- お役立ち記事
- How to practice product lifecycle management in prototyping
月間76,176名の
製造業ご担当者様が閲覧しています*
*2025年3月31日現在のGoogle Analyticsのデータより
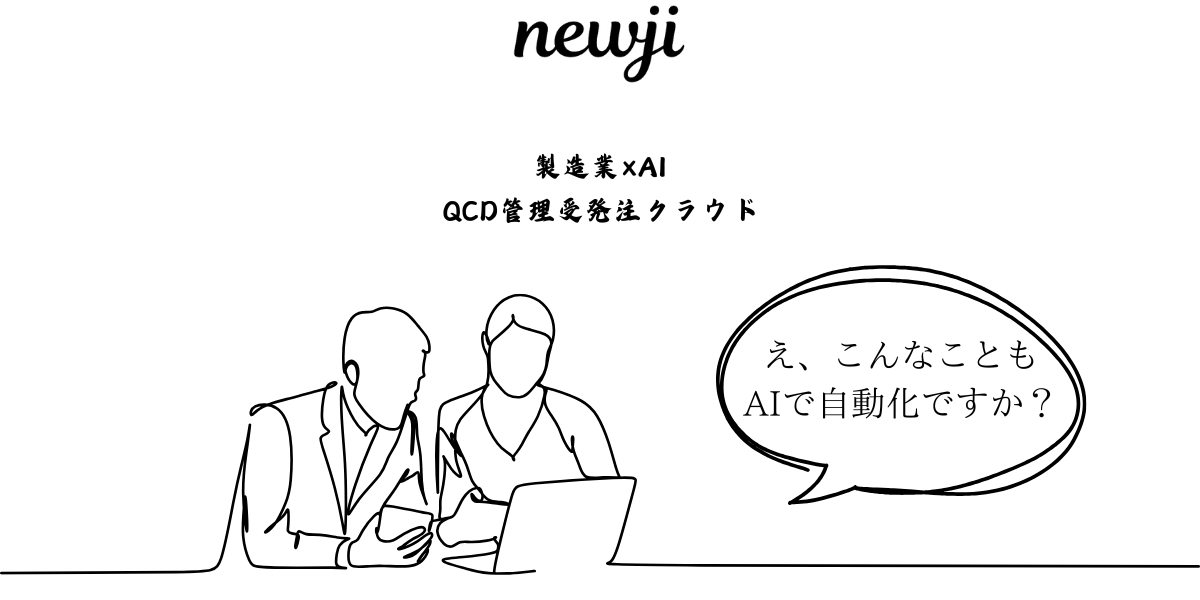
How to practice product lifecycle management in prototyping
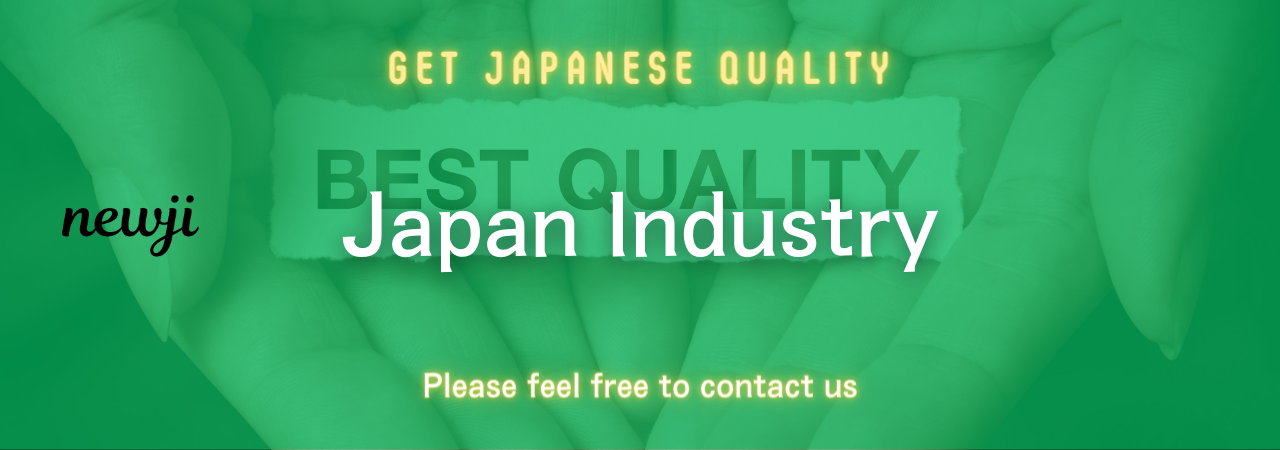
目次
Understanding Product Lifecycle Management
Product Lifecycle Management (PLM) is an essential concept that refers to the process of managing the entire lifecycle of a product from inception, through engineering design and manufacturing, to service and disposal.
The primary aim of effective PLM is to streamline production processes, enhance product quality, increase profitability, and ensure sustainability.
PLM involves a series of stages including market introduction, growth, maturity, and decline.
For businesses striving for efficiency and innovation, embracing PLM is vital, especially during the prototyping phase.
The Importance of Prototyping in PLM
Prototyping, a crucial step within the product development process, involves creating an early model of a product to test and evaluate its design, functionality, and user experience.
Prototyping plays a significant role in PLM as it provides valuable insights and feedback before a product enters full-scale production.
