- お役立ち記事
- How to find a planter OEM manufacturing company
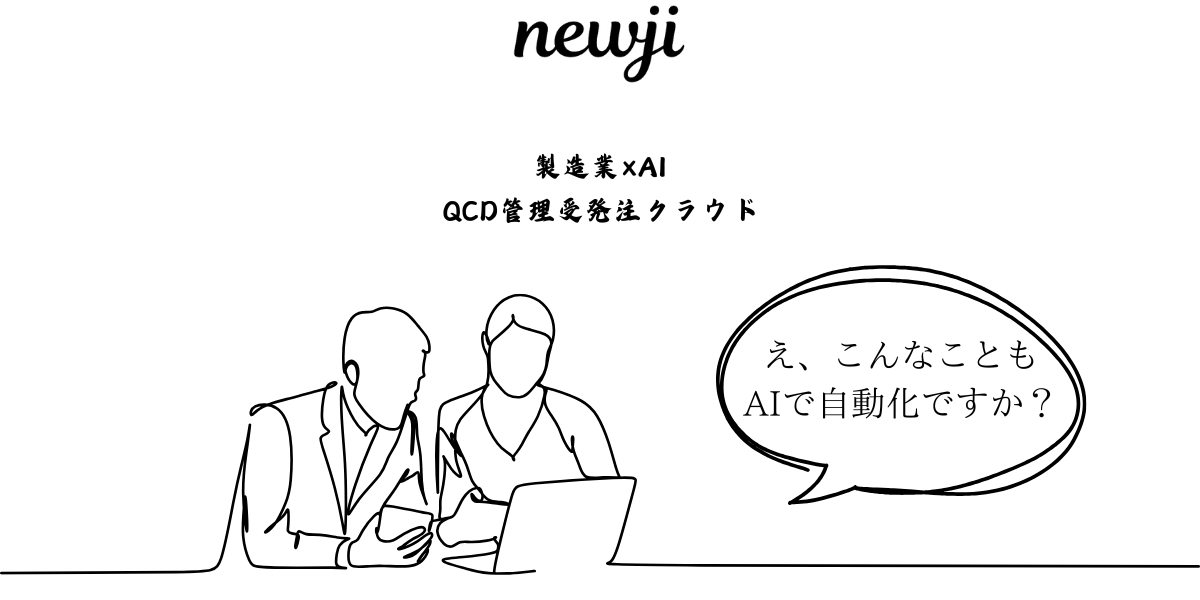
How to find a planter OEM manufacturing company
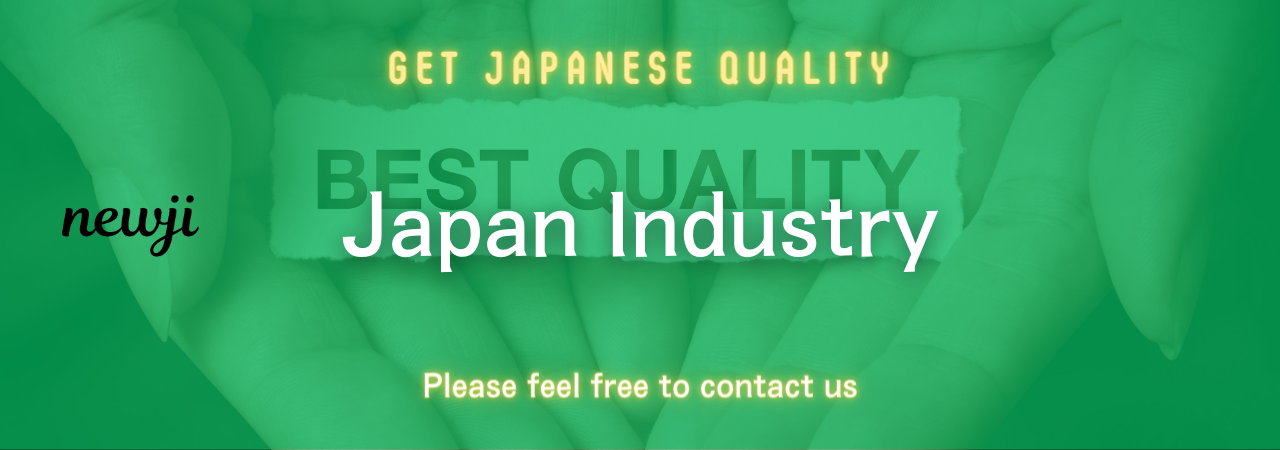
目次
What is an OEM Manufacturing Company?
OEM stands for Original Equipment Manufacturer.
These companies are specialists in creating products that are then marketed by another company under a different brand name.
In the case of planters, an OEM manufacturing company would produce the containers, while another company brands and sells them.
OEMs often have expertise in production processes, quality management, and technical know-how to create a variety of planters that meet different needs and specifications.
Why Choose an OEM for Planters?
Choosing an OEM manufacturer for your planters can offer several advantages.
Firstly, it allows you to focus on your brand and marketing efforts while experts handle the manufacturing side.
OEM companies usually have established processes and technology in place, ensuring efficiency and cost-effectiveness.
