- お役立ち記事
- How to make prototypes of plastic scraps for use in upcycled product development
月間76,176名の
製造業ご担当者様が閲覧しています*
*2025年3月31日現在のGoogle Analyticsのデータより
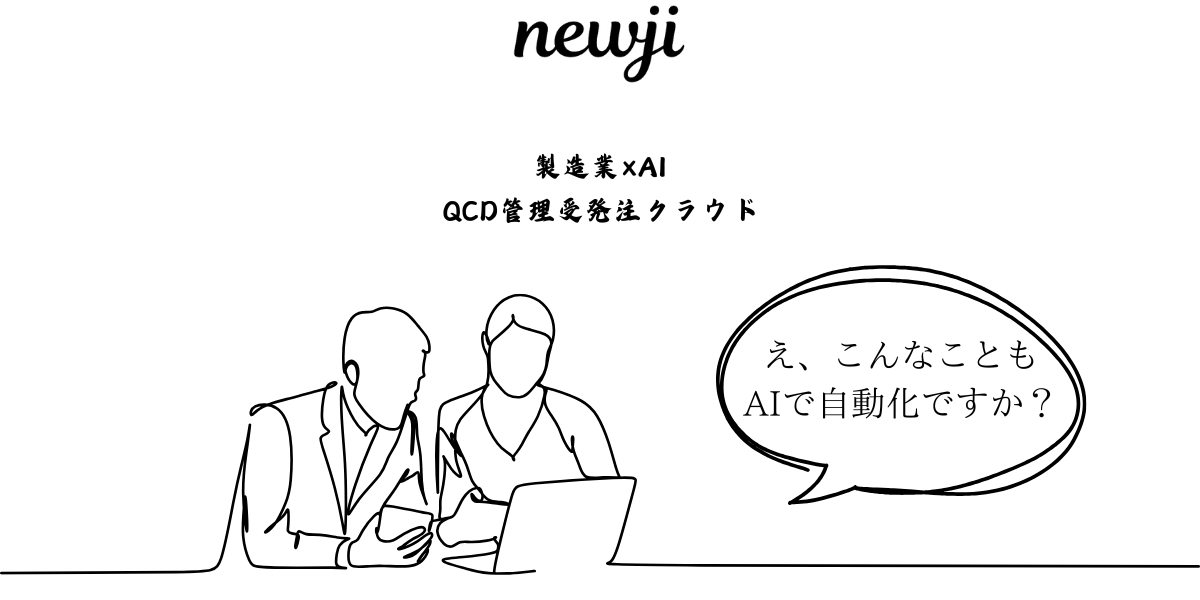
How to make prototypes of plastic scraps for use in upcycled product development
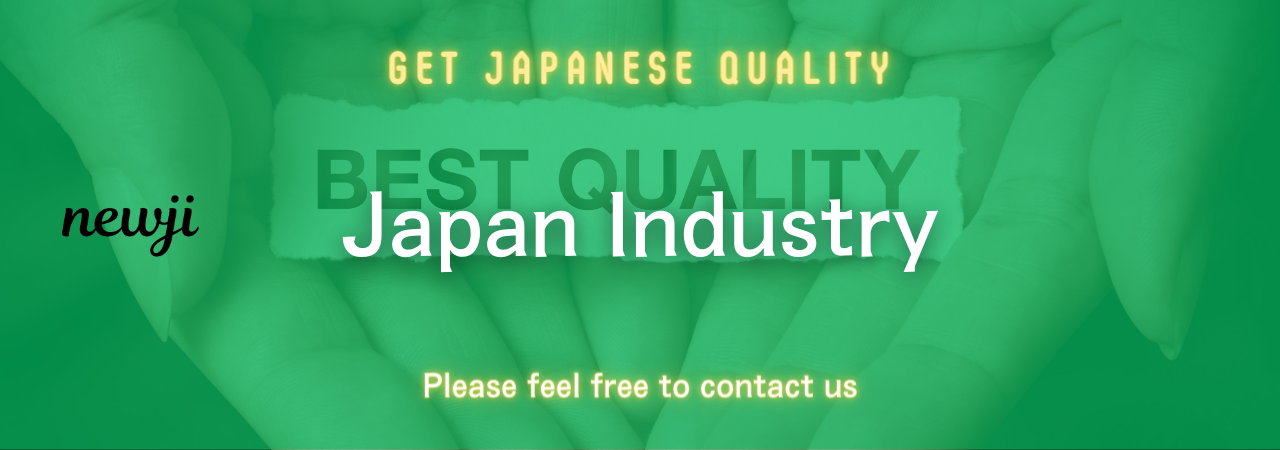
目次
Introduction to Upcycling Plastic Scraps
Upcycling is a practical and creative way to transform waste materials into valuable products.
Plastic, being one of the most ubiquitous waste products today, presents an excellent opportunity for upcycling.
Crafting prototypes from plastic scraps is a great method to visualize and develop new upcycled products.
