- お役立ち記事
- How to Improve Product Quality with Mold Design for Insert Molding
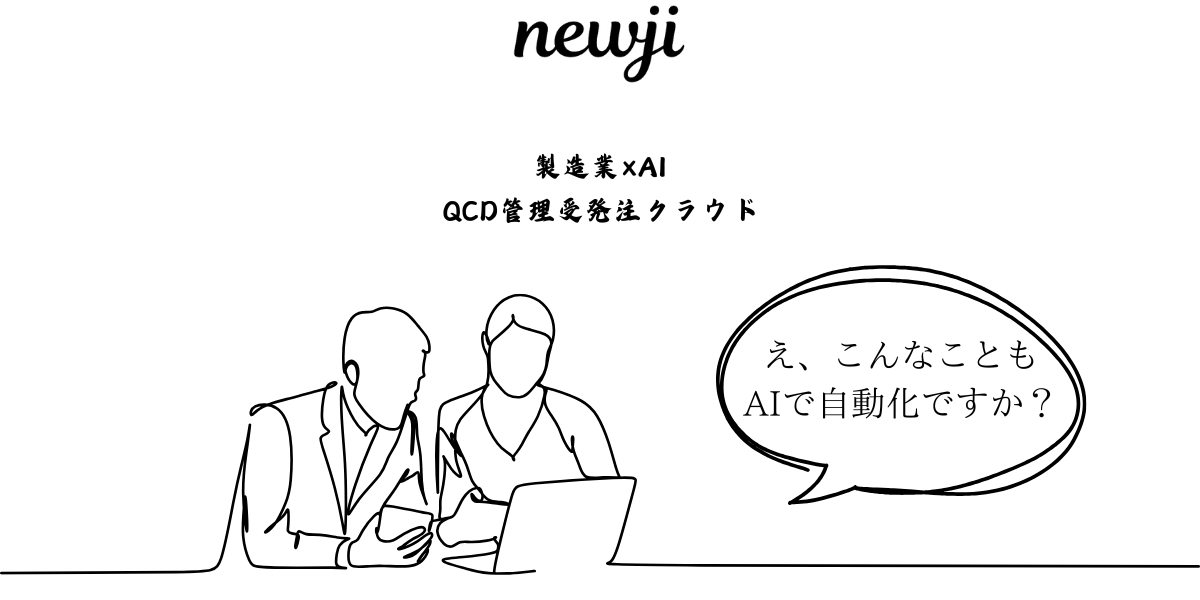
How to Improve Product Quality with Mold Design for Insert Molding
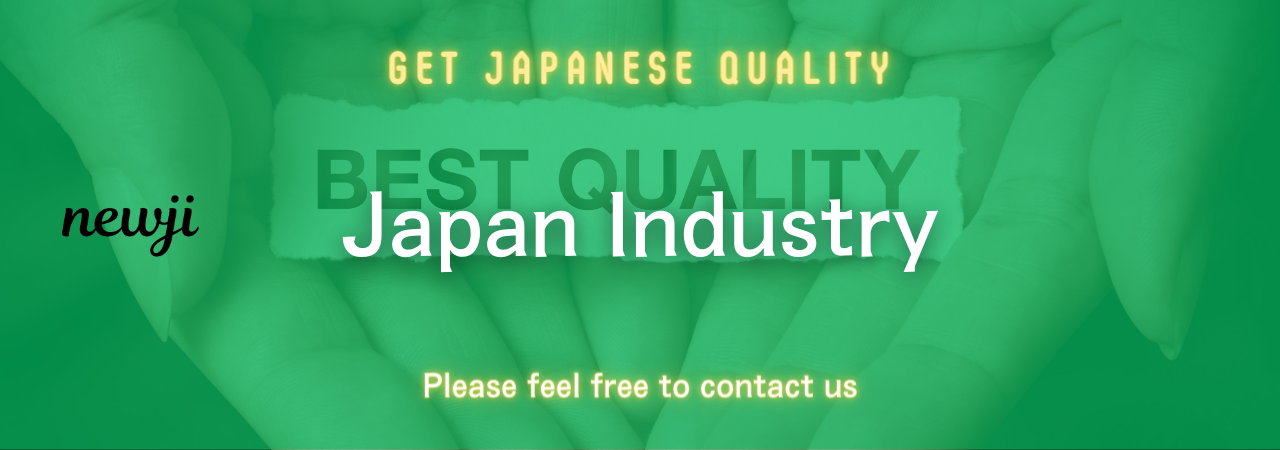
目次
Understanding Insert Molding
Insert molding is a powerful manufacturing process, adored for its ability to combine multiple materials into a single, cohesive product.
This method is particularly useful in enhancing product functionality while minimizing assembly processes.
By embedding components such as metal parts within a mold before injecting the plastic, the bond formed is incredibly strong.
