- お役立ち記事
- How to effectively utilize QFD to improve design quality that should be addressed by the mechanical design department
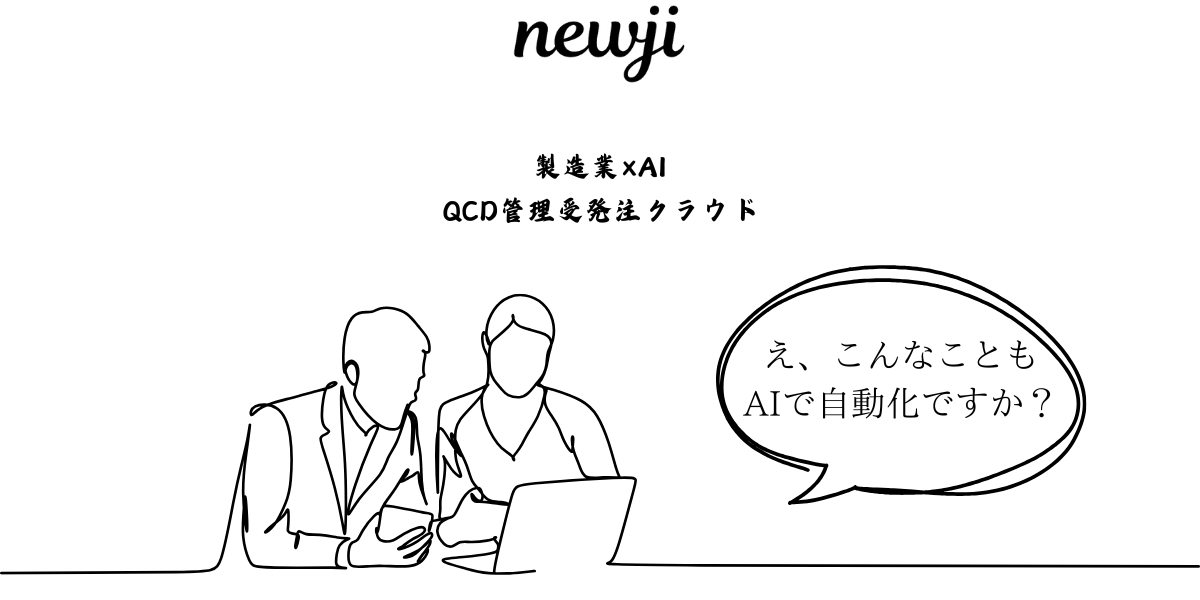
How to effectively utilize QFD to improve design quality that should be addressed by the mechanical design department
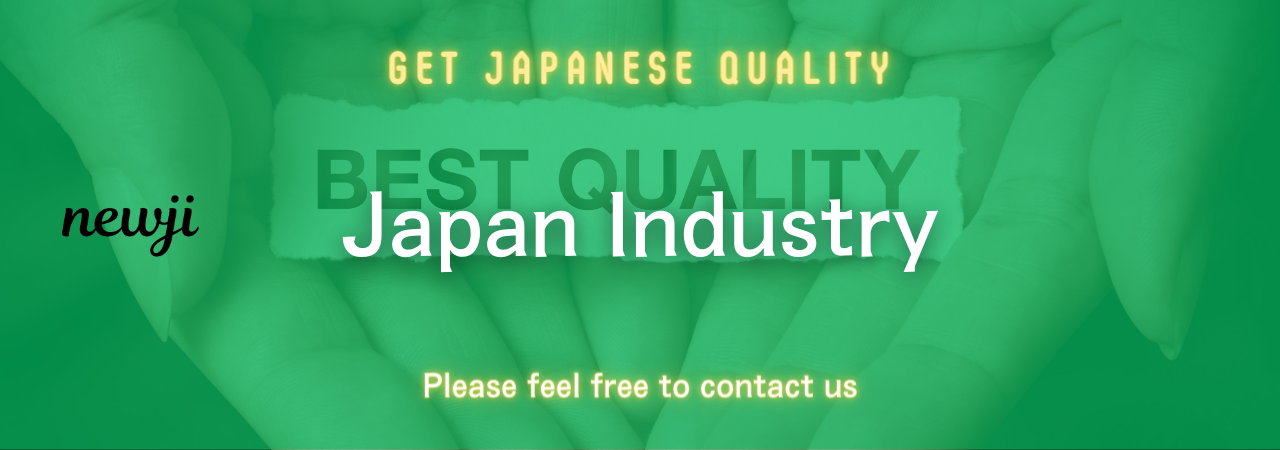
目次
Understanding Quality Function Deployment (QFD)
Quality Function Deployment (QFD) is a framework that helps teams understand customer needs and translate them into technical requirements.
