- お役立ち記事
- How to Enhance Product Strength and Precision by Optimizing Molding Cycle Times
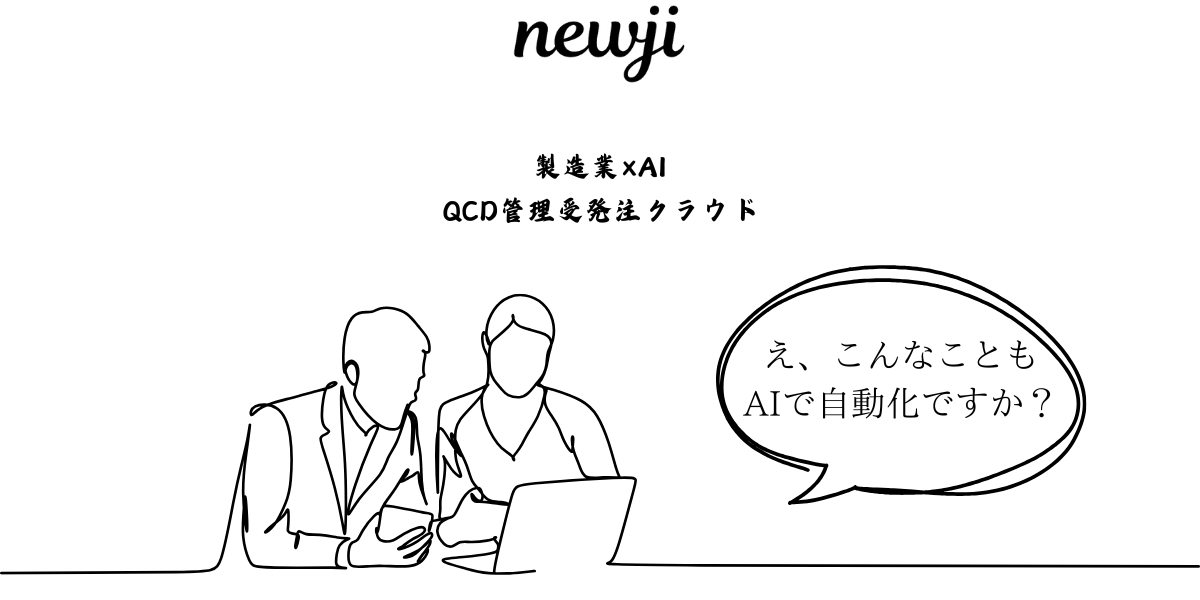
How to Enhance Product Strength and Precision by Optimizing Molding Cycle Times
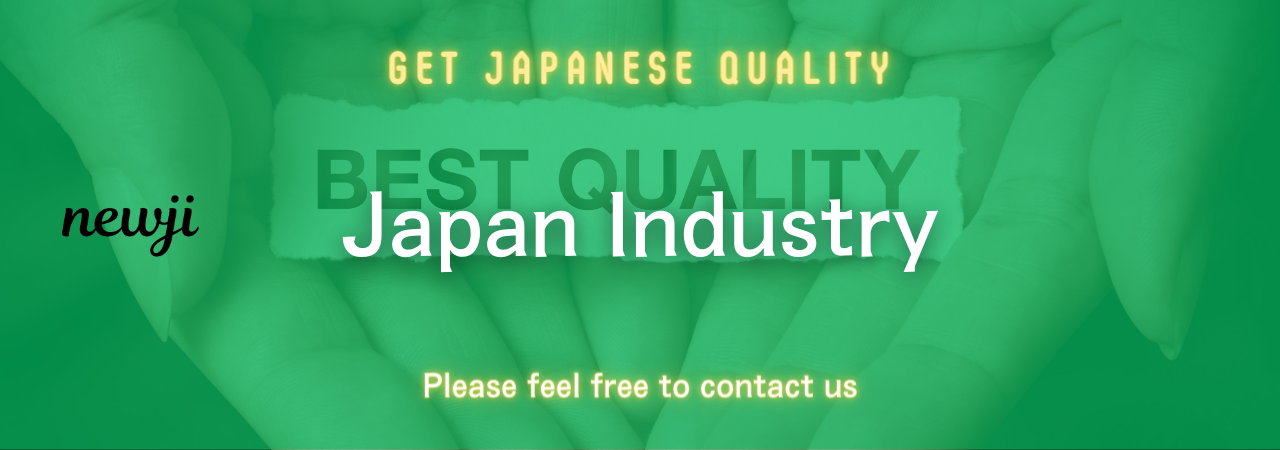
目次
Understanding Molding Cycle Times
Molding cycle time refers to the duration required to produce a single molded part from start to finish in the molding process.
It includes all phases such as filling, cooling, and ejection.
Optimizing these cycle times not only accelerates production but also enhances the strength and precision of the final product.
Getting familiar with this concept is crucial for any business or individual involved in manufacturing.
The overarching goal is to strike a balance that minimizes time without compromising quality.