This technology is predominantly employed in producing medical devices, electronic components, and automotive parts.
These sectors demand high durability, which insert molding can consistently deliver.
The Role of Mold Design
Quality products start with quality mold designs.
In insert molding, the mold design plays a pivotal role in the final product’s quality.
A well-designed mold ensures that the inserts are correctly positioned and held securely.
This accuracy prevents movement during the injection process, which in turn eliminates common issues such as misalignment and weak bonds.
A thoughtful mold design will also take into account the thermal and mechanical properties of the materials used, including plastic flow patterns.
The key to effective mold design is attention to detail and understanding of the mold’s specific interactions with the chosen materials.
Key Factors to Consider in Mold Design
Several essential factors need consideration during mold design to improve product quality in insert molding.
Selecting the Right Materials
Choosing the appropriate materials for both the inserts and the plastic is crucial.
Different materials have unique melting points, which affect how they behave during the molding process.
Consult material data sheets to understand their properties and compatibility.
By selecting materials with compatible thermal expansion rates, you minimize the risk of cracking or deforming the final product.
Precision in Insert Placement
The accuracy of insert placement cannot be overstated.
Any deviation will likely result in a flawed product.
Therefore, the mold must include precise cavities or grooves where the inserts are positioned.
Computer-aided design (CAD) software is invaluable for achieving the precision necessary.
Using CAD, designers can visualize the entire molding process, ensuring that all parts interconnect seamlessly.
Optimizing Gate Location
The gate location in the mold significantly affects the flow of plastic material.
Ideally, the gate should be located on an unnoticeable part of the product to maintain aesthetic quality.
Strategic gate placement improves material distribution and reduces the stress on the insert.
This optimization helps in maintaining the structural integrity of both the insert and the surrounding plastic, ensuring a more durable product.
Mold Cooling System
An efficient cooling system is vital for controlling the mold’s temperature.
Proper cooling minimizes cycle time, streamlines production, and ensures consistent product quality.
The cooling system needs to be designed to maintain uniform temperature, preventing hotspots that might lead to warping or uneven shrinkage in the final product.
Improving Product Quality with Advanced Techniques
Beyond the basics of mold design, there are several more advanced techniques that can further enhance product quality.
Utilizing Simulation Software
Simulation software provides a predictive model of how the plastic will behave during the molding process.
This foresight allows designers to anticipate potential defects and address them proactively.
Predictive analysis can significantly reduce trial and error, saving time and resources in the development phase.
Implementing Quality Control Measures
Consistent quality control is essential to maintaining high product standards.
Incorporate inspections at various stages of production to catch defects early.
Techniques such as statistical process control and automated visual inspection can detect inconsistencies that might affect product quality over time.
Incorporating Design for Manufacturability (DFM)
Design for Manufacturability is a design approach that simplifies the manufacturing process and reduces production costs while maintaining quality.
By integrating DFM principles, you ensure that the design is efficient, cost-effective, and reproducible on a large scale.
This process includes assessing the design from the manufacturing perspective to eliminate unnecessary complexity.
Conclusion
Improving product quality with mold design for insert molding is a multifaceted process that requires careful consideration of materials, precision in design, and strategic planning.
By understanding and implementing the key components of effective mold design, manufacturers can create high-quality products that meet industry standards.
Incorporating advanced techniques such as simulation software and robust quality control ensures that the insert molding process yields durable and reliable products.
Ultimately, attention to detail and a commitment to quality in mold design will lead to successful insert molding outcomes that benefit both manufacturers and consumers alike.
資料ダウンロード
QCD調達購買管理クラウド「newji」は、調達購買部門で必要なQCD管理全てを備えた、現場特化型兼クラウド型の今世紀最高の購買管理システムとなります。
ユーザー登録
調達購買業務の効率化だけでなく、システムを導入することで、コスト削減や製品・資材のステータス可視化のほか、属人化していた購買情報の共有化による内部不正防止や統制にも役立ちます。
NEWJI DX
製造業に特化したデジタルトランスフォーメーション(DX)の実現を目指す請負開発型のコンサルティングサービスです。AI、iPaaS、および先端の技術を駆使して、製造プロセスの効率化、業務効率化、チームワーク強化、コスト削減、品質向上を実現します。このサービスは、製造業の課題を深く理解し、それに対する最適なデジタルソリューションを提供することで、企業が持続的な成長とイノベーションを達成できるようサポートします。
オンライン講座
製造業、主に購買・調達部門にお勤めの方々に向けた情報を配信しております。
新任の方やベテランの方、管理職を対象とした幅広いコンテンツをご用意しております。
お問い合わせ
コストダウンが利益に直結する術だと理解していても、なかなか前に進めることができない状況。そんな時は、newjiのコストダウン自動化機能で大きく利益貢献しよう!
(Β版非公開)