- お役立ち記事
- How to Prevent Molding Defects by Optimizing Clamping Force
月間76,176名の
製造業ご担当者様が閲覧しています*
*2025年3月31日現在のGoogle Analyticsのデータより
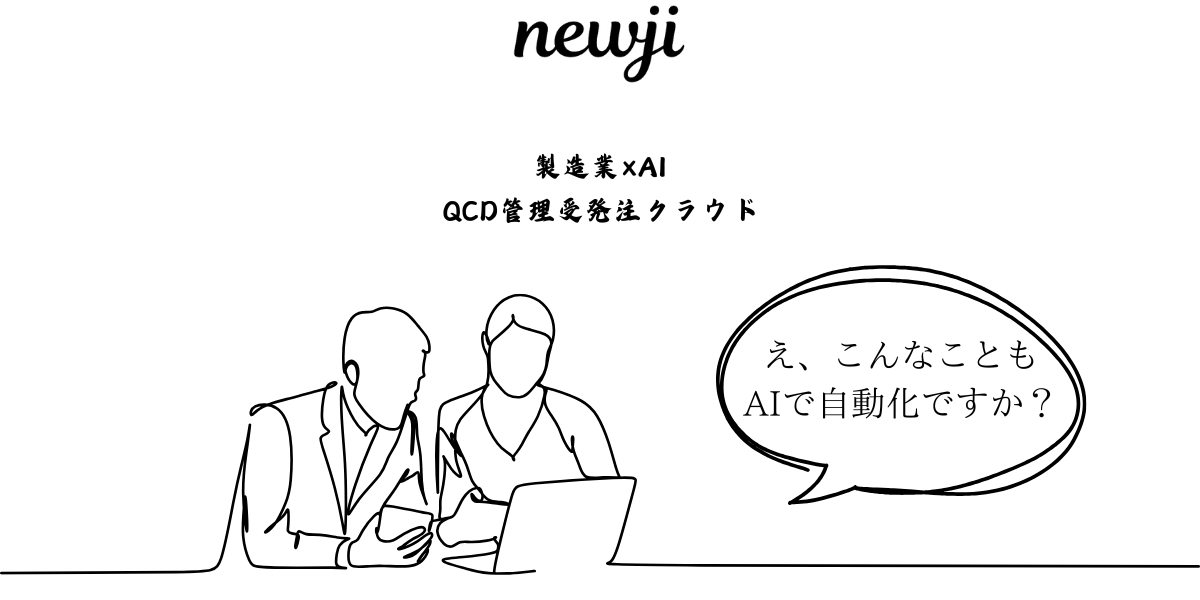
How to Prevent Molding Defects by Optimizing Clamping Force
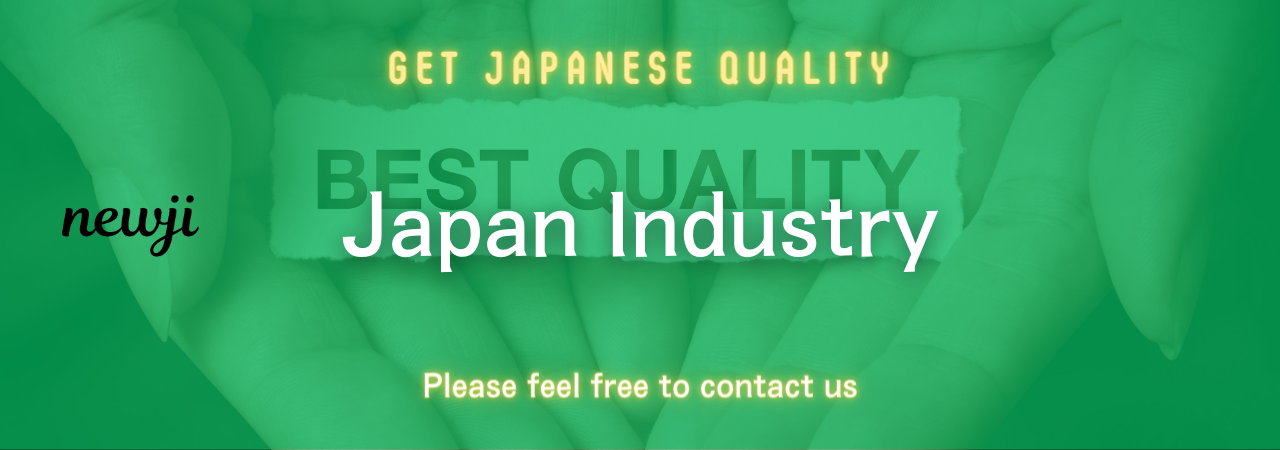
目次
Understanding Clamping Force in Injection Molding
Have you ever wondered why some plastic products have defects while others look perfect?
One crucial factor that plays a significant role in the quality of molded parts is the clamping force in the injection molding process.
Clamping force refers to the pressure applied by the molding machine to keep the mold halves closed during the injection and cooling phases.
When the clamping force is optimized, it ensures a seamless molding process, preventing defects and producing high-quality plastic parts.
The Importance of Clamping Force
The clamping force is vital in the injection molding process as it holds the mold securely in place.
