- お役立ち記事
- How to implement a supplier data integration system in the manufacturing industry
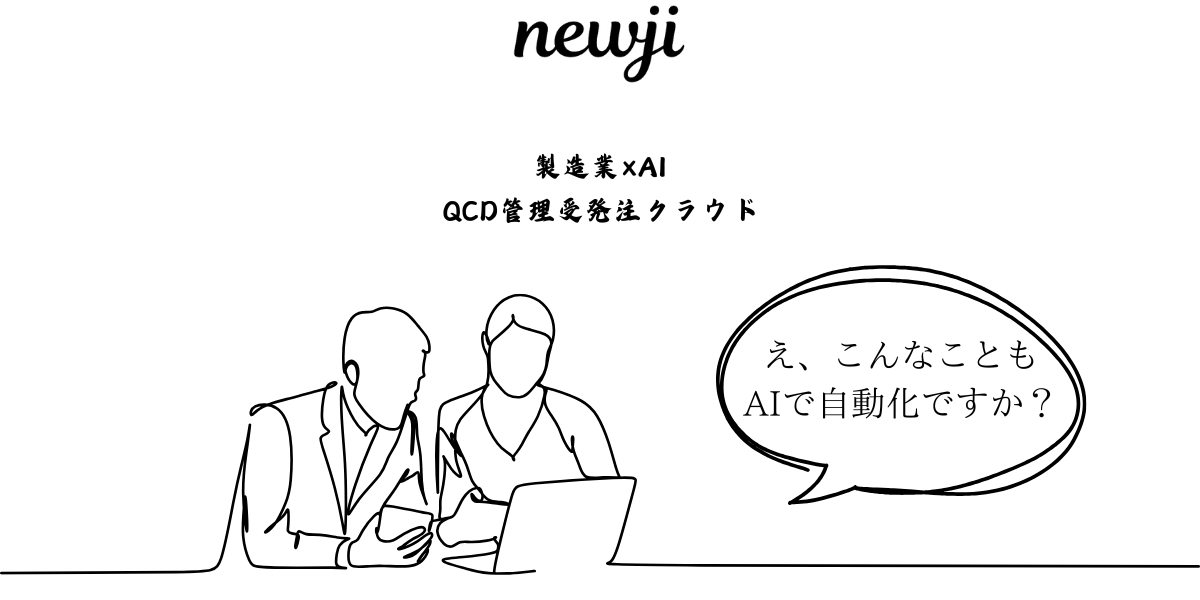
How to implement a supplier data integration system in the manufacturing industry
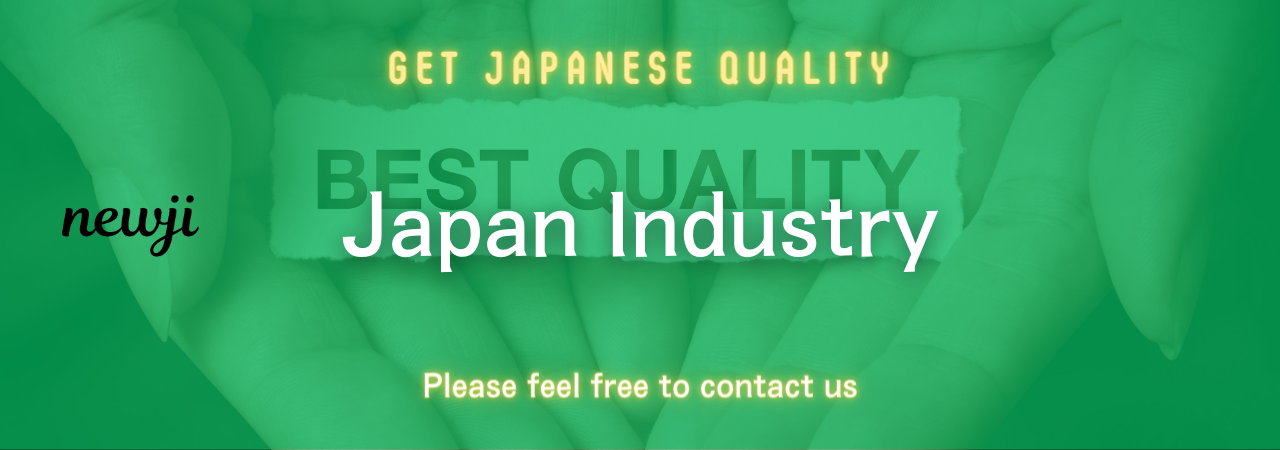
目次
Introduction to Supplier Data Integration
In the manufacturing industry, efficient supplier data integration is crucial for smooth operations, cost savings, and maintaining a competitive edge.
The ability to seamlessly integrate supplier data into a company’s internal systems allows manufacturers to streamline processes, enhance collaboration, and make informed decisions.
This guide will walk you through the essentials of implementing a supplier data integration system effectively.
Understanding the Importance of Supplier Data Integration
Supplier data integration involves consolidating and harmonizing supplier information from various sources into a centralized system.
This process ensures data consistency, improves data quality, and enables real-time data availability across all departments.
Such integration enhances visibility into supply chain operations, allowing manufacturers to mitigate risks, reduce lead times, and optimize inventory management.