The Phases of Molding Cycle
Understanding the phases of the molding cycle is fundamental.
Each step involves specific processes that influence both the efficiency and quality of the product.
Filling Phase
This is the initial stage of the molding cycle.
Molten material is injected into the mold cavity, and how quickly and uniformly this fills impacts the eventual shape and size.
Optimizing the speed and pressure can lead to more precise products without defects like warping or air pockets.
Cooling Phase
Once the material fills the mold, it needs to cool and solidify.
The cooling time is a significant part of the cycle that affects both structural integrity and production pace.
Efficient cooling methods reduce cycle time but must be meticulously controlled to prevent any shrinkage or distortion.
Ejection Phase
Once cooled, the product is ejected.
A quick and careful ejection process is essential to maintain the shape and details of the product.
This phase should be optimized to ensure that the product is released without any stress or damage.
Strategies for Optimizing Molding Cycle Times
There are a series of strategies and techniques that can be employed to optimize molding cycle times effectively.
Material Selection
Choosing the right material is crucial.
Different materials have varying melting and cooling rates.
Opt for materials that complement fast cycle times without sacrificing product quality.
Using reinforced or composite materials can also enhance strength and precision.
Mold Design
A well-designed mold is pivotal in reducing cycle times.
Consider factors like wall thickness, cooling channel design, and gate placement.
A uniform wall thickness tends to cool more effectively.
Efficient cooling channels minimize cooling times, and proper gate positioning ensures complete filling.
Process Parameters
Adjusting process parameters like temperature, pressure, and injection speed can lead to significant improvements.
Higher temperatures reduce viscosity, aiding in faster mold filling, but they need to be well-controlled.
Fine-tuning these parameters reduces filling time while maintaining product precision.
Advanced Technologies
Today, technological innovations can significantly optimize cycle times.
Using predictive software for mold simulation helps manufacturers foresee and mitigate potential issues.
Implementing automation can streamline processes, ensuring consistency and speed.
Benefits of Optimizing Molding Cycle Times
Optimizing molding cycle times brings numerous benefits that can significantly enhance your production line.
Increased Production Efficiency
The primary advantage is an obvious boost in production efficiency.
Optimized cycles mean more parts can be made in less time, directly impacting productivity rates and meeting demand more swiftly.
Cost Reduction
Shorter cycle times can equate to cost savings on both labor and energy.
Less production time means lower operational costs, making your manufacturing process more economical.
Improved Product Quality
While reducing cycle times, maintaining quality becomes critical.
The process improvements, while making cycles shorter, contribute to the manufacturing of higher-quality products that meet stringent standards.
Challenges and Solutions
Optimizing mold cycle times comes with its challenges, yet solutions are available.
Identifying these issues early on can streamline the process towards effective optimization.
Balancing Speed and Quality
It’s often challenging to accelerate production without affecting the product’s strength and precision.
This balance is achieved through meticulous testing and adjustment of process parameters and mold design.
Equipment Limitations
Older machinery may not support the advanced techniques required for optimization.
Investing in updated technology can overcome this barrier, enhancing both speed and efficiency.
Employee Training
Ensuring that the team is well-trained in the latest techniques and technologies plays a pivotal role.
Continuous education and training programs bolster knowledge, aiding in better optimization practices.
Conclusion
Optimizing molding cycle times is a highly effective way to enhance product strength and precision.
By understanding the intricacies of the molding cycle and implementing strategic adjustments, manufacturers can achieve faster production without sacrificing quality.
Addressing the challenges through innovation, equipment upgrades, and personnel training will reinforce your capability to optimize effectively.
Staying ahead in the competitive manufacturing industry requires dedication to both efficiency and excellence.
資料ダウンロード
QCD調達購買管理クラウド「newji」は、調達購買部門で必要なQCD管理全てを備えた、現場特化型兼クラウド型の今世紀最高の購買管理システムとなります。
ユーザー登録
調達購買業務の効率化だけでなく、システムを導入することで、コスト削減や製品・資材のステータス可視化のほか、属人化していた購買情報の共有化による内部不正防止や統制にも役立ちます。
NEWJI DX
製造業に特化したデジタルトランスフォーメーション(DX)の実現を目指す請負開発型のコンサルティングサービスです。AI、iPaaS、および先端の技術を駆使して、製造プロセスの効率化、業務効率化、チームワーク強化、コスト削減、品質向上を実現します。このサービスは、製造業の課題を深く理解し、それに対する最適なデジタルソリューションを提供することで、企業が持続的な成長とイノベーションを達成できるようサポートします。
オンライン講座
製造業、主に購買・調達部門にお勤めの方々に向けた情報を配信しております。
新任の方やベテランの方、管理職を対象とした幅広いコンテンツをご用意しております。
お問い合わせ
コストダウンが利益に直結する術だと理解していても、なかなか前に進めることができない状況。そんな時は、newjiのコストダウン自動化機能で大きく利益貢献しよう!
(Β版非公開)