- お役立ち記事
- How to evaluate and reduce inventory risks managed by purchasing departments
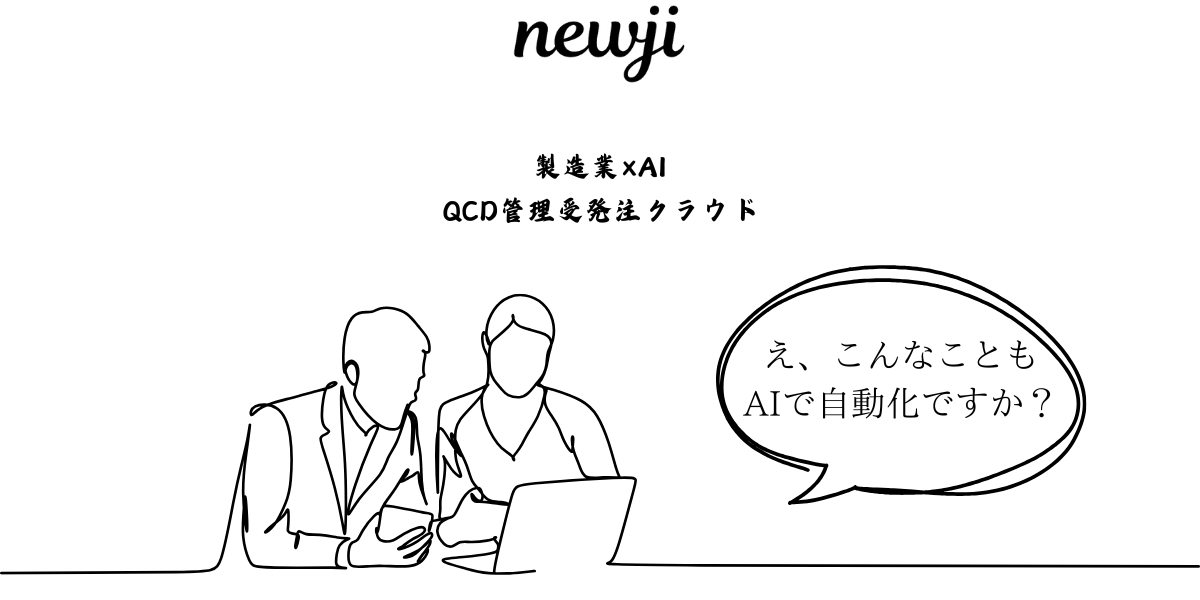
How to evaluate and reduce inventory risks managed by purchasing departments
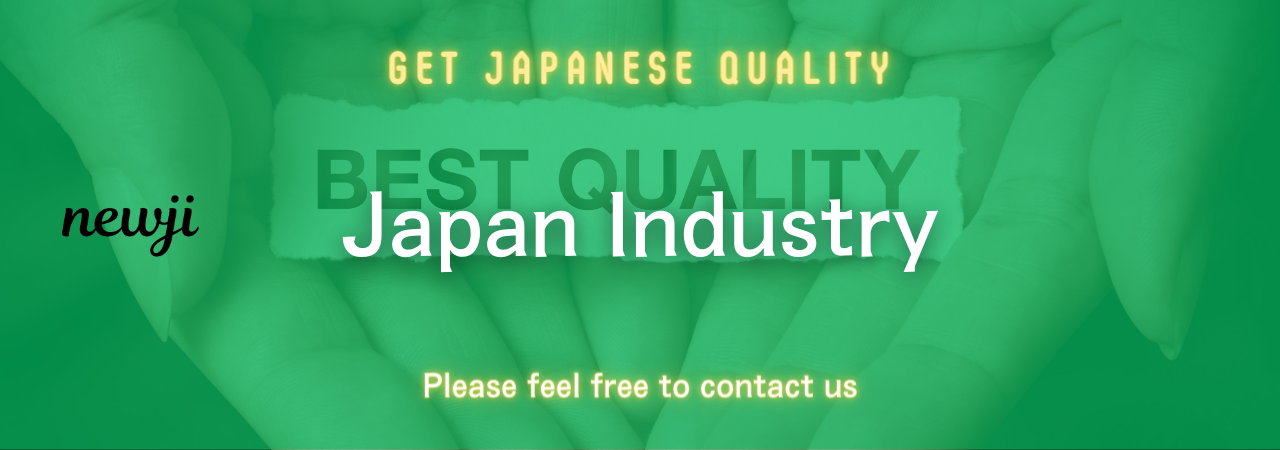
Understanding Inventory Risks in Purchasing Departments
Inventory risks are a significant concern for purchasing departments across various industries.
These risks can include overstocking, understocking, obsolescence, and fluctuating costs.
Effective management of inventory is crucial because it directly impacts a company’s finances and customer satisfaction.
To ensure smooth operations, it’s essential to evaluate and reduce these risks actively.
The Importance of Evaluating Inventory Risks
Evaluating inventory risks allows companies to identify potential threats before they cause significant issues.
By understanding the current inventory status, purchasing departments can make informed decisions on procurement and stock levels.
This process enables the organization to maintain a balance between supply and demand.
It also aids in minimizing unnecessary costs associated with excessive or insufficient inventory.
Assessing these risks helps in optimizing storage space and improving cash flow.
Returned inventory, unsold stock, or expired products all represent wasted resources.
A proper evaluation system reduces these inefficiencies, increasing profitability and efficiency.
Common Types of Inventory Risks
Before diving into strategies for evaluation and reduction, let’s examine some common inventory risks.
