- お役立ち記事
- How to introduce quality control and traceability that purchasing departments cannot ignore
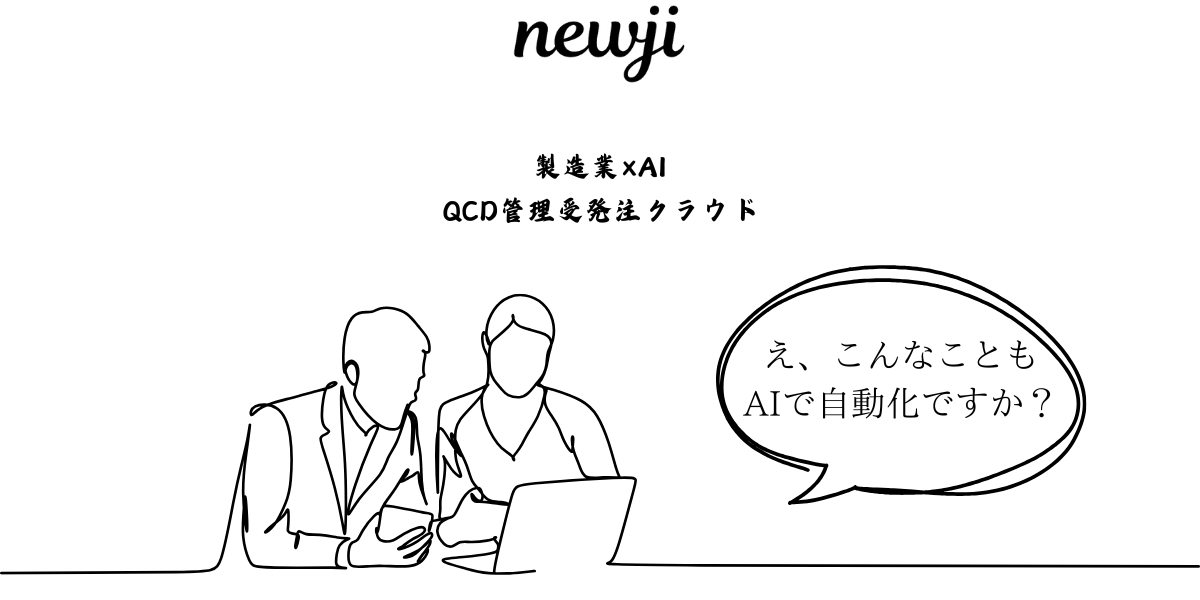
How to introduce quality control and traceability that purchasing departments cannot ignore
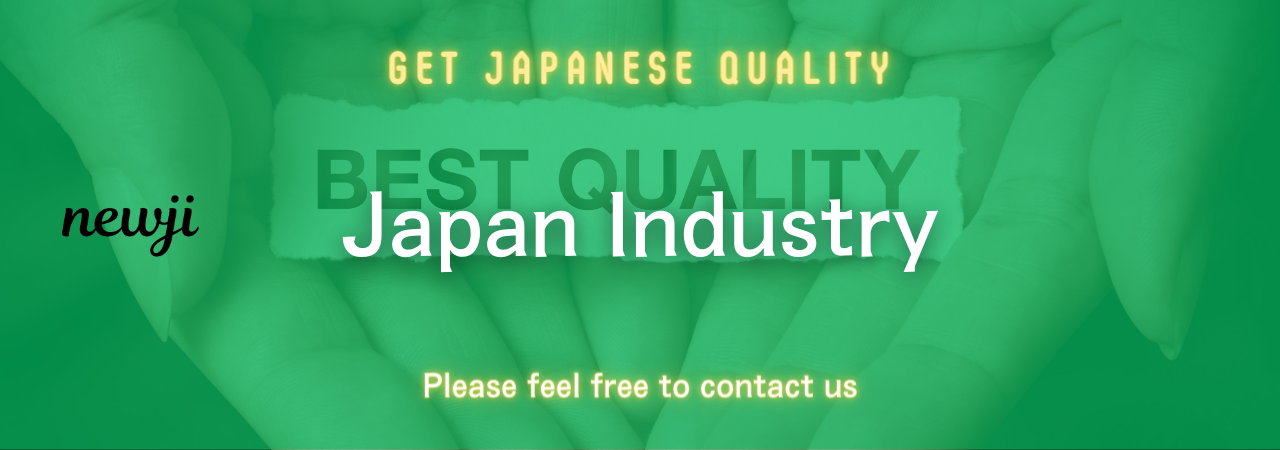
目次
Understanding Quality Control
Quality control is an essential aspect of any purchasing department because it ensures that products meet a company’s specific standards and requirements.
By implementing effective quality control measures, companies can minimize errors, reduce costs, and improve customer satisfaction.
At its core, quality control involves inspecting and testing products to ensure they match predefined quality criteria.
In the purchasing department, quality control starts with selecting suppliers who can consistently deliver goods that adhere to agreed-upon specifications.
This usually involves assessing suppliers’ quality management systems and their ability to produce goods that meet the required standards.
Furthermore, purchasing departments often conduct regular audits and quality checks on deliveries to verify compliance.
The Benefits of Quality Control
Implementing robust quality control systems yields numerous benefits for purchasing departments.
