- お役立ち記事
- How to introduce and effectively utilize PFEP (Plan For Every Part)
月間76,176名の
製造業ご担当者様が閲覧しています*
*2025年3月31日現在のGoogle Analyticsのデータより
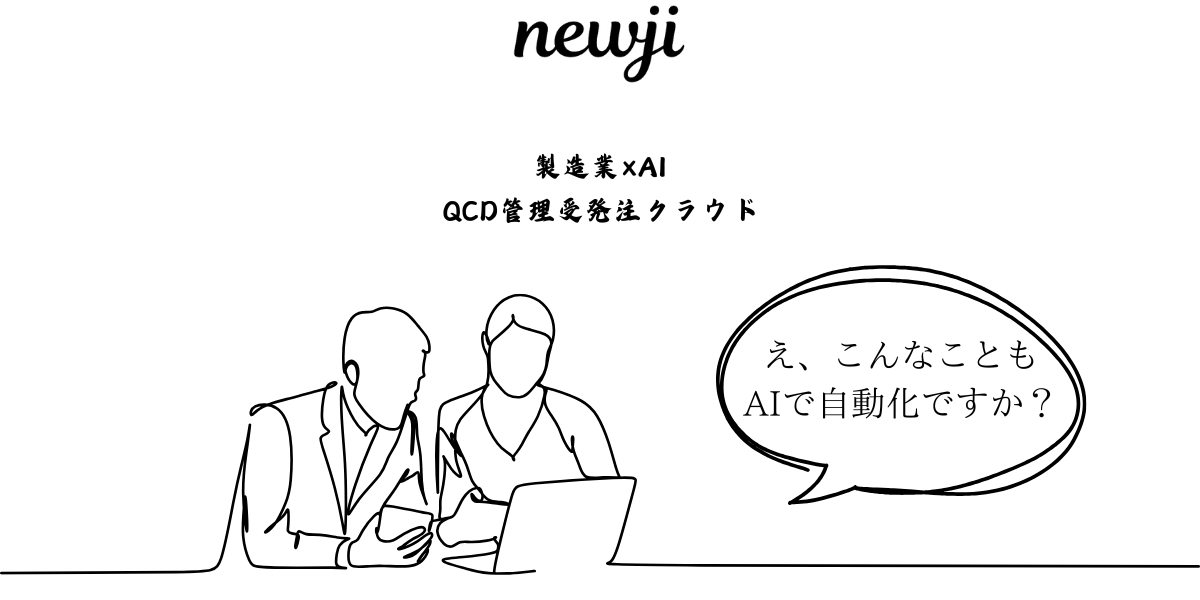
How to introduce and effectively utilize PFEP (Plan For Every Part)
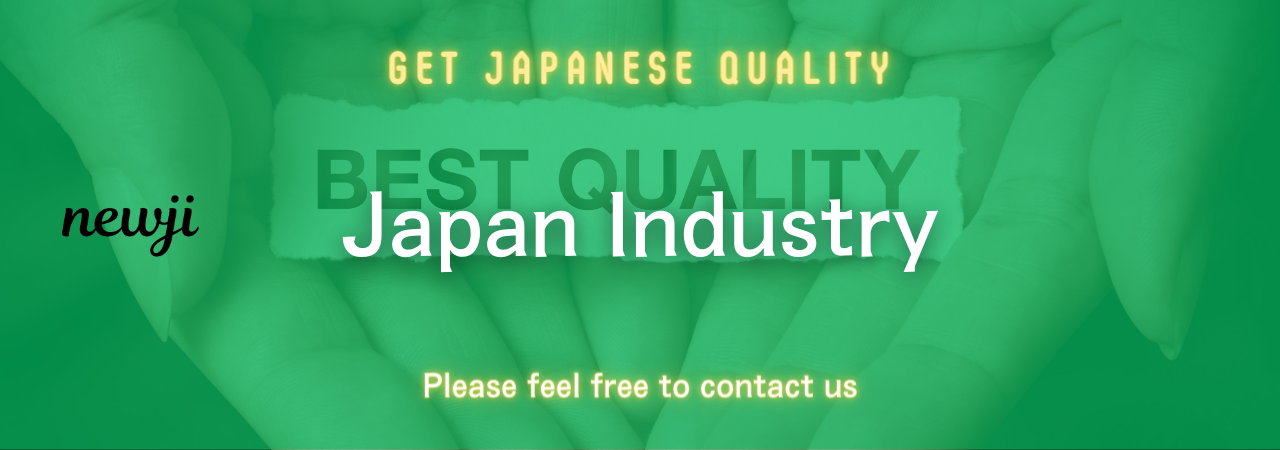
Introducing and utilizing PFEP (Plan For Every Part) effectively can be a game-changer for any manufacturing or supply chain operation.
PFEP is a meticulous method that organizes data for every part in your inventory.
It serves as a living, breathing document that evolves as your operations grow, ensuring you have up-to-date information at your fingertips.
By implementing PFEP, you increase visibility, reduce errors, and streamline your supply chain processes.
Let’s delve into how you can introduce and effectively utilize PFEP to reap its numerous benefits.
目次
Understanding PFEP
Before you can introduce PFEP into your operations, it’s crucial to understand what it entails.
PFEP is a comprehensive database that holds critical information about every single part within your supply chain.
