- お役立ち記事
- How to prevent human error by introducing poka-yoke that new leaders of equipment technology departments should tackle
月間76,176名の
製造業ご担当者様が閲覧しています*
*2025年3月31日現在のGoogle Analyticsのデータより
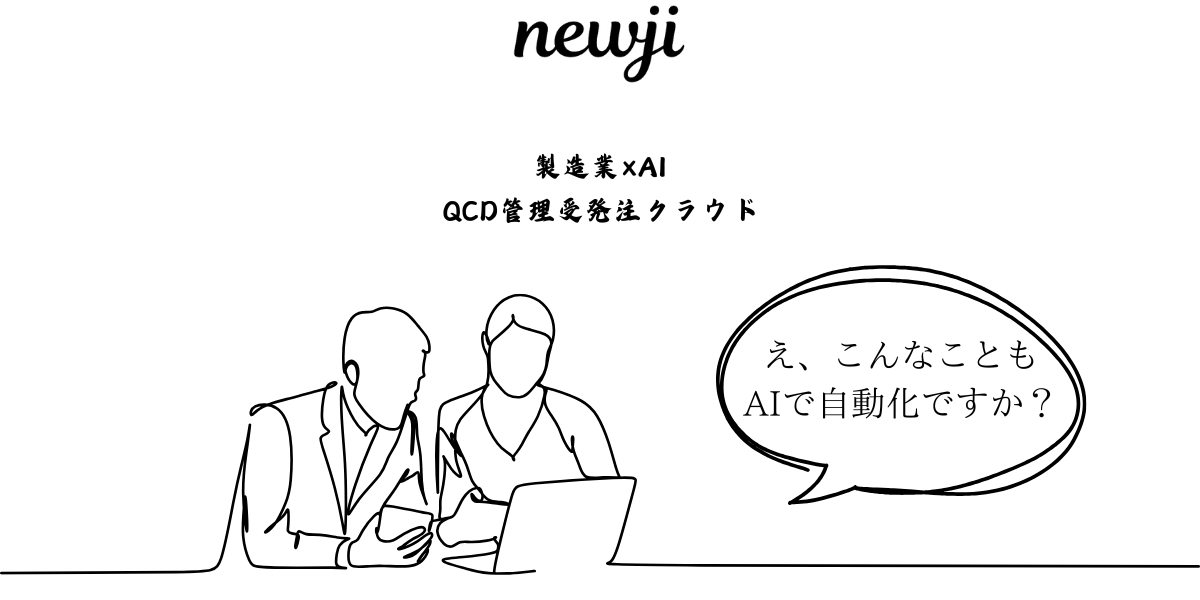
How to prevent human error by introducing poka-yoke that new leaders of equipment technology departments should tackle
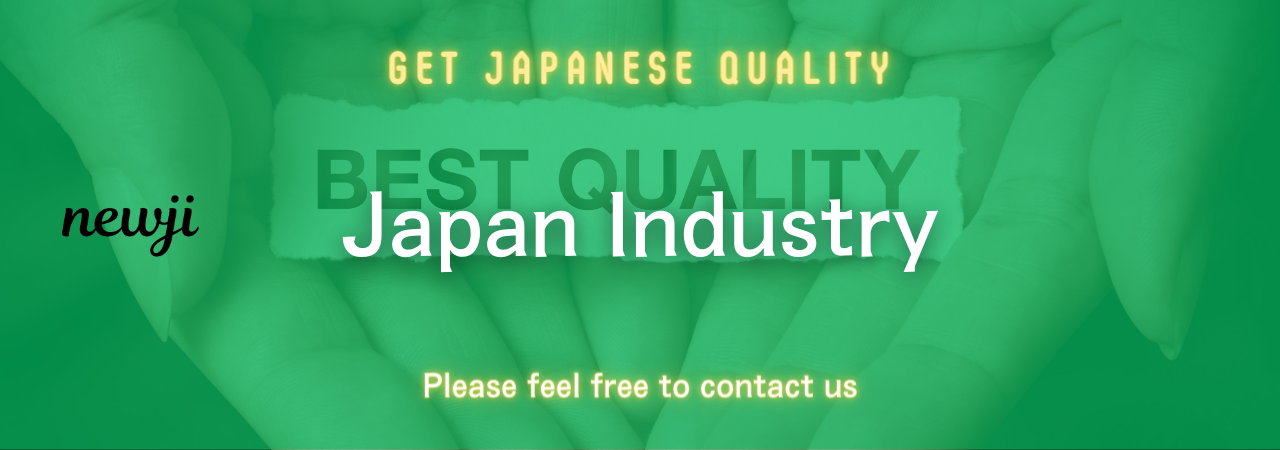
目次
Understanding Poka-Yoke
For new leaders in equipment technology departments, preventing human error is a critical objective.
One effective approach to minimize mistakes in operations is by implementing poka-yoke.
Originating from Japan, poka-yoke is a lean manufacturing tool designed to eliminate and prevent errors.
Poka-yoke translates to “mistake-proofing” and focuses on improving processes to ensure errors are caught before they occur.
