- お役立ち記事
- How to implement WMS for efficient warehouse management
月間76,176名の
製造業ご担当者様が閲覧しています*
*2025年3月31日現在のGoogle Analyticsのデータより
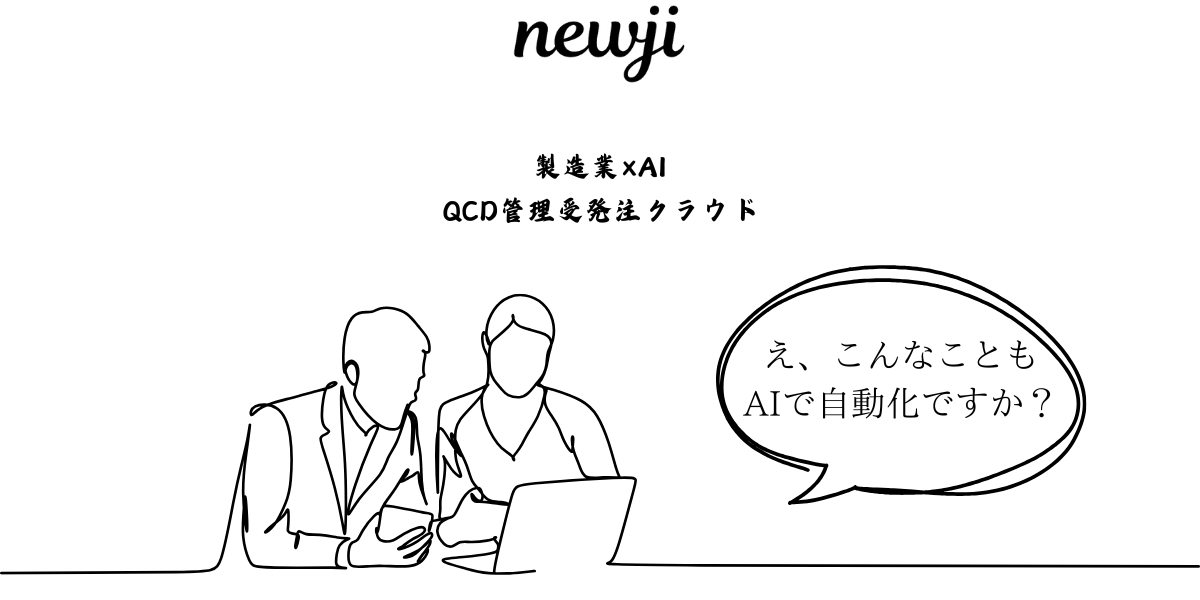
How to implement WMS for efficient warehouse management
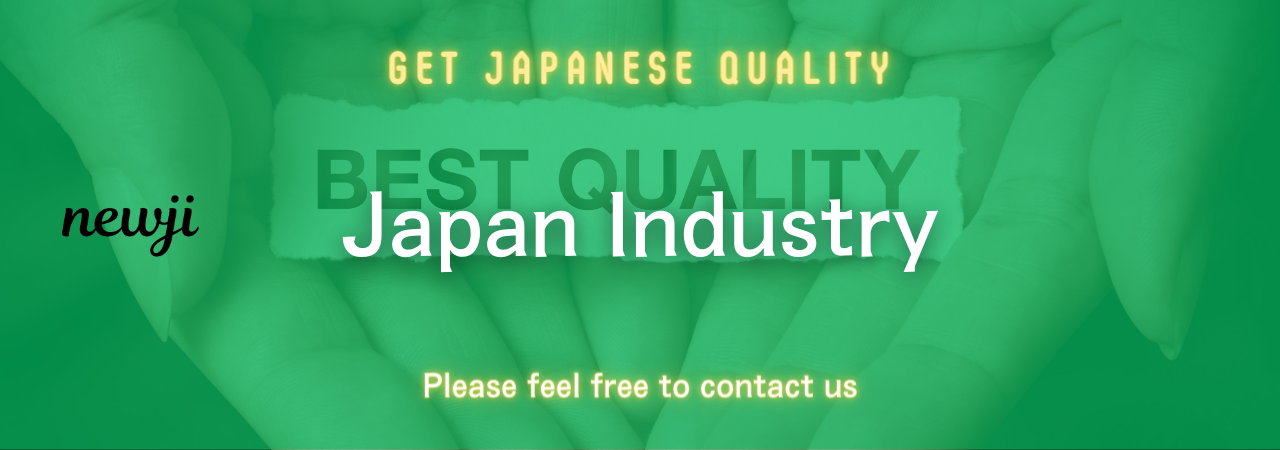
Warehouse Management Systems (WMS) have become indispensable tools in the logistics and supply chain industry.
They help in the efficient handling of every aspect of warehouse operations.
If you are considering implementing a WMS, you are taking a big step towards optimizing your warehouse management.
Here’s a detailed guide on how to effectively implement a WMS for efficient warehouse management.
目次
Understanding the Need for a WMS
Before you dive into the implementation, it’s crucial to understand why you need a WMS in the first place.
A WMS can drastically improve your warehouse operations by automating various tasks.
This includes inventory tracking, order fulfillment, and labor management.
