- お役立ち記事
- How to optimize processing of aluminum, stainless steel, and iron pipes and TIG welding
月間77,185名の
製造業ご担当者様が閲覧しています*
*2025年2月28日現在のGoogle Analyticsのデータより
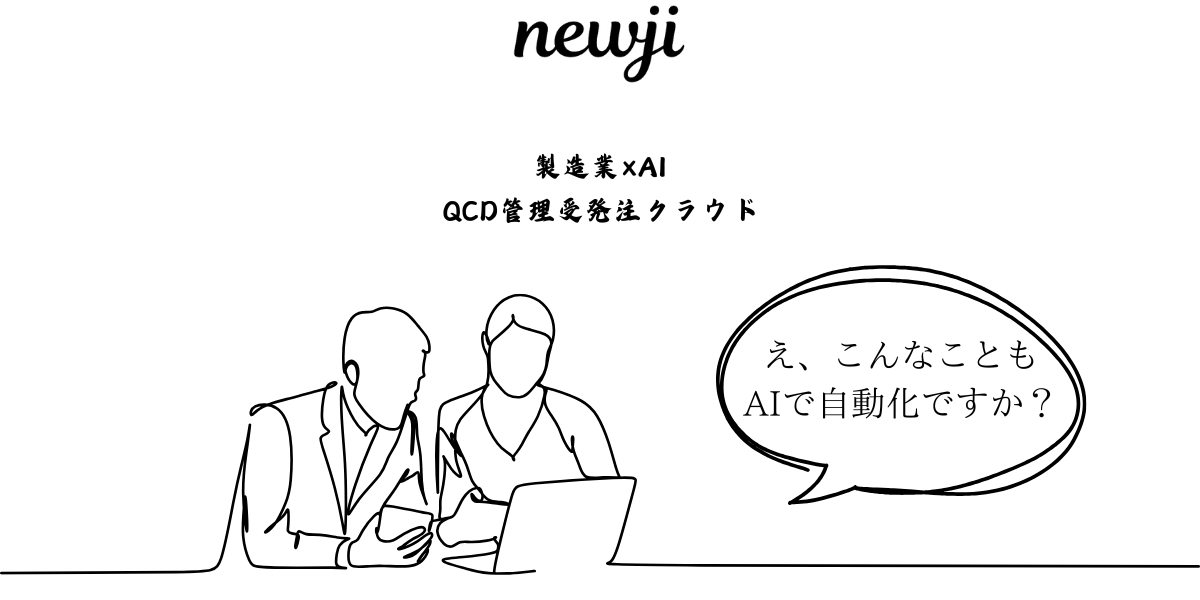
How to optimize processing of aluminum, stainless steel, and iron pipes and TIG welding
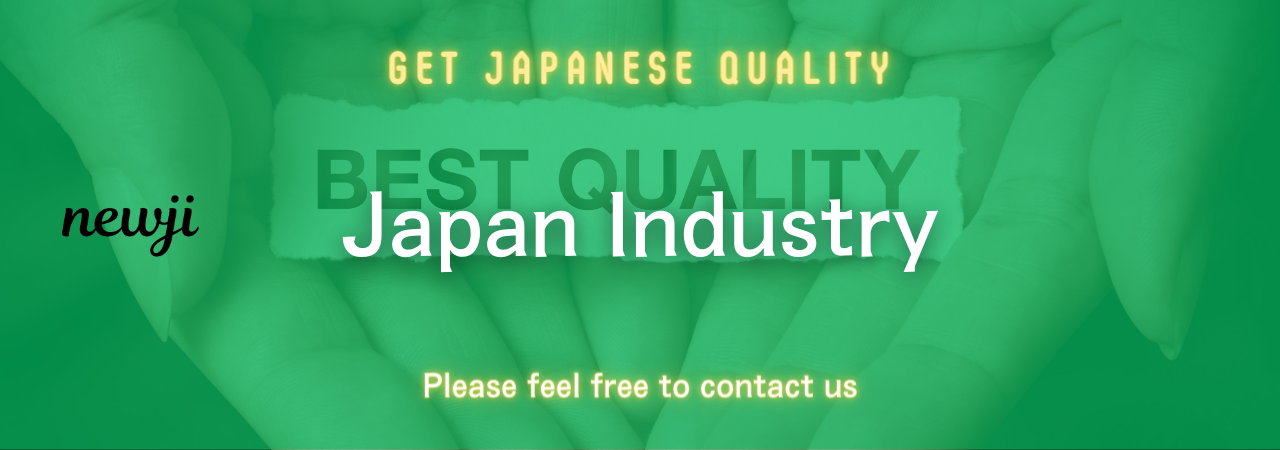
目次
Understanding the Basics of Pipe Processing
Processing aluminum, stainless steel, and iron pipes is crucial for numerous industries, from construction to automotive manufacturing.
Each material has its unique characteristics, demanding tailored approaches for optimal efficiency.
By understanding the basics of pipe processing, businesses can enhance their productivity and achieve better results in their operations.
Properties of Aluminum Pipes
Aluminum is known for its lightweight nature and excellent corrosion resistance, making it a popular choice for various applications.
However, its relatively low melting point requires careful handling during processing.
To optimize aluminum pipe processing, attention should be paid to the cutting speed and tool selection.
Using sharp blades and high-speed cutting tools can improve the efficiency of aluminum pipe processing.
