- お役立ち記事
- How to Improve Product Precision with Optimal Injection Speed Settings
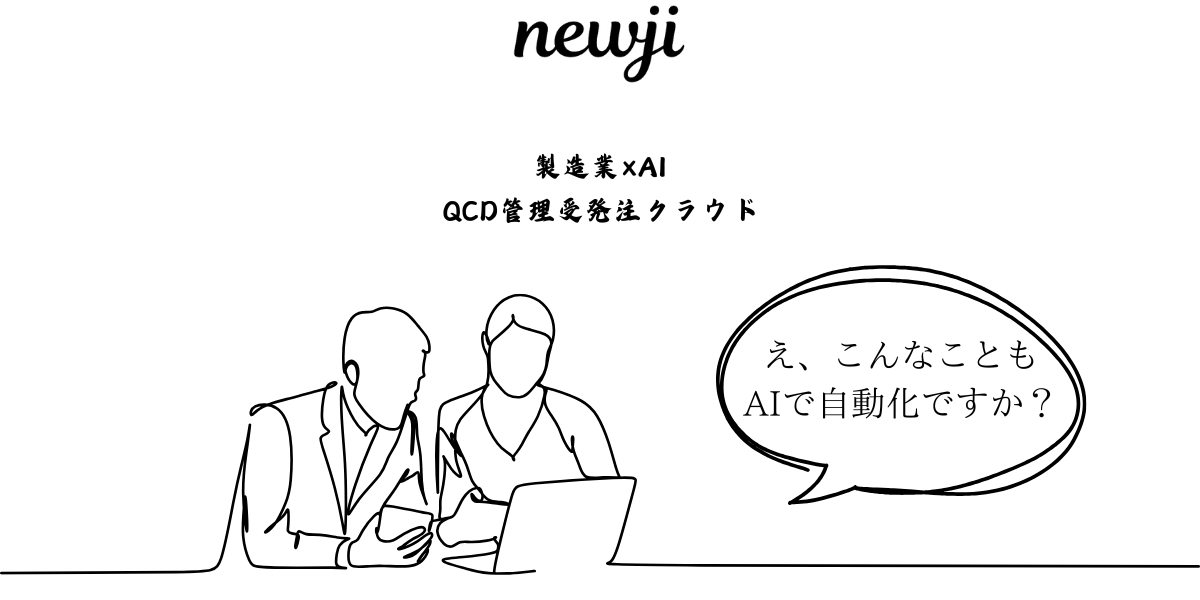
How to Improve Product Precision with Optimal Injection Speed Settings
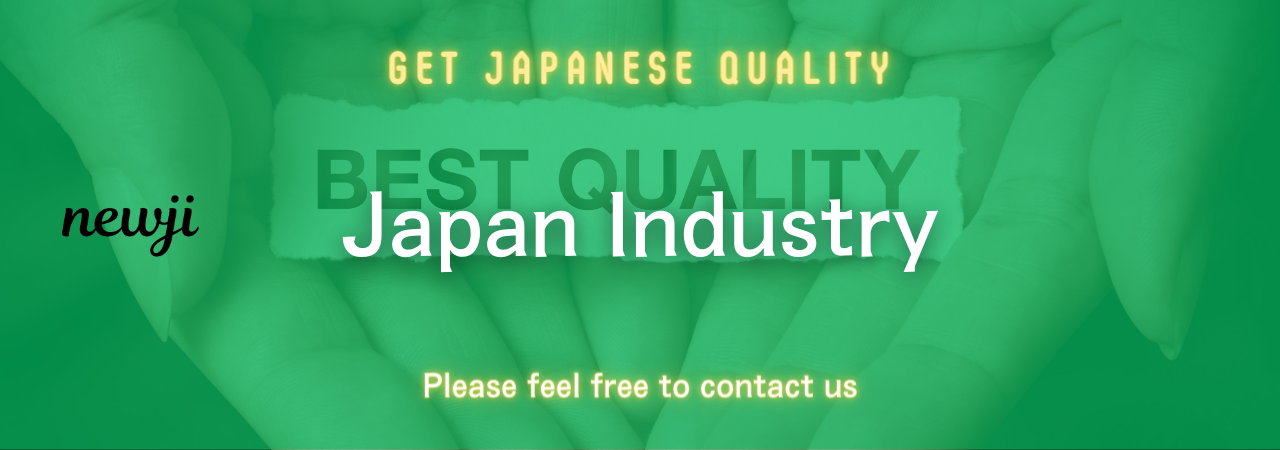
目次
Understanding the Importance of Injection Speed
Injection molding is a popular manufacturing process used to create a variety of products, from plastic bottles to automobile parts.
A critical aspect of injection molding is the setting of the injection speed.
This refers to the speed at which molten material is injected into a mold.
Properly setting the injection speed is crucial as it directly affects the precision and quality of the final product.
Adjusting the injection speed helps ensure that the mold is filled properly, which minimizes defects such as warping, incomplete filling, or surface imperfections.
Understanding and optimizing this aspect can greatly improve the overall efficiency of the production process.
