- お役立ち記事
- How to increase reliability through parameter design that mid-level employees in the design department should know
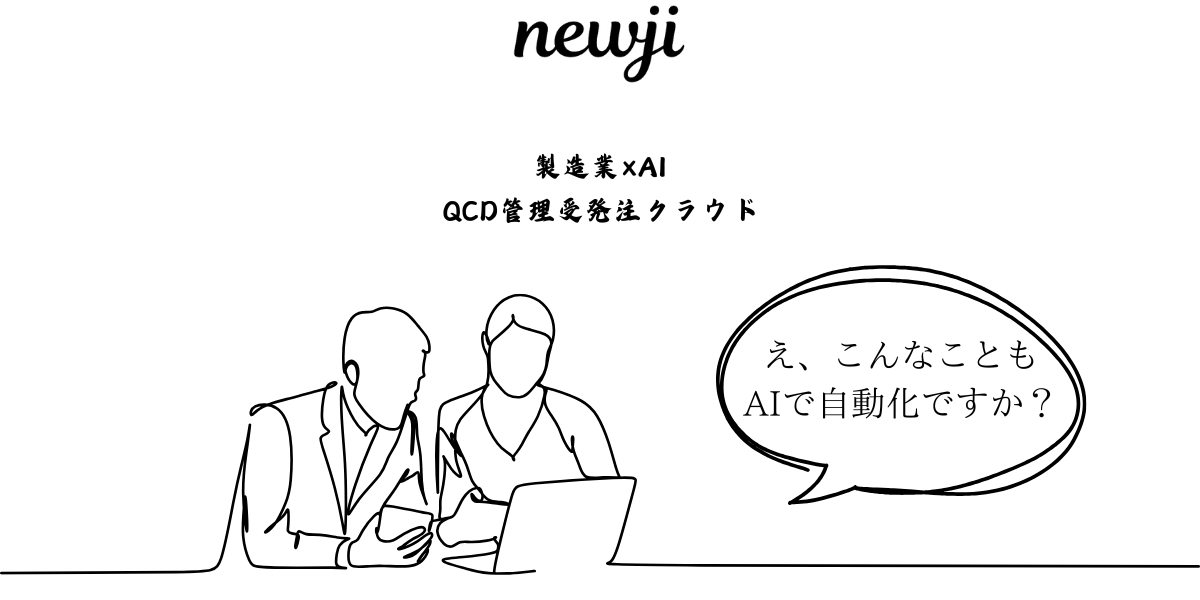
How to increase reliability through parameter design that mid-level employees in the design department should know
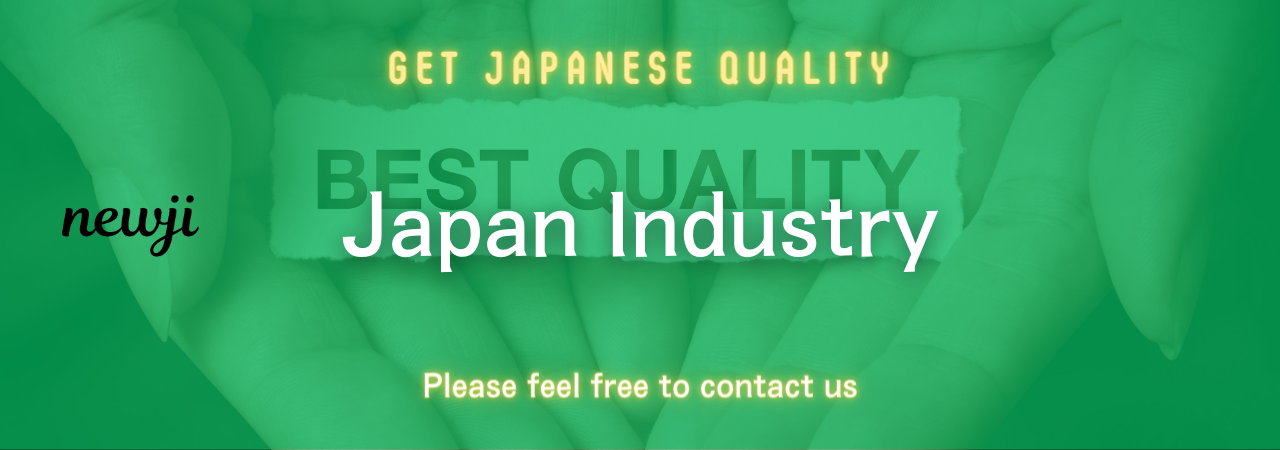
目次
Understanding Parameter Design
Parameter design is an essential concept that mid-level employees in the design department should understand thoroughly.
It involves selecting and optimizing the key factors that influence the performance and reliability of a product.
By focusing on these critical parameters, designers can ensure the product meets its intended function while maintaining higher reliability.
This process is crucial as it helps in identifying and controlling variables that can cause variations in performance.
By optimizing these aspects during the design phase, companies can prevent potential failures and ensure the product performs consistently under various conditions.
