- お役立ち記事
- How to Optimize Shot Size to Improve Molding Cycle Efficiency
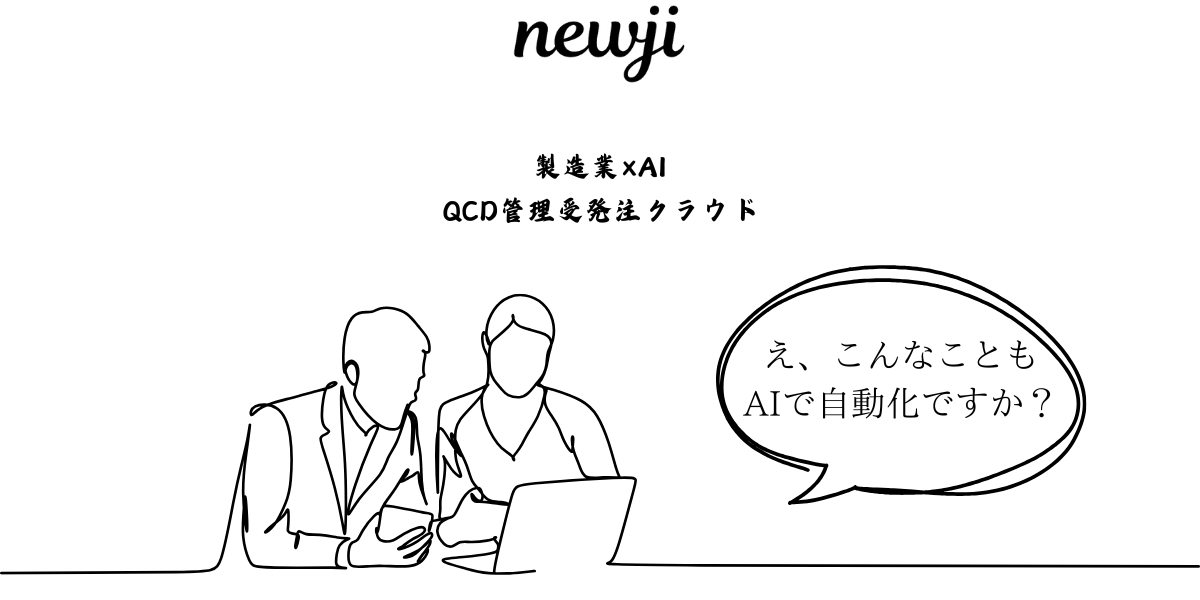
How to Optimize Shot Size to Improve Molding Cycle Efficiency
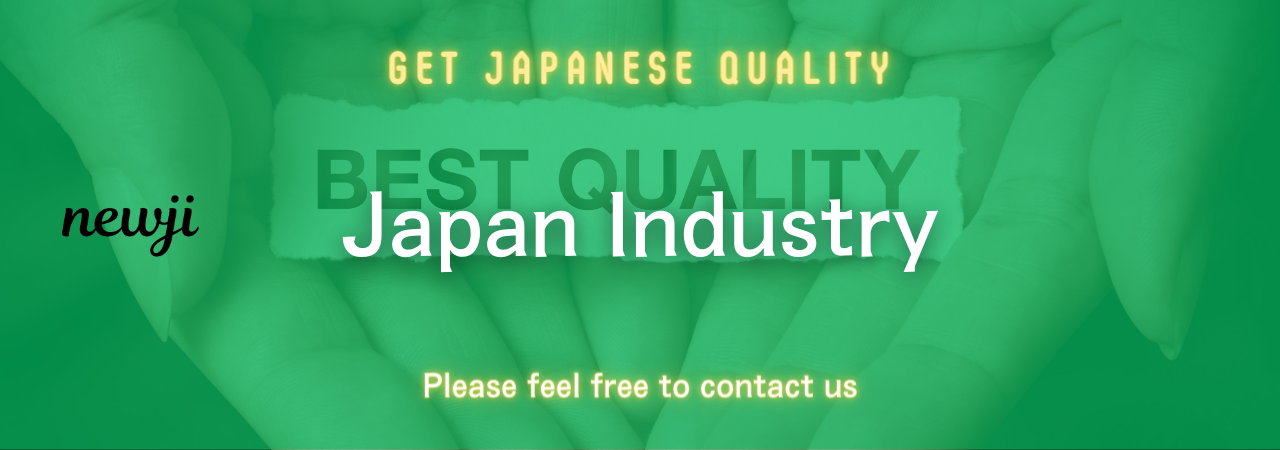
目次
Understanding Shot Size in Injection Molding
Injection molding is a widely used manufacturing process for producing plastic parts in high volume.
In this process, the term ‘shot size’ refers to the amount of molten plastic injected into the mold during each cycle.
The size of this ‘shot’ is crucial because it determines the overall efficiency, quality, and cost-effectiveness of the production cycle.
A well-optimized shot size ensures that the mold cavity is filled completely, avoiding any defects or wastage.
Therefore, understanding how to measure and optimize shot size is fundamental in improving the molding cycle efficiency.
Factors Affecting Shot Size
Several factors can influence the shot size, affecting the quality of the final product.
These include the type of plastic material being used, the temperature and pressure of the injection, and the design of the mold itself.
– **Material Type**: Different plastics have different flow characteristics.
Thermosetting plastics require specific temperatures and pressures compared to thermoplastics, which may change the shot size calculation.
