- お役立ち記事
- How to launch a waste reduction project in the manufacturing industry
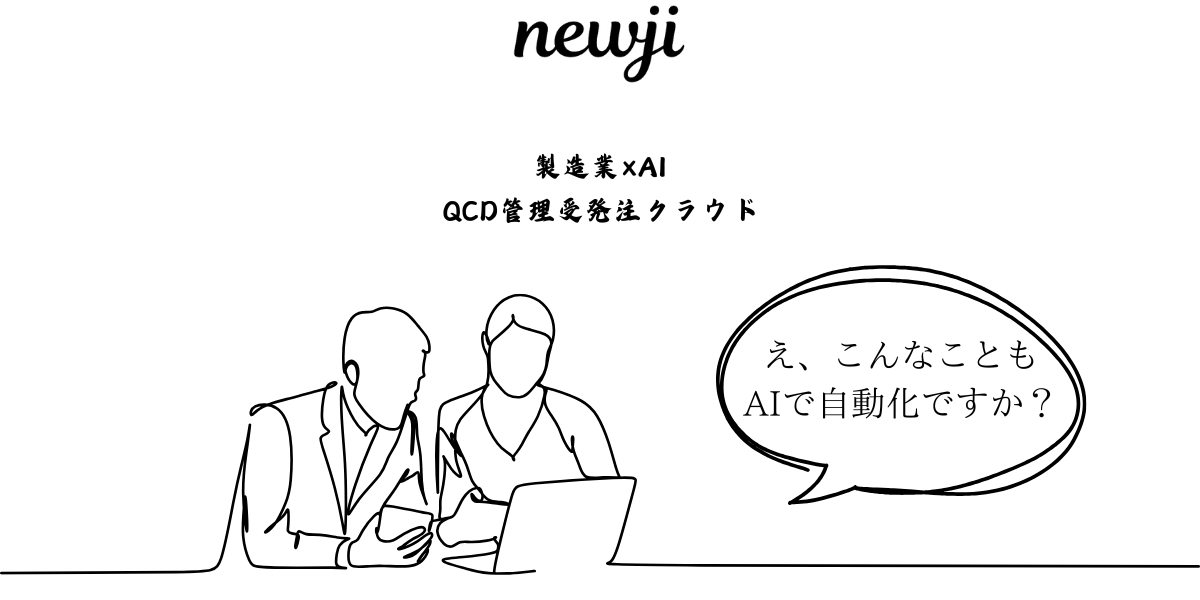
How to launch a waste reduction project in the manufacturing industry
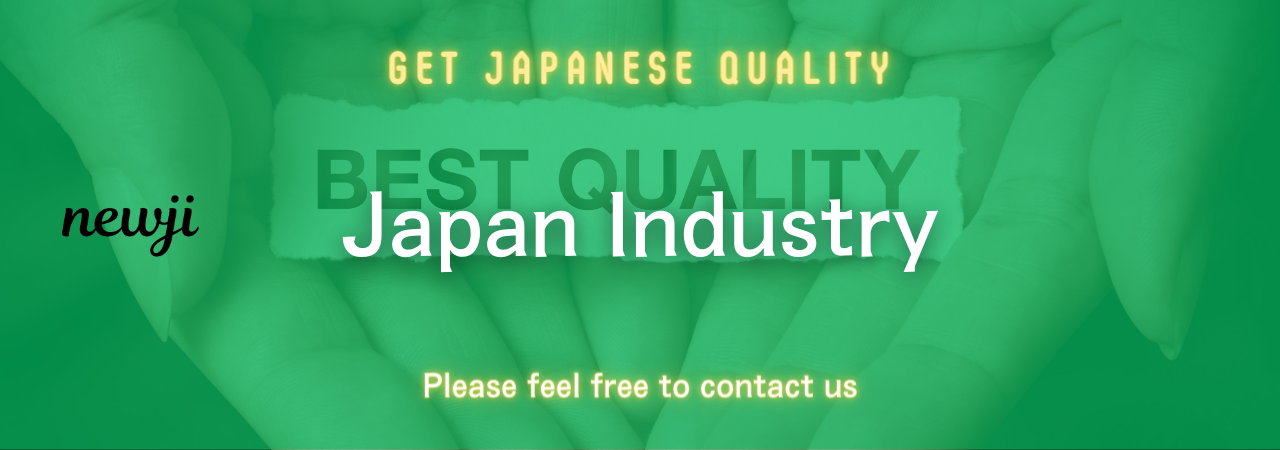
目次
Understanding Waste Reduction in Manufacturing
Waste reduction is a crucial aspect of sustainable manufacturing.
It involves minimizing the amount of waste produced during the manufacturing process.
By reducing waste, companies can lower their environmental impact, enhance efficiency, and improve profitability.
Understanding the types of waste generated in manufacturing is the first step toward launching an effective waste reduction project.
Types of Waste in Manufacturing
In manufacturing, waste can be classified into several categories.
These include:
– **Overproduction Waste**: This occurs when products are manufactured in excess or before they are needed.
– **Inventory Waste**: Excessive inventory storage leads to waste.
– **Transportation Waste**: Unnecessary movement of materials can contribute to waste.
– **Defect Waste**: Products that don’t meet quality standards must be discarded or reworked.
– **Waiting Waste**: Idle time when production could be happening elsewhere.
