- お役立ち記事
- How to effectively utilize technical information organized by evolutionary QFD for quality control and product development
月間76,176名の
製造業ご担当者様が閲覧しています*
*2025年3月31日現在のGoogle Analyticsのデータより
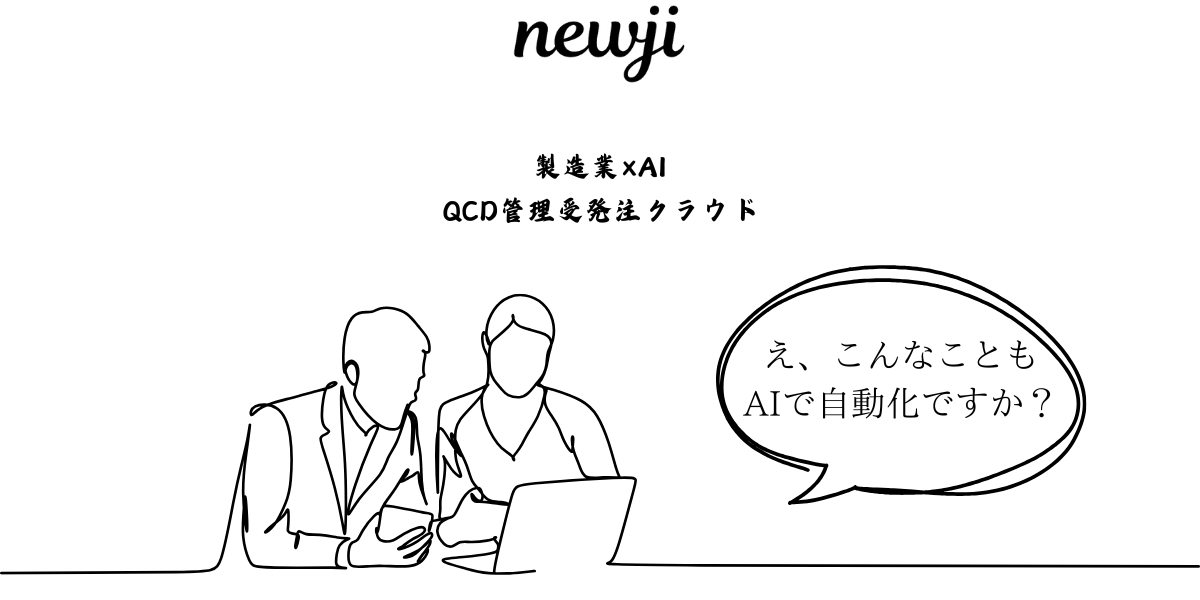
How to effectively utilize technical information organized by evolutionary QFD for quality control and product development
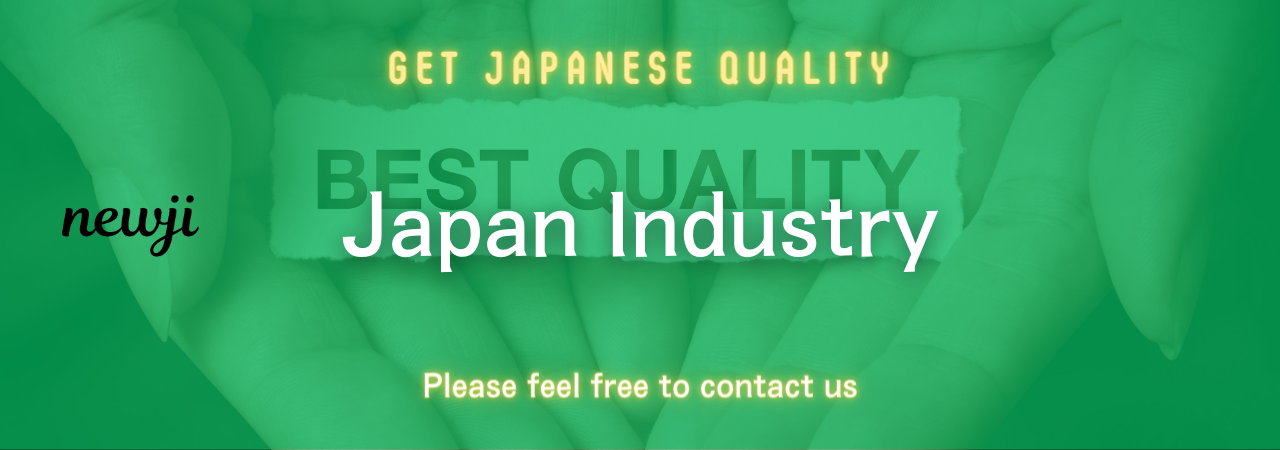
目次
Understanding Evolutionary QFD
Quality Function Deployment (QFD) is a systematic approach used to integrate customer requirements into all stages of product development and quality control.
It transforms qualitative user demands into quantitative parameters, bringing a structured way to ensure quality.
