- お役立ち記事
- How to optimize procurement of manufacturing and inspection equipment for electronic components and EMS industries
月間77,185名の
製造業ご担当者様が閲覧しています*
*2025年2月28日現在のGoogle Analyticsのデータより
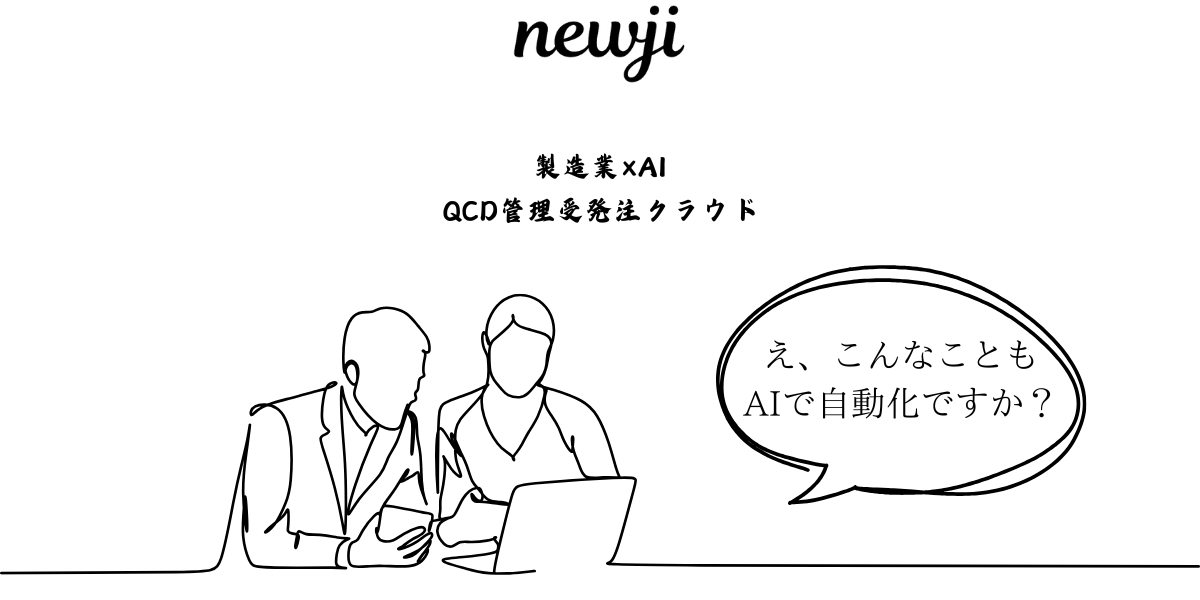
How to optimize procurement of manufacturing and inspection equipment for electronic components and EMS industries
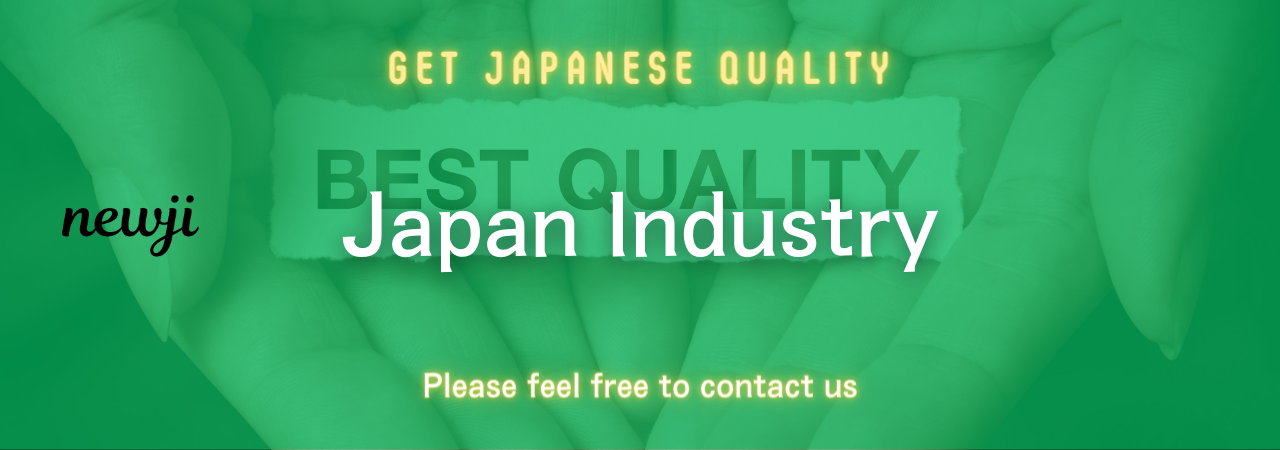
目次
Understanding the Importance of Efficient Procurement
Efficient procurement of manufacturing and inspection equipment is crucial for the electronic components and EMS (Electronics Manufacturing Services) industries.
The industry’s continuous growth depends on sourcing the right equipment, which enhances production capabilities, minimizes costs, and ensures high-quality outputs.
Proper procurement practices are integral to maintaining a competitive edge and meeting the evolving demands of technology.