If your warehouse faces challenges like misplaced inventory, delayed shipments, or inefficient labor allocation, a WMS could be the solution.
A well-implemented WMS can increase efficiency, reduce errors, and improve overall customer satisfaction.
Choosing the Right WMS
Assess Your Needs
The first step in implementing a WMS is to thoroughly assess your warehouse needs.
Identify the pain points in your current system.
Do you need better inventory tracking?
Are you looking for improved order accuracy?
Listing these requirements will help guide your selection process.
Research Options
Once you know what you need, start researching different WMS options.
There are various types available, from basic systems to advanced software with numerous features.
Look for systems that offer scalability, integration capabilities, and user-friendly interfaces.
Evaluate Vendors
After narrowing down your options, evaluate different vendors.
Check customer reviews, request demos, and compare prices.
Make sure the vendor has a reliable support system and offers training.
Your investment should not only be in the software but also in the service that comes with it.
Planning the Implementation
Set Clear Objectives
Setting clear objectives is critical for a successful WMS implementation.
What specific goals are you aiming to achieve?
Whether it’s reducing order processing time or improving inventory accuracy, having clear objectives will help you measure success.
Create a Project Team
Form a dedicated project team responsible for the implementation.
This team should include representatives from various departments like IT, operations, and human resources.
Having a diverse team ensures that all viewpoints are considered and that the implementation process runs smoothly.
Develop a Timeline
Create a realistic timeline for the implementation process.
Break down the project into stages, setting milestones and deadlines for each.
This will help you track progress and ensure timely completion.
Data Migration
Migrating your existing data to the new WMS is one of the most critical steps.
Ensure that your data is clean and updated before the migration.
Inaccurate data can lead to costly mistakes.
Back Up Data
Before you start migrating data, make sure to back it up.
This will protect you from any potential data loss during the migration process.
Data Mapping
Map your existing data fields to the new WMS.
This ensures that all data is correctly transferred and fits into the new system seamlessly.
Test the Data
Conduct thorough testing to ensure that all data has migrated correctly.
This step will help you catch any errors before the system goes live.
Training and Testing
Once the WMS is set up and your data is migrated, it’s time to train your staff.
Training is crucial for maximizing the benefits of your new system.
Comprehensive Training
Provide comprehensive training to all employees who will be using the WMS.
This includes hands-on sessions and detailed manuals.
A well-trained staff will be more comfortable with the new system, leading to fewer errors and higher efficiency.
System Testing
Before rolling out the WMS fully, conduct extensive system testing.
This includes testing all functionalities, from receiving and inventory management to order fulfillment and shipping.
System testing ensures that everything is working as expected and allows you to identify and fix any issues.
Go Live
After successful testing and training, it’s time to go live with your new WMS.
However, the go-live process should be well-coordinated to avoid disruptions.
Soft Launch
Consider a soft launch before going fully live.
This involves running the WMS in parallel with your existing system for a short period.
A soft launch helps identify any unforeseen issues and provides an additional safety net.
Monitor and Support
Once the WMS is live, closely monitor its performance.
Have a support team ready to address any issues immediately.
Constant monitoring ensures that any problems are promptly resolved, minimizing disruptions.
Measure Success
Post-implementation, it’s important to measure the success of your new WMS.
Compare the performance metrics to the objectives you initially set.
Key Performance Indicators (KPIs)
Identify key performance indicators that align with your objectives.
This could include metrics like order processing time, inventory accuracy, and labor efficiency.
Regularly review these KPIs to gauge the success of your WMS.
Continuous Improvement
Implementing a WMS is not a one-time task.
Continuously gather feedback from your staff and make necessary adjustments.
Regular system updates and training sessions can help keep your WMS running smoothly and efficiently.
Implementing a WMS for efficient warehouse management may seem daunting.
However, with careful planning, thorough training, and continuous monitoring, you can significantly improve your warehouse operations.
By following these steps, you’ll be on your way to achieving a more efficient, error-free, and streamlined warehouse management system.
資料ダウンロード
QCD管理受発注クラウド「newji」は、受発注部門で必要なQCD管理全てを備えた、現場特化型兼クラウド型の今世紀最高の受発注管理システムとなります。
ユーザー登録
受発注業務の効率化だけでなく、システムを導入することで、コスト削減や製品・資材のステータス可視化のほか、属人化していた受発注情報の共有化による内部不正防止や統制にも役立ちます。
NEWJI DX
製造業に特化したデジタルトランスフォーメーション(DX)の実現を目指す請負開発型のコンサルティングサービスです。AI、iPaaS、および先端の技術を駆使して、製造プロセスの効率化、業務効率化、チームワーク強化、コスト削減、品質向上を実現します。このサービスは、製造業の課題を深く理解し、それに対する最適なデジタルソリューションを提供することで、企業が持続的な成長とイノベーションを達成できるようサポートします。
製造業ニュース解説
製造業、主に購買・調達部門にお勤めの方々に向けた情報を配信しております。
新任の方やベテランの方、管理職を対象とした幅広いコンテンツをご用意しております。
お問い合わせ
コストダウンが利益に直結する術だと理解していても、なかなか前に進めることができない状況。そんな時は、newjiのコストダウン自動化機能で大きく利益貢献しよう!
(β版非公開)