– **Over-processing Waste**: Doing more work or using more components than necessary.
Identifying these waste types is essential in forming a comprehensive waste reduction strategy.
Setting Clear Goals
Before launching a waste reduction project, it’s vital to set clear, achievable goals.
These goals should align with the company’s overall operational strategy and sustainability targets.
SMART Goals Framework
Use the SMART criteria to set goals that are Specific, Measurable, Achievable, Relevant, and Time-bound.
For example, a goal might be to reduce defect waste by 20% within the next year.
Clearly defined goals not only provide direction but also enable the assessment of project success.
Conducting a Waste Audit
A waste audit is an effective tool to understand the current state of waste generation.
This involves evaluating processes to identify where waste is generated, how much is produced, and why it occurs.
Steps to Conduct a Waste Audit
1. **Collect Data**: Gather information on the type and quantity of waste produced during manufacturing.
2. **Analyze Processes**: Examine manufacturing processes systematically to pinpoint inefficiencies.
3. **Identify Improvement Areas**: Highlight areas where waste can be reduced or eliminated.
4. **Engage Teams**: Involve team members who have a deep understanding of existing processes to contribute valuable insights.
Executing a comprehensive waste audit will lay the groundwork for informed decision-making.
Developing a Waste Reduction Plan
A waste reduction plan should serve as a roadmap for implementing change.
This plan needs to be well-rounded, taking into consideration the complexity and nuances of manufacturing processes.
Key Components of a Waste Reduction Plan
– **Assessment of Current Waste Levels**: Use the data from your waste audit to benchmark current performance.
– **Goal Setting**: Incorporate the SMART goals identified earlier.
– **Strategy Development**: Develop strategies to tackle each type of waste identified. For example, implementing just-in-time production techniques to minimize inventory waste.
– **Resource Allocation**: Identify necessary resources, including technology and personnel, to achieve waste reduction targets.
– **Timeline Establishment**: Set a realistic timeline for implementing various components of the plan.
An effective plan is flexible yet comprehensive, accommodating the dynamic nature of manufacturing operations.
Implementing the Waste Reduction Plan
Implementation involves putting the strategies into practice, monitoring progress, and making adjustments as necessary.
Engaging Staff and Stakeholders
Successful implementation relies on the buy-in from everyone involved in the manufacturing process.
Conduct training sessions to educate staff on the importance of waste reduction.
Engage stakeholders by communicating the benefits of waste reduction projects, such as cost savings and environmental responsibility.
Monitoring and Evaluation
Continuously monitor the progress of your waste reduction efforts.
Use key performance indicators (KPIs) to evaluate success against your initial goals.
KPIs could include reductions in waste volumes, cost savings, or improvements in production efficiency.
Technology and Innovation
Leveraging technology can significantly enhance waste reduction efforts.
Adopting New Technologies
– **Automation**: Automated processes can minimize human error and reduce defect waste.
– **Data Analysis Tools**: These tools can provide insights into inefficient practices and suggest improvements.
– **Sustainable Materials**: Consider using materials that are easier to recycle or have a lower environmental impact.
Technology not only saves time but also contributes to precise monitoring and control of waste in manufacturing.
Continuous Improvement
Waste reduction is an ongoing process that requires continuous effort and improvement.
Embrace Lean Principles
Integrating lean manufacturing principles into the organization can facilitate continuous improvement.
Lean principles focus on creating more value with less work and include strategies such as minimizing waste, optimizing processes, and improving product quality.
Feedback and Adaptation
Encourage feedback from employees involved in the production process.
Regularly review and adapt your waste reduction strategies based on changing circumstances and feedback received.
Conclusion
Launching a waste reduction project in the manufacturing industry involves significant planning and commitment.
By understanding the types of waste, setting actionable goals, conducting thorough audits, and leveraging technology, organizations can achieve effective waste reduction.
Implementing these changes not only enhances operational efficiency but also underscores a commitment to environmental sustainability.
With continuous improvement practices in place, manufacturing operations can contribute towards a more sustainable future.
資料ダウンロード
QCD調達購買管理クラウド「newji」は、調達購買部門で必要なQCD管理全てを備えた、現場特化型兼クラウド型の今世紀最高の購買管理システムとなります。
ユーザー登録
調達購買業務の効率化だけでなく、システムを導入することで、コスト削減や製品・資材のステータス可視化のほか、属人化していた購買情報の共有化による内部不正防止や統制にも役立ちます。
NEWJI DX
製造業に特化したデジタルトランスフォーメーション(DX)の実現を目指す請負開発型のコンサルティングサービスです。AI、iPaaS、および先端の技術を駆使して、製造プロセスの効率化、業務効率化、チームワーク強化、コスト削減、品質向上を実現します。このサービスは、製造業の課題を深く理解し、それに対する最適なデジタルソリューションを提供することで、企業が持続的な成長とイノベーションを達成できるようサポートします。
オンライン講座
製造業、主に購買・調達部門にお勤めの方々に向けた情報を配信しております。
新任の方やベテランの方、管理職を対象とした幅広いコンテンツをご用意しております。
お問い合わせ
コストダウンが利益に直結する術だと理解していても、なかなか前に進めることができない状況。そんな時は、newjiのコストダウン自動化機能で大きく利益貢献しよう!
(Β版非公開)