- お役立ち記事
- How to introduce the optimal line layout in the prototyping process
月間76,176名の
製造業ご担当者様が閲覧しています*
*2025年3月31日現在のGoogle Analyticsのデータより
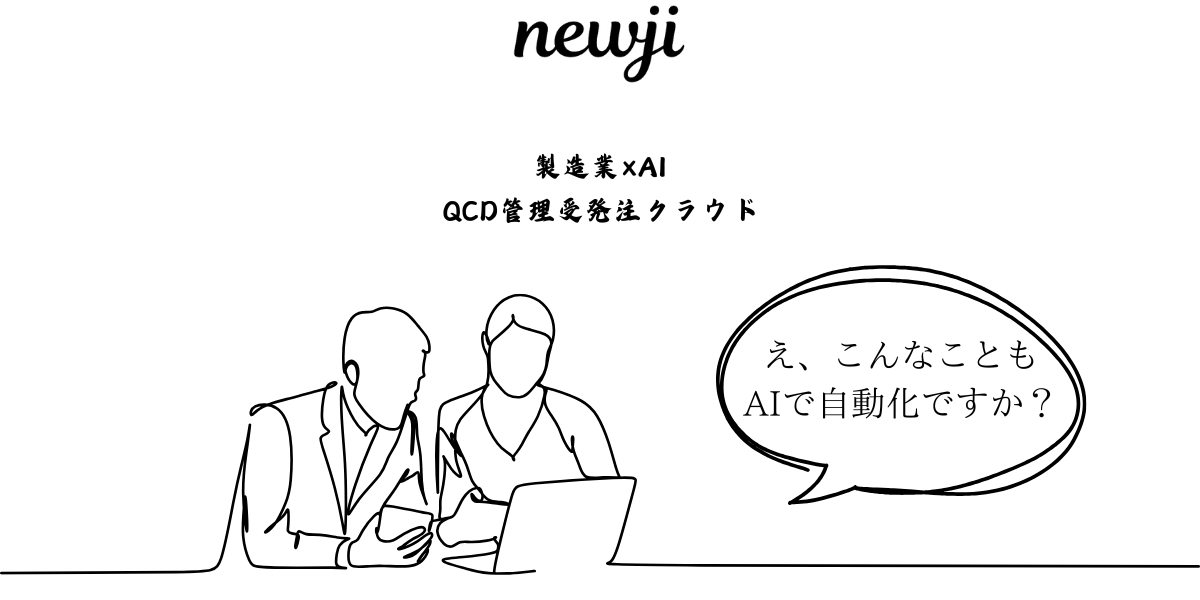
How to introduce the optimal line layout in the prototyping process
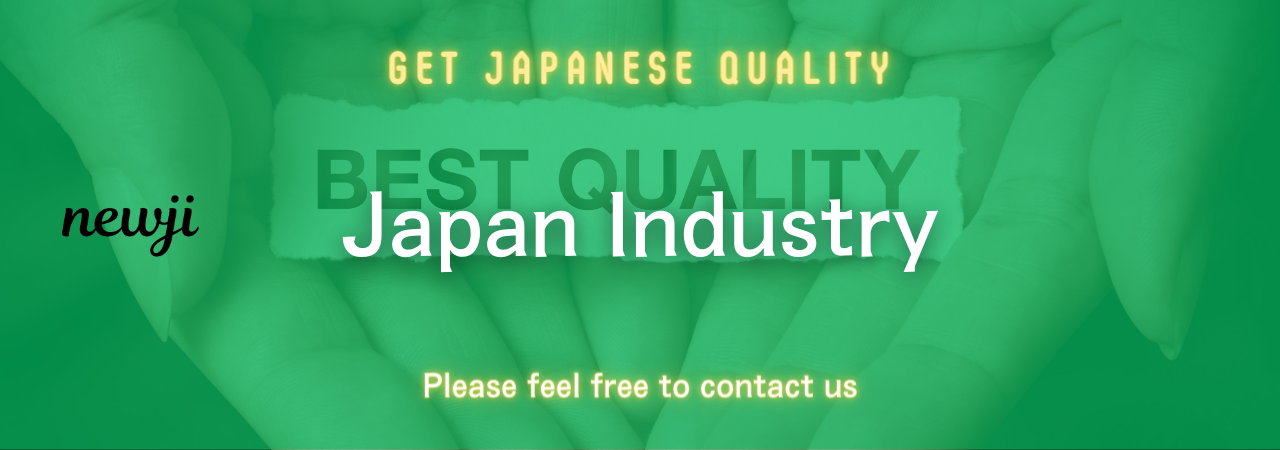
目次
Understanding the Importance of Line Layout in Prototyping
In the world of manufacturing, prototyping is a crucial step in bringing a concept to life.
It allows companies to refine their designs, identify potential issues, and enhance product efficiency before mass production.
An essential component of this process is the line layout — the geographical arrangement of equipment and workstations used during production.
