- お役立ち記事
- How to Prevent Production Line Downtime with Parts Supply Management
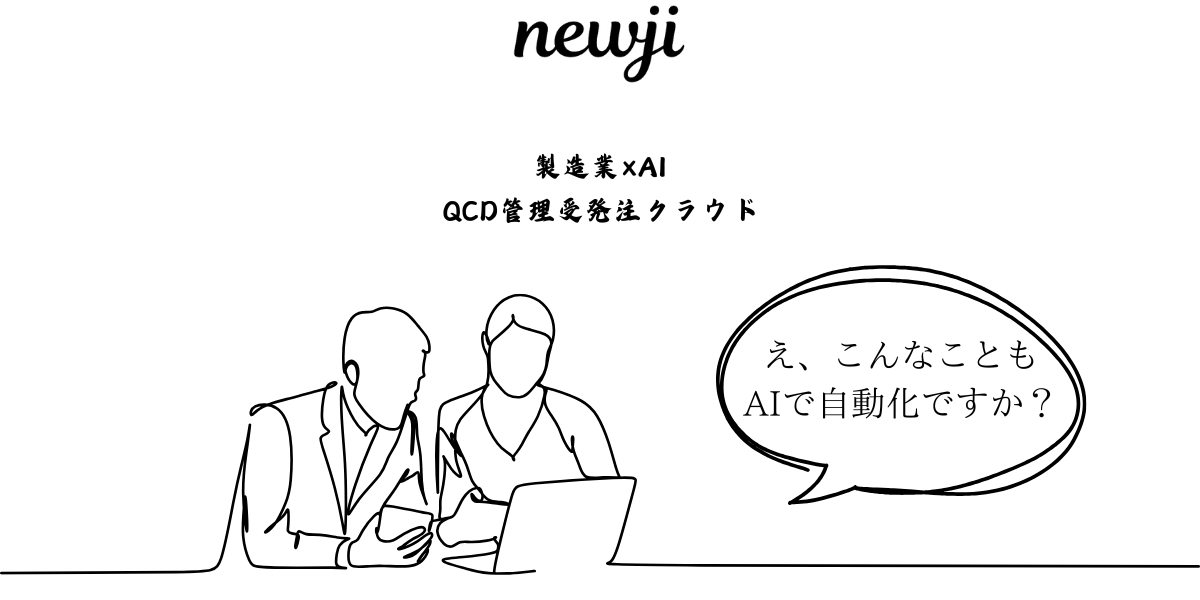
How to Prevent Production Line Downtime with Parts Supply Management
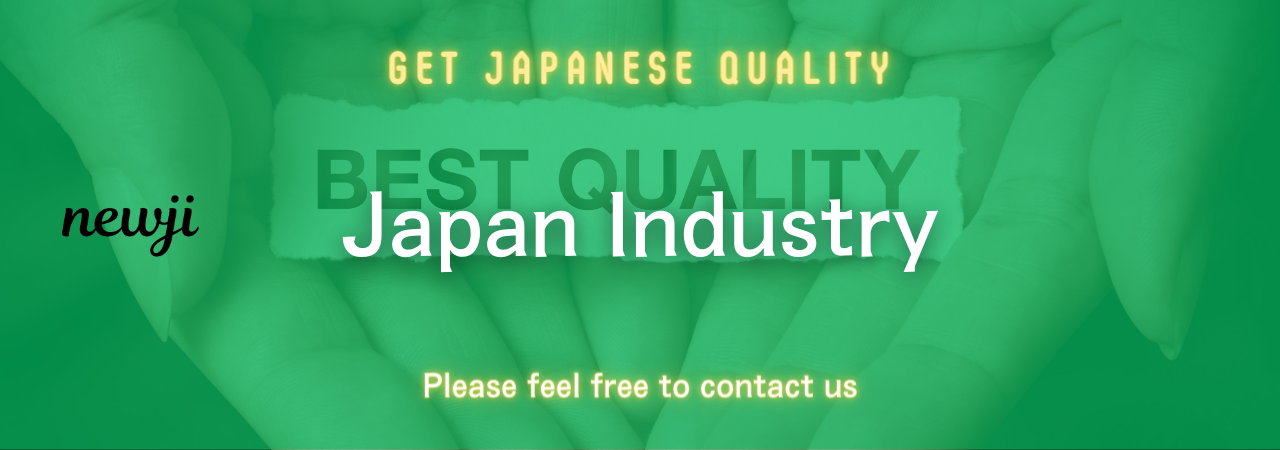
When it comes to manufacturing, one of the biggest challenges faced by businesses is production line downtime.
Downtime not only disrupts operations, but also results in significant financial losses.
However, there are ways to minimize these interruptions, one of which is effective parts supply management.
In this article, we will look at how proper parts management can prevent production line downtime and ensure smooth, continuous operations.
目次
Understanding Production Line Downtime
Production line downtime refers to any period during which manufacturing processes are halted.
Downtime can be caused by various factors, including machine breakdowns, lack of raw materials, labor shortages, and inefficiencies in the supply chain.
Every minute of downtime can translate to lost revenue, delayed orders, and dissatisfied customers.
The Financial Impact of Downtime
For many businesses, the cost of downtime can be staggering.
Not only does it mean lost production time, but also the additional costs of repairs, overtime, and expedited shipping to meet delayed schedules.
In some cases, repeated downtime can damage a company’s reputation, leading to lost business opportunities.
