- お役立ち記事
- How to manage raw material price fluctuations to reduce purchasing costs
月間76,176名の
製造業ご担当者様が閲覧しています*
*2025年3月31日現在のGoogle Analyticsのデータより
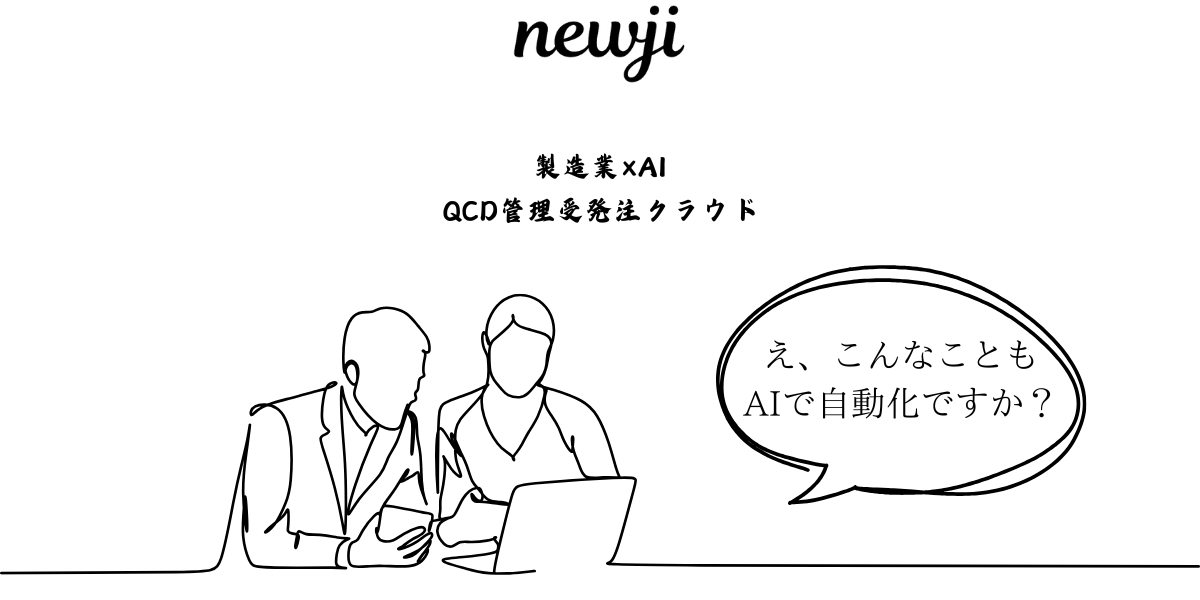
How to manage raw material price fluctuations to reduce purchasing costs
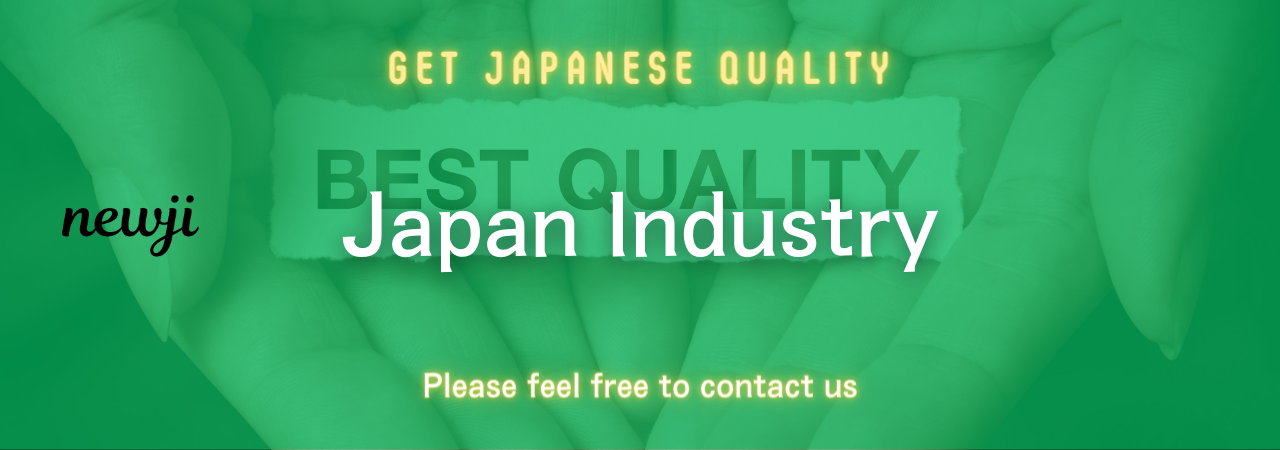
目次
Understanding Raw Material Price Fluctuations
Raw material price fluctuations are inevitable in various industries, ranging from manufacturing to food production.
These fluctuations can be caused by a multitude of factors such as changes in supply and demand, geopolitical events, natural disasters, and even changes in currency exchange rates.
Understanding these factors is critical for businesses to manage costs and maintain profitability.
When raw material prices soar, businesses may experience increased production costs.
