- お役立ち記事
- How to Manufacture Highly Durable Polycarbonate Products
月間76,176名の
製造業ご担当者様が閲覧しています*
*2025年3月31日現在のGoogle Analyticsのデータより
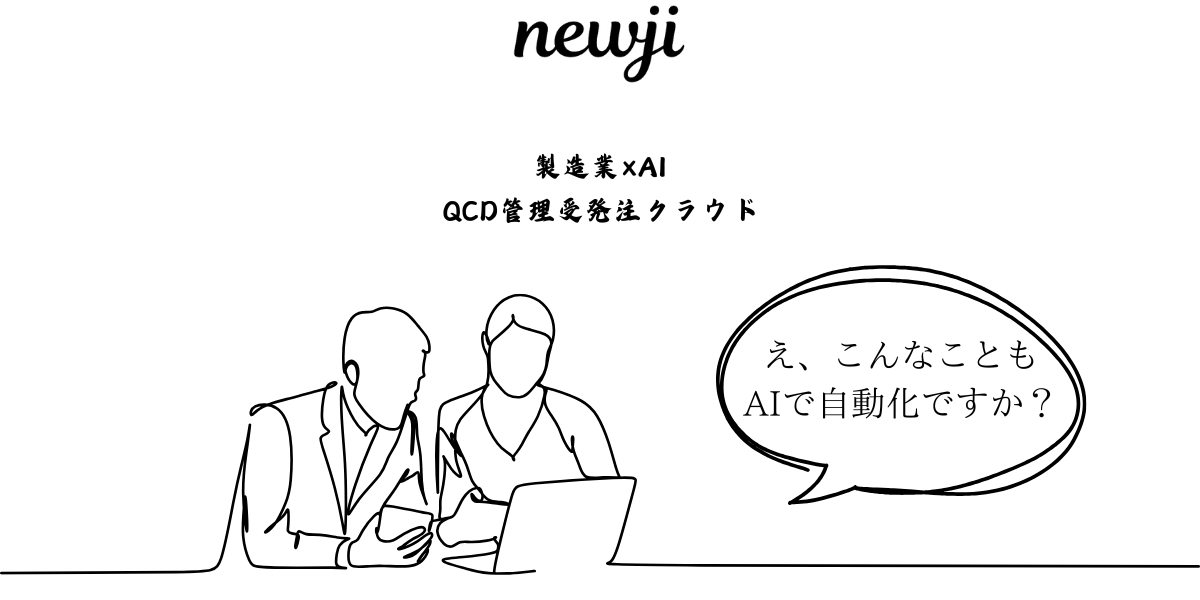
How to Manufacture Highly Durable Polycarbonate Products
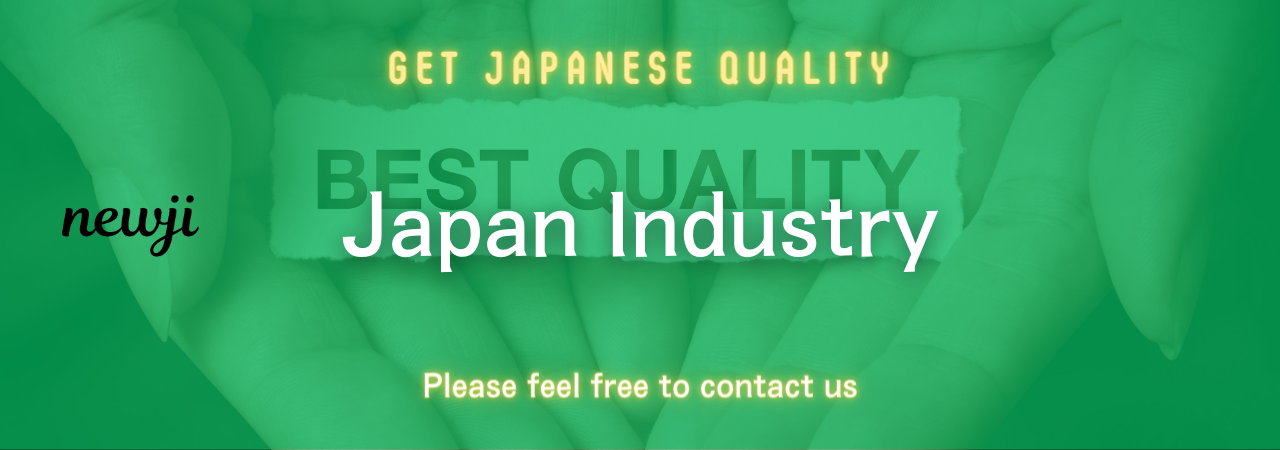
Polycarbonate is a versatile and highly durable material widely used across various industries.
Its exceptional impact resistance, transparency, and thermal stability make it an excellent choice for manufacturing products that need to withstand harsh conditions and heavy use.
In this article, we will explore the process of manufacturing highly durable polycarbonate products, guiding you through each step and the key considerations involved.
目次
Understanding Polycarbonate
Polycarbonate is a type of plastic known for its strength and clarity.
It is used in products ranging from eyeglass lenses to bulletproof windows and is chosen for its ability to maintain its shape and properties under stressful conditions.
This makes it an ideal material for industries that demand both resilience and versatility.
Properties of Polycarbonate
Polycarbonate is incredibly strong yet lightweight.
It can be molded into various shapes without losing its inherent durability.
Its transparency is similar to that of glass, yet it is much lighter and shatter-resistant.