This force helps in withstanding the pressure from the injected molten plastic.
If the clamping force is too low, it can lead to several issues such as flash, where excess plastic escapes from the mold cavity.
On the other hand, if the clamping force is too high, it can stress the clamps and damage the mold, leading to high maintenance costs.
Common Molding Defects Due to Incorrect Clamping Force
Various defects can occur when the clamping force is not optimized.
Let’s take a look at some common molding defects that arise from incorrect clamping force and how optimizing can prevent them:
– **Flash:** This defect occurs when excess material escapes through the parting line of the mold due to insufficient clamping force.
– **Short Shot:** An inadequate filling of the mold often results from excessive clamping force causing the mold to not open properly for a complete fill.
– **Warping:** Uneven clamping pressure can lead to deformation of the molded part as it cools and solidifies.
– **Burn Marks:** When the clamping force is too high, it can cause excessive friction that results in burn marks on the material surface.
Determining the Optimal Clamping Force
To prevent these defects, determining and applying the optimal clamping force is essential.
Here’s how you can achieve it:
Analyzing the Material Used
Different materials require different clamping forces.
Materials with higher viscosity or flow resistance will need a stronger clamping force.
Before starting the injection molding process, analyze the type of material to determine the right force.
Calculating the Projected Area
The projected area of the mold is crucial in calculating the clamping force.
It refers to the maximum area the mold presents to the plastic material being injected.
The projected area is used to calculate the force needed using the equation: Clamping Force = Projected Area x Molding Pressure.
Utilizing Molding Simulation Software
Advanced molding simulation software can help in predicting the best clamping force by analyzing different molding scenarios.
By running these simulations, you can optimize the clamping force without undergoing multiple trial-and-error cycles on the actual machine.
Adjusting Clamping Force During the Molding Process
Even after determining the optimal clamping force, adjustments may still be necessary during the molding process.
Monitoring and adjusting clamping force in real-time ensures consistent quality.
Monitoring Process Parameters
Keep an eye on process parameters such as temperature, injection speed, and pressure.
Significant changes in these parameters might signal the need to adjust the clamping force.
Regular Maintenance of Molding Equipment
Regular maintenance can prevent mechanical failures that could affect the clamping force.
Ensure all mechanical components are in proper working condition and inspect for wear and tear periodically.
Benefits of Optimizing Clamping Force
Optimizing clamping force not only prevents defects but also offers several benefits:
– **Enhanced Product Quality:** Optimizing clamping force ensures the production of flawless parts by minimizing the occurrence of defects.
– **Cost Efficiency:** Avoiding defects like flash or short shots reduces material wastage and machine downtime, leading to cost-efficiency.
– **Increased Production Speed:** An optimized clamping force streamlines the injection molding process, increasing the overall production speed.
– **Sustainability:** By reducing waste and improving efficiency, optimized clamping force contributes positively to environmental sustainability.
Best Practices for Preventing Molding Defects
By adopting certain best practices, you can further enhance the molding process and prevent defects.
Training Personnel
Ensure that all operating personnel are well trained in setting and adjusting clamping force.
A skilled team can make informed decisions to optimize the molding process effectively.
Documenting Process Parameters
Document the set parameters and any adjustments made during the process for future reference.
This documentation helps in troubleshooting and fine-tuning processes for similar projects.
Implementing Quality Checks
Regular quality inspections of molded parts can help in early detection of defects.
By catching these issues early, adjustments can be made swiftly to prevent a batch of defective products.
Conclusion
Optimizing clamping force is a critical step in preventing molding defects during the injection molding process.
Understanding the importance of clamping force, and knowing how to calculate and adjust it can go a long way in producing high-quality plastic parts.
By leveraging modern technologies and best practices, manufacturers can achieve a seamless molding process, resulting in flawless products, efficiency, and sustainability.
資料ダウンロード
QCD管理受発注クラウド「newji」は、受発注部門で必要なQCD管理全てを備えた、現場特化型兼クラウド型の今世紀最高の受発注管理システムとなります。
ユーザー登録
受発注業務の効率化だけでなく、システムを導入することで、コスト削減や製品・資材のステータス可視化のほか、属人化していた受発注情報の共有化による内部不正防止や統制にも役立ちます。
NEWJI DX
製造業に特化したデジタルトランスフォーメーション(DX)の実現を目指す請負開発型のコンサルティングサービスです。AI、iPaaS、および先端の技術を駆使して、製造プロセスの効率化、業務効率化、チームワーク強化、コスト削減、品質向上を実現します。このサービスは、製造業の課題を深く理解し、それに対する最適なデジタルソリューションを提供することで、企業が持続的な成長とイノベーションを達成できるようサポートします。
製造業ニュース解説
製造業、主に購買・調達部門にお勤めの方々に向けた情報を配信しております。
新任の方やベテランの方、管理職を対象とした幅広いコンテンツをご用意しております。
お問い合わせ
コストダウンが利益に直結する術だと理解していても、なかなか前に進めることができない状況。そんな時は、newjiのコストダウン自動化機能で大きく利益貢献しよう!
(β版非公開)