Furthermore, an integrated system facilitates better communication with suppliers, leading to improved relationships and collaboration.
Assessing Business Needs and Goals
Before implementing a supplier data integration system, it is essential to clearly understand the business needs and goals.
Identify the specific challenges you face with the current supplier data management processes.
Common issues may include data duplication, inconsistent information, and delayed data entry.
Determine the objectives you aim to achieve with the new system, such as improved accuracy, enhanced reporting capabilities, and reduced operational costs.
Understanding these needs and goals will guide you in selecting the right integration solution.
Choosing the Right Integration Platform
Selecting the right integration platform is a crucial step in the implementation process.
Consider platforms that offer flexibility, scalability, and compatibility with your existing IT infrastructure.
Look for solutions that support various data formats and standards, ensuring that the system can accommodate future changes in supplier data requirements.
Additionally, prioritize platforms with user-friendly interfaces and robust security features to protect sensitive supplier information.
Consulting with technology vendors and conducting thorough research will help you identify the best platform for your manufacturing business.
Evaluating Integration Methods
Various integration methods can be employed depending on the complexity and requirements of your organization.
These include:
– **Point-to-Point Integration:** A direct connection between systems, suitable for simple integration needs.
– **Hub-and-Spoke Integration:** Utilizing a central hub to connect multiple systems, ideal for complex integrations.
– **Bus Integration:** A shared integration layer that connects systems, providing high scalability and flexibility.
Evaluate each method’s pros and cons to determine the most suitable approach for your operations.
Data Mapping and Transformation
Data mapping and transformation are critical components of supplier data integration.
This process involves aligning supplier data fields with your internal system’s data structure to ensure consistency.
Start by conducting a thorough audit of supplier data to identify discrepancies and areas needing correction.
Next, develop a data mapping plan that outlines how data from various sources will be standardized and integrated.
Consider employing data transformation tools to automate this process and maintain data integrity during integration.
Implementing Data Integration Systems
The implementation phase involves setting up the chosen integration platform and configuring it to meet your business needs.
Collaborate with IT experts and suppliers to ensure a smooth integration process.
Begin with a pilot program to test the system’s functionality and identify potential issues.
Monitor the system’s performance, gather feedback, and make necessary adjustments before a full-scale rollout.
Effective training for staff members who will use the system is critical to ensure a seamless transition.
Testing and Validation
Thorough testing and validation are necessary to guarantee that the integration system functions as expected.
Conduct comprehensive tests to verify data accuracy, system compatibility, and performance under different scenarios.
Engage key stakeholders, including suppliers, in the validation process to gather insights and make refinements.
Ensure all data processes meet regulatory and compliance standards before going live.
Monitoring and Maintaining Integration Systems
Once your supplier data integration system is live, continuous monitoring is essential to ensure optimal performance.
Implement regular audits to identify discrepancies, data security issues, or system inefficiencies.
Create a maintenance plan that includes periodic updates, backups, and security checks.
Setting up automated alerts can help in detecting and addressing potential issues promptly.
Regularly review system performance and gather user feedback for continuous improvement.
Benefits of Effective Supplier Data Integration
A well-implemented supplier data integration system offers numerous benefits to manufacturing businesses.
It leads to improved operational efficiency through streamlined processes and reduced manual data entry.
Real-time data access fosters better decision-making, enabling demand forecasting and inventory optimization.
Enhanced collaboration with suppliers results in stronger partnerships and more robust supply chain operations.
Additionally, such integration supports compliance and risk management, safeguarding the business against disruptions.
Conclusion
Implementing a supplier data integration system in the manufacturing industry is a strategic investment with significant rewards.
By understanding your business needs, selecting the right platform, and following best practices, you can achieve a seamless integration that enhances your operations.
The end result is a more agile, efficient, and competitive manufacturing business that can respond to market demands and challenges effectively.
資料ダウンロード
QCD調達購買管理クラウド「newji」は、調達購買部門で必要なQCD管理全てを備えた、現場特化型兼クラウド型の今世紀最高の購買管理システムとなります。
ユーザー登録
調達購買業務の効率化だけでなく、システムを導入することで、コスト削減や製品・資材のステータス可視化のほか、属人化していた購買情報の共有化による内部不正防止や統制にも役立ちます。
NEWJI DX
製造業に特化したデジタルトランスフォーメーション(DX)の実現を目指す請負開発型のコンサルティングサービスです。AI、iPaaS、および先端の技術を駆使して、製造プロセスの効率化、業務効率化、チームワーク強化、コスト削減、品質向上を実現します。このサービスは、製造業の課題を深く理解し、それに対する最適なデジタルソリューションを提供することで、企業が持続的な成長とイノベーションを達成できるようサポートします。
オンライン講座
製造業、主に購買・調達部門にお勤めの方々に向けた情報を配信しております。
新任の方やベテランの方、管理職を対象とした幅広いコンテンツをご用意しております。
お問い合わせ
コストダウンが利益に直結する術だと理解していても、なかなか前に進めることができない状況。そんな時は、newjiのコストダウン自動化機能で大きく利益貢献しよう!
(Β版非公開)