- お役立ち記事
- How to organize and utilize defect information to help prevent problems in design, development, and manufacturing
How to organize and utilize defect information to help prevent problems in design, development, and manufacturing
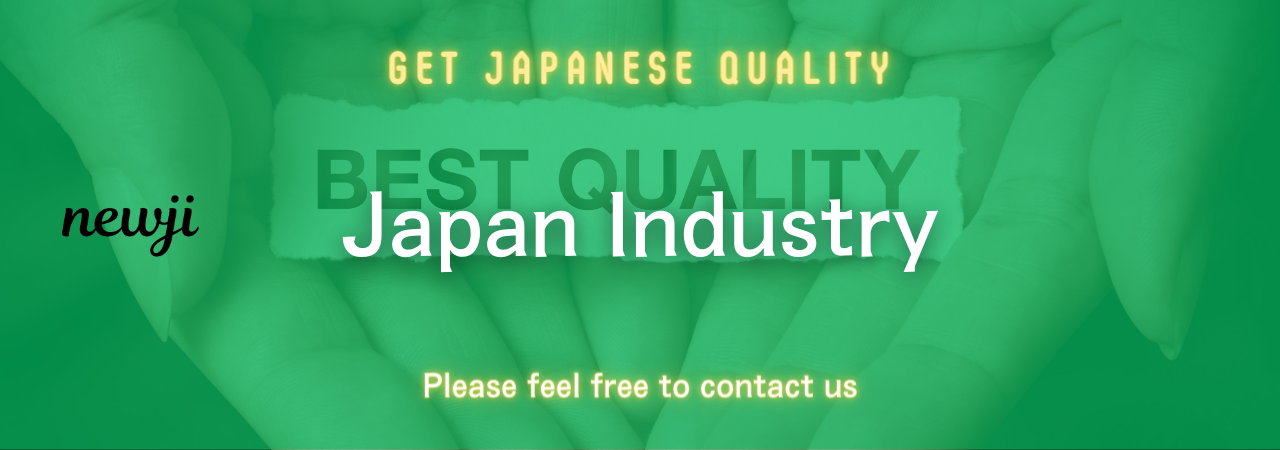
目次
Understanding Defect Information
Defect information is crucial in ensuring the quality and reliability of products across various industries.
When we talk about defects, we’re referring to any deviations from expected standards or specifications.
These defects can occur at any stage of the product development cycle, including design, development, and manufacturing.
Collecting and analyzing defect information is essential for identifying areas of improvement.
This data helps teams to prevent future problems and perform more efficiently.
By understanding the sources and causes of defects, organizations can implement strategies to reduce or eliminate them.
The Importance of Organizing Defect Information
A well-organized defect information system is key to improving product quality.
Organizing this data correctly helps teams to access and analyze it efficiently.
Clear organization structures help in tracking, managing, and resolving defects systematically.
It also enables teams to identify patterns and trends that might lead to recurring issues.
Without proper organization, defect information can become overwhelming.
It may lead to lost time, resources, and potentially more defects if data is mishandled.
Therefore, using a structured approach to organizing defect information is crucial.
Steps to Organizing Defect Information
1. Centralize Data Collection
Centralizing data collection is essential to prevent isolated information silos.
Implement a unified system where defect data from all stages of product lifecycle is collected and stored in one location.
This enables a comprehensive view of defects across the entire process.
Utilize defect tracking software that supports centralized data storage, facilitating easy access and analysis.
2. Categorization and Prioritization
Defects should be categorized based on severity, type, and source.
Prioritize defects that have a high impact on product quality or customer satisfaction.
This prioritization allows teams to focus on resolving the most critical issues first.
Categories could include design defects, development errors, and manufacturing flaws, among others.
3. Consistent Documentation Standards
Implement consistent documentation standards to ensure defect information is clear and detailed.
This includes defining how defects are reported, the information required, and the format for documentation.
