- お役立ち記事
- How to Maximize Production Efficiency by Shortening Molding Cycle Times
月間76,176名の
製造業ご担当者様が閲覧しています*
*2025年3月31日現在のGoogle Analyticsのデータより
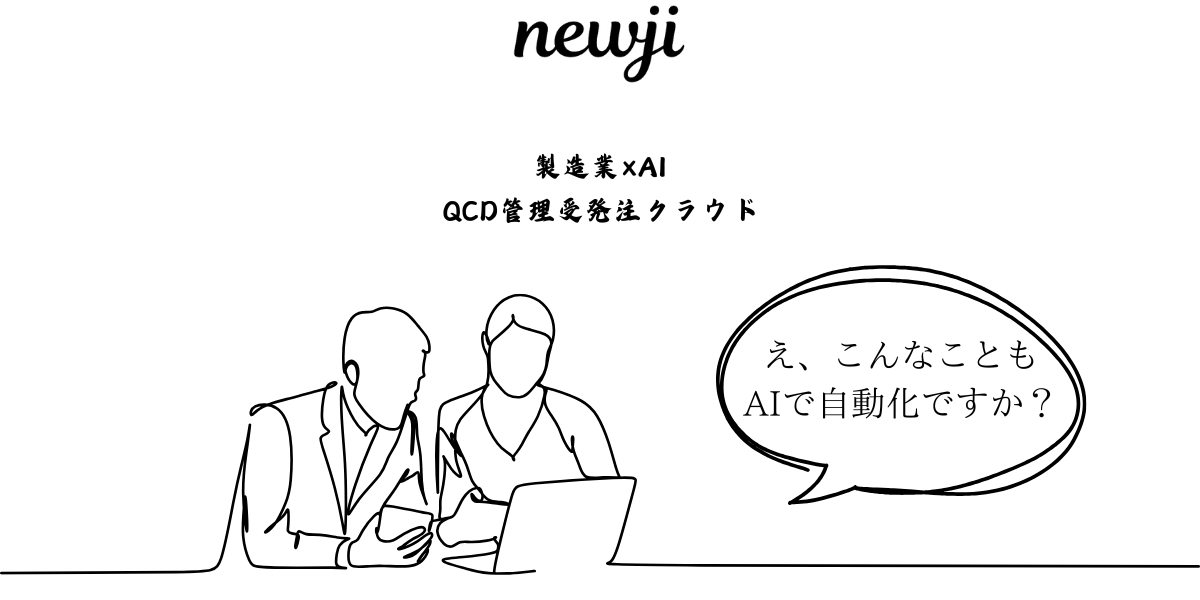
How to Maximize Production Efficiency by Shortening Molding Cycle Times
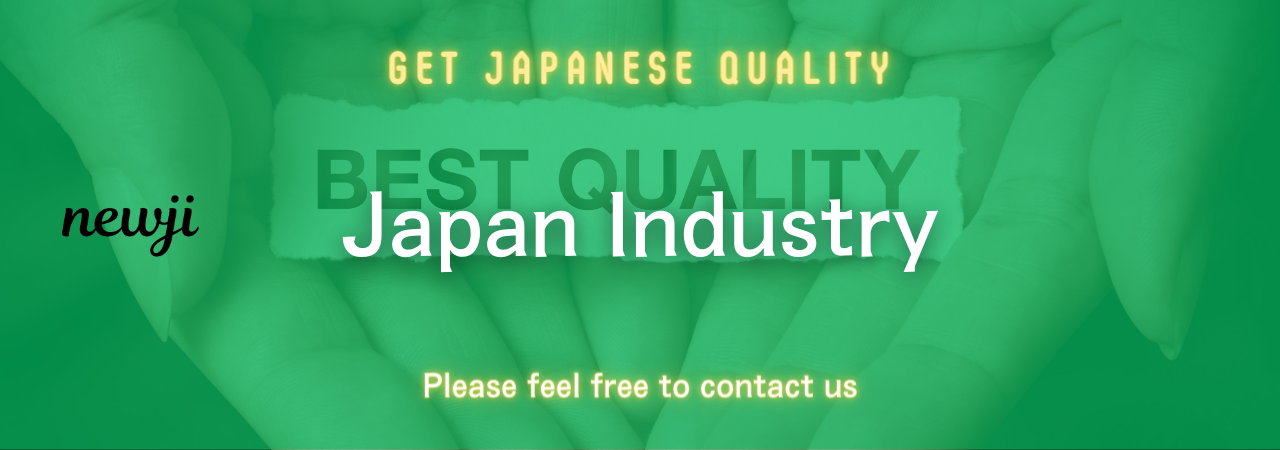
目次
Understanding the Molding Process
Molding is a crucial process in manufacturing various plastic and rubber parts.
This method involves shaping raw materials using a mold to achieve the desired form and size.
To maximize production efficiency, manufacturers aim to shorten the molding cycle times.
Cycle time is the total time taken to complete one cycle of the molding process.
This includes the time needed to fill the mold, cool the product, and eject it from the mold.
Reducing these cycle times can lead to significant improvements in overall production and profitability.
Here are a few effective strategies to achieve this.
