- お役立ち記事
- How to improve product quality with parts traceability management led by the purchasing department
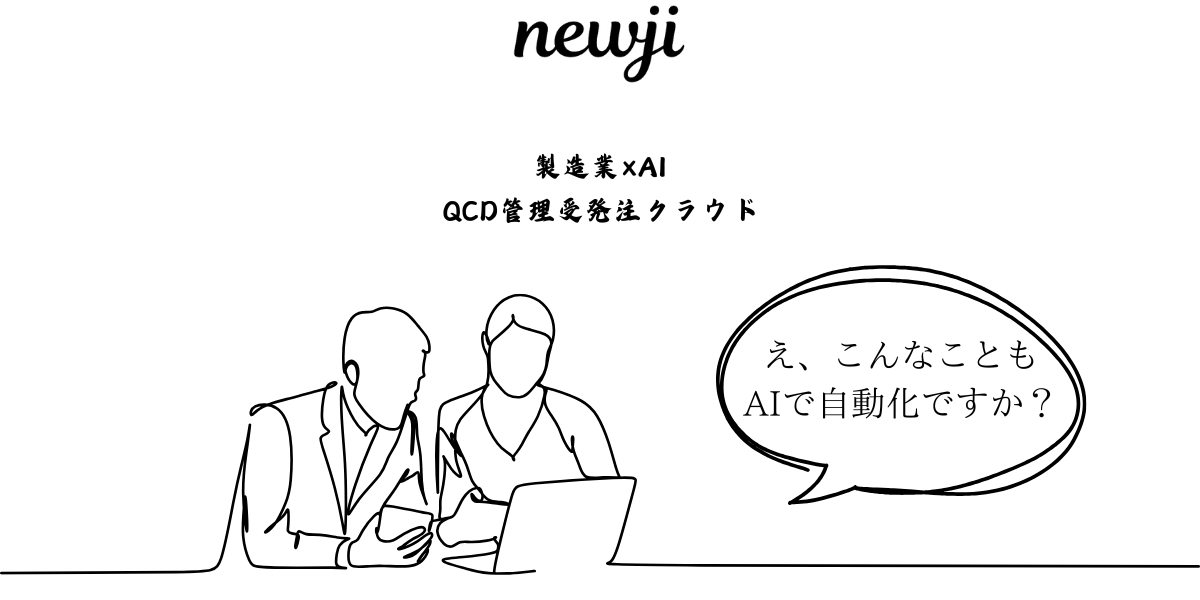
How to improve product quality with parts traceability management led by the purchasing department
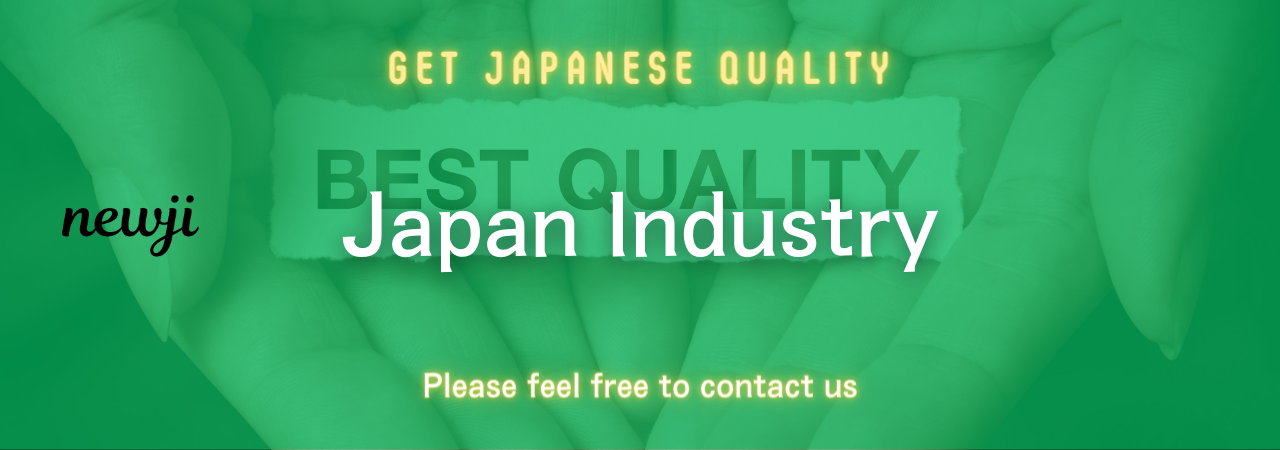
目次
Understanding Parts Traceability Management
In the world of manufacturing, product quality is paramount.
One effective way to enhance product quality is through parts traceability management.
This process involves tracking each part or component of a product from the supplier to the production line, and all the way to the end consumer.
By maintaining detailed records, manufacturers can quickly identify and address issues, ensuring that only the best products reach the market.
The purchasing department plays a crucial role in this system.
It acts as a bridge between the suppliers and the production team, ensuring that the right parts are acquired and traced accurately.
By leading parts traceability management, the purchasing department can significantly contribute to improving product quality.
