- お役立ち記事
- How to predict aging and lifespan of equipment and structures and utilize them for accident prevention measures
月間76,176名の
製造業ご担当者様が閲覧しています*
*2025年3月31日現在のGoogle Analyticsのデータより
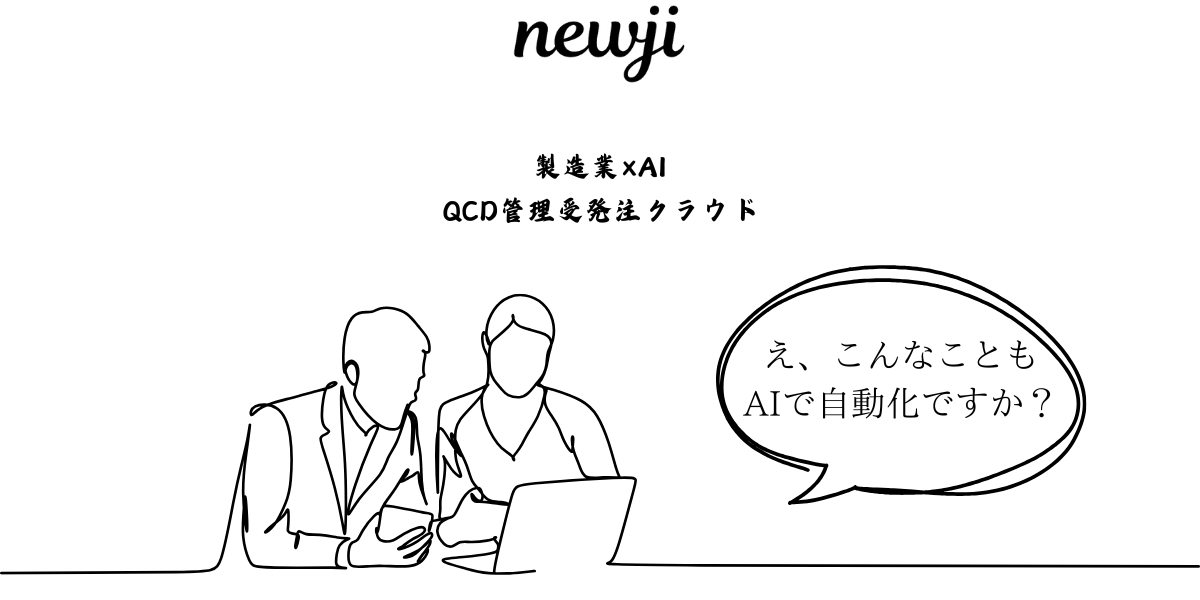
How to predict aging and lifespan of equipment and structures and utilize them for accident prevention measures
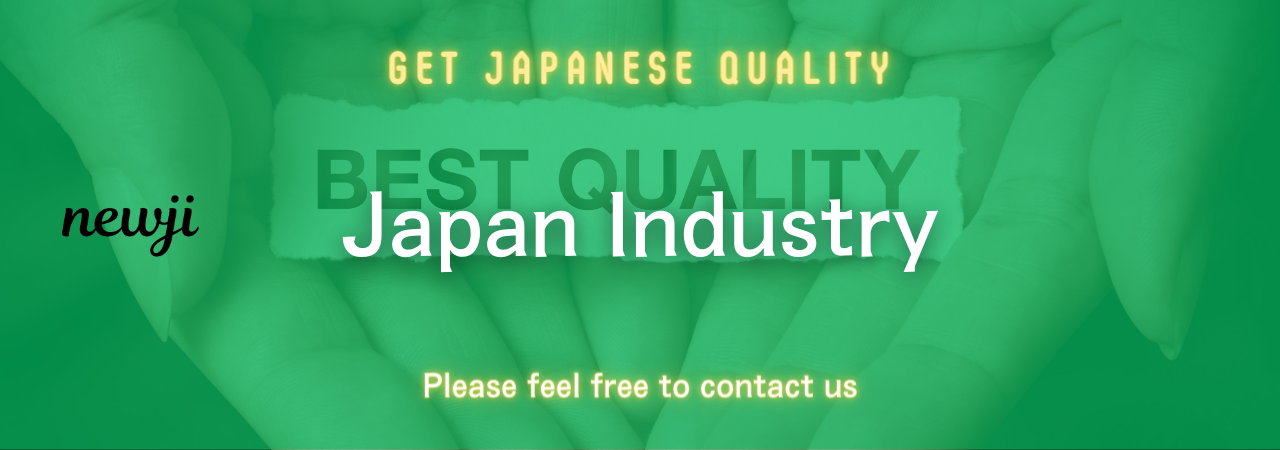
Predicting the aging and lifespan of equipment and structures is an essential task in many industries, from manufacturing to construction and infrastructure management. By understanding how and when these assets may fail, organizations can implement proactive measures to prevent accidents and ensure safety. This process involves a combination of data analysis, monitoring technologies, and predictive maintenance strategies. Let’s explore how these elements come together to help us anticipate equipment and structural deterioration effectively.
目次
Understanding Equipment Aging
Equipment aging refers to the gradual degradation of machinery and structures over time. This deterioration is influenced by various factors, including environmental conditions, operational stress, material fatigue, and inadequate maintenance. Recognizing these factors is crucial for developing accurate predictive models that estimate when equipment or structures might fail.