This technique can be applied in various settings, from manufacturing floors to administrative processes, making it versatile and valuable for any department.
The Importance of Poka-Yoke
In any organization, human error is inevitable, impacting productivity, safety, and quality.
Errors can lead to time-consuming rework, increased costs, and even safety hazards.
By introducing poka-yoke into your processes, you can significantly reduce these risks.
Poka-yoke’s preventative nature ensures that errors are identified and corrected in real-time, rather than after a defect is discovered.
It enhances operational efficiency and helps in maintaining high-quality standards, which are particularly important in technology-driven environments.
How to Implement Poka-Yoke
Implementing poka-yoke requires a clear understanding of your department’s processes and potential error points.
Here’s a simplified approach to getting started with poka-yoke:
1. Identify Potential Error Sources
The first step in implementing poka-yoke is identifying where errors are most likely to occur.
Analyze your workflows to pinpoint stages where human intervention or decision-making introduces the risk of mistakes.
For instance, in a manufacturing environment, this could be during assembly lines, testing, or packaging processes.
In an administrative department, errors might occur when inputting data or processing documents.
2. Design Error-Proofing Solutions
Once error-prone areas are identified, design effective poka-yoke mechanisms to prevent these mistakes.
Solutions can range from simple changes, like visual cues or templates, to more complex systems like sensors or automated machines that halt processes when anomalies are detected.
For example, color-coding parts can ensure they are assembled correctly, or digital forms with mandatory fields can prevent data entry errors.
Remember, the goal is to design solutions that make it difficult for errors to go unnoticed.
3. Test and Refine Your Solutions
After designing your poka-yoke solutions, it’s crucial to test them in real-time operations.
Observe whether they effectively prevent errors and where improvements might be needed.
This iterative process will allow you to refine your designs for maximum effectiveness, ensuring that they’re both efficient and user-friendly.
Training and Involvement of Staff
To successfully implement poka-yoke, your team must be knowledgeable and engaged with the process.
1. Educate Your Team
Provide training sessions to educate your team about the principles and benefits of poka-yoke.
Understanding why mistake-proofing is essential will help in gaining their support and cooperation.
Ensure that they are aware of how their roles contribute to the overall effectiveness of the poka-yoke systems you establish.
2. Encourage Feedback
Encourage team members to offer feedback on the poka-yoke solutions in place.
Their hands-on experience can provide valuable insights into further improvements or potential oversights.
An open channel for feedback will not only enhance poka-yoke implementations but also foster a collaborative culture geared towards continuous improvement.
Monitoring and Continuous Improvement
Poka-yoke is not a one-time setup; it requires ongoing monitoring and refinement to remain effective.
1. Establish a Monitoring System
Implement a system for regularly reviewing the effectiveness of your poka-yoke mechanisms.
Analyze data related to error rates, process efficiency, and any incidents that occur despite your systems.
Regular audits can provide a clear picture of where additional improvements are needed, helping you stay proactive.
2. Foster a Culture of Improvement
Promote a culture that values innovation and continuous refinement.
Encourage your team to view poka-yoke not just as a static system but as a dynamic strategy that evolves with your department’s needs.
Frequent workshops or staff meetings focused on brainstorming new ideas can also help in identifying potential enhancements.
Conclusion
For new leaders in equipment technology departments, understanding and implementing poka-yoke is an essential strategy for minimizing human error and enhancing operational efficiency.
By systematically identifying error-prone areas, designing and testing solutions, and fostering an engaged and educated team, you can successfully integrate mistake-proofing into your processes.
Remember, poka-yoke is not just about fixing errors — it’s about preventing them altogether.
By taking a proactive approach to error prevention, you can protect your department from the costly consequences of human mistakes while promoting a high standard of quality and efficiency.
資料ダウンロード
QCD管理受発注クラウド「newji」は、受発注部門で必要なQCD管理全てを備えた、現場特化型兼クラウド型の今世紀最高の受発注管理システムとなります。
ユーザー登録
受発注業務の効率化だけでなく、システムを導入することで、コスト削減や製品・資材のステータス可視化のほか、属人化していた受発注情報の共有化による内部不正防止や統制にも役立ちます。
NEWJI DX
製造業に特化したデジタルトランスフォーメーション(DX)の実現を目指す請負開発型のコンサルティングサービスです。AI、iPaaS、および先端の技術を駆使して、製造プロセスの効率化、業務効率化、チームワーク強化、コスト削減、品質向上を実現します。このサービスは、製造業の課題を深く理解し、それに対する最適なデジタルソリューションを提供することで、企業が持続的な成長とイノベーションを達成できるようサポートします。
製造業ニュース解説
製造業、主に購買・調達部門にお勤めの方々に向けた情報を配信しております。
新任の方やベテランの方、管理職を対象とした幅広いコンテンツをご用意しております。
お問い合わせ
コストダウンが利益に直結する術だと理解していても、なかなか前に進めることができない状況。そんな時は、newjiのコストダウン自動化機能で大きく利益貢献しよう!
(β版非公開)