**Overstocking:** This occurs when a company holds more stock than needed.
It’s typically due to inaccurate demand forecasting or redundant purchasing.
The excess inventory ties up capital and increases storage costs.
**Understocking:** The opposite of overstocking, this happens when there’s insufficient stock to meet demand.
It results in missed sales opportunities and can damage the company’s reputation.
**Obsolescence:** Products may become outdated or irrelevant over time, especially in technology-driven sectors.
Obsolete inventory represents a loss, as it might need to be sold at a discount or written off entirely.
**Fluctuating Costs:** Volatility in market prices for raw materials or finished goods can lead to unexpected expenses.
This fluctuation affects profit margins and budgeting.
Evaluating Inventory Risks
Effective evaluation of inventory risks involves several critical steps:
1. **Data Analysis:** Collect and analyze historical data on sales, inventory levels, and market trends.
This data provides insights into patterns and aids in accurate forecasting.
2. **Demand Forecasting:** Use statistical methods and tools to predict future demand.
Take into account factors such as seasonality, market conditions, and customer preferences.
3. **Inventory Audits:** Conduct regular audits to assess current inventory status.
Identify slow-moving or obsolete items and take corrective action.
4. **Supplier Collaboration:** Communicate closely with suppliers to understand their capabilities and limitations.
It ensures timely delivery and helps mitigate the risks of understocking or overstocking.
5. **Risk Assessment Models:** Implement risk assessment models to quantify potential risks.
These models assist in making strategic decisions by evaluating scenarios and their possible impact on inventory.
Reducing Inventory Risks
Once you have evaluated the inventory risks, it’s crucial to reduce them effectively through strategic measures.
1. **Optimized Inventory Management Systems:** Invest in reliable inventory management software.
These systems provide real-time updates and facilitate better tracking of inventory levels.
2. **Just-In-Time Inventory:** Adopt a just-in-time inventory approach, reducing the amount of stock held.
This method aligns production schedules with demand forecasts.
3. **Vendor-Managed Inventory:** In cases where strong supplier relationships exist, consider vendor-managed inventory.
Suppliers take responsibility for maintaining inventory levels, reducing the burden on the purchasing department.
4. **Diversifying Suppliers:** Avoid dependency on a single supplier.
Having multiple suppliers reduces the risk of supply disruption.
5. **Regular Training:** Ensure that purchasing staff receives regular training on modern inventory management techniques.
Well-educated staff can better anticipate and handle inventory challenges.
Leveraging Technology for Risk Management
Technology plays a vital role in enhancing the evaluation and management of inventory risks.
1. **ERP Systems:** Enterprise Resource Planning (ERP) systems integrate various business functions, providing a holistic view of inventory.
It aids in demand planning, procurement, and stock control.
2. **AI and Machine Learning:** Utilize AI and machine learning algorithms to improve demand forecasting accuracy.
These technologies can analyze complex data sets and predict trends more precisely.
3. **IoT in Inventory Management:** The Internet of Things (IoT) can enhance tracking and monitoring of inventory.
Real-time data from IoT devices helps in maintaining optimal inventory levels.
4. **Blockchain for Supply Chain Transparency:** Blockchain technology ensures transparency and traceability in supply chains.
It fosters trust between partners and helps mitigate risks associated with fraud or errors.
Continuous Improvement for Long-Term Success
Inventory risk management is not a one-time task but a continuous process.
Regularly reviewing and updating inventory strategies is crucial for long-term success.
1. **Performance Metrics:** Set clear performance metrics to measure the effectiveness of inventory management practices.
Analyze these metrics regularly to identify areas for improvement.
2. **Feedback Loops:** Establish feedback loops between sales, procurement, and logistics teams.
This collaboration ensures that decisions regarding inventory are both informed and swift.
3. **Adapting to Market Changes:** Stay agile and adjust to market changes promptly.
Economic shifts, consumer behavior changes, and technological advancements call for adaptability in inventory strategies.
In conclusion, by understanding, evaluating, and reducing inventory risks, purchasing departments can enhance operational efficiency and profitability.
With the right strategies, tools, and continuous improvement practices, firms can ensure they meet customer demands without overextending resources.
This balanced approach results in a robust and resilient supply chain poised for success.
資料ダウンロード
QCD調達購買管理クラウド「newji」は、調達購買部門で必要なQCD管理全てを備えた、現場特化型兼クラウド型の今世紀最高の購買管理システムとなります。
ユーザー登録
調達購買業務の効率化だけでなく、システムを導入することで、コスト削減や製品・資材のステータス可視化のほか、属人化していた購買情報の共有化による内部不正防止や統制にも役立ちます。
NEWJI DX
製造業に特化したデジタルトランスフォーメーション(DX)の実現を目指す請負開発型のコンサルティングサービスです。AI、iPaaS、および先端の技術を駆使して、製造プロセスの効率化、業務効率化、チームワーク強化、コスト削減、品質向上を実現します。このサービスは、製造業の課題を深く理解し、それに対する最適なデジタルソリューションを提供することで、企業が持続的な成長とイノベーションを達成できるようサポートします。
オンライン講座
製造業、主に購買・調達部門にお勤めの方々に向けた情報を配信しております。
新任の方やベテランの方、管理職を対象とした幅広いコンテンツをご用意しております。
お問い合わせ
コストダウンが利益に直結する術だと理解していても、なかなか前に進めることができない状況。そんな時は、newjiのコストダウン自動化機能で大きく利益貢献しよう!
(Β版非公開)