- お役立ち記事
- How to Minimize the Impact of Weld Lines and Improve Product Precision
月間76,176名の
製造業ご担当者様が閲覧しています*
*2025年3月31日現在のGoogle Analyticsのデータより
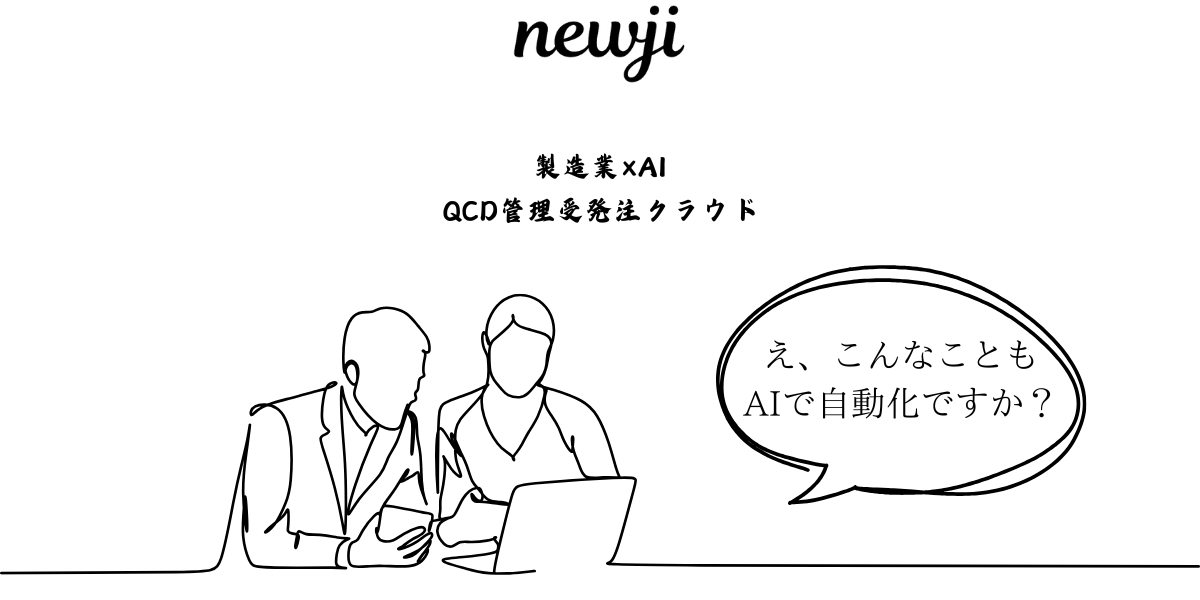
How to Minimize the Impact of Weld Lines and Improve Product Precision
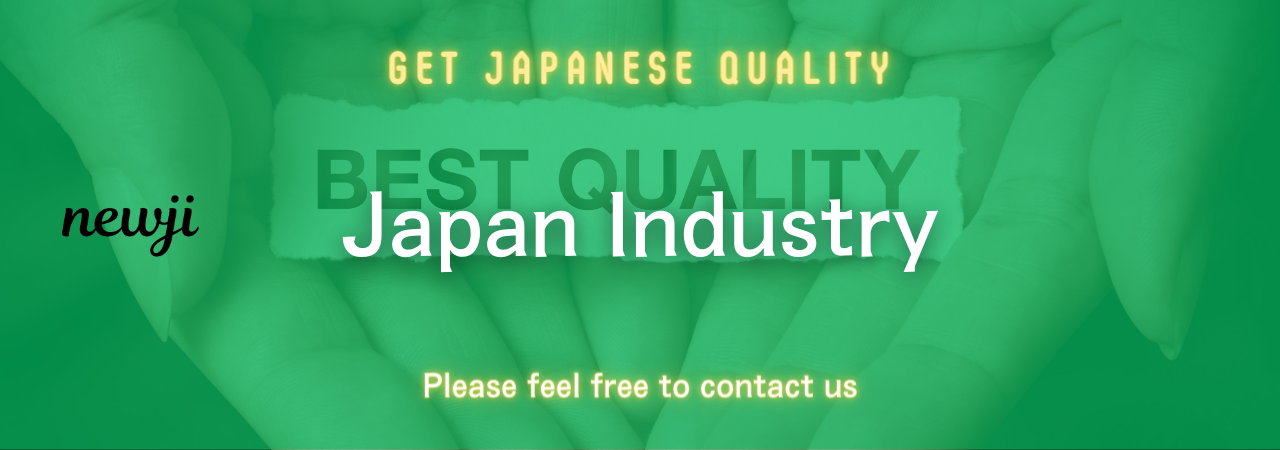
目次
Understanding Weld Lines
Weld lines, often referred to as knit lines, are a common occurrence in the manufacturing process, particularly in injection molding.
These lines form when two or more flow fronts of molten plastic meet during the filling process.
Their presence can negatively impact the structural integrity and appearance of the final product.
