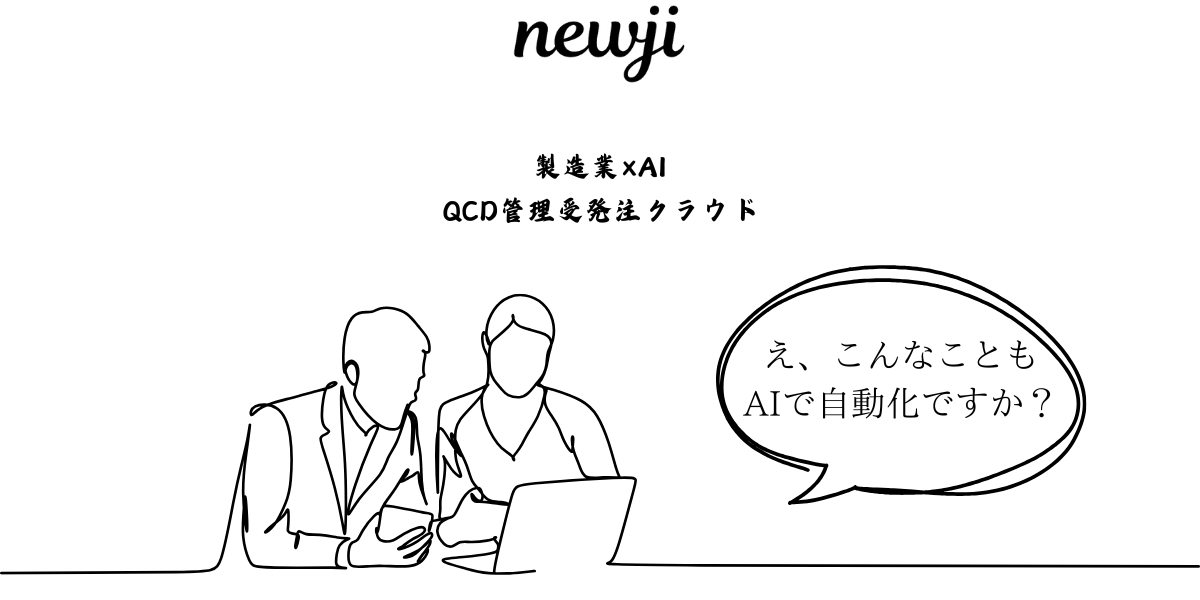
How to effectively utilize CAE and points to use in design practice
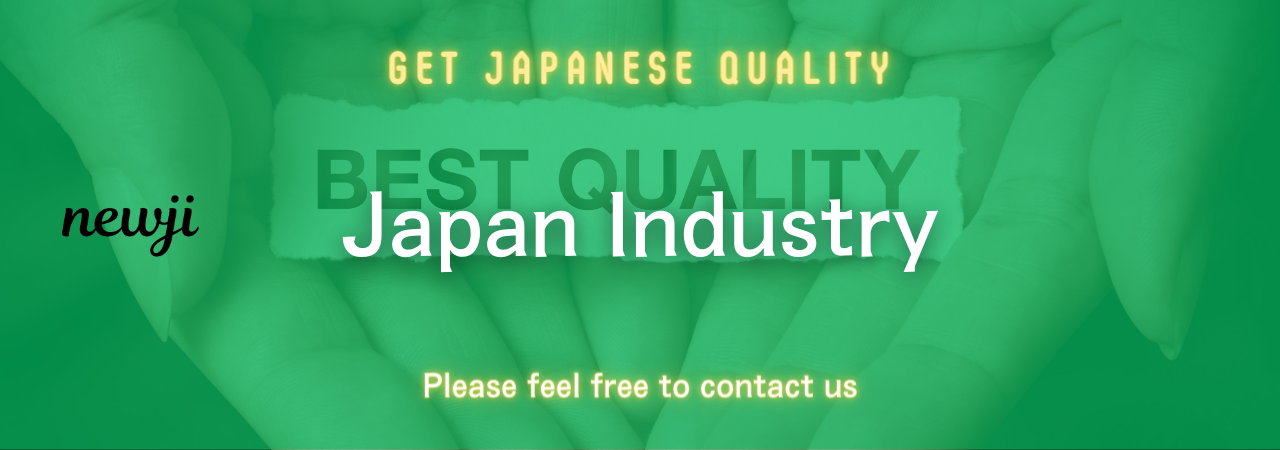
目次
Understanding CAE: What Is It?
Computer-Aided Engineering, commonly known as CAE, refers to the use of computer software to simulate performance in order to improve product design and manufacturing processes.
CAE helps engineers to perform tests and analyses on products and systems to predict how they will behave in real-world conditions.
By utilizing CAE, organizations can enhance the design, testing, and refinement process, making it more efficient and cost-effective.
Through CAE, engineers can conduct a wide range of engineering analyses that include stress tests, thermal evaluations, and fluid dynamics assessments, among others.
These analyses help in identifying and resolving potential issues before the actual production, reducing the risk of failure and ensuring product quality.
CAE tools are invaluable across various industries, including automotive, aerospace, and electronics, where precision and reliability are crucial.
Benefits of Using CAE in Design Practice
Accelerated Product Development
One of the primary advantages of utilizing CAE is that it significantly speeds up the product development cycle.