This can reduce profit margins unless measures are taken to counterbalance these costs.
On the flip side, if prices fall significantly, it might benefit businesses by reducing costs, but it could also indicate supply chain instability or weak demand.
Strategies to Manage Price Fluctuations
To effectively manage raw material price fluctuations, businesses can adopt several strategies.
These strategies help in reducing purchasing costs while ensuring a stable supply of essential materials.
1. Long-Term Contracts
One of the most effective ways to manage price fluctuations is through long-term contracts with suppliers.
These contracts can lock in prices for a certain period, providing price stability and predictability.
Businesses benefit by securing a steady supply at a known cost, thereby protecting themselves from sudden price spikes.
However, long-term contracts also require careful negotiation to avoid potential pitfalls.
Factors such as changes in demand and market conditions should be considered.
Both parties need to agree on terms that are beneficial in the long run.
2. Diversifying Suppliers
Relying on a single supplier can be risky, especially during periods of price volatility.
By diversifying suppliers, businesses can mitigate risks associated with price hikes or supply disruptions from a particular source.
Engaging multiple suppliers ensures that a business can compare prices and negotiate better deals.
Additionally, having a diverse supplier base can provide leverage during negotiations, as businesses are not solely reliant on one supplier for their needs.
3. Hedging Strategies
Hedging is a financial strategy used to protect against price fluctuations.
It involves using financial instruments like futures contracts, options, and swaps to lock in prices for raw materials.
This approach can be complex, but it offers a way to manage risk.
Businesses seeking to hedge must understand the financial markets and engage in careful planning.
Consulting with financial experts or advisors can help in crafting an appropriate hedging strategy tailored to the business’s needs.
4. Demand Forecasting and Inventory Management
Accurate demand forecasting allows businesses to anticipate needs and adjust purchases accordingly.
By understanding demand patterns, businesses can optimize their inventory levels to avoid overstocking or understocking.
Modern technology and software solutions can aid in demand forecasting by analyzing historical data and market trends.
This approach supports better decision-making and cost management by ensuring that raw material purchases align with actual demand.
Leveraging Technology and Data Analytics
Technology plays a crucial role in managing raw material price fluctuations.
Data analytics can provide insights into market trends, supplier performance, and price movements.
By analyzing data, businesses can make informed decisions regarding supplier selection, purchasing timing, and inventory levels.
Investing in supply chain management software can streamline operations and enhance visibility across the supply chain.
This enables businesses to respond quickly to changes in the market and optimize their procurement processes.
Moreover, machine learning algorithms can predict price trends, allowing businesses to plan future purchases with greater accuracy.
These technological advancements support cost-saving initiatives and improve operational efficiency.
Building Strong Supplier Relationships
Establishing strong relationships with suppliers can be advantageous during times of price volatility.
Open communication and collaboration can lead to more favorable terms and conditions.
Suppliers may offer discounts, flexible payment terms, or other incentives to businesses with whom they have a strong rapport.
Moreover, a collaborative relationship can lead to improved quality, timely deliveries, and innovative solutions tailored to the business’s needs.
Building trust and fostering long-term partnerships can thus be valuable in navigating the challenges of price fluctuations.
Conclusion: Prioritizing Flexibility and Adaptability
Managing raw material price fluctuations is essential for maintaining profitability and reducing purchasing costs.
By implementing strategies such as long-term contracts, supplier diversification, hedging, and demand forecasting, businesses can better manage these challenges.
Leveraging technology and data analytics can further enhance decision-making and operational efficiency.
Finally, building strong supplier relationships fosters collaboration and may result in better terms and support during volatile times.
Ultimately, the key to success lies in being flexible and adaptable.
By staying informed and being proactive, businesses can navigate the complexities of raw material price fluctuations and position themselves for sustainable growth.
資料ダウンロード
QCD管理受発注クラウド「newji」は、受発注部門で必要なQCD管理全てを備えた、現場特化型兼クラウド型の今世紀最高の受発注管理システムとなります。
ユーザー登録
受発注業務の効率化だけでなく、システムを導入することで、コスト削減や製品・資材のステータス可視化のほか、属人化していた受発注情報の共有化による内部不正防止や統制にも役立ちます。
NEWJI DX
製造業に特化したデジタルトランスフォーメーション(DX)の実現を目指す請負開発型のコンサルティングサービスです。AI、iPaaS、および先端の技術を駆使して、製造プロセスの効率化、業務効率化、チームワーク強化、コスト削減、品質向上を実現します。このサービスは、製造業の課題を深く理解し、それに対する最適なデジタルソリューションを提供することで、企業が持続的な成長とイノベーションを達成できるようサポートします。
製造業ニュース解説
製造業、主に購買・調達部門にお勤めの方々に向けた情報を配信しております。
新任の方やベテランの方、管理職を対象とした幅広いコンテンツをご用意しております。
お問い合わせ
コストダウンが利益に直結する術だと理解していても、なかなか前に進めることができない状況。そんな時は、newjiのコストダウン自動化機能で大きく利益貢献しよう!
(β版非公開)