Evolutionary QFD takes this one step further by adapting and evolving as new information and technology emerge.
It provides a dynamic framework that is especially crucial in industries where rapid innovation is key.
The evolutionary aspect of QFD is its ability to adjust to changes over time and the incorporation of new technical information.
With this approach, companies can anticipate trends, recognize shifting customer needs, and implement cutting-edge technology swiftly into their products and processes.
The Importance of Technical Information
Technical information is at the heart of effective QFD implementation.
It encompasses all data related to product specifications, technological advancements, material properties, and manufacturing processes.
When organized well, this information allows for more accurate decision-making and improved product designs.
Access to up-to-date technical information ensures that all stakeholders are informed, reducing errors and delays that could arise from miscommunication or outdated data.
It fosters a unified approach to product development, ensuring that customer needs are met while optimizing resources.
Organizing Technical Information for Easy Access
The key to successful QFD lies in how technical information is organized and accessed.
Firstly, all relevant data should be stored in a centralized database.
This enables easy access and update by various departments, from design to production to marketing.
Secondly, this database should be regularly updated to reflect the latest advancements and compliance with industry standards.
Effective categorization is essential; information should be divided into clear sections such as materials, processes, technologies, and market trends.
Clear labeling and indexing further facilitate searchability, ensuring users can quickly find the needed data.
Utilizing Digital Tools for Organization
Incorporating digital tools can significantly enhance the organization of technical information.
Project management software, collaborative platforms, and data analytics tools can streamline the process.
These tools allow for real-time updating, ensure accurate tracking of changes, and improve communication across teams.
For instance, a collaborative platform can enable engineers and designers to share insights and feedback instantly, leading to quicker problem-solving and innovation.
Cloud-based solutions can also store vast amounts of data, keeping it secure and accessible from anywhere.
Applying Technical Information in QFD
Once technical information is organized efficiently, applying it within the QFD framework is the next step.
This involves translating customer demands into design specifications using the organized data.
The House of Quality, a QFD tool, helps in this translation process by mapping customer needs against technical requirements.
With organized information, this mapping becomes more straightforward, allowing for a clear visualization of priorities and potential trade-offs.
Organized technical data aids in setting realistic targets and identifying necessary adjustments early in the development process.
This ensures that any changes made at the design stage align with the overall product goals and customer expectations.
Improving Product Quality and Innovation
Utilizing technical information effectively through evolutionary QFD can significantly enhance product quality and drive innovation.
By having a well-structured repository of technical data, teams can focus more on creative solutions and less on administrative tasks.
It also promotes a proactive approach to quality control, as consistent updates can reveal potential issues before they arise, allowing for preventive measures.
This leads to higher customer satisfaction, as products are not only innovative but also reliable and aligned with user expectations.
Training Teams for Effective Utilization
To take full advantage of organized technical information, training teams is vital.
Employees should be well-versed in using the QFD methodology and understanding how to access and interpret technical data.
Regular workshops and training sessions can equip teams with the skills needed to leverage technical information effectively.
These sessions can cover topics such as data analysis, digital tool usage, and trends in product development and quality control.
Encouraging a culture of continuous learning and adaptation is essential, as technological advancements and customer needs are constantly evolving.
By investing in team training, organizations ensure that their workforce is prepared to utilize emerging information efficiently.
Conclusion
The evolutionary QFD approach, when combined with expertly organized technical information, forms a powerful tool for quality control and product development.
Ensuring easy access and effective application of this information helps bridge the gap between customer expectations and product performance.
By embracing technology and fostering a culture of continuous learning, organizations can stay ahead of the curve, delivering innovative products that stand out in the marketplace.
資料ダウンロード
QCD管理受発注クラウド「newji」は、受発注部門で必要なQCD管理全てを備えた、現場特化型兼クラウド型の今世紀最高の受発注管理システムとなります。
ユーザー登録
受発注業務の効率化だけでなく、システムを導入することで、コスト削減や製品・資材のステータス可視化のほか、属人化していた受発注情報の共有化による内部不正防止や統制にも役立ちます。
NEWJI DX
製造業に特化したデジタルトランスフォーメーション(DX)の実現を目指す請負開発型のコンサルティングサービスです。AI、iPaaS、および先端の技術を駆使して、製造プロセスの効率化、業務効率化、チームワーク強化、コスト削減、品質向上を実現します。このサービスは、製造業の課題を深く理解し、それに対する最適なデジタルソリューションを提供することで、企業が持続的な成長とイノベーションを達成できるようサポートします。
製造業ニュース解説
製造業、主に購買・調達部門にお勤めの方々に向けた情報を配信しております。
新任の方やベテランの方、管理職を対象とした幅広いコンテンツをご用意しております。
お問い合わせ
コストダウンが利益に直結する術だと理解していても、なかなか前に進めることができない状況。そんな時は、newjiのコストダウン自動化機能で大きく利益貢献しよう!
(β版非公開)