Moreover, lubrication plays a crucial role in reducing friction and extending tool life, ensuring smoother cuts and finishes.
Processing Stainless Steel Pipes
Stainless steel pipes are renowned for their durability and resistance to rust, making them ideal for environments prone to moisture.
Processing stainless steel, however, can be challenging due to its hardness.
For optimal results, fabricators must choose tools specifically designed for stainless steel.
Employing carbide-tipped tools can help in achieving clean cuts without compromising the structural integrity of the stainless steel pipes.
In addition, using coolants during the machining process is essential to prevent excessive heat that can lead to deformation or surface damage.
Iron Pipe Fabrication Techniques
Iron pipes are characterized by their robustness and are often used in heavy-duty applications.
Its processing demands consideration of aspects such as the pipe’s thickness and the intended function.
While iron is relatively easier to machine compared to stainless steel, selecting the right tools is crucial to maintain the quality of the pipe.
Cutting iron pipes with high-speed steel blades or carbide tools can enhance the precision and efficiency of the process.
Proper clamping is also essential when cutting or shaping iron pipes to prevent vibrations that can result in inaccuracies.
Mastering the TIG Welding Process
TIG welding, or Tungsten Inert Gas welding, is a vital process used to join aluminum, stainless steel, and iron pipes.
It offers high precision and produces clean, high-quality welds suitable for various industries.
Understanding the nuances of TIG welding enhances the outcome of the welding process.
Choosing the Right Electrode
The choice of electrode is paramount in TIG welding as it influences the weld quality and stability.
Pure tungsten electrodes are typically used for welding aluminum due to their excellent arc stability.
Meanwhile, thoriated or ceriated tungsten electrodes are preferred for stainless steel and iron because they offer improved arc performance and longevity.
Managing Welding Parameters
Effective management of welding parameters such as current, voltage, and travel speed is crucial in achieving optimal TIG welding results.
For aluminum welding, it is important to use alternating current (AC) mode to break the aluminum oxide layer and ensure proper weld penetration.
On the other hand, stainless steel and iron pipes usually require direct current (DC) mode to achieve deeper penetration and cleaner welds.
Moreover, adjusting the travel speed according to the thickness of the material being welded can help avoid defects such as excessive spatter or burn-through.
Importance of Shielding Gas
Shielding gas plays a significant role in TIG welding by protecting the weld pool from atmospheric contamination.
Argon is the most commonly used shielding gas for welding aluminum, stainless steel, and iron, owing to its inert nature.
However, argon-helium mixtures can be considered for thicker materials to enhance heat input, especially when working with aluminum.
Ensuring a consistent flow of shielding gas helps in maintaining the weld integrity and appearance, preventing porosity and oxidation.
Enhancing Pipe Processing Through Technology
Advancements in technology have led to significant improvements in the processing of aluminum, stainless steel, and iron pipes.
For instance, automation and CNC (Computer Numerical Control) machines enable precise, repeatable cuts and welds, reducing human error and production time.
Laser Cutting and Automation
Laser cutting technology offers unparalleled precision and speed, making it an ideal choice for pipe processing.
Whether working with aluminum, stainless steel, or iron, laser cutting ensures minimal material wastage and high accuracy.
Coupled with automation, laser cutting systems can dramatically increase production efficiency and consistency.
CNC Machining for Precision Work
CNC machining has revolutionized the manufacturing industry by allowing for complex and precise operations on aluminum, stainless steel, and iron pipes.
The programmability of CNC machines permits highly accurate cuts, reducing the need for manual intervention and minimizing errors.
Incorporating CNC technology into pipe processing operations not only improves the quality of the output but also enhances the scalability of production.
Conclusion
Optimizing the processing of aluminum, stainless steel, and iron pipes requires a comprehensive understanding of each material’s properties and the application of precise techniques.
Whether through leveraging advanced technologies or mastering the nuances of TIG welding, careful consideration of these processes can lead to superior results.
By implementing best practices and constantly upgrading skills and equipment, industries can significantly boost productivity and achieve high-quality outputs in pipe processing operations.
資料ダウンロード
QCD管理受発注クラウド「newji」は、受発注部門で必要なQCD管理全てを備えた、現場特化型兼クラウド型の今世紀最高の受発注管理システムとなります。
ユーザー登録
受発注業務の効率化だけでなく、システムを導入することで、コスト削減や製品・資材のステータス可視化のほか、属人化していた受発注情報の共有化による内部不正防止や統制にも役立ちます。
NEWJI DX
製造業に特化したデジタルトランスフォーメーション(DX)の実現を目指す請負開発型のコンサルティングサービスです。AI、iPaaS、および先端の技術を駆使して、製造プロセスの効率化、業務効率化、チームワーク強化、コスト削減、品質向上を実現します。このサービスは、製造業の課題を深く理解し、それに対する最適なデジタルソリューションを提供することで、企業が持続的な成長とイノベーションを達成できるようサポートします。
製造業ニュース解説
製造業、主に購買・調達部門にお勤めの方々に向けた情報を配信しております。
新任の方やベテランの方、管理職を対象とした幅広いコンテンツをご用意しております。
お問い合わせ
コストダウンが利益に直結する術だと理解していても、なかなか前に進めることができない状況。そんな時は、newjiのコストダウン自動化機能で大きく利益貢献しよう!
(β版非公開)