- お役立ち記事
- How to Optimize Cooling Time to Enhance Product Strength and Precision
How to Optimize Cooling Time to Enhance Product Strength and Precision
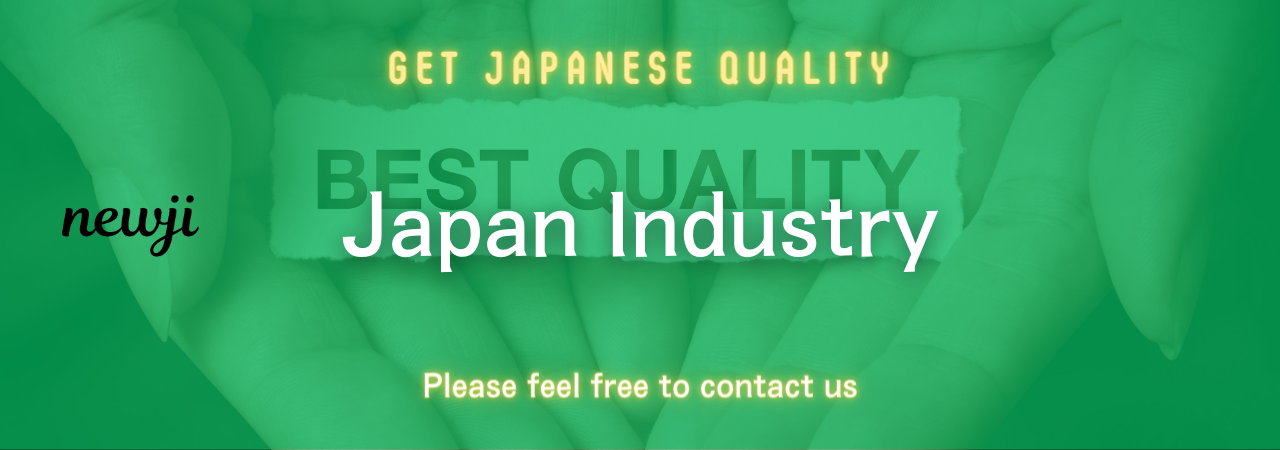
目次
Understanding the Importance of Cooling Time
When it comes to manufacturing processes, cooling time plays a critical role in determining the quality and durability of the final product.
Whether it’s molding plastic, baking ceramics, or casting metals, the period during which a product is allowed to cool can significantly impact its strength and precision.
This is because the way a material cools affects its structural integrity.
Rapid or uneven cooling can lead to internal stresses, warping, or other defects that compromise the product’s functionality.
The Science Behind Cooling
Understanding the science behind cooling is essential for optimizing this crucial phase.
When a material cools, it contracts.
The speed and uniformity of this contraction determine the material’s final properties.
For instance, in metal casting, faster cooling might lead to increased brittleness but enhanced strength, while slower cooling can result in a product with greater ductility.
Coordination of cooling is necessary to avoid deformities and ensure consistency in quality.
The right cooling process minimizes residual stress, which occurs when different parts of an object contract at different rates.
Techniques for Enhancing Cooling Efficiency
Controlled Cooling Techniques
Implementing controlled cooling techniques is a strategic approach to ensure uniform temperature reduction across the material.
Using advanced technology, manufacturers can maintain the integrity of materials while allowing for modifications in flexibility and strength based on desired product specifications.
For instance, in plastics manufacturing, air or fluid-bed cooling systems are used to facilitate uniform cooling.
Such systems are equipped with sensors and controllers that adapt the cooling process in real-time, providing precision in temperature decrease rates.
Environment Control
Manipulating the surrounding environment can also significantly impact cooling efficiency.
Environmental factors such as humidity, ambient temperature, and air circulation can affect how evenly and quickly a product cools.
In environments with fluctuating conditions, maintaining a consistent temperature in the cooling area can prevent undesirable variations in cooling rates.
Where applicable, manufacturers can enclose cooling areas to control these factors, thereby ensuring that the entire batch of products receives the same treatment.
Optimizing Material Composition
Selecting the Right Material
The composition of the material being cooled has a profound effect on the cooling process.
