- お役立ち記事
- How to Manufacture Lightweight Products Using High-Speed Injection Molding Technology
How to Manufacture Lightweight Products Using High-Speed Injection Molding Technology
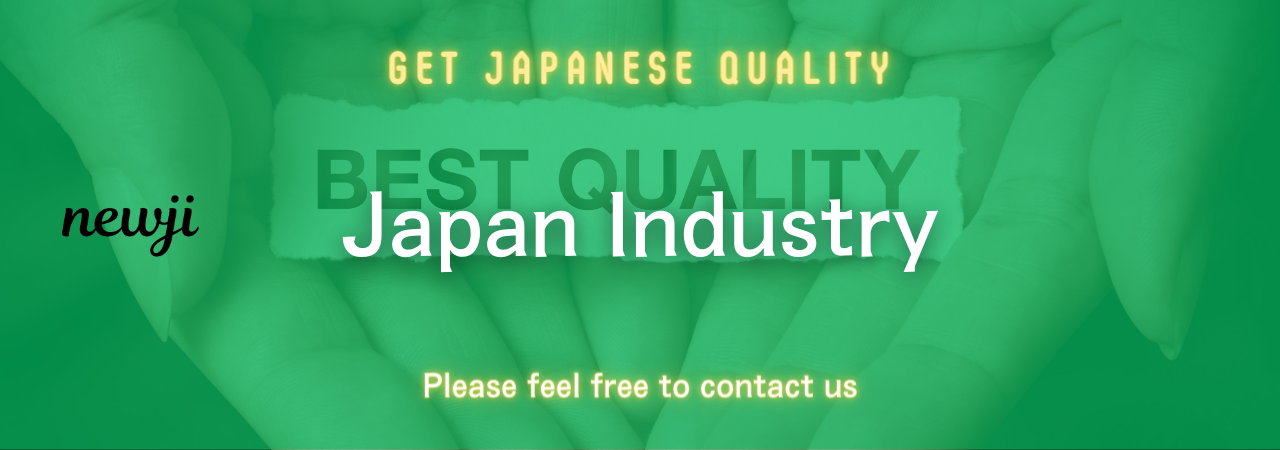
目次
Understanding High-Speed Injection Molding
High-speed injection molding is a revolutionary manufacturing technique used to produce lightweight products rapidly and efficiently.
This technology has gained popularity in various industries, such as automotive, aerospace, and consumer electronics, due to its ability to produce complex and high-quality components.
The basic principle of high-speed injection molding involves injecting molten material into a mold at extremely high speeds.
This ensures that the material fills the mold completely before solidifying, resulting in the creation of precise, detailed, and lightweight products.
Benefits of High-Speed Injection Molding
There are several advantages to using high-speed injection molding technology.
First and foremost is the reduction in cycle time.
By using rapid injection speeds, manufacturers can significantly decrease the time it takes to produce a single part, leading to increased production rates.
Another key benefit is enhanced product quality.
The nature of high-speed injection molding allows for the creation of highly detailed and intricate designs that might be challenging or impossible with other methods.
Additionally, this technique results in low waste production, making it a cost-effective option for manufacturing.
The precise control over injection speed and pressure also reduces material wastage, which has positive environmental implications.
The adaptability of high-speed injection molding to various types of materials, including biodegradable and recyclable plastics, further enhances its sustainability appeal.
Materials Suitable for High-Speed Injection Molding
A wide range of materials is compatible with high-speed injection molding, allowing manufacturers to choose the best option for their specific application.
Thermoplastics are the most common materials used in this process due to their versatility and ease of molding.
Examples of thermoplastics suitable for high-speed injection molding include polypropylene, polycarbonate, and nylon.
Besides thermoplastics, certain thermosetting plastics and elastomers can also be used, depending on the desired properties of the end product.
Each material comes with its unique benefits, such as flexibility, strength, or heat resistance, making material selection an essential part of the design process.
Choosing the Right Material
Selecting the appropriate material for high-speed injection molding requires considering factors like product function, cost, and environmental impact.
