- お役立ち記事
- How to Prevent Flash in Injection Molding Through Counter Pressure Control
月間76,176名の
製造業ご担当者様が閲覧しています*
*2025年3月31日現在のGoogle Analyticsのデータより
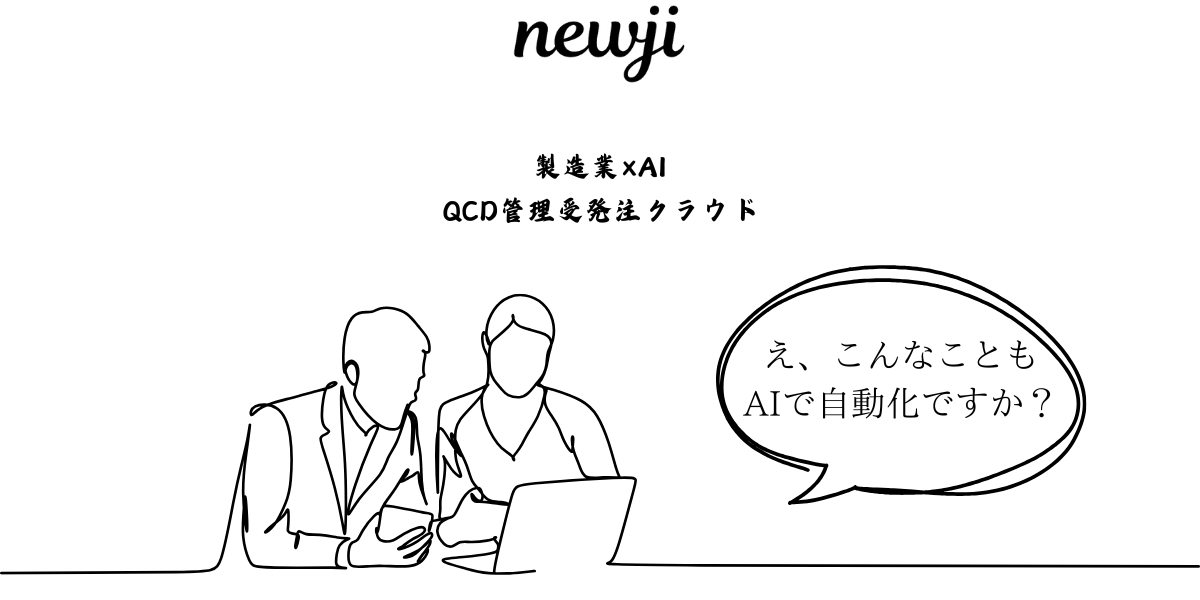
How to Prevent Flash in Injection Molding Through Counter Pressure Control
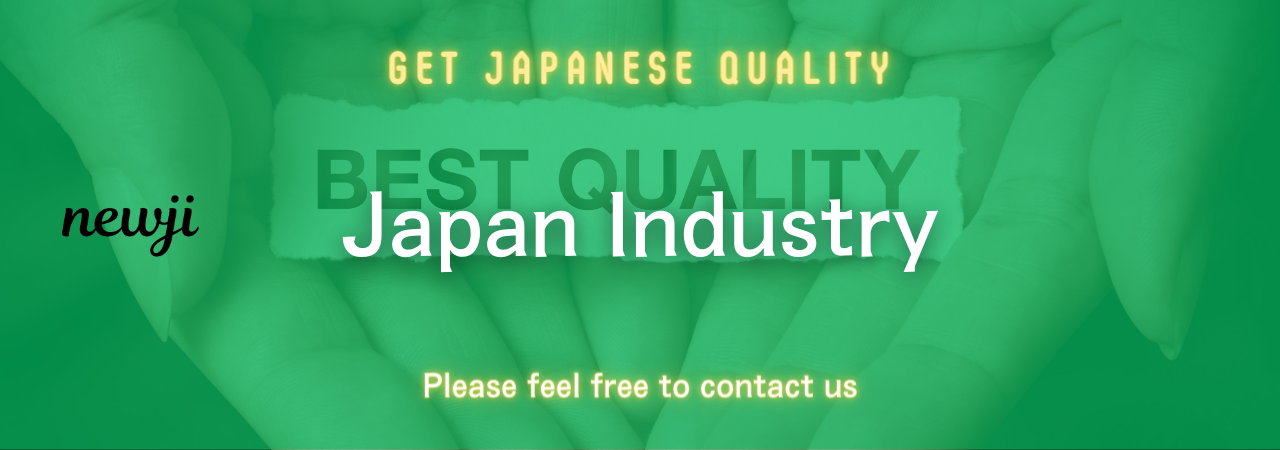
Injection molding is a manufacturing process used to produce plastic parts by injecting molten material into a mold.
It is widely used across various industries due to its efficiency and ability to produce complex shapes with high precision.
However, one common problem faced in injection molding is the occurrence of flash, which refers to the thin layer of excess material that appears at the parting line of the mold.
Flash not only affects the aesthetic quality of the final product but can also compromise its functionality.
目次
What is Flash in Injection Molding?
Flash is a defect that occurs when molten material escapes and leaks out of the mold cavity, which typically happens due to poor mold design or improper machine settings.
