- お役立ち記事
- How to proceed with effective why-why analysis and key points to prevent recurrence and leakage of defects
月間77,185名の
製造業ご担当者様が閲覧しています*
*2025年2月28日現在のGoogle Analyticsのデータより
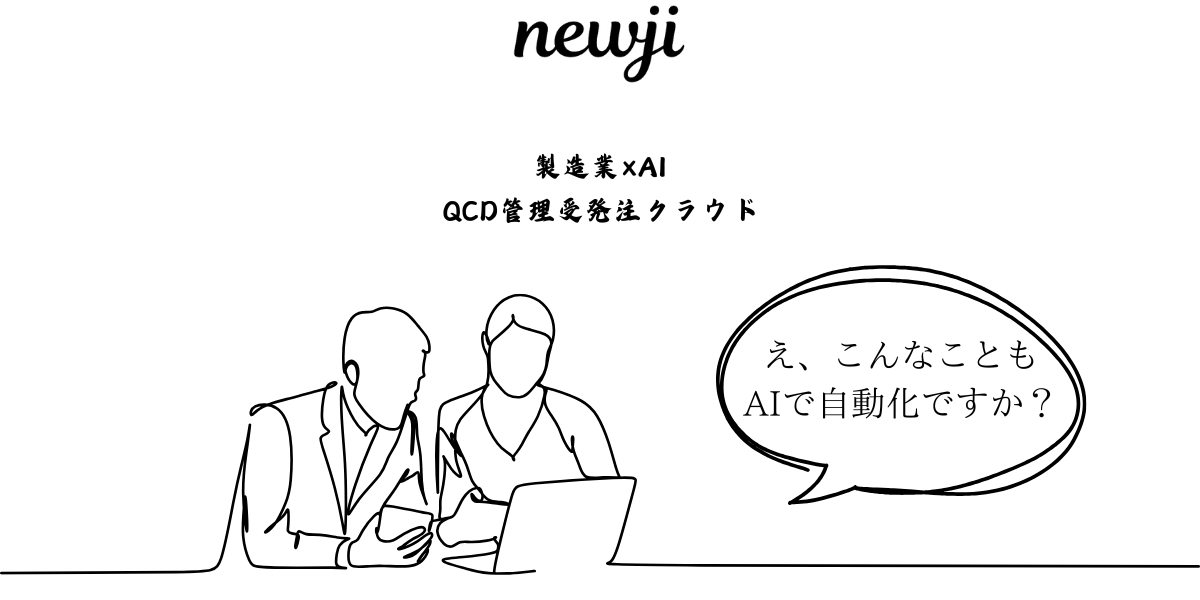
How to proceed with effective why-why analysis and key points to prevent recurrence and leakage of defects
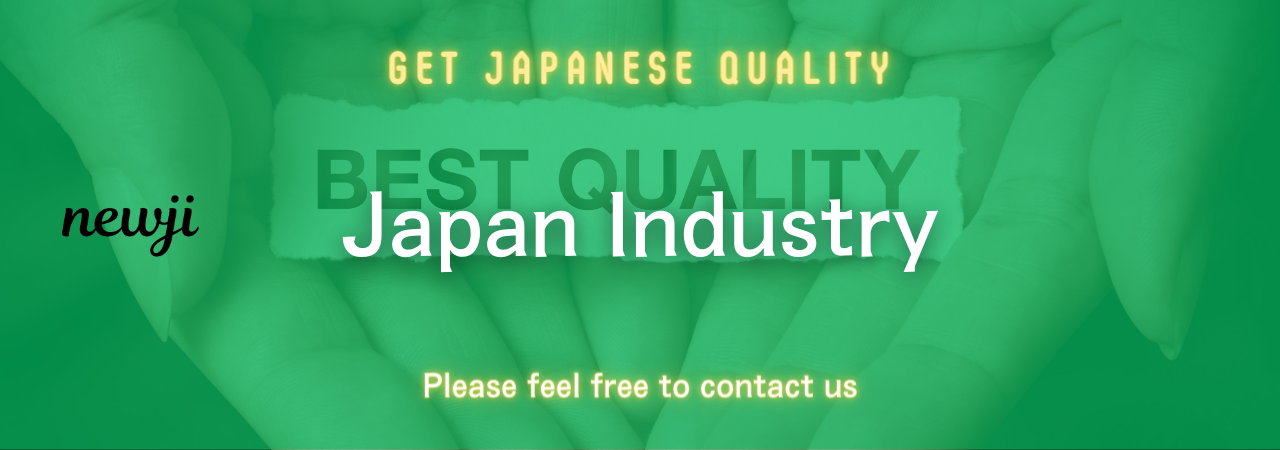
目次
Understanding the Why-Why Analysis
The why-why analysis is a problem-solving method aimed at uncovering the root cause of issues or defects.
It involves repeatedly asking the question “why” to peel away the layers of symptoms and reach the fundamental cause.