The Role of the Purchasing Department
The purchasing department is responsible for obtaining the necessary parts and materials for production.
With traceability management, this department takes on a more strategic role.
It becomes responsible for ensuring that every part sourced is documented, with its origin, specifications, and journey through the supply chain recorded.
By implementing standardized procedures and using advanced traceability software, the purchasing team can monitor each part and maintain an accessible record of its history.
This not only helps in quality control but also in compliance with regulatory standards and quick response to recalls.
Choosing Reliable Suppliers
An integral part of parts traceability is selecting reliable suppliers.
The purchasing department must thoroughly vet each supplier, checking their compliance with quality standards and their ability to provide traceable components.
This evaluation helps ensure that the parts being used are of the highest quality, reducing the risk of product defects.
By building strong relationships with reputable suppliers, the purchasing department can negotiate better terms and establish consistency in quality.
This partnership also facilitates easier tracking and improved communication, which are essential for effective traceability management.
Implementing Traceability Systems
For effective parts traceability management, the purchasing department must implement robust traceability systems.
These systems enable the seamless tracking of parts throughout their lifecycle.
Here’s how the process works:
Integrating Technology
Traceability systems rely heavily on technology.
By using software that integrates with existing ERP (Enterprise Resource Planning) systems, the purchasing department can automate data entry and tracking processes.
Barcode scanning, RFID tags, and QR codes are common tools that assist in this digital transformation, providing real-time updates on part location and status.
These technological tools not only make traceability more efficient but also enhance accuracy.
With precise data logging, manufacturers can drastically reduce errors, improving overall product quality.
Tracking Parts Through the Supply Chain
Tracking each part from supplier to consumer is essential.
This involves documenting every stage of the supply chain: from the moment a part is purchased, through delivery, storage, assembly, and finally its incorporation into the final product.
Each stage is recorded systematically, creating a comprehensive audit trail.
With a thorough monitoring system, issues can be identified more swiftly.
For instance, if a defect is reported, the traceability system allows manufacturers to trace the defect back to its source, whether it be a faulty batch from a supplier or a misstep in assembly, and address it accordingly.
Benefits of Effective Parts Traceability Management
Proper parts traceability management offers numerous benefits that extend beyond product quality.
Here are some advantages of implementing this approach effectively:
Enhanced Product Quality
With detailed knowledge of a part’s journey, manufacturers can ensure that only high-quality parts are used.
This reduces the risk of defects and improves the end product’s reliability.
Customers are likely to notice and appreciate products that consistently meet high-quality standards.
Efficient Recall Management
In the event of a quality issue, efficient traceability enables quick identification of affected products.
This allows manufacturers to conduct targeted recalls, minimizing waste and maintaining brand reputation.
It also means problems can be rectified before they escalate, saving time and resources.
Regulatory Compliance
Many industries have strict regulations regarding product traceability.
Implementing a robust traceability management system ensures that manufacturers comply with these regulations, avoiding potential legal issues and fines.
Compliance also opens opportunities in markets that emphasize regulatory adherence.
Cost Savings
While the initial setup of a traceability system might require investment, the long-term savings are substantial.
By reducing errors, streamlining operations, and avoiding widespread recalls, manufacturers can save significantly on costs.
Effective traceability also leads to better inventory management, reducing overhead related to excess stock or shortages.
Conclusion
Parts traceability management is a vital strategy for improving product quality.
Led by the purchasing department, this process ensures that every part is tracked meticulously, from supplier to consumer.
Through reliable supplier partnerships, implementation of advanced technology, and comprehensive tracking, manufacturers can enhance product quality, ensure regulatory compliance, manage recalls effectively, and achieve significant cost savings.
As the manufacturing landscape evolves, the role of parts traceability management becomes increasingly important.
By investing in this system, companies not only enhance their product offerings but also build a robust framework for future growth and success.
資料ダウンロード
QCD調達購買管理クラウド「newji」は、調達購買部門で必要なQCD管理全てを備えた、現場特化型兼クラウド型の今世紀最高の購買管理システムとなります。
ユーザー登録
調達購買業務の効率化だけでなく、システムを導入することで、コスト削減や製品・資材のステータス可視化のほか、属人化していた購買情報の共有化による内部不正防止や統制にも役立ちます。
NEWJI DX
製造業に特化したデジタルトランスフォーメーション(DX)の実現を目指す請負開発型のコンサルティングサービスです。AI、iPaaS、および先端の技術を駆使して、製造プロセスの効率化、業務効率化、チームワーク強化、コスト削減、品質向上を実現します。このサービスは、製造業の課題を深く理解し、それに対する最適なデジタルソリューションを提供することで、企業が持続的な成長とイノベーションを達成できるようサポートします。
オンライン講座
製造業、主に購買・調達部門にお勤めの方々に向けた情報を配信しております。
新任の方やベテランの方、管理職を対象とした幅広いコンテンツをご用意しております。
お問い合わせ
コストダウンが利益に直結する術だと理解していても、なかなか前に進めることができない状況。そんな時は、newjiのコストダウン自動化機能で大きく利益貢献しよう!
(Β版非公開)