Some materials heat and cool more efficiently than others due to their specific heat capacity, thermal conductivity, and phase change temperatures.
For optimal results, manufacturers should choose materials based on their compatibility with the desired cooling profile.
Materials with higher thermal conductivities cool faster, which can be beneficial or detrimental depending on the nature of the product.
In cases where increased strength is required, materials that provide a balance between cooling speed and thermal expansion are preferred.
Monitoring and Adjustments
Real-time Monitoring
Incorporating real-time monitoring systems within the cooling process allows manufacturers to fine-tune the process as necessary.
By using state-of-the-art sensors and software, it is possible to track temperature changes and adjust cooling parameters on-the-fly.
This adaptability ensures that any deviations from the expected cooling curve can be corrected immediately, maintaining consistent product quality.
Feedback Loops
Feedback loops are integral to the enhancement of cooling procedures.
With data collected during the monitoring phase, manufacturers can devise strategies to improve future processes.
Pattern recognition algorithms can detect anomalies and predict outcomes based on historical data trends, allowing for proactive adaptations to the cooling process.
The Role of Equipment in Cooling Optimization
Investing in Advanced Technology
Since the efficiency of cooling largely depends on the equipment used, investing in advanced technology is crucial.
Modern cooling equipment is designed with operational efficiency and versatility in mind, capable of complex controls like variable speed fans or adjustable heat exchangers.
Manufacturers should seek equipment that offers adaptability to a wide range of materials and product designs, enabling them to switch between different cooling profiles as needed.
Regular Maintenance
Regular maintenance of cooling systems ensures they perform at maximum efficiency.
Over time, components can wear down or become clogged, reducing their effectiveness.
Consistent checks and necessary replacements can prevent unexpected breakdowns and sustain high-quality output.
Routine maintenance guarantees that the system operates under optimal conditions, directly affecting cooling performance.
Benefits of Optimizing Cooling Time
Enhanced Product Quality
Optimizing cooling time results in products with improved precision and strength.
This means fewer defects, lower rejection rates, and better overall quality.
The enhanced product integrity leads to longer-lasting products and satisfied customers.
Increased Efficiency
Efficient cooling reduces cycle times, increases throughput, and ultimately boosts production capacity.
Streamlined cooling processes can help manufacturers meet demands faster, reducing lead times without compromising on quality.
Cost Reduction
The strategic management of cooling time can significantly reduce energy costs.
Efficient cooling systems consume less power and require less maintenance, translating into cost savings.
Moreover, reducing defects and enhancing product reliability decreases material waste and potential warranty claims.
In conclusion, optimizing cooling time is a multifaceted process that requires a thorough understanding of material science, continuous monitoring, and investing in the right equipment.
By focusing on these elements, manufacturers can enhance product strength and precision, leading to successful and profitable operations.
資料ダウンロード
QCD調達購買管理クラウド「newji」は、調達購買部門で必要なQCD管理全てを備えた、現場特化型兼クラウド型の今世紀最高の購買管理システムとなります。
ユーザー登録
調達購買業務の効率化だけでなく、システムを導入することで、コスト削減や製品・資材のステータス可視化のほか、属人化していた購買情報の共有化による内部不正防止や統制にも役立ちます。
NEWJI DX
製造業に特化したデジタルトランスフォーメーション(DX)の実現を目指す請負開発型のコンサルティングサービスです。AI、iPaaS、および先端の技術を駆使して、製造プロセスの効率化、業務効率化、チームワーク強化、コスト削減、品質向上を実現します。このサービスは、製造業の課題を深く理解し、それに対する最適なデジタルソリューションを提供することで、企業が持続的な成長とイノベーションを達成できるようサポートします。
オンライン講座
製造業、主に購買・調達部門にお勤めの方々に向けた情報を配信しております。
新任の方やベテランの方、管理職を対象とした幅広いコンテンツをご用意しております。
お問い合わせ
コストダウンが利益に直結する術だと理解していても、なかなか前に進めることができない状況。そんな時は、newjiのコストダウン自動化機能で大きく利益貢献しよう!
(Β版非公開)