By simulating real-life conditions early in the design process, engineers can quickly identify and address potential issues, ensuring that designs meet specifications and standards.
This enables faster prototyping, which in turn accelerates time to market.
Cost Efficiency
Traditional testing methods can be expensive, involving the creation of multiple physical prototypes and the execution of numerous tests.
With CAE, multiple design iterations can be tested virtually, reducing the need for costly physical models.
The ability to foresee issues and make adjustments before the manufacturing stage can also substantially decrease waste and rework.
Improved Product Quality
By allowing detailed simulations of how a product will behave under various conditions, CAE helps in improving overall product quality and reliability.
It provides engineers with comprehensive data and insights, enabling them to refine designs and ensure they perform optimally under expected stressors.
High-quality products result in fewer failures and returns, leading to enhanced customer satisfaction and brand loyalty.
Key Considerations When Employing CAE
Understanding Software Capabilities
Not all CAE software is created equal.
Different tools may specialize in specific analyses, such as structural analysis or fluid dynamics.
Engineers must understand the capabilities and limitations of the software they are utilizing to ensure it meets the needs of their specific projects.
Comprehensive training and familiarity with the chosen CAE tool are crucial for maximizing its effectiveness.
Accurate Data Input
The accuracy of CAE simulations depends heavily on the data input into the system.
Engineers must ensure that all material properties, boundary conditions, and load scenarios are accurately represented to achieve valid results.
Inaccurate input data can lead to unreliable outcomes, potentially resulting in design flaws or safety issues.
Integration with Other Design Tools
For optimal results, CAE should be integrated with other computer-aided technologies such as CAD (Computer-Aided Design) and CAM (Computer-Aided Manufacturing).
This integrated approach facilitates seamless data exchange and collaboration, ensuring all aspects of product development are aligned.
Coordination between various design and manufacturing teams is also enhanced through such integrations.
Steps to Effectively Utilize CAE in Design Practice
Define Objectives and Requirements
The first step in effectively utilizing CAE is to clearly define the design objectives and requirements.
This involves understanding the key functionality, performance criteria, and constraints for the product.
Clear objectives ensure that the engineering team can focus the CAE analyses on critical aspects that will influence the product’s success.
Select the Right Tools
With a clear understanding of the project needs, choose CAE tools that best meet those specific requirements.
Consider factors like the type of analyses required, the complexity of models, and user-friendliness of the tools.
Consulting with CAE experts or leveraging previous experience can assist in selecting the most appropriate tools.
Create Detailed Designs
Develop detailed CAD models as inputs for CAE simulations.
The precision of these models will significantly impact the CAE results.
Ensure all product dimensions, materials, and configurations are well-represented in the models to enable accurate analyses.
Conduct Comprehensive Simulations
Perform a range of simulations to test the design under different scenarios and conditions.
This may include stress analysis, thermal simulations, and crash testing, among others, depending on the product.
Assess how variations in materials, dimensions, or configurations affect the performance and iteratively refine designs based on the results.
Collaborate and Review Results
CAE results should be reviewed in collaboration with different teams, including design, manufacturing, and quality assurance departments.
This collaborative approach ensures that different perspectives are considered, and potential issues are identified and addressed early.
Regular design reviews also facilitate the decision-making process and keep the project on track.
Implement Iterative Improvements
The iterative design process is a core principle of CAE.
Use feedback and simulations from different iterations to continuously improve the design.
This iterative refinement helps in gradually optimizing the product for performance, safety, and cost-effectiveness.
Conclusion
The effective use of CAE in design practice can bring about significant advantages, from accelerated development times to improved product quality and cost savings.
By understanding the capabilities of CAE tools, accurately inputting data, and fostering integration with other digital engineering technologies, teams can harness CAE for optimal results.
Through clear planning, collaboration, and iterative improvements, CAE can become an integral part of design and manufacturing processes, contributing to the creation of innovative and reliable products.
資料ダウンロード
QCD管理受発注クラウド「newji」は、受発注部門で必要なQCD管理全てを備えた、現場特化型兼クラウド型の今世紀最高の受発注管理システムとなります。
ユーザー登録
受発注業務の効率化だけでなく、システムを導入することで、コスト削減や製品・資材のステータス可視化のほか、属人化していた受発注情報の共有化による内部不正防止や統制にも役立ちます。
NEWJI DX
製造業に特化したデジタルトランスフォーメーション(DX)の実現を目指す請負開発型のコンサルティングサービスです。AI、iPaaS、および先端の技術を駆使して、製造プロセスの効率化、業務効率化、チームワーク強化、コスト削減、品質向上を実現します。このサービスは、製造業の課題を深く理解し、それに対する最適なデジタルソリューションを提供することで、企業が持続的な成長とイノベーションを達成できるようサポートします。
製造業ニュース解説
製造業、主に購買・調達部門にお勤めの方々に向けた情報を配信しております。
新任の方やベテランの方、管理職を対象とした幅広いコンテンツをご用意しております。
お問い合わせ
コストダウンが利益に直結する術だと理解していても、なかなか前に進めることができない状況。そんな時は、newjiのコストダウン自動化機能で大きく利益貢献しよう!
(β版非公開)