Factors Influencing Optimal Injection Speed
Several factors come into play when determining the optimal injection speed for a product.
One of the primary considerations is the type of material being used.
Different materials have varying viscosities and flow characteristics, which affect how they behave during the injection process.
Another factor is the complexity and size of the mold itself.
Larger or more intricate molds may require slower speeds to ensure that the material fills every detail evenly.
In addition, the desired surface finish and part precision can also influence speed settings.
Components that require high precision may benefit from more controlled, gradual filling, while those with simpler designs might allow for faster injection speeds.
The Impact of Material Properties
Understanding the properties of the material you are working with is essential for setting the right injection speed.
Thermoplastics, for instance, have particular melt viscosities that define how they flow under pressure.
Some thermoplastics need rapid injection speeds to prevent premature cooling and incomplete fills, while others might necessitate slower speeds to avoid excessive shear forces that could compromise the material’s structural integrity.
Similarly, thermosetting polymers may require a different approach since their chemical reactions during curing can be influenced by injection speed.
Knowing these properties helps in selecting an appropriate speed that enhances product precision.
Techniques for Determining Optimal Injection Speed
Achieving the most effective injection speed involves a combination of empirical testing and advanced simulation tools.
The empirical approach may involve conducting preliminary trials and closely observing the outcomes.
By adjusting the injection speed incrementally and evaluating the quality of the molded parts, manufacturers can gradually home in on the ideal settings.
However, this method can be time-consuming and costly due to the wastage of materials.
On the other hand, using simulation tools like mold flow analysis software provides a more efficient path.
These tools allow for virtual testing by simulating how different speed settings would affect material flow within a mold.
This can significantly reduce trial-and-error and is a cost-effective way to predict and enhance the behavior of materials during the process, leading to better precision in the final product.
The Role of Machine Capabilities
Injection molding machines play an essential role in setting and maintaining the optimal injection speed.
Modern machines often come with programmable control systems that allow for highly precise manipulation of speed settings.
These systems can be equipped with sensors that provide real-time feedback, allowing for adjustments during the injection process.
Utilizing such advanced capabilities enables operators to maintain consistent speed that adheres closely to the defined optimal settings, ultimately ensuring a high level of product quality and precision.
Common Challenges and How to Overcome Them
While determining the optimal injection speed can greatly enhance product precision, there are common challenges that manufacturers may face.
One such challenge is balancing speed with cycle time.
Higher speeds may reduce cycle time but could lead to issues like flash or burn marks on the part.
Conversely, slower speeds can improve part quality but might extend the cycle time too much, impacting production efficiency.
Addressing these challenges involves finding a middle ground where speed is optimized without compromising on quality or efficiency.
Another challenge can be the variability of the raw materials, where the same material from different batches might behave slightly differently.
Implementing a robust quality control system and maintaining a buffer inventory can mitigate the impact of such variability.
Importance of Operator Training
Ensuring that operators are adequately trained in using the machines and understanding the material properties is crucial.
Trained operators can make real-time adjustments and recognize potential issues early on, preventing unscheduled downtimes or large-scale defects.
Training programs should emphasize the significance of setting the right injection speeds and interpreting data from sensors and control systems for precise and efficient production.
Conclusion: Striving for Precision
In conclusion, improving product precision in injection molding starts with understanding and setting the optimal injection speed.
By considering factors like material properties, machine capabilities, and mold complexity, manufacturers can set appropriate speed parameters.
Employing advanced techniques such as simulations and implementing consistent quality control systems further aids in refining the speed settings.
Overcoming challenges related to speed settings requires a balance between speed and efficiency, increased operator expertise, and a proactive approach to problem-solving.
Striving for optimal precision not only enhances the quality of products but also contributes to the overall success and sustainability of manufacturing operations.
資料ダウンロード
QCD調達購買管理クラウド「newji」は、調達購買部門で必要なQCD管理全てを備えた、現場特化型兼クラウド型の今世紀最高の購買管理システムとなります。
ユーザー登録
調達購買業務の効率化だけでなく、システムを導入することで、コスト削減や製品・資材のステータス可視化のほか、属人化していた購買情報の共有化による内部不正防止や統制にも役立ちます。
NEWJI DX
製造業に特化したデジタルトランスフォーメーション(DX)の実現を目指す請負開発型のコンサルティングサービスです。AI、iPaaS、および先端の技術を駆使して、製造プロセスの効率化、業務効率化、チームワーク強化、コスト削減、品質向上を実現します。このサービスは、製造業の課題を深く理解し、それに対する最適なデジタルソリューションを提供することで、企業が持続的な成長とイノベーションを達成できるようサポートします。
オンライン講座
製造業、主に購買・調達部門にお勤めの方々に向けた情報を配信しております。
新任の方やベテランの方、管理職を対象とした幅広いコンテンツをご用意しております。
お問い合わせ
コストダウンが利益に直結する術だと理解していても、なかなか前に進めることができない状況。そんな時は、newjiのコストダウン自動化機能で大きく利益貢献しよう!
(Β版非公開)