Clear documentation aids in better understanding and quicker resolution of defects.
4. Regular Reviews and Updates
Defect information should be regularly reviewed and updated to ensure accuracy and relevance.
Scheduled reviews help teams to assess the success of remediation efforts and adjust strategies accordingly.
It also provides opportunities to update processes and systems based on the latest defect trends.
Utilizing Defect Information to Prevent Future Problems
1. Root Cause Analysis
Root cause analysis is a tool used to drill down to the underlying reasons for defects.
By identifying the root causes, teams can implement corrective measures that address the issue at its source.
There are several methods for conducting root cause analysis, including the 5 Whys technique and Fishbone diagrams.
2. Implement Preventive Measures
Once root causes are identified, implement preventive measures to eliminate the potential for recurring defects.
This could involve changes in design specifications, development processes, or manufacturing procedures.
Ensure that these measures are integrated into standard operating procedures to reinforce quality control.
3. Continuous Improvement Programs
Establish continuous improvement programs that focus on regular assessment and enhancement of processes.
These programs encourage proactive rather than reactive approaches to defect management.
By fostering a culture of continuous improvement, organizations can remain agile and responsive to potential issues.
4. Training and Awareness
Provide training and awareness programs for employees to understand the importance of defect prevention.
Educate teams on best practices for defect identification, reporting, and resolution.
Increased awareness and knowledge across teams leads to collective efforts in maintaining high-quality standards.
The Role of Technology in Defect Information Management
Technology plays a significant role in effectively managing and utilizing defect information.
Implementing sophisticated defect management tools enhances data collection, analysis, and reporting.
1. Automated Tracking Systems
Automated tracking systems provide real-time monitoring of defect occurrences and resolutions.
These systems reduce the risk of human errors associated with manual tracking and ensure consistency.
Automation allows for faster response and adjustments when defects are detected.
2. Data Analytics Tools
Leverage data analytics tools to uncover patterns and insights from defect data.
Advanced analytics can predict potential future defects and recommend actions to mitigate risks.
Data-driven decisions promote efficiency and product quality improvements.
3. Collaboration Platforms
Use collaboration platforms to streamline communication and information sharing between teams.
These platforms allow for immediate updates and feedback, improving the coordination in solving defects.
Enhanced collaboration ensures that all stakeholders are aligned towards common quality goals.
Conclusion
Properly organizing and utilizing defect information is crucial in preventing future problems in design, development, and manufacturing.
By centralizing data, implementing preventive measures, and leveraging technology, organizations can achieve lower defect rates and improve product quality.
Consistent effort in defect management leads to better customer satisfaction and business success.
資料ダウンロード
QCD調達購買管理クラウド「newji」は、調達購買部門で必要なQCD管理全てを備えた、現場特化型兼クラウド型の今世紀最高の購買管理システムとなります。
ユーザー登録
調達購買業務の効率化だけでなく、システムを導入することで、コスト削減や製品・資材のステータス可視化のほか、属人化していた購買情報の共有化による内部不正防止や統制にも役立ちます。
NEWJI DX
製造業に特化したデジタルトランスフォーメーション(DX)の実現を目指す請負開発型のコンサルティングサービスです。AI、iPaaS、および先端の技術を駆使して、製造プロセスの効率化、業務効率化、チームワーク強化、コスト削減、品質向上を実現します。このサービスは、製造業の課題を深く理解し、それに対する最適なデジタルソリューションを提供することで、企業が持続的な成長とイノベーションを達成できるようサポートします。
オンライン講座
製造業、主に購買・調達部門にお勤めの方々に向けた情報を配信しております。
新任の方やベテランの方、管理職を対象とした幅広いコンテンツをご用意しております。
お問い合わせ
コストダウンが利益に直結する術だと理解していても、なかなか前に進めることができない状況。そんな時は、newjiのコストダウン自動化機能で大きく利益貢献しよう!
(Β版非公開)