- お役立ち記事
- How to foster a quality mindset in quality control in manufacturing and how to spread this mindset to the workplace
How to foster a quality mindset in quality control in manufacturing and how to spread this mindset to the workplace
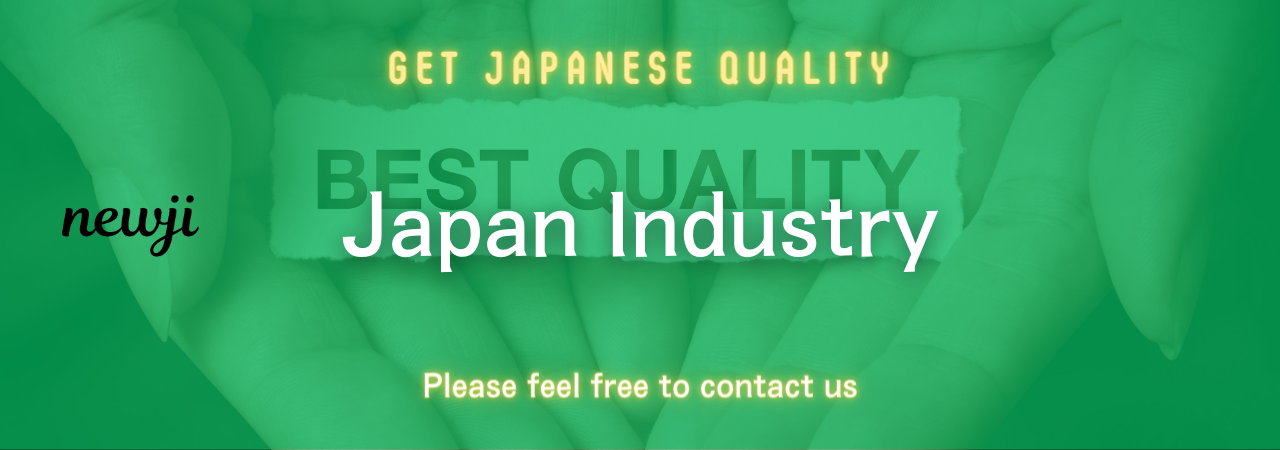
Quality control (QC) is essential in manufacturing to ensure products meet the required standards.
A quality mindset in QC goes beyond routine checks and compliance—it involves a culture where quality is a central value.
Fostering this mindset is crucial for improving product reliability, customer satisfaction, and operational efficiency.
目次
Understanding the Importance of Quality Control in Manufacturing
Quality control in manufacturing ensures that products are made according to specifications and meet customer expectations.
Effective QC can lead to reduced waste, lower costs, and a stronger reputation for the company.
It involves various techniques and processes, such as inspections, testing, and statistical methods, to detect and correct defects.
The Cost of Poor Quality
Poor quality can have significant financial and reputational impacts.
Products that fail to meet standards may result in returns, rework, and recalls, which are costly and time-consuming.
Moreover, consistent quality issues can damage a company’s reputation and erode customer trust.
Fostering a Quality Mindset
Developing a quality mindset starts with leadership and permeates throughout the organization.
Here are some strategies to cultivate this mindset in your workplace:
Leadership Commitment
Leadership must demonstrate a commitment to quality.
This involves setting clear quality goals, providing necessary resources, and embodying quality values.
When employees see that quality is a priority for management, they are more likely to adopt the same attitude.
Employee Training and Education
Regular training and education are essential for developing a quality mindset.
Employees need to understand the importance of quality and how their roles contribute to it.
Ongoing training on QC procedures, industry standards, and continuous improvement techniques can help reinforce this mindset.
Encourage Open Communication
Open communication about quality issues and solutions is vital.
Employees should feel comfortable reporting problems without fear of repercussions.
Encouraging a culture of transparency ensures that issues are identified and addressed promptly.
Involve Employees in Quality Improvements
Engage employees in quality improvement initiatives.
Involving workers in identifying problems and developing solutions can foster a sense of ownership and accountability for quality.
Employee input can provide practical insights and innovative ideas for enhancing QC processes.
Spreading the Quality Mindset
Once a quality mindset is established, it must be consistently promoted to ensure it becomes ingrained in the culture.
Integrate Quality into Daily Activities
Incorporate quality checks and discussions into everyday operations.