When the mold is not tightly closed, the pressure of the injected material can force it through small gaps, resulting in a thin layer of excess material along the edges of the molded part.
This excess material must be removed, leading to additional time and cost in the manufacturing process.
Understanding Counter Pressure Control
Counter pressure control is a technique used to minimize or eliminate flash in injection molding.
It involves applying pressure to the mold during the injection and cooling phases to ensure that the mold halves remain tightly closed.
How Counter Pressure Works
Counter pressure works by applying a reverse force on the mold halves, which counteracts the injection pressure.
This reverse force keeps the mold tightly closed, preventing any molten material from escaping.
There are two types of counter pressure control:
Mechanical Counter Pressure
In mechanical counter pressure, the mold is designed to apply physical force to keep the mold halves tightly closed.
This can be achieved through the use of clamping mechanisms, springs, or other mechanical components.
While effective, mechanical counter pressure can be complex and may require frequent maintenance.
Hydraulic Counter Pressure
Hydraulic counter pressure uses fluid pressure to keep the mold halves closed.
This method involves the use of hydraulic cylinders or other fluid-based systems to generate the necessary force.
Hydraulic counter pressure is more flexible and easier to control compared to mechanical counter pressure.
Benefits of Counter Pressure Control
Implementing counter pressure control in injection molding offers several benefits beyond just preventing flash.
Improved Part Quality
By ensuring that the mold halves remain tightly closed, counter pressure control helps produce parts with better dimensional accuracy and surface finish.
This reduces the need for additional finishing operations.
Enhanced Production Efficiency
Preventing flash reduces the need for post-processing to remove excess material.
This not only saves time but also reduces material waste, leading to cost savings.
Reduced Maintenance
Maintaining a tightly closed mold reduces wear and tear on the mold components, extending their lifespan and reducing the frequency of maintenance and repairs.
Consistent Performance
Counter pressure control allows for more consistent molding conditions, which helps maintain the quality and performance of the molded parts across different production runs.
Implementing Counter Pressure Control
To effectively implement counter pressure control in injection molding, several factors need to be considered:
Mold Design
The mold design should accommodate the addition of counterpressure mechanisms.
Proper mold design ensures that the counter pressure system can be effectively integrated and operate without hindrance.
Machine Settings
The injection molding machine settings must be adjusted to optimize the application of counter pressure.
This includes setting the appropriate injection pressure, counter pressure force, and cooling time.
Material Selection
The choice of material can also influence the effectiveness of counter pressure control.
Materials with higher viscosity may require higher counter pressure to prevent flash.
Monitoring and Control
Implementing monitoring and control systems can help ensure that the counter pressure control is functioning effectively.
Sensors and control systems can provide real-time feedback and adjustments to maintain optimal conditions.
Challenges and Solutions
While counter pressure control offers numerous benefits, it may present some challenges.
Complexity of Implementation
Implementing counter pressure control can be complex and require modifications to existing mold designs and machinery.
Working with experienced engineers and mold designers can help overcome this challenge.
Cost Implications
The initial cost of implementing counter pressure control may be higher due to the need for additional components and modifications.
However, the long-term cost savings from reduced flash and improved part quality can offset these initial expenses.
Training and Expertise
Operating and maintaining a counter pressure control system requires specialized knowledge and training.
Investing in employee training programs can ensure that the system is used effectively.
Conclusion
Flash in injection molding can be a significant issue, impacting both the quality and cost-effectiveness of the manufacturing process.
Counter pressure control offers an effective solution to prevent flash by maintaining a tightly closed mold during injection and cooling.
By optimizing mold design, machine settings, material selection, and implementing appropriate monitoring and control systems, manufacturers can benefit from improved part quality, enhanced production efficiency, and reduced maintenance costs.
Despite the challenges of implementation, the long-term benefits of counter pressure control make it a worthwhile investment for achieving superior results in injection molding.
資料ダウンロード
QCD管理受発注クラウド「newji」は、受発注部門で必要なQCD管理全てを備えた、現場特化型兼クラウド型の今世紀最高の受発注管理システムとなります。
ユーザー登録
受発注業務の効率化だけでなく、システムを導入することで、コスト削減や製品・資材のステータス可視化のほか、属人化していた受発注情報の共有化による内部不正防止や統制にも役立ちます。
NEWJI DX
製造業に特化したデジタルトランスフォーメーション(DX)の実現を目指す請負開発型のコンサルティングサービスです。AI、iPaaS、および先端の技術を駆使して、製造プロセスの効率化、業務効率化、チームワーク強化、コスト削減、品質向上を実現します。このサービスは、製造業の課題を深く理解し、それに対する最適なデジタルソリューションを提供することで、企業が持続的な成長とイノベーションを達成できるようサポートします。
製造業ニュース解説
製造業、主に購買・調達部門にお勤めの方々に向けた情報を配信しております。
新任の方やベテランの方、管理職を対象とした幅広いコンテンツをご用意しております。
お問い合わせ
コストダウンが利益に直結する術だと理解していても、なかなか前に進めることができない状況。そんな時は、newjiのコストダウン自動化機能で大きく利益貢献しよう!
(β版非公開)