With effective prototyping, businesses can minimize risks and costs associated with product development, ensuring that any necessary changes are implemented before mass production begins.
Steps to Implement PLM in Prototyping
To effectively integrate PLM into the prototyping phase, several steps need to be meticulously followed.
These steps ensure that products are developed efficiently and align with customer needs and market trends.
1. Planning and Conceptualization
The first step in practicing PLM during prototyping is planning and conceptualization.
This involves identifying consumer needs, setting targets for product functionality, and outlining design requirements.
Businesses need to conduct market research to understand their audience, competitors, and potential gaps in the market.
Creating a clear and concise product concept is foundational, guiding subsequent phases of prototyping and development.
2. Designing the Prototype
Once the product concept is established, the next stage is designing the prototype.
This involves creating detailed designs using digital tools like CAD (Computer-Aided Design) software to visualize the product.
It is essential to focus on designing a prototype that is both functional and aligned with the established requirements and specifications.
Iterative design processes allow for refinement and modifications, ensuring the prototype meets all necessary criteria before proceeding to physical construction.
3. Developing the Prototype
With the design finalized, the actual creation of the prototype takes place.
During this stage, the physical model of the product is built using various materials and technologies depending on the product type.
It’s crucial to use realistic materials to accurately assess the prototype’s performance and usability.
Businesses must ensure that the prototype aligns closely with the planned design and properly represents how the final product should function.
4. Testing and Evaluation
Testing and evaluating the prototype are pivotal components of PLM, providing actionable insights into the product’s feasibility.
Different tests are conducted to assess usability, durability, safety, and regulatory compliance.
Feedback gathered from these tests informs necessary adjustments, helping refine the prototype and address any flaws or inefficiencies.
Continuous evaluation during this stage is key to verifying that the product meets desired standards and user expectations.
5. Refinement and Iteration
Refinement involves making necessary adjustments based on the testing and evaluation outcomes.
This stage might require multiple iterations, modifying the prototype until it aligns precisely with the desired functionality and quality.
Consistency in refinement ensures that the final product not only fulfills customer requirements but also adheres to the company’s standards and objectives.
Each iteration provides an opportunity to address unforeseen challenges, optimizing the prototype for better performance and user satisfaction.
6. Final Review and Approval
After numerous iterations and improvements, the prototype undergoes a final review and approval process.
This step ensures that the prototype successfully meets all design, functional, and market expectations.
Stakeholders, including designers, engineers, and product managers, examine the prototype, making sure it is ready for mass production.
Receiving final approval signifies the transition from prototyping to the actual production phase, where the product is manufactured on a larger scale and introduced to the market.
Benefits of PLM in Prototyping
Implementing PLM in the prototyping phase brings numerous advantages to product development.
Improved Product Quality
By systematically managing every aspect of the product lifecycle, businesses can ensure higher quality outcomes.
Efficient prototyping under PLM allows for identifying and resolving potential issues early in the development process, leading to a superior final product.
Cost Reduction
Effective PLM minimizes unnecessary expenditures by detecting flaws and inefficiencies during the prototyping stage rather than during full-scale production.
Reducing errors and implementing cost-effective solutions lead to significant savings.
Enhanced Collaboration
PLM fosters enhanced collaboration among multidisciplinary teams, ensuring seamless communication and coordination throughout the prototyping phase.
This collaborative environment promotes innovation and expedites problem-solving, significantly improving the development process.
Accelerated Time-to-Market
Streamlined processes and efficient feedback loops inherent in PLM lead to accelerated time-to-market for new products.
Quick adaptation and implementation of changes ensure that products are developed in line with trends and consumer demand, giving businesses a competitive edge.
Conclusion
Practicing PLM in prototyping is an invaluable strategy for businesses aiming to excel in product development.
The structured approach ensures that products are not only innovative and high-quality but are also aligned with market demands and consumer expectations.
By embracing PLM in the prototyping phase, companies can achieve sustainable and profitable growth in the competitive market landscape.
資料ダウンロード
QCD管理受発注クラウド「newji」は、受発注部門で必要なQCD管理全てを備えた、現場特化型兼クラウド型の今世紀最高の受発注管理システムとなります。
ユーザー登録
受発注業務の効率化だけでなく、システムを導入することで、コスト削減や製品・資材のステータス可視化のほか、属人化していた受発注情報の共有化による内部不正防止や統制にも役立ちます。
NEWJI DX
製造業に特化したデジタルトランスフォーメーション(DX)の実現を目指す請負開発型のコンサルティングサービスです。AI、iPaaS、および先端の技術を駆使して、製造プロセスの効率化、業務効率化、チームワーク強化、コスト削減、品質向上を実現します。このサービスは、製造業の課題を深く理解し、それに対する最適なデジタルソリューションを提供することで、企業が持続的な成長とイノベーションを達成できるようサポートします。
製造業ニュース解説
製造業、主に購買・調達部門にお勤めの方々に向けた情報を配信しております。
新任の方やベテランの方、管理職を対象とした幅広いコンテンツをご用意しております。
お問い合わせ
コストダウンが利益に直結する術だと理解していても、なかなか前に進めることができない状況。そんな時は、newjiのコストダウン自動化機能で大きく利益貢献しよう!
(β版非公開)