This technique helps not only in identifying the root cause but also in preventing future occurrences of similar problems.
The method is simple but can be incredibly effective if done correctly.
Its simplicity makes it a great tool for teams across different industries to improve processes and products.
Let’s explore how to carry out an effective why-why analysis and point out the key factors needed to ensure successful prevention of defect recurrence and leakage.
Step-by-Step Guide to Conducting Why-Why Analysis
Step 1: Identify the Problem
To start with the why-why analysis, you first need to clearly define the problem.
A well-defined problem helps in narrowing down the analysis and increases the accuracy of finding the root cause.
Be specific about the issue at hand.
For example, instead of saying, “The machine isn’t working,” specify, “The conveyor belt motor stopped functioning during a production cycle.”
Step 2: Formulate the First “Why”
Ask the first “Why” to understand why the problem occurred.
The answer to this question should provide the immediate cause of the issue.
For instance, why did the conveyor belt motor stop functioning?
The answer could be, “Because it overheated.”
Step 3: Dig Deeper with Subsequent “Whys”
Once you have an answer, continue asking “why” to delve deeper into the cause.
The objective is to go beyond surface reasoning and discover the underlying cause.
Why did the motor overheat?
Perhaps the answer is, “Because the cooling fan failed to operate.”
Step 4: Continue Asking “Why” Until You Reach the Root Cause
Keep asking “why” until you find a reason that is actionable and not merely another symptom.
The analysis usually requires asking “why” around five times, but the number can vary.
Let’s continue: why did the cooling fan fail to operate?
The reason might be, “Because of a failure in the power supply to the fan.”
Step 5: Identify the Root Cause
When the answers reach a point where further questioning does not lead to new insights or deeper causes, you have likely reached the root cause of the problem.
After examining why the power supply failed, you could find that the power supply malfunctioned due to poor maintenance.
Key Points to Effectively Prevent Recurrence
Implement Corrective Actions
Once the root cause is determined, it is crucial to implement corrective actions to fix it and prevent similar issues from happening again.
For instance, if the root cause was inadequate maintenance, your corrective action might be to establish a regular maintenance schedule.
Monitor Changes and Adjust
Changes should be monitored over time to ensure they are effective.
Collect data on the defect or problem to see if the recurrence has decreased or any new issues have arisen from the changes made.
This monitoring helps in understanding whether the corrective actions are working effectively or need adjustment.
Engage Your Team
Problem-solving is often more effective when a team works together.
The insights and perspectives of diverse team members can shed light on different aspects of the problem and brainstorming solutions.
Involving members from multiple departments ensures a more comprehensive approach and broader commitment to the solution.
Avoid Leakage of Defects
Improve and Strengthen Processes
Identify process gaps or weaknesses that allowed the defect to occur and address them.
Strengthening these processes helps in catching defects before they escalate or impact the final product.
Regular Training and Education
Ensure that all team members are well-trained and informed about new processes or changes.
Continued education helps employees understand their roles in defect prevention and how to address issues promptly when they arise.
Utilize Technology and Automation
Where feasible, leverage technology to automate processes, reducing human error.
Automation can be used to track processes, monitor systems, and alert teams to potential issues before they become more significant.
Conclusion
A why-why analysis can be an effective tool for identifying root causes and preventing recurrence and leakage of defects.
By using this structured approach to problem-solving, organizations can significantly minimize disruptions and improve overall quality.
It requires a commitment to detail, thoroughness, and regular follow-ups to be genuinely effective.
Through team collaboration, continuous monitoring, and process adjustments, companies can create a robust culture of quality and efficiency.
資料ダウンロード
QCD管理受発注クラウド「newji」は、受発注部門で必要なQCD管理全てを備えた、現場特化型兼クラウド型の今世紀最高の受発注管理システムとなります。
ユーザー登録
受発注業務の効率化だけでなく、システムを導入することで、コスト削減や製品・資材のステータス可視化のほか、属人化していた受発注情報の共有化による内部不正防止や統制にも役立ちます。
NEWJI DX
製造業に特化したデジタルトランスフォーメーション(DX)の実現を目指す請負開発型のコンサルティングサービスです。AI、iPaaS、および先端の技術を駆使して、製造プロセスの効率化、業務効率化、チームワーク強化、コスト削減、品質向上を実現します。このサービスは、製造業の課題を深く理解し、それに対する最適なデジタルソリューションを提供することで、企業が持続的な成長とイノベーションを達成できるようサポートします。
製造業ニュース解説
製造業、主に購買・調達部門にお勤めの方々に向けた情報を配信しております。
新任の方やベテランの方、管理職を対象とした幅広いコンテンツをご用意しております。
お問い合わせ
コストダウンが利益に直結する術だと理解していても、なかなか前に進めることができない状況。そんな時は、newjiのコストダウン自動化機能で大きく利益貢献しよう!
(β版非公開)