Regularly review quality performance metrics and discuss them during team meetings.
Highlighting quality in routine activities reinforces its importance.
Recognize and Reward Quality Efforts
Recognize and reward employees who demonstrate a commitment to quality.
Positive reinforcement can motivate others to prioritize quality in their work.
Implementing a recognition program for quality excellence can create a competitive yet cooperative environment.
Share Success Stories
Sharing success stories related to quality improvements can inspire and motivate the workforce.
Highlighting real-life examples of how quality initiatives have benefited the company can show the tangible impact of a quality mindset.
This can be done through newsletters, meetings, or internal communications platforms.
Develop a Quality-Friendly Work Environment
Create a work environment that supports quality practices.
This includes adequate lighting, organized workspaces, and access to necessary tools and equipment.
A well-maintained environment can reduce errors and facilitate better quality control.
Continuous Improvement and Feedback
A quality mindset is not a one-time initiative but a continuous journey.
Implementing a continuous improvement process is key to maintaining high-quality standards.
Implement a Continuous Improvement Program
Establish a continuous improvement program, such as Lean or Six Sigma.
These programs provide structured methodologies for identifying, analyzing, and solving quality-related issues.
Training employees in these methodologies can empower them to contribute to ongoing improvement efforts.
Conduct Regular Audits and Reviews
Regular audits and reviews help assess QC processes and identify areas for improvement.
Internal audits can ensure compliance with standards and highlight areas where additional training or resources may be needed.
Conducting these audits regularly maintains accountability and keeps quality at the forefront.
Solicit Feedback from Customers and Employees
Feedback from customers and employees is valuable for identifying quality gaps.
Customer feedback can reveal how products are performing in the real world, while employee feedback can provide insights into process inefficiencies.
Acting on this feedback can lead to meaningful improvements.
Leveraging Technology for Quality Control
Incorporating technology into QC processes can enhance accuracy and efficiency.
Automation, data analytics, and other technological advancements can support a quality mindset.
Use Automation for Repetitive Tasks
Automating routine QC tasks can reduce human error and increase efficiency.
Automation can be applied to inspections, measurements, and data collection.
This allows employees to focus on more complex quality-related activities.
Implement Data Analytics
Data analytics can provide valuable insights into quality performance.
Analyzing data from QC processes can help identify trends, predict potential issues, and inform decision-making.
Utilizing data analytics tools can lead to more proactive and effective quality management.
Adopt Advanced Quality Management Systems
Advanced quality management systems (QMS) can integrate various QC processes and provide real-time monitoring.
A QMS can streamline documentation, track compliance, and facilitate continuous improvement.
Investing in a robust QMS can significantly enhance QC capabilities.
In conclusion, fostering a quality mindset in manufacturing requires a concerted effort from leadership, ongoing training, and a supportive culture.
Spreading this mindset throughout the workplace involves regular communication, recognition, and continuous improvement.
Leveraging technology can further enhance QC processes, ensuring high standards are consistently met.
By prioritizing quality at every level, manufacturers can achieve lasting success and customer satisfaction.
資料ダウンロード
QCD調達購買管理クラウド「newji」は、調達購買部門で必要なQCD管理全てを備えた、現場特化型兼クラウド型の今世紀最高の購買管理システムとなります。
ユーザー登録
調達購買業務の効率化だけでなく、システムを導入することで、コスト削減や製品・資材のステータス可視化のほか、属人化していた購買情報の共有化による内部不正防止や統制にも役立ちます。
NEWJI DX
製造業に特化したデジタルトランスフォーメーション(DX)の実現を目指す請負開発型のコンサルティングサービスです。AI、iPaaS、および先端の技術を駆使して、製造プロセスの効率化、業務効率化、チームワーク強化、コスト削減、品質向上を実現します。このサービスは、製造業の課題を深く理解し、それに対する最適なデジタルソリューションを提供することで、企業が持続的な成長とイノベーションを達成できるようサポートします。
オンライン講座
製造業、主に購買・調達部門にお勤めの方々に向けた情報を配信しております。
新任の方やベテランの方、管理職を対象とした幅広いコンテンツをご用意しております。
お問い合わせ
コストダウンが利益に直結する術だと理解していても、なかなか前に進めることができない状況。そんな時は、newjiのコストダウン自動化機能で大きく利益貢献しよう!
(Β版非公開)