Key Factors Influencing Aging
Various factors contribute to the aging process of equipment and structures. Some of them include:
– **Environmental Conditions**: Exposure to harsh weather conditions, such as extreme temperatures, humidity, or corrosive substances, can accelerate wear and tear.
– **Operational Stress**: Intensive use, high loads, and frequent startup and shutdown cycles increase the stress on equipment, shortening their lifespan.
– **Material Fatigue**: Repeated mechanical or thermal loading leads to micro-damage within materials, eventually causing them to fail.
– **Maintenance Practices**: Regular maintenance can slow aging, but inadequate or incorrect maintenance can hasten it.
Monitoring Technologies
Integrating monitoring technologies is a critical step in predicting the lifespan of equipment and structures. These technologies can continuously track various parameters, providing valuable insights into the state of an asset.
Sensors and IoT Devices
Sensors and Internet of Things (IoT) devices are instrumental in collecting real-time data on equipment conditions. They measure key metrics such as vibration, temperature, pressure, and load, which are indicative of the equipment’s health.
Structural Health Monitoring (SHM)
SHM systems are designed to evaluate the condition of large-scale structures like bridges, towers, and buildings. These systems use a network of sensors to detect shifts or anomalies in structural integrity. For example, accelerometers can detect excessive vibrations, and strain gauges can measure deformation, both of which signal potential problems.
Data Analysis and Predictive Modeling
Analyzing the data gathered from monitoring systems allows for creating predictive models to anticipate equipment failures and lifespan.
Data Collection and Preprocessing
Data must be collected systematically and processed for accuracy and relevance. This involves cleaning data, dealing with missing values, and correcting any anomalies.
Machine Learning and AI
Machine learning (ML) and artificial intelligence (AI) algorithms can identify patterns and correlations in the data that are not apparent to the human eye. These technologies are particularly effective for predicting equipment failure times and identifying the factors that most significantly impact lifespan.
For instance, ML models can be trained on historical failure data to learn which signs precede equipment breakdowns. They can then predict future failures based on current sensor data, helping to prevent unplanned downtime.
Utilizing Predictions for Accident Prevention
Predictive insights can be leveraged to implement strategies that minimize the risk of accidents caused by equipment and structural failures.
Preventive Maintenance
With reliable lifespan predictions, organizations can schedule maintenance activities before equipment fails. This approach extends the operational life of assets and reduces the likelihood of sudden breakdowns, which could lead to safety incidents.
Risk Assessment and Management
Predictive models support comprehensive risk assessments, allowing organizations to understand which assets are most vulnerable and need attention. By prioritizing high-risk equipment and structures for monitoring and maintenance, companies can efficiently allocate resources and enhance safety.
Design Improvements and Upgrades
Insights from aging predictions can inform design improvements for future equipment and structures. For example, identifying common failure modes may lead to the adoption of more durable materials or changes in structural design to extend lifespan and reduce the likelihood of failure.
Challenges and Considerations
Predicting equipment and structural lifespan is complex and requires careful consideration of several factors.
Data Accuracy and Reliability
The reliability of predictions depends heavily on the quality of data collected. Inaccuracies can lead to wrong forecasts, potentially increasing the risk of unnoticed failures.
Implementation Costs
The integration of monitoring systems and the development of predictive models involve significant initial investment. However, the long-term benefits of accident prevention and maintenance cost savings can justify these expenses.
Regulatory Compliance
Organizations must ensure that their predictive maintenance strategies comply with industry standards and regulations to avoid legal issues.
Conclusion
Predicting the aging and lifespan of equipment and structures is crucial for maintaining safety and operational efficiency. By understanding and monitoring the factors that contribute to aging, utilizing cutting-edge technologies like IoT and AI, and applying predictive maintenance practices, businesses can effectively prevent accidents and extend the life of their assets. Despite challenges, the proactive management of equipment and structures not only ensures safety but also offers economic benefits through reduced downtime and repair costs. As technology continues to advance, the effectiveness of predictive measures is expected to increase, contributing to safer and more reliable operations across various industries.
資料ダウンロード
QCD管理受発注クラウド「newji」は、受発注部門で必要なQCD管理全てを備えた、現場特化型兼クラウド型の今世紀最高の受発注管理システムとなります。
ユーザー登録
受発注業務の効率化だけでなく、システムを導入することで、コスト削減や製品・資材のステータス可視化のほか、属人化していた受発注情報の共有化による内部不正防止や統制にも役立ちます。
NEWJI DX
製造業に特化したデジタルトランスフォーメーション(DX)の実現を目指す請負開発型のコンサルティングサービスです。AI、iPaaS、および先端の技術を駆使して、製造プロセスの効率化、業務効率化、チームワーク強化、コスト削減、品質向上を実現します。このサービスは、製造業の課題を深く理解し、それに対する最適なデジタルソリューションを提供することで、企業が持続的な成長とイノベーションを達成できるようサポートします。
製造業ニュース解説
製造業、主に購買・調達部門にお勤めの方々に向けた情報を配信しております。
新任の方やベテランの方、管理職を対象とした幅広いコンテンツをご用意しております。
お問い合わせ
コストダウンが利益に直結する術だと理解していても、なかなか前に進めることができない状況。そんな時は、newjiのコストダウン自動化機能で大きく利益貢献しよう!
(β版非公開)