Weld lines can cause weak spots in the material, leading to potential breakages or failures.
Moreover, they can mar the aesthetic appeal of the product, making it less attractive to consumers.
Understanding the causes of weld lines is crucial in minimizing their impact and achieving a high level of product precision.
Factors like the design of the mold, the quality of the raw materials, and the processing conditions play significant roles in the formation of weld lines.
By addressing these factors, manufacturers can significantly reduce the presence of weld lines and improve the overall quality of their products.
Designing Molds to Reduce Weld Lines
One of the most effective ways to minimize weld lines is by optimizing the design of the mold.
Carefully considering the placement of gates and ensuring proper flow paths can help in reducing the formation of these lines.
Molds should be designed to promote even filling, thereby minimizing the chances of multiple flow fronts meeting and creating weld lines.
Consider using multiple gates strategically placed to balance the flow of material and reduce pressure differences.
This can help in achieving a more uniform material flow, thereby reducing the likelihood of weak points.
Integrating flow leaders or flow restrictors in the design can also aid in controlling the speed and direction of the molten material, helping to prevent weld lines.
Optimizing Process Conditions
Beyond mold design, optimizing the process conditions during manufacturing can have a significant impact on the occurrence of weld lines.
Controlling temperature, pressure, and injection speed are key factors in managing the flow of material and preventing the formation of weld lines.
Maintaining an optimal temperature profile is crucial to ensure that the material flows smoothly and bonds properly.
Lowering the injection speed may allow more time for the weld lines to meld, improving their integrity.
However, if the speed is too low, it can cause other defects, so finding a balance is crucial.
Adjusting the holding pressure can also lead to better packing of the material, thus enhancing the strength and appearance of the product.
Material Selection and Quality
The type and quality of the material used in the production process can greatly influence the formation of weld lines.
Using high-quality materials with good flow characteristics can reduce the incidence of these lines.
Certain materials, such as those with fillers, can exacerbate the visibility of weld lines.
Consideration should be given to the compatibility of material characteristics with the design and process conditions.
Choosing materials with better melt flow ratings can aid in achieving smoother, more uniform fills, thereby reducing weld line formation.
Additionally, selecting materials with appropriate additives or stabilizers could enhance the bonding at the weld lines, resulting in stronger finished products.
Quality Control and Inspection
Implementing strict quality control measures is essential in identifying and addressing weld lines before products reach the market.
Regular inspection and analysis of finished products can help in detecting weld lines early, allowing for corrective measures to be taken.
Using advanced inspection technologies, such as thermal imaging and X-ray systems, can provide a deeper understanding of the internal structure of the product.
This not only helps in spotting potential weak areas but also aids in identifying the root causes of weld lines.
Revising production processes based on these insights can lead to continuous improvements and higher product quality.
Collaborating with Material and Mold Experts
Engaging with experts in material science and mold design can provide valuable insights into minimizing weld lines.
These professionals can offer guidance on selecting appropriate materials and designing molds with optimal characteristics for specific products.
Leveraging their expertise can help manufacturers fine-tune their processes, ultimately leading to products with fewer defects and higher precision.
Continuous collaboration can also promote innovation in materials and processes, leading to further reductions in weld lines.
Conclusion
Minimizing the impact of weld lines is essential for improving product precision and ensuring customer satisfaction.
By focusing on mold design, optimizing process conditions, selecting the right materials, and implementing rigorous quality control measures, manufacturers can significantly reduce the occurrence of these imperfections.
Engaging with industry experts can further enhance the quality of the final product, making it stronger, more reliable, and aesthetically pleasing.
With the right strategies in place, manufacturers can achieve higher precision in their products, thereby setting themselves apart in a competitive market.
資料ダウンロード
QCD管理受発注クラウド「newji」は、受発注部門で必要なQCD管理全てを備えた、現場特化型兼クラウド型の今世紀最高の受発注管理システムとなります。
ユーザー登録
受発注業務の効率化だけでなく、システムを導入することで、コスト削減や製品・資材のステータス可視化のほか、属人化していた受発注情報の共有化による内部不正防止や統制にも役立ちます。
NEWJI DX
製造業に特化したデジタルトランスフォーメーション(DX)の実現を目指す請負開発型のコンサルティングサービスです。AI、iPaaS、および先端の技術を駆使して、製造プロセスの効率化、業務効率化、チームワーク強化、コスト削減、品質向上を実現します。このサービスは、製造業の課題を深く理解し、それに対する最適なデジタルソリューションを提供することで、企業が持続的な成長とイノベーションを達成できるようサポートします。
製造業ニュース解説
製造業、主に購買・調達部門にお勤めの方々に向けた情報を配信しております。
新任の方やベテランの方、管理職を対象とした幅広いコンテンツをご用意しております。
お問い合わせ
コストダウンが利益に直結する術だと理解していても、なかなか前に進めることができない状況。そんな時は、newjiのコストダウン自動化機能で大きく利益貢献しよう!
(β版非公開)