- お役立ち記事
- How to maximize customer satisfaction by utilizing quality charts required by quality assurance departments
How to maximize customer satisfaction by utilizing quality charts required by quality assurance departments
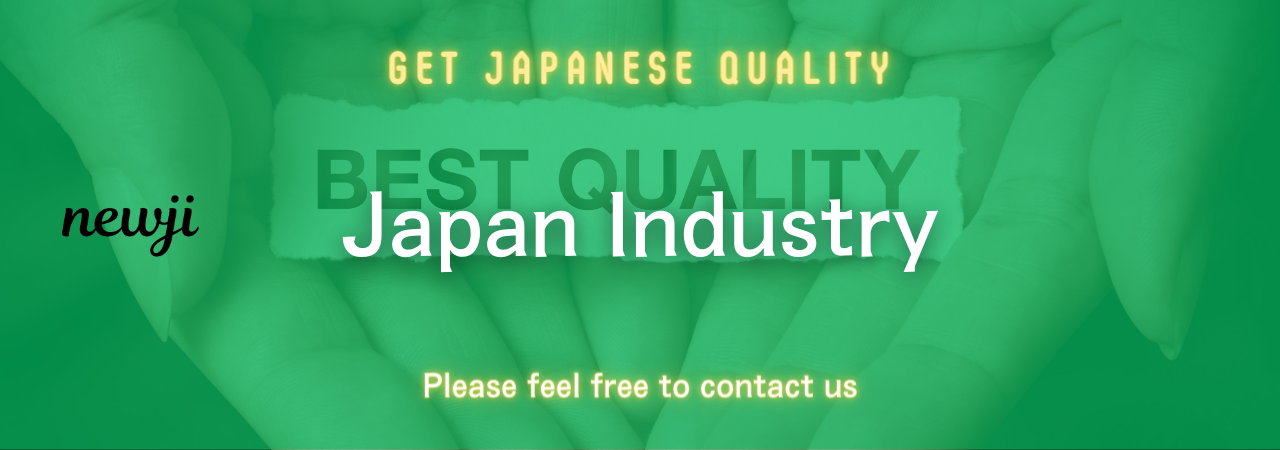
目次
Understanding the Importance of Quality Charts
Customer satisfaction is vital for any successful business, and it can be significantly enhanced through effective quality assurance practices.
One crucial tool used by quality assurance departments is quality charts.
By understanding how to utilize these charts, businesses can improve the quality of their products and services, ultimately leading to higher customer satisfaction.
What Are Quality Charts?
Quality charts are graphical representations of data related to a product’s or service’s quality.
These charts help in monitoring, controlling, and improving quality processes, ensuring that they meet customer expectations consistently.
They come in various types, each serving a specific purpose in the quality assurance process.
Types of Quality Charts
Several types of quality charts exist, each designed to address different aspects of quality control and improvement.
Here are some common types:
Control Charts
Control charts, also known as Shewhart charts or process-behavior charts, are used to monitor a process over time.
They help identify any variations or trends that deviate from customer expectations, allowing businesses to take corrective actions promptly.
By keeping processes within control limits, companies can ensure consistent quality.
Pareto Charts
Pareto charts are used to prioritize issues that need attention based on their impact.
They follow the Pareto principle, which states that 80% of problems are often caused by 20% of the issues.
This chart helps quality assurance teams focus on the most significant factors affecting customer satisfaction.
Histogram
Histograms are used to visualize the distribution of data over a range.
These charts are helpful for identifying patterns, trends, and anomalies in quality data, enabling businesses to pinpoint areas where improvements are needed.
Fishbone Diagram
Also known as cause-and-effect diagrams, fishbone diagrams help identify potential causes of a problem.
This chart aids in brainstorming and organizing factors that may affect product or service quality, helping teams identify root causes for issues impacting customer satisfaction.
Using Quality Charts to Maximize Customer Satisfaction
Quality charts play a vital role in identifying and resolving quality issues that impact customer satisfaction.
Here’s how they can be effectively utilized:
Proactive Problem-Solving
By using control charts, businesses can detect issues before they become significant problems.
This proactive approach helps in maintaining high-quality standards, ensuring customers receive reliable products or services consistently.
Focus on Major Issues
Pareto charts help prioritize quality issues, directing focus and resources to where they are most needed.
By resolving the most impactful problems first, businesses can see a significant boost in customer satisfaction quickly.
Understand Process Variation
Histograms can reveal process variations that might not be apparent through other means.
By understanding these variations, businesses can target improvements more accurately, enhancing overall product or service quality.
Identify Root Causes
Fishbone diagrams enable teams to explore and identify root causes of issues.
Addressing the real cause rather than symptoms ensures long-term solutions and leads to consistent improvements in customer satisfaction.
Steps to Implement Quality Charts in Your Quality Assurance Process
Implementing quality charts in your quality assurance process can be done in several steps:
Step 1: Training and Education
Ensure that your quality assurance team understands different quality charts and their specific applications.
Training sessions can provide the necessary knowledge and skills, ensuring that team members are well-equipped to apply these tools effectively.
Step 2: Data Collection
Accurate data collection is crucial for quality charts to be effective.
Ensure that data is being gathered systematically and is up-to-date, allowing for reliable analysis and insights.
Step 3: Selecting the Right Chart
Choose the appropriate quality chart based on the specific quality issue at hand.
The right chart will provide the clarity needed to address the issue effectively and efficiently.
Step 4: Regular Monitoring
Continuously monitor and update your quality charts to reflect changes and improvements.
Regular reviews ensure your processes stay on track and can quickly adapt to any new quality challenges.
Conclusion
Utilizing quality charts in the quality assurance process is a powerful way to maximize customer satisfaction.
These charts offer valuable insights into the quality performance, facilitating proactive problem-solving and continuous improvement.
By integrating quality charts into your operations, you can enhance your products and services, leading to happier customers and a more successful business.
資料ダウンロード
QCD調達購買管理クラウド「newji」は、調達購買部門で必要なQCD管理全てを備えた、現場特化型兼クラウド型の今世紀最高の購買管理システムとなります。
ユーザー登録
調達購買業務の効率化だけでなく、システムを導入することで、コスト削減や製品・資材のステータス可視化のほか、属人化していた購買情報の共有化による内部不正防止や統制にも役立ちます。
NEWJI DX
製造業に特化したデジタルトランスフォーメーション(DX)の実現を目指す請負開発型のコンサルティングサービスです。AI、iPaaS、および先端の技術を駆使して、製造プロセスの効率化、業務効率化、チームワーク強化、コスト削減、品質向上を実現します。このサービスは、製造業の課題を深く理解し、それに対する最適なデジタルソリューションを提供することで、企業が持続的な成長とイノベーションを達成できるようサポートします。
オンライン講座
製造業、主に購買・調達部門にお勤めの方々に向けた情報を配信しております。
新任の方やベテランの方、管理職を対象とした幅広いコンテンツをご用意しております。
お問い合わせ
コストダウンが利益に直結する術だと理解していても、なかなか前に進めることができない状況。そんな時は、newjiのコストダウン自動化機能で大きく利益貢献しよう!
(Β版非公開)