Analyzing Current Cycle Times
The first step in improving molding cycle times is to analyze the current process.
Review the overall production to identify any bottlenecks or delays.
Examine each phase of the molding cycle from start to finish.
Pay special attention to filling time, cooling time, and ejection time, as these are often the most time-consuming steps.
With this analysis, manufacturers can pinpoint areas that require enhancement.
Create a detailed report of these findings to serve as a benchmark for implementing changes and assessing improvements over time.
Using Advanced Equipment
Investing in state-of-the-art equipment can drastically reduce cycle times.
Modern machinery often includes faster, more efficient injection systems and precision molds that facilitate quicker cooling.
Variable frequency drives and servo motors can optimize the speed and accuracy of the injection process.
This precision results in more consistent production and reduced scrap rates.
Consider upgrading to machinery with higher clamping force which allows operation at faster speeds without compromising part quality.
Conduct thorough market research to determine which advanced equipment best suits existing manufacturing needs and budget constraints.
Optimizing Mold Design
Superior mold design can directly impact cycle time efficiency.
Collaborate with engineers to adjust part geometry, tweak gate locations, and refine runner layouts.
Utilize computer-aided design (CAD) software to experiment with different configurations and identify designs that improve coolant distribution and minimize material waste.
Multi-cavity molds are another solution for productivity gains.
These molds allow for the production of multiple parts in a single cycle, effectively boosting output rates.
Evaluate and implement design changes with careful testing, ensuring that modifications don’t affect product quality or integrity.
Enhancing Resin Selection and Preparation
Selecting the right resin and preparing it effectively can also influence cycle time.
Choose materials that offer shorter cooling times without compromising the mechanical properties of the final product.
Some resins inherently cool faster and are less prone to defects such as warping or shrinkage.
Properly drying and thoroughly blending materials minimizes impurities and ensures uniform material characteristics.
This attention to material preparation reduces the likelihood of processing issues, facilitating smoother operation throughout the cycle.
Improving Cooling Systems
Cooling time often represents the longest phase of the molding cycle, presenting a significant opportunity for time reductions.
Improving cooling efficiency can be achieved through enhanced mold designs, as previously noted, but also with advanced cooling technologies.
Implement inside-the-mold cooling with sophisticated channels that allow coolant to flow closer to the mold’s surface where heat transfer is most effective.
Experiment with alternative cooling methods, such as conformal cooling, which employs 3D-printed mold inserts designed to optimize coolant flow.
These technologies provide rapid and even cooling, reducing the time needed before ejection.
Regular Maintenance and Process Monitoring
Regular maintenance is critical to maintaining efficient cycle times.
Preventative measures ensure machinery and molds operate under optimal conditions, reducing downtime caused by unexpected malfunctions or wear.
Conduct routine inspections of all equipment, and perform necessary cleaning, lubrication, and calibration.
Utilize process monitoring software to gain a real-time view of operations.
These systems provide valuable insights into potential inefficiencies and alert operators to any deviations from standard parameters.
Addressing issues swiftly maintains a consistent production pace and minimizes prolonged cycle phases.
Training and Workforce Engagement
An adept workforce is integral to achieving shorter molding cycle times.
Continuously train employees on the latest equipment, technologies, and best practices within the industry.
Empower staff with the skills needed to identify inefficiencies and propose viable solutions.
By promoting a collaborative environment, manufacturers harness collective expertise and develop innovative strategies for improvement.
Engagement leads to increased accountability and dedication to operational excellence, resulting in more efficient production cycles.
Conclusion
Shortening molding cycle times requires a multifaceted approach that combines technology, design, and human expertise.
By implementing these strategies, manufacturers can significantly enhance production efficiency, remain competitive, and ultimately boost profitability.
Continuous assessment and adaptation of the processes ensure persistence in achieving desired efficiency gains.
With commitment and innovation, the journey toward maximum productivity is not only achievable but sustainable.
資料ダウンロード
QCD管理受発注クラウド「newji」は、受発注部門で必要なQCD管理全てを備えた、現場特化型兼クラウド型の今世紀最高の受発注管理システムとなります。
ユーザー登録
受発注業務の効率化だけでなく、システムを導入することで、コスト削減や製品・資材のステータス可視化のほか、属人化していた受発注情報の共有化による内部不正防止や統制にも役立ちます。
NEWJI DX
製造業に特化したデジタルトランスフォーメーション(DX)の実現を目指す請負開発型のコンサルティングサービスです。AI、iPaaS、および先端の技術を駆使して、製造プロセスの効率化、業務効率化、チームワーク強化、コスト削減、品質向上を実現します。このサービスは、製造業の課題を深く理解し、それに対する最適なデジタルソリューションを提供することで、企業が持続的な成長とイノベーションを達成できるようサポートします。
製造業ニュース解説
製造業、主に購買・調達部門にお勤めの方々に向けた情報を配信しております。
新任の方やベテランの方、管理職を対象とした幅広いコンテンツをご用意しております。
お問い合わせ
コストダウンが利益に直結する術だと理解していても、なかなか前に進めることができない状況。そんな時は、newjiのコストダウン自動化機能で大きく利益貢献しよう!
(β版非公開)