- お役立ち記事
- How to improve manufacturing productivity with experimental design
月間77,185名の
製造業ご担当者様が閲覧しています*
*2025年2月28日現在のGoogle Analyticsのデータより
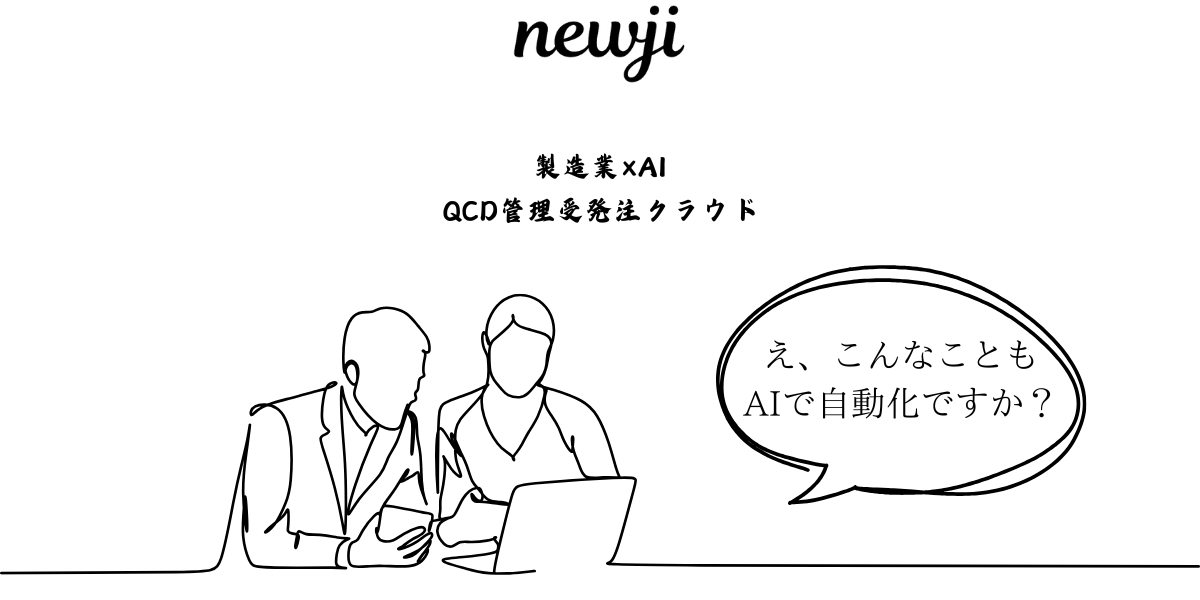
How to improve manufacturing productivity with experimental design
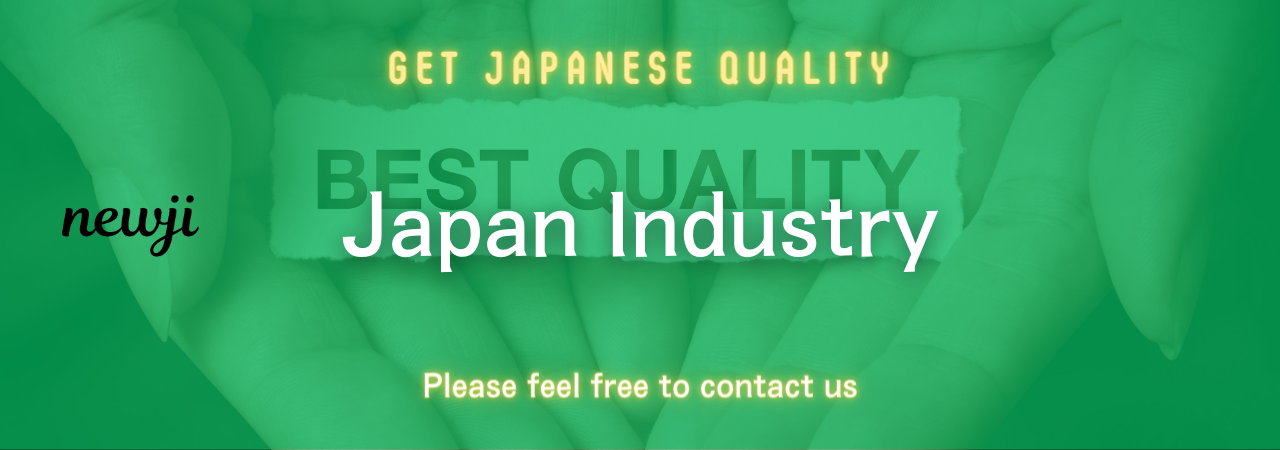
目次
Understanding Experimental Design
To improve manufacturing productivity, it’s crucial to understand the concept of experimental design.
At its core, experimental design is a statistical approach used to determine the relationship between factors affecting a process and the output of that process.
It helps in identifying cause-and-effect relationships by systematically changing the inputs and observing the changes in output.
In manufacturing, various factors such as temperature, pressure, and raw materials can influence productivity.
By employing experimental design, manufacturers can pinpoint which factors have the most significant impact and optimize them to improve productivity.
The Importance of Experimental Design in Manufacturing
Manufacturers face numerous challenges, including maintaining high quality and reducing costs.
