- お役立ち記事
- How to Link Engagement to Profit: Case Studies of High-Profit Factories
How to Link Engagement to Profit: Case Studies of High-Profit Factories
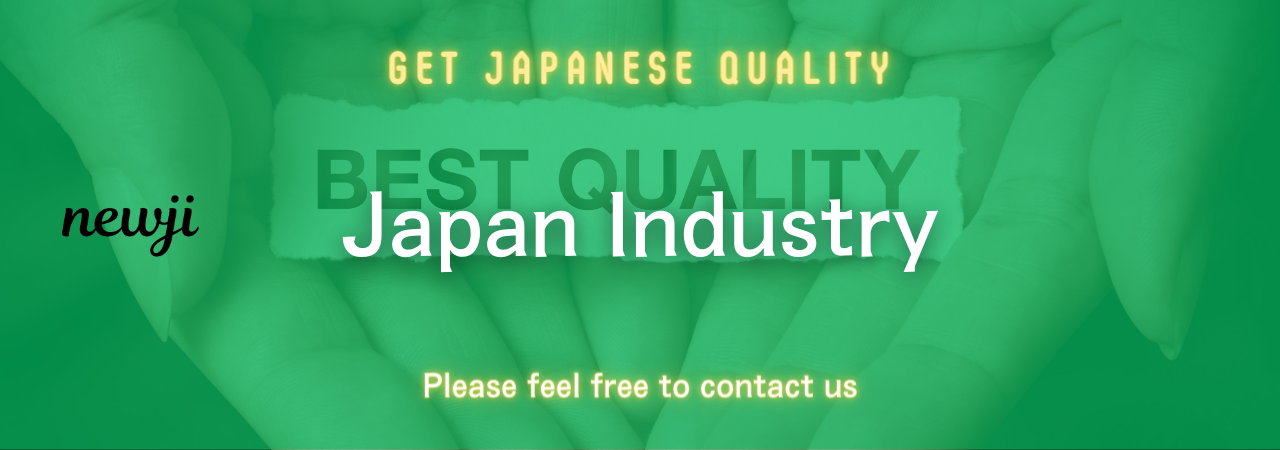
目次
Understanding the Connection Between Engagement and Profit
Employee engagement is more than just a buzzword; it’s a critical factor that can directly impact a company’s profitability.
When employees are fully engaged, they are more productive, innovative, and committed to their work.
But how does this translate into profit, especially in the context of factories?
In some fascinating case studies, we can see a clear link between high engagement levels and impressive profit margins in manufacturing settings.
This article will delve into the details of these cases to uncover valuable insights.
Case Study 1: Implementing Open Communication Lines
Background
Our first case study involves a mid-sized factory that manufactures electronic components.
The factory was struggling with high employee turnover and low productivity levels.
Management decided to implement open communication lines to tackle these issues.
Strategies Implemented
1. **Regular Meetings:** Weekly meetings were held where employees could voice their concerns and offer suggestions.
2. **Feedback Systems:** An anonymous feedback system was introduced to ensure employees felt safe airing grievances.
3. **Manager Training:** Managers underwent training to improve their listening skills and approachability.
Results
Within six months, the factory saw a 20% reduction in employee turnover and a 15% increase in productivity.
Employee engagement scores went up significantly, and the factory’s profit margins saw a corresponding increase of 12%.
Open communication lines allowed employees to feel heard and valued, boosting their engagement and, ultimately, the company’s profit.
Case Study 2: Investing in Employee Development
Background
The second case study focuses on a large automotive parts factory facing challenges with quality control and production efficiency.
To tackle these issues, the factory decided to invest in employee development programs.
Strategies Implemented
1. **Skill Development Workshops:** Regular workshops were organized to upskill workers in the latest manufacturing techniques.
2. **Leadership Programs:** Potential leaders were given opportunities to attend leadership training courses.
3. **Growth Plans:** Individual growth plans were created to help employees see a clear career path within the organization.
Results
Over a year, the factory saw a 25% improvement in production quality and a 30% reduction in defects.
Employee surveys indicated a significant rise in engagement levels, as employees felt their skills were being valued and developed.
This resulted in a 20% increase in profitability, showcasing how investing in employee development directly contributes to higher profits.
Case Study 3: Enhancing Work-Life Balance
Background
Our third case study examines a small textile factory that was experiencing high levels of employee burnout and absenteeism.
The factory decided to enhance work-life balance to address these issues.
Strategies Implemented
1. **Flexible Schedules:** Employees were allowed to choose flexible working hours to better balance their personal and work lives.
2. **Remote Work Options:** Where possible, remote work options were introduced.
3. **Wellness Programs:** Wellness programs, including yoga and mindfulness sessions, were offered to help employees manage stress.
Results
Within nine months, the factory saw a 40% reduction in absenteeism and a 35% decrease in employee burnout.
Engagement scores went up, and the factory experienced a 15% increase in overall productivity.
The improved work-life balance led to happier, more engaged employees, which in turn resulted in a 10% boost in profit margins.
Case Study 4: Creating a Positive Work Environment
Background
The fourth case study focuses on a food processing factory where morale was at an all-time low.
Management decided to create a more positive work environment to combat this issue.
Strategies Implemented
1. **Employee Recognition Programs:** Regular recognition programs were introduced to celebrate employee contributions.
2. **Team Building Activities:** Monthly team-building activities were organized to foster a sense of camaraderie.
3. **Facility Improvements:** The factory improved its facilities by introducing better break rooms and recreational areas.
Results
Over six months, employee satisfaction and engagement levels increased substantially.
The factory saw a 20% rise in productivity and a corresponding 18% increase in profit margins.
The positive work environment made employees feel more valued and motivated, leading to higher engagement and profitability.
Final Thoughts
The case studies demonstrate a clear link between employee engagement and profitability in various factory settings.
Whether through open communication, employee development, work-life balance, or a positive work environment, the key is to make employees feel valued and engaged.
By implementing these strategies, factories can improve not only their employee engagement scores but also their bottom line.
It’s a win-win situation that any factory can achieve with the right approach.
資料ダウンロード
QCD調達購買管理クラウド「newji」は、調達購買部門で必要なQCD管理全てを備えた、現場特化型兼クラウド型の今世紀最高の購買管理システムとなります。
ユーザー登録
調達購買業務の効率化だけでなく、システムを導入することで、コスト削減や製品・資材のステータス可視化のほか、属人化していた購買情報の共有化による内部不正防止や統制にも役立ちます。
NEWJI DX
製造業に特化したデジタルトランスフォーメーション(DX)の実現を目指す請負開発型のコンサルティングサービスです。AI、iPaaS、および先端の技術を駆使して、製造プロセスの効率化、業務効率化、チームワーク強化、コスト削減、品質向上を実現します。このサービスは、製造業の課題を深く理解し、それに対する最適なデジタルソリューションを提供することで、企業が持続的な成長とイノベーションを達成できるようサポートします。
オンライン講座
製造業、主に購買・調達部門にお勤めの方々に向けた情報を配信しております。
新任の方やベテランの方、管理職を対象とした幅広いコンテンツをご用意しております。
お問い合わせ
コストダウンが利益に直結する術だと理解していても、なかなか前に進めることができない状況。そんな時は、newjiのコストダウン自動化機能で大きく利益貢献しよう!
(Β版非公開)