– **Mold Design**: The complexity and intricacy of a mold design can affect the flow of molten plastic.
Features like thin walls or intricate shapes may require adjustments in shot size to ensure consistent quality.
– **Machine Capabilities**: The injection molding machine itself has limitations in terms of pressure, temperature, and volumetric capabilities.
Being aware of these limitations is key to determining the optimal shot size.
– **Temperature and Pressure**: Proper control of temperature and pressure during the injection process is vital to achieving the desired shot size.
Variance in these parameters can lead to incomplete filling or defective products.
Steps to Optimize Shot Size
Optimizing shot size requires a careful analysis of various components and a methodical approach.
Here are the steps that can guide you in optimizing shot size effectively:
1. Assess Material and Machine Specifications
Start by evaluating the specifications of the plastic material you are using and the capabilities of your injection molding machine.
Ascertain the material’s melt flow index, viscosity, and cooling time, coupled with your machine’s injection pressure, volume capacity, and temperature control.
Understanding these parameters helps in setting initial boundaries for shot size optimization.
2. Analyze the Mold Design
Review your mold design to identify possible bottlenecks that could affect the shot size.
Look for areas that might cause flow hesitation or air entrapment.
Redesigning problem areas or optimizing gate locations can help distribute the molten plastic more evenly.
This contributes to refining the shot size for efficiency.
3. Experiment and Adjust Parameters
Conduct test runs by varying parameters such as temperature, pressure, and injection speed.
Document the outcomes to understand how these changes affect the shot size and the quality of the product.
Incremental adjustments are key, as drastic changes might lead to defects or material wastage.
4. Utilize Simulation Tools
Employ simulation software to predict how changes in shot size will affect the molding process.
Simulation tools can provide invaluable insight by modeling the flow of the material within the mold.
These tools help in visualizing potential defects or inefficiencies, allowing you to preemptively make necessary adjustments.
5. Implement Statistical Process Control (SPC)
Use Statistical Process Control to continuously monitor and record data related to the injection molding process.
SPC tools help in identifying trends or patterns that may affect shot size consistency.
This brings a systematic approach to optimizing shot size by allowing data-driven decisions.
The Benefits of Shot Size Optimization
Optimizing the shot size can lead to numerous benefits that elevate the overall efficiency of the injection molding process.
With the shot size properly balanced, manufacturers can expect improvements in product quality, cycle times, and material usage.
Enhancing Product Quality
A precise shot size reduces the likelihood of defects such as voids, weld lines, or sink marks.
This precision leads to an increase in the quality of the final product, ensuring it meets both functional and aesthetic standards.
Reducing Cycle Times
By determining the optimal shot size, cycle times can be significantly reduced.
This reduction is achieved by minimizing material wastage and avoiding excessive cooling times or rework.
A faster cycle time increases the production efficiency and allows for higher throughput.
Lowering Material Costs
Optimizing shot size helps in achieving ideal material utilization.
This minimizes wastage and reduces the amount of excess scrap produced during the molding process.
Consequently, the cost associated with raw materials is also minimized, leading to a more cost-effective production line.
Challenges in Shot Size Optimization
While there are clear benefits, optimizing shot size also presents challenges that manufacturers need to overcome.
Complexity of Design
Highly complex or intricate mold designs can make shot size optimization challenging.
Balance is needed between filling the mold completely and avoiding over-packing, which requires meticulous planning and testing.
Variability in Material Properties
Variations in material batches or changes in environmental conditions may affect material properties like viscosity.
These differences necessitate constant monitoring and adjustments to maintain optimal shot size.
Machine Limitations
The physical limitations of the injection molding machines, such as maximum pressure or capacity limits, can also constrain shot size optimization.
Being aware of these limitations and adapting conditions accordingly is crucial.
Conclusion
Optimizing shot size is a fundamental step in enhancing the efficiency of the injection molding process.
Through careful analysis of material, mold design, and machine capabilities, manufacturers can significantly improve product quality, cycle times, and reduce costs.
Adopting a strategic approach, complemented with simulation tools and SPC methodologies can address the challenges in shot size optimization.
This leads to a more efficient, cost-effective, and quality-centric production process, critical for maintaining competitiveness in high-volume manufacturing environments.
資料ダウンロード
QCD調達購買管理クラウド「newji」は、調達購買部門で必要なQCD管理全てを備えた、現場特化型兼クラウド型の今世紀最高の購買管理システムとなります。
ユーザー登録
調達購買業務の効率化だけでなく、システムを導入することで、コスト削減や製品・資材のステータス可視化のほか、属人化していた購買情報の共有化による内部不正防止や統制にも役立ちます。
NEWJI DX
製造業に特化したデジタルトランスフォーメーション(DX)の実現を目指す請負開発型のコンサルティングサービスです。AI、iPaaS、および先端の技術を駆使して、製造プロセスの効率化、業務効率化、チームワーク強化、コスト削減、品質向上を実現します。このサービスは、製造業の課題を深く理解し、それに対する最適なデジタルソリューションを提供することで、企業が持続的な成長とイノベーションを達成できるようサポートします。
オンライン講座
製造業、主に購買・調達部門にお勤めの方々に向けた情報を配信しております。
新任の方やベテランの方、管理職を対象とした幅広いコンテンツをご用意しております。
お問い合わせ
コストダウンが利益に直結する術だと理解していても、なかなか前に進めることができない状況。そんな時は、newjiのコストダウン自動化機能で大きく利益貢献しよう!
(Β版非公開)