- お役立ち記事
- How to improve quality and productivity by introducing TQM that quality assurance department managers should keep in mind
月間76,176名の
製造業ご担当者様が閲覧しています*
*2025年3月31日現在のGoogle Analyticsのデータより
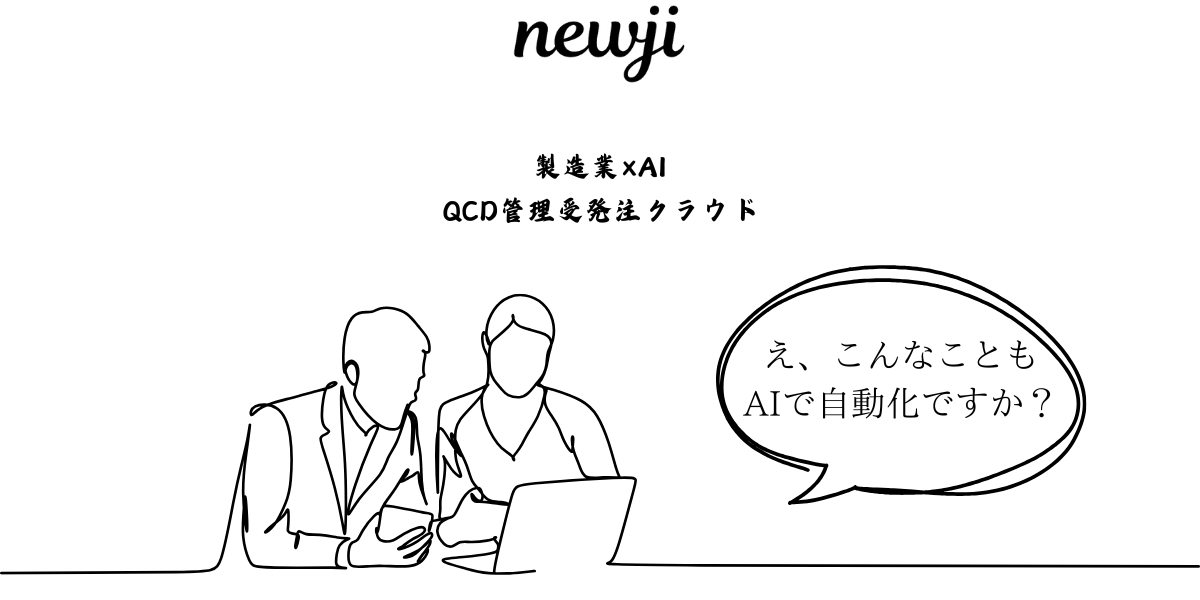
How to improve quality and productivity by introducing TQM that quality assurance department managers should keep in mind
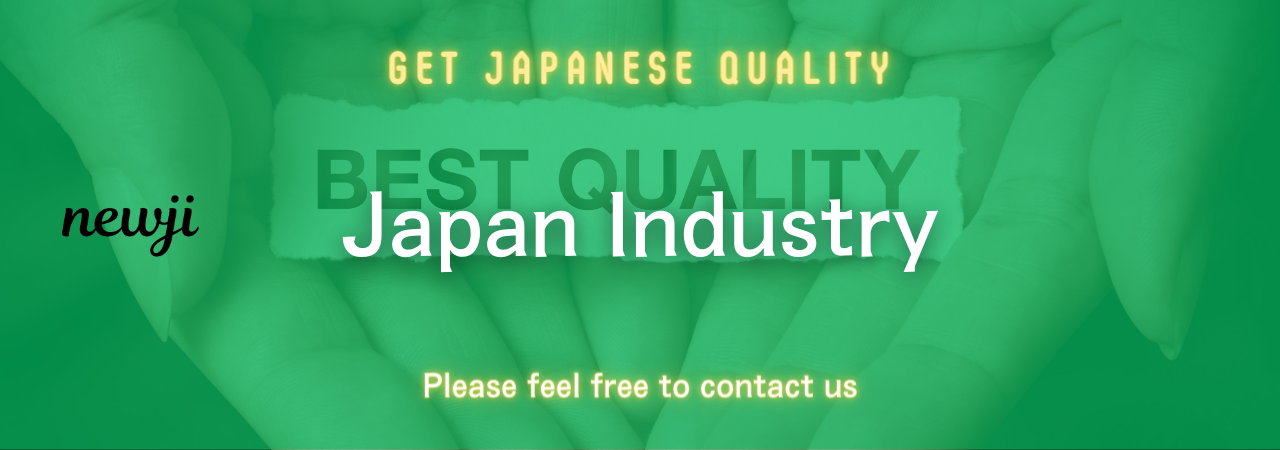
目次
Understanding Total Quality Management (TQM)
Total Quality Management (TQM) is a comprehensive management approach that focuses on improving the quality and performance of an organization’s products and services.
By implementing TQM, companies can enhance customer satisfaction and streamline operations, which ultimately leads to higher productivity.
TQM is rooted in a collaborative effort among all members of an organization.
Everyone from top management to frontline employees plays a part in ensuring quality improvement at every level.
The goal is to create a culture where quality becomes a natural part of daily operations.
Key Principles of TQM
TQM is based on several core principles that guide organizations towards higher quality and productivity.