Manufacturers must balance these factors to choose a material that meets both performance requirements and budget constraints.
For example, polypropylene is often chosen for its lightweight and cost-effective nature, making it ideal for consumer goods.
On the other hand, polycarbonate might be preferred for its strength and thermal resistance, which is necessary for certain automotive components.
Steps in the High-Speed Injection Molding Process
The high-speed injection molding process involves several detailed steps, each crucial for ensuring the production of high-quality and lightweight components.
1. Mold Design and Fabrication
The first step is designing the mold, which plays a critical role in the final product’s dimensions and features.
The mold must be precisely engineered to allow easy filling, complete thermal exchange, and effective ejection of the final part.
Utilizing advanced computer-aided design (CAD) programs can aid in creating highly detailed mold designs.
Once the design is finalized, the mold is fabricated using durable materials such as steel or aluminum to withstand the high pressures and speeds involved in molding.
2. Material Preparation
Before beginning the molding process, the chosen material must be prepared.
The material is typically mixed with any necessary additives, such as colorants or stabilizers, and then melted to achieve a uniform consistency.
This ensures that the material will flow smoothly and evenly into the mold cavity.
3. Injection Molding
The core of the process is the actual injection of the material into the mold.
During this step, the molten material is injected at high speed into the mold cavity, ensuring it fills the cavity completely and takes on the required shape.
Advanced machines are equipped with precise control systems that monitor parameters such as temperature, pressure, and injection speed.
These systems are essential for achieving optimal results and maintaining consistency across production runs.
4. Cooling and Ejection
Once the mold cavity is filled, the material needs to cool and solidify.
This cooling phase is crucial; it affects the final product’s dimensions and structural integrity.
The quick cooling is often facilitated through hydraulic or air cooling systems integrated into the mold.
After cooling, the mold opens, and the finished product is ejected, ready for any further processing or assembly.
Applications of High-Speed Injection Molding
High-speed injection molding technology is instrumental in creating lightweight components for diverse applications.
In the automotive industry, it produces parts like dashboards, bumpers, and other interior elements that require precise dimensions and reduced weight for improved fuel efficiency.
The technology is also prevalent in the electronics sector, where it fabricates cases, connectors, and components that demand high precision and reduced mass for the technical devices.
Additionally, consumer goods like food containers, toys, and household items benefit from the rapid production capabilities and high quality achieved through this method.
Conclusion
High-speed injection molding technology is transforming the landscape of manufacturing by offering an efficient way to produce lightweight products with exceptional precision.
Its numerous advantages, such as decreased cycle times, improved quality, and reduced waste, make it an attractive option for various industries.
By understanding the intricacies of this process, manufacturers can leverage its benefits to create innovative products that meet modern demands.
資料ダウンロード
QCD調達購買管理クラウド「newji」は、調達購買部門で必要なQCD管理全てを備えた、現場特化型兼クラウド型の今世紀最高の購買管理システムとなります。
ユーザー登録
調達購買業務の効率化だけでなく、システムを導入することで、コスト削減や製品・資材のステータス可視化のほか、属人化していた購買情報の共有化による内部不正防止や統制にも役立ちます。
NEWJI DX
製造業に特化したデジタルトランスフォーメーション(DX)の実現を目指す請負開発型のコンサルティングサービスです。AI、iPaaS、および先端の技術を駆使して、製造プロセスの効率化、業務効率化、チームワーク強化、コスト削減、品質向上を実現します。このサービスは、製造業の課題を深く理解し、それに対する最適なデジタルソリューションを提供することで、企業が持続的な成長とイノベーションを達成できるようサポートします。
オンライン講座
製造業、主に購買・調達部門にお勤めの方々に向けた情報を配信しております。
新任の方やベテランの方、管理職を対象とした幅広いコンテンツをご用意しております。
お問い合わせ
コストダウンが利益に直結する術だと理解していても、なかなか前に進めることができない状況。そんな時は、newjiのコストダウン自動化機能で大きく利益貢献しよう!
(Β版非公開)