These prototypes can demonstrate the potential of discarded plastic, offering both environmental and economic benefits.
Collecting and Sorting Plastic Scraps
The first step in creating upcycled products is gathering the necessary raw materials.
This involves collecting various plastic scraps, which might range from used bottles to discarded packaging.
It’s important to ensure that the plastics are clean and free from any hazardous contaminants.
Once collected, sorting the plastics based on type is crucial.
Different types of plastic, such as PET, HDPE, and PVC, have unique properties and melting points.
Sorting them correctly will make the melting process more efficient and ensure the final product’s quality.
Cleaning and Preparing the Plastic
After sorting the plastics, the next step is thorough cleaning.
Remove labels, dirt, and any other residues that might affect the quality of the prototype.
This can be done with water and mild detergent, followed by a rinse with clean water.
Once cleaned, the plastic should be dried completely.
Moisture can interfere with the heating process and result in a flawed prototype.
You may also need to shred the plastics into smaller pieces to make the melting process easier and more uniform.
Melting and Molding Plastic
With your plastic pieces ready, it’s time to melt them down and mold them into a prototype.
Use a heat source that’s appropriate for the plastic type you’re working with, ensuring you stay within the recommended temperature ranges to avoid releasing toxic fumes.
It is advisable to work in a well-ventilated area or use a specialized plastic melting machine.
Once the plastic is melted, it’s ready to be poured into a mold.
Molds can be made from a variety of materials, such as silicone or metal, depending on the complexity and detail required for the prototype.
Allow the plastic to cool and harden within the mold, forming the initial shape of your prototype.
Creating DIY Molds
If you don’t have access to pre-made molds, creating your own can be a simple alternative.
Materials like plaster or clay can be fashioned into custom shapes, offering a personalized approach to prototype design.
Coat the mold with a release agent to ensure the plastic can be easily removed once cooled.
Innovative Techniques for Unique Designs
Experiment with additional materials and techniques to enhance your prototype.
For instance, you can incorporate natural fibers or dyes from plants to add color and texture.
Layering different types of plastics can also create unique patterns and structural properties.
Assembling and Finishing the Prototype
Once the melted plastic has cooled and solidified, remove it from the mold for assembly.
Depending on your prototype, this could involve joining different pieces together using adhesive or additional heating techniques.
Finishing touches are vital to making your prototype realistic and practical.
This might include sanding rough edges, painting, or adding functionality features.
These steps not only improve the aesthetic of your prototype but test its viability as a marketable product.
Testing and Iterating the Prototype
With your prototype complete, the next step is testing its functionality and durability.
This includes examining how it holds up under stress, its usability, and its aesthetic appeal.
Gather feedback from potential users and make note of areas that can be improved.
Iterate on your prototype based on the testing phase.
Make adjustments to the design, materials, or manufacturing process as needed.
This iterative process is essential to creating an upcycled product that is both effective and appealing.
Environmental and Economic Benefits
Creating prototypes from upcycled plastic provides numerous benefits.
Environmentally, it reduces waste in landfills and decreases the demand for virgin plastics.
Economically, it can lead to innovative products with cost-effective production processes.
Businesses can leverage upcycling as part of their sustainability initiatives, attracting eco-conscious consumers and enhancing their brand image.
It’s a win-win scenario that highlights the importance of innovation in solving environmental challenges.
Conclusion
Prototyping with plastic scraps is more than just a creative endeavor; it’s a step toward a sustainable future.
Through careful collection, sorting, and processing, new products can emerge from what was once considered waste.
The journey from discarded plastic to a functional prototype is a testament to the power of upcycling.
By embracing these techniques, we contribute to a greener planet while uncovering new economic opportunities.
資料ダウンロード
QCD管理受発注クラウド「newji」は、受発注部門で必要なQCD管理全てを備えた、現場特化型兼クラウド型の今世紀最高の受発注管理システムとなります。
ユーザー登録
受発注業務の効率化だけでなく、システムを導入することで、コスト削減や製品・資材のステータス可視化のほか、属人化していた受発注情報の共有化による内部不正防止や統制にも役立ちます。
NEWJI DX
製造業に特化したデジタルトランスフォーメーション(DX)の実現を目指す請負開発型のコンサルティングサービスです。AI、iPaaS、および先端の技術を駆使して、製造プロセスの効率化、業務効率化、チームワーク強化、コスト削減、品質向上を実現します。このサービスは、製造業の課題を深く理解し、それに対する最適なデジタルソリューションを提供することで、企業が持続的な成長とイノベーションを達成できるようサポートします。
製造業ニュース解説
製造業、主に購買・調達部門にお勤めの方々に向けた情報を配信しております。
新任の方やベテランの方、管理職を対象とした幅広いコンテンツをご用意しております。
お問い合わせ
コストダウンが利益に直結する術だと理解していても、なかなか前に進めることができない状況。そんな時は、newjiのコストダウン自動化機能で大きく利益貢献しよう!
(β版非公開)