Polycarbonate also has excellent thermal stability, withstanding temperatures from -40 to 250 degrees Fahrenheit without deforming.
Manufacturing Process of Polycarbonate Products
Creating durable polycarbonate products involves a systematic process that ensures the material’s properties are optimized.
Below is a step-by-step guide to the manufacturing process.
1. Designing the Product
Before manufacturing begins, designing the product is crucial.
Designers need to consider the product’s purpose, the environmental conditions it will face, and aesthetic requirements.
Using computer-aided design (CAD) software helps in visualizing the final product and identifying potential structural issues.
2. Selecting the Right Grade of Polycarbonate
Different applications require different polycarbonate grades.
For instance, flame retardant polycarbonate may be needed for electrical components, while UV-stabilized polycarbonate is suitable for outdoor use.
Selecting the correct grade ensures that the product has the necessary properties for its intended use.
3. Material Preparation
Once the design and material grade are finalized, the raw polycarbonate pellets are prepared.
These pellets are thoroughly cleaned to remove any impurities which could affect the product’s clarity and strength.
Colorants or additives may be mixed with the pellets if required for the application.
4. Molding Process
The next step is molding the product.
There are two primary methods for molding polycarbonate: injection molding and extrusion.
Injection Molding
Injection molding is used for complex and detailed shapes.
In this process, the prepared polycarbonate pellets are fed into a heated barrel.
The material melts and is then injected into a mold cavity where it cools and solidifies into the desired shape.
This method is ideal for producing items like lenses or optical disks.
Extrusion
Extrusion is used to create long products with consistent cross-sections, such as sheets and panels.
The polycarbonate pellets are melted and pushed through a die that gives the product its shape.
Once cooled, the item is cut to the required dimensions.
5. Post-Processing
After molding, products may undergo additional processes to enhance their properties or functionality.
These can include annealing to relieve internal stresses, coating for UV protection, or mechanical processing like drilling or cutting to refine the product shape.
6. Quality Control
Quality control is essential throughout the manufacturing process to ensure the final product meets all specifications and standards.
This involves rigorous testing for strength, clarity, dimension accuracy, and overall appearance.
Quality assurance teams use various tools and methodologies to evaluate these aspects, ensuring that only top-quality products reach the market.
Environmental and Safety Considerations
Polycarbonate manufacturing must adhere to strict safety and environmental standards.
Recycling and Sustainability
Polycarbonate is recyclable, which is a significant advantage in terms of sustainability.
Manufacturers are increasingly adopting recycling practices to reduce waste and environmental impact.
Recycled polycarbonate can be used in less demanding applications, thus extending the material’s lifecycle.
Occupational Safety
Ensuring the safety of the workforce is paramount.
This involves providing adequate personal protective equipment and ensuring that machinery and facilities comply with the latest safety regulations.
Advantages of Polycarbonate Products
The benefits of polycarbonate products are numerous, which is why they are highly sought after in various fields.
Durability
Polycarbonate products are built to last.
Their ability to withstand impact without cracking or breaking makes them ideal for applications involving high levels of physical demand.
Optical Clarity
Despite their toughness, polycarbonate products maintain excellent clarity, making them suitable for use in optical and lighting applications.
Thermal Resistance
Their capability to withstand significant temperature fluctuations without deforming ensures they are suitable for a wide range of environments.
Challenges in Manufacturing
While polycarbonate offers numerous advantages, its manufacturing does present some challenges.
Cost
Polycarbonate is more expensive than materials like acrylic, which can be a limiting factor in some projects.
The cost of high-quality molds needed for precision manufacturing also adds to the overall expense.
Scratching
Although tough, polycarbonate can be prone to scratches without additional coatings.
Manufacturers often apply scratch-resistant layers to enhance the product’s durability in environments where abrasive wear is likely.
In summary, manufacturing highly durable polycarbonate products involves a careful selection of materials and methods tailored to the application’s demands.
The process includes product design, material preparation, molding, post-processing, and stringent quality control.
Despite some challenges, the advantages of polycarbonate—such as impact resistance, optical clarity, and thermal stability—make it an outstanding choice for durable products.
By adhering to environmental and safety standards, polycarbonate manufacturing can sustain long-term benefits while minimizing its environmental footprint.
資料ダウンロード
QCD管理受発注クラウド「newji」は、受発注部門で必要なQCD管理全てを備えた、現場特化型兼クラウド型の今世紀最高の受発注管理システムとなります。
ユーザー登録
受発注業務の効率化だけでなく、システムを導入することで、コスト削減や製品・資材のステータス可視化のほか、属人化していた受発注情報の共有化による内部不正防止や統制にも役立ちます。
NEWJI DX
製造業に特化したデジタルトランスフォーメーション(DX)の実現を目指す請負開発型のコンサルティングサービスです。AI、iPaaS、および先端の技術を駆使して、製造プロセスの効率化、業務効率化、チームワーク強化、コスト削減、品質向上を実現します。このサービスは、製造業の課題を深く理解し、それに対する最適なデジタルソリューションを提供することで、企業が持続的な成長とイノベーションを達成できるようサポートします。
製造業ニュース解説
製造業、主に購買・調達部門にお勤めの方々に向けた情報を配信しております。
新任の方やベテランの方、管理職を対象とした幅広いコンテンツをご用意しております。
お問い合わせ
コストダウンが利益に直結する術だと理解していても、なかなか前に進めることができない状況。そんな時は、newjiのコストダウン自動化機能で大きく利益貢献しよう!
(β版非公開)