- お役立ち記事
- How to maintain quality with multiple suppliers for mid-level employees in the purchasing department
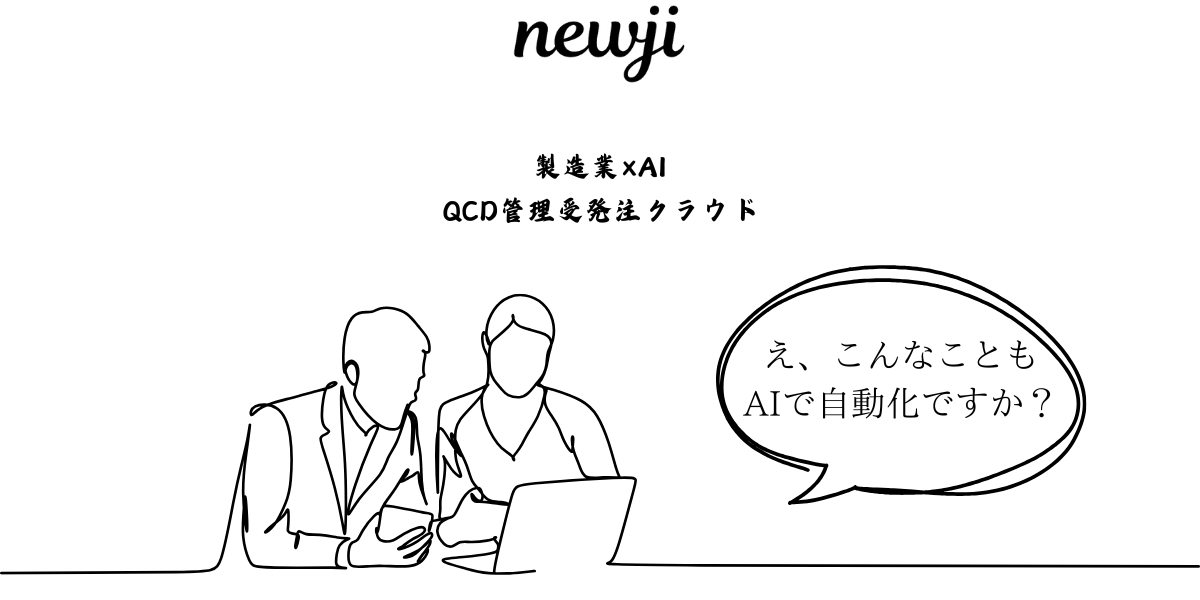
How to maintain quality with multiple suppliers for mid-level employees in the purchasing department
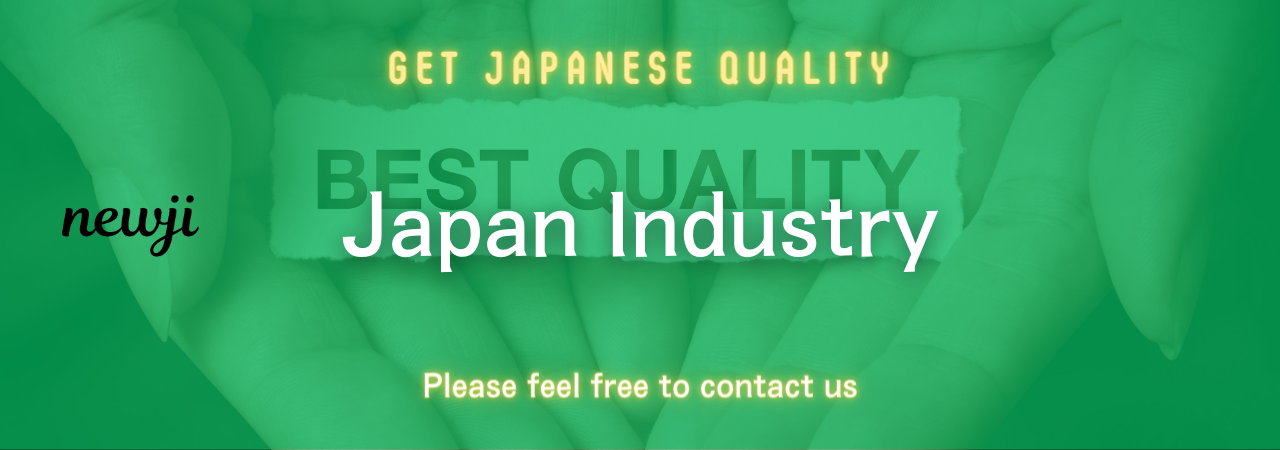
目次
Understanding the Importance of Supplier Quality
In the world of purchasing, particularly for mid-level employees, maintaining quality with multiple suppliers can be a challenging task.
Quality is the backbone of any product or service offered by a company.
Ensuring that all suppliers meet the required standards is crucial for the company’s success and reputation.