The essence of QFD lies in ensuring that customer satisfaction is central to every stage of product development.
For mechanical design departments, this focus can lead to significantly improved design quality.
The Importance of Customer Feedback
In mechanical design, translating customer requirements into tangible product features can be challenging.
However, by effectively utilizing QFD, teams can bridge the gap between customer expectations and engineering capabilities.
The process begins by collecting detailed customer inputs and interpreting them into prioritized product features.
QFD ensures that even the most minute customer desires are considered during the design phase.
By using tools like the House of Quality matrix, the design department can evaluate customer requirements against feasible technical solutions.
This matrix acts as a visual tool, helping engineers to maintain focus on high-priority design elements.
Implementing QFD in Mechanical Design
Integrating QFD into the existing design process requires careful planning and execution.
Firstly, the mechanical design team needs to establish a cross-functional group involving marketing, engineering, and product management.
This ensures diverse perspectives and expertise are incorporated during decision-making.
The initial step in QFD implementation is to create a comprehensive list of customer demands.
These are gathered through various methods like surveys, focus groups, and market research.
Once compiled, each requirement is analyzed to understand its significance and potential impact on the design.
The next phase involves defining engineering characteristics that can meet these customer needs.
This is where the mechanical design department plays a crucial role.
Engineers formulate specifications and measurable parameters to guide the creation of product features.
Benefits of QFD in Mechanical Design
Using QFD provides numerous advantages to the mechanical design team.
One of the primary benefits is a more structured approach to product development.
With a clear framework, engineers can better allocate resources and reduce time spent on unnecessary revisions.
QFD also enhances collaboration within the department.
By involving multiple departments, it fosters a culture of teamwork and collective problem-solving.
When everyone understands customer priorities, it becomes easier to work towards common goals.
Additionally, QFD reduces the risk of product failure.
By aligning design features with customer expectations right from the start, the likelihood of defects or oversights diminishes.
Ultimately, this leads to higher customer satisfaction and brand loyalty.
Challenges in Implementing QFD
Despite its benefits, implementing QFD is not without challenges.
One significant hurdle is resistance to change.
Mechanical design departments accustomed to traditional processes might apprehend the introduction of a new framework.
Moreover, gathering accurate and comprehensive customer data can be difficult.
The quality of information from customers is critical, as it forms the foundation of the entire QFD process.
There’s also the challenge of integrating QFD with existing design tools and methodologies.
It requires balancing traditional practices with the new processes introduced by QFD.
Overcoming Implementation Challenges
To successfully overcome these challenges, mechanical design departments need to embrace adaptability.
Conducting workshops and training sessions can help the team understand the advantages of QFD and mitigate resistance.
In terms of data collection, leveraging technology can significantly improve data accuracy and efficiency.
Toolsets like software analytics and customer relationship management systems can streamline this aspect.
Finally, it’s essential to create a phased integration plan for QFD.
Gradually introducing its principles into the current workflow can ease the transition and ensure seamless adoption.
Conclusion
For mechanical design departments striving to enhance their design quality, QFD offers a robust framework to achieve this goal.
By keeping customer needs at the forefront, it aligns design attributes with market demand, ensuring products not only meet but exceed expectations.
With the right approach to implementation, overcoming initial challenges, and a commitment to customer-centric design, QFD can become a game-changer in the mechanical design landscape.
In the long run, its adoption could translate into a competitive advantage and a greater market presence.
資料ダウンロード
QCD調達購買管理クラウド「newji」は、調達購買部門で必要なQCD管理全てを備えた、現場特化型兼クラウド型の今世紀最高の購買管理システムとなります。
ユーザー登録
調達購買業務の効率化だけでなく、システムを導入することで、コスト削減や製品・資材のステータス可視化のほか、属人化していた購買情報の共有化による内部不正防止や統制にも役立ちます。
NEWJI DX
製造業に特化したデジタルトランスフォーメーション(DX)の実現を目指す請負開発型のコンサルティングサービスです。AI、iPaaS、および先端の技術を駆使して、製造プロセスの効率化、業務効率化、チームワーク強化、コスト削減、品質向上を実現します。このサービスは、製造業の課題を深く理解し、それに対する最適なデジタルソリューションを提供することで、企業が持続的な成長とイノベーションを達成できるようサポートします。
オンライン講座
製造業、主に購買・調達部門にお勤めの方々に向けた情報を配信しております。
新任の方やベテランの方、管理職を対象とした幅広いコンテンツをご用意しております。
お問い合わせ
コストダウンが利益に直結する術だと理解していても、なかなか前に進めることができない状況。そんな時は、newjiのコストダウン自動化機能で大きく利益貢献しよう!
(Β版非公開)