This information can include part numbers, supplier details, lead times, order quantities, storage locations, and much more.
PFEP helps in managing the flow of materials throughout the supply chain, from procurement to delivery.
With this information at hand, decision-makers have a clear view of inventory levels, facilitating more accurate forecasting and planning.
Steps to Introduce PFEP
1. Gather Detailed Data
The first step in introducing PFEP is to gather as much information as possible about each part in your inventory.
Create a comprehensive list that includes part numbers, descriptions, dimensions, weights, supplier details, minimum and maximum inventory levels, and reorder points.
The more data you collect, the more beneficial your PFEP will be.
2. Develop a Central Database
Once you have gathered all the necessary data, centralize it in a single database.
This database should be easily accessible to all relevant parties within your organization.
Using software tools such as a dedicated PFEP software or even an ERP (Enterprise Resource Planning) system can be extremely helpful.
The key is to ensure that your data is organized and easily retrievable.
3. Standardize Data Entry
Data consistency is vital for a functional PFEP.
Develop standardized templates and guidelines for data entry to maintain uniformity across your database.
Having a standardized approach ensures that the data is accurate and up to date.
Train employees involved in data entry on these standards to minimize errors.
4. Conduct Regular Audits
Introduce regular audits to verify the accuracy of the data within your PFEP.
Audits help in identifying discrepancies, obsolete information, or missing data.
Regular updates ensure that your PFEP reflects the current state of your inventory, enabling better decision-making.
Effective Utilization of PFEP
1. Enhance Inventory Management
PFEP helps in maintaining optimal inventory levels by providing real-time data on part quantities.
It enables you to reorder parts before they run out, avoiding production delays.
Utilize the data from PFEP to set minimum and maximum inventory levels, ensuring a smoother procurement process.
2. Improve Supplier Relationships
With detailed supplier information at your fingertips, you can strengthen your relationships with suppliers.
You can track lead times, negotiate better terms, and plan for potential delays more effectively.
Having this information also enables you to identify and work with reliable suppliers consistently.
3. Streamline Production Planning
PFEP provides valuable insights into which parts are crucial for your production process.
By understanding lead times and usage rates, you can better plan production schedules, minimizing downtime and maximizing efficiency.
Ensure that you always have critical parts available when needed to keep your production line running smoothly.
4. Facilitate Cost Savings
Accurate data in your PFEP allows you to identify cost-saving opportunities.
You can optimize order quantities, reduce excess inventory, and avoid rush orders that typically come with higher costs.
In addition, PFEP can reveal parts that can be aggregated for bulk purchasing, leading to further cost reductions.
5. Enhance Communication
A well-maintained PFEP fosters better communication between different departments within your organization.
It provides a single source of truth for inventory data, ensuring everyone has access to the same information.
This consistency enhances collaborative efforts and speeds up decision-making processes.
Challenges in Implementing PFEP
1. Initial Data Collection
Gathering detailed information about every part in your inventory can be time-consuming and labor-intensive.
It requires a dedicated team to ensure the data’s accuracy and comprehensiveness.
2. Data Maintenance
Keeping the PFEP database updated requires ongoing efforts and regular audits.
Consistency in data entry is crucial and can be challenging to uphold without stringent standards and trained personnel.
3. Staff Training
Employees need to be trained to understand the importance of PFEP and how to use it effectively.
Training programs are necessary to ensure that everyone involved in data entry and utilization is on the same page.
Conclusion
Introducing and effectively utilizing PFEP can transform your supply chain and manufacturing operations.
From enhancing inventory management and supplier relationships to streamlining production planning and facilitating cost savings, the benefits are substantial.
While implementing PFEP may come with challenges, such as initial data collection and maintenance, the long-term advantages far outweigh these initial hurdles.
By gathering detailed data, developing a central database, standardizing data entry, and conducting regular audits, you lay the foundation for a successful PFEP initiative.
Once in place, leverage PFEP to improve communication, decision-making, and overall operational efficiency.
Ultimately, PFEP paves the way for a more organized, cost-effective, and efficient supply chain, setting the stage for your business’s ongoing growth and success.
資料ダウンロード
QCD管理受発注クラウド「newji」は、受発注部門で必要なQCD管理全てを備えた、現場特化型兼クラウド型の今世紀最高の受発注管理システムとなります。
ユーザー登録
受発注業務の効率化だけでなく、システムを導入することで、コスト削減や製品・資材のステータス可視化のほか、属人化していた受発注情報の共有化による内部不正防止や統制にも役立ちます。
NEWJI DX
製造業に特化したデジタルトランスフォーメーション(DX)の実現を目指す請負開発型のコンサルティングサービスです。AI、iPaaS、および先端の技術を駆使して、製造プロセスの効率化、業務効率化、チームワーク強化、コスト削減、品質向上を実現します。このサービスは、製造業の課題を深く理解し、それに対する最適なデジタルソリューションを提供することで、企業が持続的な成長とイノベーションを達成できるようサポートします。
製造業ニュース解説
製造業、主に購買・調達部門にお勤めの方々に向けた情報を配信しております。
新任の方やベテランの方、管理職を対象とした幅広いコンテンツをご用意しております。
お問い合わせ
コストダウンが利益に直結する術だと理解していても、なかなか前に進めることができない状況。そんな時は、newjiのコストダウン自動化機能で大きく利益貢献しよう!
(β版非公開)