Consistency in quality from all suppliers not only helps in achieving business goals but also builds trust with customers.
Establishing Clear Standards and Expectations
The first step to maintaining quality with multiple suppliers is to establish clear standards and expectations.
Communicate your company’s quality requirements to all suppliers clearly and consistently.
This involves setting specific measurable criteria that suppliers must meet to be considered compliant.
These criteria can include aspects like material quality, delivery timelines, and cost constraints.
Providing suppliers with a comprehensive guide or manual can help clarify these expectations.
Developing a Supplier Scorecard
One effective way to measure supplier performance is by developing a supplier scorecard.
A supplier scorecard provides an organized method to assess each supplier against the established standards.
It typically includes metrics related to quality, delivery, cost, and flexibility.
By regularly updating and reviewing this scorecard, purchasing employees can identify areas where suppliers excel and where improvements are necessary.
Building Strong Relationships with Suppliers
Building strong relationships with suppliers is fundamental to ensuring quality.
When suppliers feel valued and understood, they are more likely to go the extra mile to meet your company’s quality requirements.
Engage with your suppliers regularly through meetings, feedback sessions, and site visits.
Understanding their processes and challenges can foster a cooperative relationship that supports mutual growth and quality improvements.
Collaborative Problem Solving
Should a quality issue arise, approach the situation with a collaborative mindset.
Work with the supplier to identify the root cause of the problem and develop a solution together.
This joint effort not only resolves the issue faster but also strengthens the trust between your company and the supplier.
Remember, the goal is not just to fix immediate problems but to prevent future occurrences.
Incorporating Technology and Automation
Utilizing technology can be a game-changer in maintaining supplier quality.
Implementing software solutions that offer real-time data analytics can provide insights into supplier performance.
Automation can streamline tasks such as order processing and inventory management, reducing the margin for error.
Consider investing in systems that offer supplier portals to enhance communication and transparency.
Conducting Regular Audits and Inspections
Regular audits and inspections are vital in maintaining supplier quality.
These processes help ensure that suppliers are consistently adhering to the standards set.
Audits can be scheduled or unscheduled and include a detailed examination of records, quality control processes, and product outputs.
Keeping an inspection checklist can simplify the process and ensure a comprehensive review.
Continuous Improvement and Training
Fostering a culture of continuous improvement is essential in achieving long-term quality standards with suppliers.
Encourage suppliers to adopt best practices and innovative techniques that can enhance quality.
Offering training sessions or workshops can provide suppliers with the knowledge and skills required to meet and exceed your quality standards.
Monitoring Market Trends
Stay informed about market trends that could impact supplier performance and quality.
Understanding the broader market dynamics can help your company and suppliers anticipate changes and adapt accordingly.
Being proactive rather than reactive ensures that quality is maintained irrespective of external influences.
Balancing Cost and Quality
Balancing cost and quality is one of the most significant challenges for purchasing employees.
While it might be tempting to choose suppliers based on cost alone, inferior quality can lead to higher costs in the long run due to rework, returns, and lost customer trust.
Evaluate potential suppliers based on a comprehensive analysis that includes both cost and quality factors.
Building relationships based on quality will yield greater value over time.
Conclusion
Maintaining quality with multiple suppliers requires a strategic approach centered on clear communication, collaborative relationships, and continuous improvement.
By establishing standards, utilizing technology, conducting regular audits, and balancing cost and quality, mid-level employees in the purchasing department can ensure that supplier performance aligns with the company’s expectations.
Ultimately, quality becomes a shared responsibility, fostering a network of committed partners dedicated to excellence.
資料ダウンロード
QCD調達購買管理クラウド「newji」は、調達購買部門で必要なQCD管理全てを備えた、現場特化型兼クラウド型の今世紀最高の購買管理システムとなります。
ユーザー登録
調達購買業務の効率化だけでなく、システムを導入することで、コスト削減や製品・資材のステータス可視化のほか、属人化していた購買情報の共有化による内部不正防止や統制にも役立ちます。
NEWJI DX
製造業に特化したデジタルトランスフォーメーション(DX)の実現を目指す請負開発型のコンサルティングサービスです。AI、iPaaS、および先端の技術を駆使して、製造プロセスの効率化、業務効率化、チームワーク強化、コスト削減、品質向上を実現します。このサービスは、製造業の課題を深く理解し、それに対する最適なデジタルソリューションを提供することで、企業が持続的な成長とイノベーションを達成できるようサポートします。
オンライン講座
製造業、主に購買・調達部門にお勤めの方々に向けた情報を配信しております。
新任の方やベテランの方、管理職を対象とした幅広いコンテンツをご用意しております。
お問い合わせ
コストダウンが利益に直結する術だと理解していても、なかなか前に進めることができない状況。そんな時は、newjiのコストダウン自動化機能で大きく利益貢献しよう!
(Β版非公開)