Moreover, they can often scale production up or down based on demand, offering more flexibility to your business.
Finally, OEM partners can lend their expertise to innovate and customize your product line, giving you a competitive edge.
Where to Start Your Search for an OEM Manufacturer?
The first step in finding the right planter OEM manufacturing company is research.
Utilize search engines, online directories, and trade association websites to identify potential manufacturers.
Websites like Alibaba, Global Sources, or ThomasNet can provide a list of OEM manufacturers specializing in planters.
Networking with industry peers or attending trade shows specifically related to gardening, horticulture, or manufacturing can also yield important insights and contacts.
Evaluate Potential Manufacturers
Once you have a list of potential OEM manufacturers, the next step is evaluation.
Start by examining their experience in producing planters.
Do they have a good track record?
Customer reviews and testimonials can provide insights into their reliability and quality of work.
Also, check if they have the necessary certifications and comply with industry standards.
Understanding their production capacity is crucial too, as it determines whether they can meet your volume requirements.
Assess Technological Capabilities
Assessing a company’s technological capabilities is key to ensuring they can produce high-quality planters.
Find out what types of materials they specialize in and if they use advanced machinery or technologies that enable efficient production.
3D printing, automated assembly lines, or environmentally friendly production techniques are some indicators of a technologically capable manufacturer.
These capabilities not only influence the quality and design of the planters but can also impact production timelines and costs.
Financial Stability and Longevity
The financial stability and longevity of a manufacturing company are significant factors to consider.
A company that’s been around for a while is likely to have a well-established process and refined expertise.
Furthermore, it’s less likely to face disruptions in delivering orders.
A look at their financial performance might also indicate their ability to invest in new technologies and capacity if needed.
Communication and Culture Compatibility
Effective communication is a pillar of successful business partnerships.
A responsive and communicative OEM manufacturer can address issues promptly, offer solutions when required, and keep the production schedules on track.
Moreover, having a shared understanding or mutual cultural values can influence the smoothness of the partnership.
Transparency, reliability, and mutual respect are crucial elements to look for in a prospective OEM partner.
Quality Assurance and Testing Procedures
Quality assurance is another critical aspect when choosing a planter OEM manufacturing company.
Inquire about their quality control measures and how they test products before they are shipped.
Do they have a dedicated team for quality checks?
What kind of quality certifications do they hold?
Ensuring that the manufacturer maintains high standards will help in reducing defects and returns, ultimately satisfying your customers.
Sample Orders and Prototyping
Before finalizing any agreement, request sample orders or prototypes.
This will give you a hands-on feel of the planter’s quality, design, and durability.
Prototyping can also serve as an opportunity to make any necessary adjustments before full-scale production begins.
It’s an essential step to ensure the manufacturer understands your specifications and requirements fully.
Negotiating Terms and Finalizing Contracts
Once you have narrowed down your choice, it is time to negotiate terms and finalize contracts.
Discuss pricing, payment terms, delivery timelines, and minimum order quantities.
A clear contract should also define the responsibilities of each party, confidentiality agreements, intellectual property rights, and penalty clauses in case of non-compliance.
Having a well-drafted contract minimizes risks and misunderstandings, paving the way for a successful and productive partnership.
Monitoring and Maintaining the Relationship
Building a lasting relationship with your OEM partner is an ongoing process.
Regularly review the performance of the manufacturer against agreed KPIs (Key Performance Indicators).
Always provide feedback on areas requiring improvement and recognize achievements.
Maintaining open lines of communication and addressing any issues proactively can ensure continuous improvement and mutual benefit from the partnership.
In conclusion, finding the right planter OEM manufacturing company requires thorough research, evaluation, and diligent relationship management.
By considering factors such as experience, technological capabilities, communication, and quality assurance measures, you can select an OEM partner that aligns with your business goals and standards.
資料ダウンロード
QCD調達購買管理クラウド「newji」は、調達購買部門で必要なQCD管理全てを備えた、現場特化型兼クラウド型の今世紀最高の購買管理システムとなります。
ユーザー登録
調達購買業務の効率化だけでなく、システムを導入することで、コスト削減や製品・資材のステータス可視化のほか、属人化していた購買情報の共有化による内部不正防止や統制にも役立ちます。
NEWJI DX
製造業に特化したデジタルトランスフォーメーション(DX)の実現を目指す請負開発型のコンサルティングサービスです。AI、iPaaS、および先端の技術を駆使して、製造プロセスの効率化、業務効率化、チームワーク強化、コスト削減、品質向上を実現します。このサービスは、製造業の課題を深く理解し、それに対する最適なデジタルソリューションを提供することで、企業が持続的な成長とイノベーションを達成できるようサポートします。
オンライン講座
製造業、主に購買・調達部門にお勤めの方々に向けた情報を配信しております。
新任の方やベテランの方、管理職を対象とした幅広いコンテンツをご用意しております。
お問い合わせ
コストダウンが利益に直結する術だと理解していても、なかなか前に進めることができない状況。そんな時は、newjiのコストダウン自動化機能で大きく利益貢献しよう!
(Β版非公開)