The Importance of Reliability in Design
Reliability is a measure of how consistently a product performs its intended function without failure.
It is a critical attribute that affects customer satisfaction and brand reputation.
A reliable product minimizes warranty claims and enhances consumer trust, leading to a positive impact on a company’s bottom line.
In a highly competitive market, reliability can be a significant differentiator.
Customers prefer products that deliver dependable performance over time.
Thus, ensuring reliability through parameter design has become an indispensable practice for design departments aiming at superior product quality.
Key Concepts in Parameter Design
Parameter design focuses on identifying control factors and noise factors.
Control factors are variables that can be adjusted during testing and development to achieve optimum performance.
On the other hand, noise factors are variables that the user cannot control and that might affect the performance under different circumstances.
The goal of parameter design is to find the right combination of control factors so that the product remains robust against variations introduced by noise factors.
This is achieved through systematic experimentation, typically involving techniques such as Design of Experiments (DOE) and the Taguchi method.
Design of Experiments (DOE)
Design of Experiments is a structured approach used to test multiple variables simultaneously.
By systematically manipulating design parameters, DOE helps in understanding their impact on product performance and reliability.
DOE provides valuable insights and allows designers to identify the best possible setup of parameters.
Experimenting under controlled conditions reduces the risk of unforeseen failures and enables data-driven decision-making.
The Taguchi Method
The Taguchi method is a statistical approach developed to improve quality and performance.
It focuses on designing products that are less sensitive to variations, thus improving reliability.
This method suggests using standard orthogonal arrays to study control factors and their interactions comprehensively.
The goal is to analyze and predict how changes in design parameters affect the outcome, leading to designs that are more robust.
Steps to Implement Parameter Design for Improved Reliability
Implementing parameter design effectively involves a series of concise steps.
It requires a detailed understanding of the product, its potential failure modes, and the environment where it will operate.
Identify Critical Parameters
Begin by identifying the parameters that are most likely to affect performance.
This step involves comprehensive brainstorming and analysis of the product design and its application.
Once identified, classify these parameters into control factors and noise factors.
Determine which variables can be manipulated and which ones are outside of direct influence yet might impact product performance.
Establish Objective Criteria
Set clear objectives and criteria for performance outcomes.
Defining measurable results is essential for evaluating the effectiveness of parameter adjustments.
This involves specifying what constitutes acceptable performance and reliability standards for the product.
Conduct Systematic Experiments
Utilize methods like DOE or the Taguchi method to conduct systematic experiments.
This involves varying control factors methodically to observe impacts on product performance.
Based on these experiments, you can determine the optimal levels of each parameter.
This leads to a design that is more reliable and consistent in performance.
Analyze Results and Optimize Design
Analyze the data from your experiments to find correlations between parameter modifications and performance outcomes.
Use statistical tools to ensure the results are significant and provide insights into potential improvements.
Implement the findings by refining the design parameters.
Ensure these adjustments lead to enhanced reliability, making the product robust against potential variations.
Validate the Improved Design
Finally, validate the improved design by testing it under standard conditions and scenarios similar to real-world use.
The validation phase ensures that all potential issues have been addressed, and the design performs as expected.
Once confirmed, document the findings and integrate the successful parameters into the full-scale production process.
Conclusion
Increasing reliability through parameter design is a vital strategy for improving product quality.
By systematically identifying and optimizing critical factors, mid-level employees in the design department can significantly influence the longevity and performance of the product.
This process not only helps in minimizing failures and enhancing customer satisfaction but also reduces costs associated with warranty claims and product recalls.
By adopting these practices, companies can lead the market with products that meet consumer expectations and maintain a competitive edge.
資料ダウンロード
QCD調達購買管理クラウド「newji」は、調達購買部門で必要なQCD管理全てを備えた、現場特化型兼クラウド型の今世紀最高の購買管理システムとなります。
ユーザー登録
調達購買業務の効率化だけでなく、システムを導入することで、コスト削減や製品・資材のステータス可視化のほか、属人化していた購買情報の共有化による内部不正防止や統制にも役立ちます。
NEWJI DX
製造業に特化したデジタルトランスフォーメーション(DX)の実現を目指す請負開発型のコンサルティングサービスです。AI、iPaaS、および先端の技術を駆使して、製造プロセスの効率化、業務効率化、チームワーク強化、コスト削減、品質向上を実現します。このサービスは、製造業の課題を深く理解し、それに対する最適なデジタルソリューションを提供することで、企業が持続的な成長とイノベーションを達成できるようサポートします。
オンライン講座
製造業、主に購買・調達部門にお勤めの方々に向けた情報を配信しております。
新任の方やベテランの方、管理職を対象とした幅広いコンテンツをご用意しております。
お問い合わせ
コストダウンが利益に直結する術だと理解していても、なかなか前に進めることができない状況。そんな時は、newjiのコストダウン自動化機能で大きく利益貢献しよう!
(Β版非公開)