A well-organized line layout can significantly improve workflow, reduce production costs, and boost product quality.
Thus, understanding how to introduce the optimal line layout in the prototyping process is key to improving overall manufacturing efficiency.
Factors to Consider When Designing Line Layouts
Before implementing a line layout, several key factors should be considered:
1. Product Characteristics
The design and complexity of the product greatly affect the layout of the production line.
Components that require specific tools or more elaborate procedures will demand different layouts.
For example, a simple product with few parts might benefit from a linear flow, while a complex assembly with many parts might need a modular approach.
2. Production Volume
The projected production volume also plays a vital role in determining the optimal layout.
High volume production typically requires a more automated and streamlined layout, while low volume runs allow for more flexible arrangements that can easily adapt to changes.
3. Available Space
The physical space available within the production facility must be carefully analyzed.
Maximizing this space can help to ensure that all necessary equipment and workstations are efficiently integrated without overcrowding, allowing for smooth workflow and improved safety.
4. Worker Efficiency
Designing a line layout that boosts worker productivity and minimizes fatigue is essential.
This includes considerations such as ergonomic workstation design, minimizing unnecessary movements, and ensuring easy access to tools and materials.
Types of Line Layouts in Prototyping
There are several common types of line layouts used in the prototyping process, each with its own advantages and challenges:
1. Linear Layout
Often referred to as a straight line layout, this arrangement sees workstations set up in a straight path, allowing materials to flow smoothly from one stage to another.
This type works well for products that move through a straightforward set of processes.
The primary benefit of a linear layout is its simplicity and straightforwardness in managing material flow.
2. U-Shaped Layout
In a U-shaped layout, workstations are arranged in a “U” form.
This enables workers to interact more closely and share resources effectively.
U-shaped layouts are especially beneficial for small batch production, where teamwork and flexibility are crucial.
3. Modular Layout
Modular layouts consist of independent units or modules that can be rearranged with minimal disruption.
This is ideal for facilities needing frequent changes in line setup or those producing a diverse range of products.
4. Fixed Position Layout
With fixed position layouts, the product remains stationary, and tools and workers move around it.
This layout is most applicable in prototyping large items or products that require detailed customization, such as aircraft or ships.
Steps to Implement Optimal Line Layout in Prototyping
To introduce an optimal line layout in a prototyping process, follow these practical steps:
1. Conduct a Thorough Process Analysis
Start by conducting an in-depth analysis of the current processes to identify inefficiencies, bottlenecks, and areas for improvement.
Understanding each step in the workflow and its dependencies is key to creating an efficient line layout.
2. Collaborate with Cross-Functional Teams
Engage with teams from different departments including engineering, production, quality, and safety, to gain diverse perspectives.
Involving cross-functional teams ensures all considerations are addressed, resulting in a balanced and practical layout design.
3. Plan for Flexibility
The ability to adapt to changes in production demand, design modifications, or technological advancements is critical.
Incorporate adaptability into the layout planning by designing with future needs in mind and using modular or adjustable components whenever possible.
4. Utilize Technology
Leverage cutting-edge software tools for designing and simulating line layout scenarios.
These tools provide visual models that can help predict workflow, highlight potential issues, and allow for practical adjustments before physical implementation.
5. Evaluate and Iterate
Once the layout is implemented, continuously monitor its performance.
Collect data on production efficiency, quality, and worker productivity to evaluate its success.
Use this information to make necessary adjustments and strive for continual improvement.
Conclusion
Introducing the optimal line layout in the prototyping process is a decisive factor for any manufacturing operation striving towards efficiency and excellence.
By understanding the aspects involved, choosing the right layout types, and following a structured implementation approach, companies can achieve streamlined production processes, reduced costs, and improved product quality.
資料ダウンロード
QCD管理受発注クラウド「newji」は、受発注部門で必要なQCD管理全てを備えた、現場特化型兼クラウド型の今世紀最高の受発注管理システムとなります。
ユーザー登録
受発注業務の効率化だけでなく、システムを導入することで、コスト削減や製品・資材のステータス可視化のほか、属人化していた受発注情報の共有化による内部不正防止や統制にも役立ちます。
NEWJI DX
製造業に特化したデジタルトランスフォーメーション(DX)の実現を目指す請負開発型のコンサルティングサービスです。AI、iPaaS、および先端の技術を駆使して、製造プロセスの効率化、業務効率化、チームワーク強化、コスト削減、品質向上を実現します。このサービスは、製造業の課題を深く理解し、それに対する最適なデジタルソリューションを提供することで、企業が持続的な成長とイノベーションを達成できるようサポートします。
製造業ニュース解説
製造業、主に購買・調達部門にお勤めの方々に向けた情報を配信しております。
新任の方やベテランの方、管理職を対象とした幅広いコンテンツをご用意しております。
お問い合わせ
コストダウンが利益に直結する術だと理解していても、なかなか前に進めることができない状況。そんな時は、newjiのコストダウン自動化機能で大きく利益貢献しよう!
(β版非公開)