Identifying Procurement Needs
The first step toward optimizing procurement is understanding the specific needs of your production and inspection processes.
Begin by assessing the technologies, components, and tools required for your production lines.
Identify equipment that can maximize efficiency and adapt to future business growth or technological advancements.
It’s essential to involve key stakeholders from various departments such as engineering, production, and quality control to ensure all requirements are considered.
Analyzing Current Equipment
Review the performance and limitations of your existing equipment by conducting a comprehensive audit.
This involves examining the productivity, reliability, and energy efficiency of the current systems.
By identifying any bottlenecks, outdated technologies, or equipment failures, you can prioritize which areas need immediate attention.
Researching Potential Suppliers
A crucial aspect of procurement is sourcing reliable and innovative suppliers.
Start by compiling a list of potential suppliers renowned for their quality products and services within the industry.
Reviewing their history, client testimonials, and market reputation can provide insights into their reliability and capability to meet your needs.
Supplier Evaluation Criteria
When evaluating suppliers, consider their technical expertise, product offerings, and capabilities in terms of customization and support.
Pricing, delivery timelines, and after-sales services are other critical factors to evaluate to avoid disruptions in your production process.
Additionally, potential suppliers with research and development capabilities can offer advanced products, keeping your manufacturing processes future-proof.
Negotiating and Securing Contracts
Successful procurement hinges on effective negotiation.
Begin negotiations by discussing pricing, payment terms, and any potential discounts for long-term relationships or bulk purchases.
Consider contracts that offer flexibility and can be adapted as your business grows.
By ensuring agreement clarity on equipment warranties, maintenance support, and intellectual property rights, you protect your investment and reduce risks.
Streetwise Contract Management
Develop a strategic contract management approach that tracks supplier performance, compliance with terms, and timely renewals or terminations.
Implementing a centralized system for contract management can streamline communication, improve service delivery, and address issues proactively.
Implementing Procurement Technology
Adopting procurement technologies can greatly enhance efficiency and transparency.
Modern solutions such as e-procurement platforms facilitate easy collaboration between suppliers and stakeholders, enable faster decision-making, and offer valuable data analysis for strategic procurement.
Artificial Intelligence and Automation
Artificial intelligence and automation in procurement processes can predict demand trends, manage inventory more effectively, and optimize supplier schedules.
These technological advancements offer precision and insights that manual processes might lack, significantly improving procurement outcomes.
Ensuring Quality and Compliance
For any equipment procured, from manufacturing units to inspection systems, ensuring compliance with industry standards and regulations is vital.
This guarantees that your products meet quality benchmarks and safety requirements, minimizing legal risks and enhancing brand reputation.
Vendor Audits and Quality Checks
Regular vendor audits and quality checks are essential to maintain high standards.
These assessments review the vendor’s production processes, control measures, and adherence to your specifications.
Prioritize vendors with robust quality management systems and mitigation plans for potential issues.
Investing in Staff Training
Procurement involves not only sourcing the latest equipment but ensuring that your staff understands and can efficiently operate and maintain these technologies.
Investing in comprehensive training programs facilitates smoother transitions, reduces human error, and enhances operation longevity.
Continuous Improvement Programs
Implement ongoing improvement programs that encourage staff to suggest enhancements based on hands-on experiences.
Such initiatives can unearth valuable ground-level insights for procurement strategies and overall operational efficiency.
Conclusion
To optimize procurement in the electronic components and EMS industries, businesses must adopt a strategic and comprehensive approach.
From understanding specific requirements and researching suppliers to implementing cutting-edge technologies and ensuring compliance, each step plays a pivotal role in driving success.
By continuously reviewing, improving, and adapting procurement practices, organizations can ensure sustained growth and a competitive advantage in the dynamic landscape of electronics manufacturing.
資料ダウンロード
QCD管理受発注クラウド「newji」は、受発注部門で必要なQCD管理全てを備えた、現場特化型兼クラウド型の今世紀最高の受発注管理システムとなります。
ユーザー登録
受発注業務の効率化だけでなく、システムを導入することで、コスト削減や製品・資材のステータス可視化のほか、属人化していた受発注情報の共有化による内部不正防止や統制にも役立ちます。
NEWJI DX
製造業に特化したデジタルトランスフォーメーション(DX)の実現を目指す請負開発型のコンサルティングサービスです。AI、iPaaS、および先端の技術を駆使して、製造プロセスの効率化、業務効率化、チームワーク強化、コスト削減、品質向上を実現します。このサービスは、製造業の課題を深く理解し、それに対する最適なデジタルソリューションを提供することで、企業が持続的な成長とイノベーションを達成できるようサポートします。
製造業ニュース解説
製造業、主に購買・調達部門にお勤めの方々に向けた情報を配信しております。
新任の方やベテランの方、管理職を対象とした幅広いコンテンツをご用意しております。
お問い合わせ
コストダウンが利益に直結する術だと理解していても、なかなか前に進めることができない状況。そんな時は、newjiのコストダウン自動化機能で大きく利益貢献しよう!
(β版非公開)