1. **Customer Focus**: The first and foremost principle of TQM is having a strong customer focus.
Understanding the needs and expectations of customers is crucial, as it allows companies to tailor their products and services accordingly.
2. **Total Employee Involvement**: Every employee in the organization should be engaged in the process of quality improvement.
When employees are involved, they are more likely to take ownership of their roles in ensuring quality.
3. **Process-Centered Approach**: TQM emphasizes the importance of processes.
Businesses should focus on improving their processes to enhance the overall quality of their products and services.
4. **Integrated System**: TQM requires an integrated system that aligns business processes with the strategic goals of the organization.
Every department and function must collaborate to achieve common quality objectives.
5. **Strategic Approach**: Quality improvement under TQM should align with the strategic planning of the organization.
Long-term strategies are designed with quality as a foundational element.
6. **Data-Driven Decision Making**: Decisions under TQM are based on data and analysis.
By making informed decisions, organizations can identify areas of improvement and measure progress effectively.
7. **Continuous Improvement**: The concept of continuous improvement is central to TQM.
Organizations should constantly seek ways to enhance quality and increase productivity.
8. **Effective Communication**: For TQM to succeed, clear and effective communication is vital.
Information must flow freely across all levels of the organization to support quality initiatives.
Implementing TQM in the Quality Assurance Department
For quality assurance managers, implementing TQM can significantly impact their department’s effectiveness.
Here’s how to go about it:
Assess Current Quality Processes
The first step to implementing TQM is to assess the current quality processes in the organization.
Identify the strengths and weaknesses of existing systems.
This assessment will provide a baseline for improvement and help prioritize areas that require immediate attention.
Set Clear Quality Goals
Establish clear, measurable quality goals aligned with the organization’s overall objectives.
Goals should be specific, achievable, and time-bound.
Having clear objectives will guide the quality assurance team in their efforts to implement TQM effectively.
Engage and Empower Employees
Involve employees at all levels in the TQM process.
Empowering employees by providing training and resources is crucial for successful implementation.
Foster a culture of open communication and encourage employees to contribute ideas for quality improvement.
Focus on Customer Needs
Quality assurance efforts should always revolve around meeting customer needs and expectations.
Gather customer feedback and use it to improve products and processes.
By putting customers at the center, the quality assurance department can deliver value and enhance satisfaction.
Adopt a Process-Based Approach
Analyze and map out key processes within your department.
Identify areas that need improvement to enhance efficiency and reduce waste.
Optimizing processes will lead to increased productivity and better quality outcomes.
Utilize Data and Analytics
Data is a powerful tool in the TQM framework.
Collect and analyze data to monitor progress and identify trends.
Using data-driven insights can help make informed decisions that contribute to quality improvement.
Develop a Continuous Improvement Plan
Implementing TQM is not a one-time task.
Develop a continuous improvement plan that outlines the steps for ongoing quality enhancement.
Regularly review and adjust the plan based on feedback and performance metrics.
Benefits of TQM for Quality Assurance
Implementing TQM in the quality assurance department brings numerous benefits, including:
– **Enhanced Customer Satisfaction**: By focusing on quality, organizations can meet and exceed customer expectations, leading to increased customer loyalty.
– **Improved Productivity**: Streamlined processes reduce waste and inefficiencies, allowing employees to work more effectively.
– **Better Employee Engagement**: Involving employees in the quality process boosts morale and job satisfaction.
– **Reduced Costs**: By addressing quality issues proactively, TQM can significantly lower costs associated with defects and rework.
– **Stronger Brand Reputation**: Consistently high-quality products and services strengthen the organization’s reputation in the market.
Conclusion
Total Quality Management is a vital strategy for any organization aiming to improve quality and productivity.
By focusing on customer needs, involving employees at all levels, and utilizing data-driven decision-making, quality assurance departments can achieve remarkable results.
Implementing TQM not only enhances the quality of products and services but also contributes to a more efficient, engaged, and sustainable organization.
資料ダウンロード
QCD管理受発注クラウド「newji」は、受発注部門で必要なQCD管理全てを備えた、現場特化型兼クラウド型の今世紀最高の受発注管理システムとなります。
ユーザー登録
受発注業務の効率化だけでなく、システムを導入することで、コスト削減や製品・資材のステータス可視化のほか、属人化していた受発注情報の共有化による内部不正防止や統制にも役立ちます。
NEWJI DX
製造業に特化したデジタルトランスフォーメーション(DX)の実現を目指す請負開発型のコンサルティングサービスです。AI、iPaaS、および先端の技術を駆使して、製造プロセスの効率化、業務効率化、チームワーク強化、コスト削減、品質向上を実現します。このサービスは、製造業の課題を深く理解し、それに対する最適なデジタルソリューションを提供することで、企業が持続的な成長とイノベーションを達成できるようサポートします。
製造業ニュース解説
製造業、主に購買・調達部門にお勤めの方々に向けた情報を配信しております。
新任の方やベテランの方、管理職を対象とした幅広いコンテンツをご用意しております。
お問い合わせ
コストダウンが利益に直結する術だと理解していても、なかなか前に進めることができない状況。そんな時は、newjiのコストダウン自動化機能で大きく利益貢献しよう!
(β版非公開)