Therefore, minimizing downtime is crucial for maintaining profitability and competitive advantage.
The Role of Parts Supply Management
Effective parts supply management involves ensuring that all necessary parts and materials are available when needed.
It includes forecasting demand, maintaining appropriate inventory levels, and developing strong relationships with suppliers.
By managing parts supply efficiently, companies can mitigate the risks of production line downtime.
Forecasting Demand
Accurate demand forecasting is essential for parts supply management.
By analyzing historical data and market trends, businesses can predict their needs more accurately.
This helps in maintaining an optimal inventory, reducing the risk of both overstocking and stockouts.
Advanced software tools can be used to generate forecasts that take into account seasonal variations, market dynamics, and lead times.
Maintaining Optimal Inventory Levels
Maintaining optimal inventory levels is a balancing act.
While having too much inventory ties up capital and incurs storage costs, having too little can lead to production halts.
Implementing an inventory management system can help in tracking stock levels, setting reorder points, and automating replenishment processes.
Just-in-time (JIT) inventory practices are also useful, as they aim to receive parts just when they are needed, minimizing storage costs and waste.
Supplier Relationships
Building strong relationships with reliable suppliers is a cornerstone of parts supply management.
Reliable suppliers ensure timely deliveries and are more likely to respond quickly in case of urgent requirements.
Establishing clear communication channels and performance metrics can help in evaluating supplier reliability.
Long-term contracts and collaborative planning with suppliers can also contribute to a more stable parts supply chain.
Strategies to Prevent Downtime with Parts Supply Management
To prevent production line downtime, businesses must implement robust strategies focused on effective parts supply management.
Here are some key strategies to consider:
Implementing an Inventory Management System
An efficient inventory management system helps in keeping track of parts in real-time.
It ensures that inventory levels are always optimal by providing alerts for low stock, generating purchase orders, and tracking deliveries.
Systems that offer integration with other business processes, such as production planning and procurement, can further enhance efficiency.
Regular Maintenance and Inspection
Regular maintenance and timely inspection of machinery are crucial to prevent unexpected breakdowns.
Having a maintenance schedule ensures that equipment is serviced and any worn-out parts are replaced before they fail.
This proactive approach minimizes downtime and maintains the smooth operation of the production line.
Developing a Backup Supplier Network
Relying on a single supplier can be risky.
It is advisable to develop a network of backup suppliers.
In case the primary supplier fails to deliver, a backup can step in and prevent disruption.
Diversifying the supply chain reduces dependency risks and enhances resilience.
Employee Training and Empowerment
Employees play a critical role in managing parts supply and preventing downtime.
Providing regular training ensures that they are aware of best practices and procedures.
Empower employees to make decisions and take proactive steps in case of potential supply chain issues.
Involving them in decision-making processes can enhance their commitment and contribution to downtime prevention.
Embracing Technology
Modern technologies offer various solutions that can aid in parts supply management.
Automation and IoT
Automation tools and the Internet of Things (IoT) can streamline parts supply management.
Automated systems can track stock levels, place orders, and manage deliveries without human intervention.
IoT devices can monitor machinery conditions and predict when parts need replacement, allowing for timely maintenance.
Data Analytics
Advanced data analytics provides insights into supply chain dynamics and production patterns.
By analyzing data, businesses can identify bottlenecks, forecast demand more accurately, and optimize inventory levels.
Predictive analytics can help in anticipating potential issues and taking preventive measures.
Cloud-Based Solutions
Cloud-based inventory management solutions offer flexibility and scalability.
These solutions enable real-time tracking of inventory, streamline communication with suppliers, and facilitate quick decision-making.
Collaborative platforms can also enhance coordination among different departments, ensuring that everyone is on the same page.
Conclusion
Preventing production line downtime is essential for the success of any manufacturing business.
Effective parts supply management plays a crucial role in achieving this goal.
By forecasting demand accurately, maintaining optimal inventory levels, developing strong supplier relationships, and embracing modern technologies, businesses can minimize the risks of downtime.
Implementing these strategies not only ensures continuous production but also contributes to overall operational efficiency and profitability.
資料ダウンロード
QCD調達購買管理クラウド「newji」は、調達購買部門で必要なQCD管理全てを備えた、現場特化型兼クラウド型の今世紀最高の購買管理システムとなります。
ユーザー登録
調達購買業務の効率化だけでなく、システムを導入することで、コスト削減や製品・資材のステータス可視化のほか、属人化していた購買情報の共有化による内部不正防止や統制にも役立ちます。
NEWJI DX
製造業に特化したデジタルトランスフォーメーション(DX)の実現を目指す請負開発型のコンサルティングサービスです。AI、iPaaS、および先端の技術を駆使して、製造プロセスの効率化、業務効率化、チームワーク強化、コスト削減、品質向上を実現します。このサービスは、製造業の課題を深く理解し、それに対する最適なデジタルソリューションを提供することで、企業が持続的な成長とイノベーションを達成できるようサポートします。
オンライン講座
製造業、主に購買・調達部門にお勤めの方々に向けた情報を配信しております。
新任の方やベテランの方、管理職を対象とした幅広いコンテンツをご用意しております。
お問い合わせ
コストダウンが利益に直結する術だと理解していても、なかなか前に進めることができない状況。そんな時は、newjiのコストダウン自動化機能で大きく利益貢献しよう!
(Β版非公開)