Experimental design plays a vital role by providing insights that lead to informed decision-making.
Rather than relying on guesswork, manufacturers can use experimental design to test hypotheses and obtain data-driven results.
This approach minimizes waste and maximizes efficiency.
When manufacturers understand which factors contribute to inefficiencies, they can implement targeted improvements.
As a result, productivity increases, and the overall production process becomes more streamlined.
Steps to Implement Experimental Design
1. Define the Problem
The first step in implementing experimental design is to clearly define the problem.
Identify the specific issue or aspect of the manufacturing process that needs improvement.
Whether it’s reducing defects or increasing the speed of production, having a clear problem statement guides the entire process.
2. Select Factors and Levels
Once the problem is defined, the next step is to select the factors that might impact the process.
These could include variables like temperature, time, or machinery settings.
Determine the different levels at which each factor will be tested.
For instance, if temperature is a factor, levels could be set at low, medium, and high.
3. Design the Experiment
Designing the experiment is crucial and involves planning the series of tests that will be conducted.
There are various designs to choose from, including full factorial, fractional factorial, and response surface methodology.
The choice depends on the complexity of the process and the number of factors involved.
4. Conduct the Experiment
With the design in place, it’s time to conduct the actual experiments.
Ensure that the tests are carried out consistently and under controlled conditions to prevent external influences from skewing the data.
Accurate data collection is key to obtaining reliable results.
5. Analyze the Data
After the experiments are conducted, analyze the data to determine which factors significantly impact productivity.
Statistical software can help in visualizing the data and understanding complex interactions between different variables.
Interpreting these results allows manufacturers to make informed decisions about process improvements.
Real-World Applications of Experimental Design
Experimental design is not just a theoretical concept; it has practical applications that many industries benefit from.
For example, in automotive manufacturing, experimental design helps in optimizing assembly line processes to enhance speed and efficiency.
Similarly, in the food industry, it aids in improving the quality and consistency of products by refining cooking and packaging processes.
Another application is in electronics manufacturing, where experimental design can reduce defects and improve yields by optimizing component assembly methods.
By implementing findings from an experimental design, companies can achieve better product quality and increase customer satisfaction.
Benefits of Using Experimental Design in Manufacturing
1. Enhanced Efficiency
One of the primary benefits of using experimental design in manufacturing is increased efficiency.
By identifying and focusing on the critical factors affecting productivity, manufacturers can implement changes that streamline operations and reduce waste.
2. Cost Reduction
With improved processes come cost savings.
By reducing material wastage and minimizing downtime, manufacturers can lower production costs significantly.
Experimental design helps in achieving these savings by highlighting inefficiencies and suggesting optimal operational conditions.
3. Quality Improvement
Experimental design also leads to improvements in product quality.
By understanding how different variables affect the end product, manufacturers can make necessary adjustments to enhance quality.
This proactive approach reduces defects and maintains high standards.
4. Informed Decision-Making
Experimental design empowers manufacturers to make decisions based on data rather than intuition.
This leads to more consistent and reliable outcomes.
With a clear understanding of the factors that influence productivity, manufacturers can strategically plan future innovations and expansions.
Challenges in Implementing Experimental Design
While the benefits are clear, implementing experimental design does come with challenges.
One significant challenge is the initial time and resource investment needed to conduct experiments and analyze data.
Manufacturers must be prepared to allocate resources and time for these activities.
Another challenge is the learning curve associated with understanding and applying statistical methods.
To overcome this, manufacturers may need to invest in training or hire experts in statistics and experimental design.
Despite these challenges, the long-term gains from improved productivity and efficiency outweigh the initial hurdles.
Conclusion
Improving manufacturing productivity is a complex task, but using experimental design offers a structured and effective approach.
By systematically testing and analyzing factors, manufacturers can make data-driven decisions that lead to significant improvements in efficiency, cost savings, quality, and overall productivity.
Embracing experimental design not only enhances current manufacturing processes but also paves the way for future innovations and competitive advantages.
資料ダウンロード
QCD管理受発注クラウド「newji」は、受発注部門で必要なQCD管理全てを備えた、現場特化型兼クラウド型の今世紀最高の受発注管理システムとなります。
ユーザー登録
受発注業務の効率化だけでなく、システムを導入することで、コスト削減や製品・資材のステータス可視化のほか、属人化していた受発注情報の共有化による内部不正防止や統制にも役立ちます。
NEWJI DX
製造業に特化したデジタルトランスフォーメーション(DX)の実現を目指す請負開発型のコンサルティングサービスです。AI、iPaaS、および先端の技術を駆使して、製造プロセスの効率化、業務効率化、チームワーク強化、コスト削減、品質向上を実現します。このサービスは、製造業の課題を深く理解し、それに対する最適なデジタルソリューションを提供することで、企業が持続的な成長とイノベーションを達成できるようサポートします。
製造業ニュース解説
製造業、主に購買・調達部門にお勤めの方々に向けた情報を配信しております。
新任の方やベテランの方、管理職を対象とした幅広いコンテンツをご用意しております。
お問い合わせ
コストダウンが利益に直結する術だと理解していても、なかなか前に進めることができない状況。そんな時は、newjiのコストダウン自動化機能で大きく利益貢献しよう!
(β版非公開)