First, it significantly reduces the risk of receiving defective goods, which can cause production delays and increased costs.
With effective quality control processes in place, companies can reject substandard products before they enter the production line.
Another advantage is the enhancement of the company’s reputation.
By consistently delivering high-quality products, businesses can build trust with customers and establish themselves as reliable market leaders.
Moreover, effective quality control measures can also lead to improved supplier relationships, as they provide clear expectations and accountability in delivering quality goods.
Additionally, a strong quality control system helps in identifying inefficiencies and areas for improvement within the supply chain.
This can lead to cost savings, as companies can address issues before they escalate into more significant problems.
Traceability and Its Importance
Traceability in supply chain management refers to the ability to track the movement of a product from its origin through to the final sale.
By maintaining comprehensive records, companies can easily trace a product’s history, including its components, suppliers, and production processes.
This level of traceability is particularly crucial for industries like food, pharmaceuticals, and electronics, where quality and safety are paramount.
In the purchasing department, traceability is integrated with quality control to enhance overall supply chain transparency and accountability.
Benefits of Implementing Traceability
Traceability offers several key benefits for purchasing departments.
Firstly, it enhances quality management by allowing companies to track the source of defects or inconsistencies quickly.
By identifying the root cause of issues, companies can address them efficiently and prevent similar problems in the future.
Traceability also improves regulatory compliance.
In sectors with stringent regulations, traceability ensures that companies can provide the necessary documentation during audits or inspections, demonstrating control over their supply chains.
Moreover, traceability supports sustainability initiatives by enabling companies to verify the ethical sourcing of raw materials and components.
This transparency helps businesses meet consumer demands for responsibly sourced and environmentally friendly products.
Integrating Quality Control and Traceability
To maximize their effectiveness, quality control and traceability should be closely integrated within the purchasing department.
By working hand-in-hand, these two processes ensure that products not only meet quality standards but can also be reliably tracked throughout the supply chain.
One way to achieve this integration is through the use of technology.
Advanced software systems can streamline data collection and analysis, providing real-time visibility into quality and traceability metrics.
These systems can automatically record product details, track progress, and alert teams to potential issues promptly.
Another method is to establish clear communication channels among suppliers, manufacturers, and the purchasing department.
Regular updates and feedback loops foster collaboration and ensure that quality control and traceability practices are consistently upheld.
Steps to Implement Effective Systems
Implementing quality control and traceability systems involves several key steps.
First, it is essential to define what quality means for your organization, outlining specific criteria and standards that products must meet.
Next, assess current suppliers and their ability to meet these quality standards.
This may involve conducting audits, requesting certifications, or establishing strategic partnerships with high-performing suppliers.
Following this, develop and disseminate clear guidelines and procedures for conducting quality checks.
Train staff in the purchasing department to recognize potential quality issues and know the appropriate actions to take.
Implement technology solutions that support traceability.
This might involve barcode systems, RFID tags, or cloud-based platforms that enable real-time tracking and reporting.
Lastly, continuously review and optimize quality control and traceability systems.
Use data and feedback to identify areas for improvement and adapt processes to changing market conditions or regulatory requirements.
Challenges and How to Overcome Them
Despite their benefits, integrating quality control and traceability into the purchasing process can be challenging.
One common issue is resistance to change, particularly when introducing new technologies or procedures.
To overcome this, it’s crucial to involve stakeholders at all levels, providing training and addressing concerns to facilitate smooth transitions.
Another challenge is the cost associated with implementing robust systems.
While the initial investment may be significant, the long-term savings from reduced errors and improved compliance often outweigh the expenses.
For companies with complex supply chains, maintaining traceability can be daunting.
In such cases, collaborating with supply chain experts or consultants may help in designing and implementing efficient, scalable systems.
In conclusion, by effectively introducing quality control and traceability, purchasing departments can enhance product quality, improve supplier relationships, and maintain compliance with industry standards.
Through careful planning, leveraging technology, and continuous improvement, businesses can ensure a consistent supply of high-quality products that meet customer expectations and regulatory requirements.
資料ダウンロード
QCD調達購買管理クラウド「newji」は、調達購買部門で必要なQCD管理全てを備えた、現場特化型兼クラウド型の今世紀最高の購買管理システムとなります。
ユーザー登録
調達購買業務の効率化だけでなく、システムを導入することで、コスト削減や製品・資材のステータス可視化のほか、属人化していた購買情報の共有化による内部不正防止や統制にも役立ちます。
NEWJI DX
製造業に特化したデジタルトランスフォーメーション(DX)の実現を目指す請負開発型のコンサルティングサービスです。AI、iPaaS、および先端の技術を駆使して、製造プロセスの効率化、業務効率化、チームワーク強化、コスト削減、品質向上を実現します。このサービスは、製造業の課題を深く理解し、それに対する最適なデジタルソリューションを提供することで、企業が持続的な成長とイノベーションを達成できるようサポートします。
オンライン講座
製造業、主に購買・調達部門にお勤めの方々に向けた情報を配信しております。
新任の方やベテランの方、管理職を対象とした幅広いコンテンツをご用意しております。
お問い合わせ
コストダウンが利益に直結する術だと理解していても、なかなか前に進めることができない状況。そんな時は、newjiのコストダウン自動化機能で大きく利益貢献しよう!
(Β版非公開)