- お役立ち記事
- How to proceed with efficient accelerated testing and failure analysis to build reliability in electronic equipment
月間77,185名の
製造業ご担当者様が閲覧しています*
*2025年2月28日現在のGoogle Analyticsのデータより
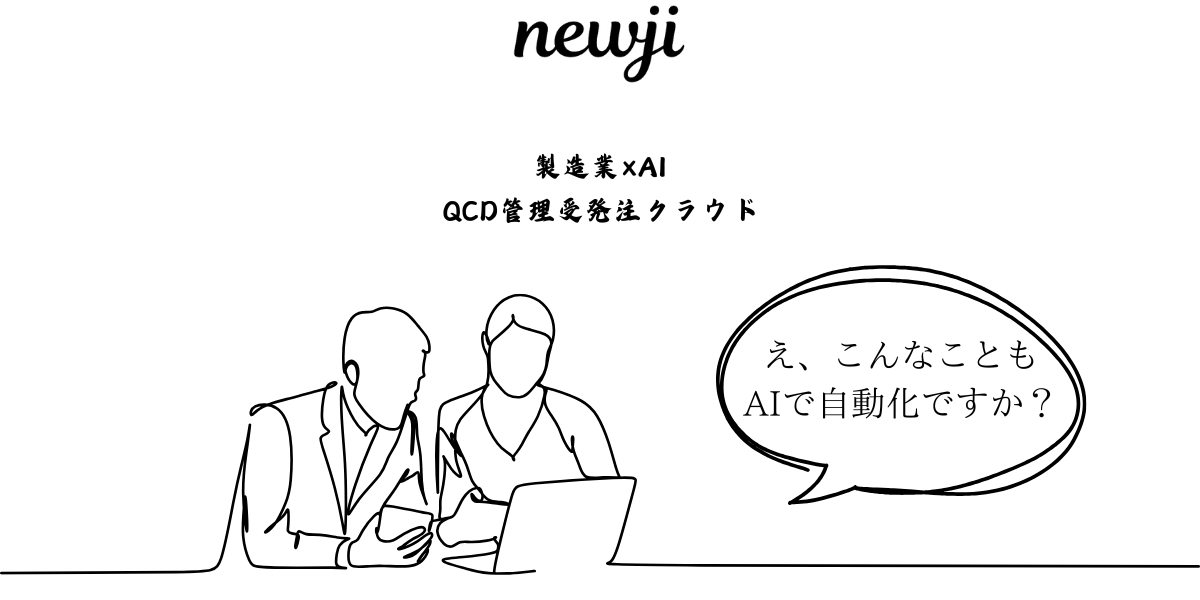
How to proceed with efficient accelerated testing and failure analysis to build reliability in electronic equipment
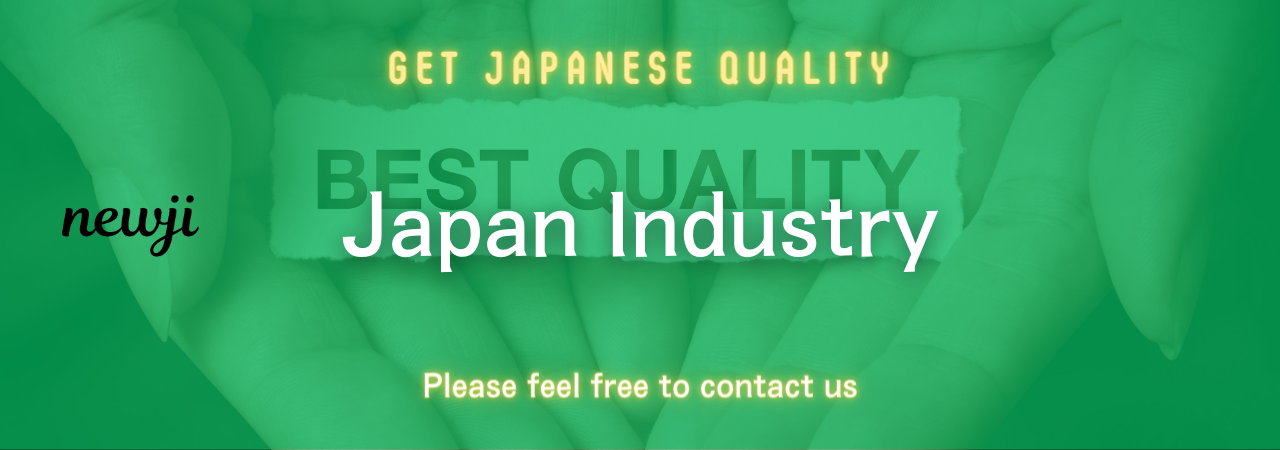
目次
Understanding Accelerated Testing
Accelerated testing is a crucial methodology in the electronics industry, particularly for those looking to enhance product reliability in a time-efficient manner.
It involves subjecting electronic devices to heightened operational stresses to identify potential failure modes and weak components before they hit the market.
This process enables manufacturers to simulate long-term usage conditions in a shorter period, allowing for quicker identification of design flaws or material weaknesses.
By accelerating the aging process, engineers can predict how a product will perform over its expected lifespan.
Understanding and implementing these tests effectively can save time and money while boosting overall product quality.
Types of Accelerated Testing
There are several types of accelerated testing strategies employed within the industry.
Each serves its unique purpose and helps in uncovering different potential weaknesses.
Some of the notable ones include:
Highly Accelerated Life Testing (HALT)
HALT is a process used to push products to their absolute limits under extreme conditions.
The aim is to detect design flaws by stressing products beyond their specifications.
This form of testing identifies the operational and destruct limits of the product, offering insights into its potential longevity and performance.
Highly Accelerated Stress Screening (HASS)
After identifying potential faults in HALT, HASS comes into play as a production screening tool.
The primary goal of HASS is to ensure that products manufactured meet the quality standards established during the design phase.
It’s more of a quality assurance process that focuses on catching faults that might have slipped through the manufacturing process unnoticed.
Thermal Cycling and Shock Testing
This form of testing subjects the electronic components to rapidly changing temperatures.
Thermal cycling exposes the components to cycles of heating and cooling, while thermal shock testing involves transferring products from one extreme temperature to another quickly.
These tests are essential for evaluating the electronic equipment’s resistance to expansion and contraction, which can cause stress on the components.
The Importance of Accelerated Testing
Accelerated testing plays a significant role in maintaining and enhancing the reliability of electronic equipment.
By ensuring that products are tested thoroughly before release, manufacturers can anticipate and rectify potential problems.
This leads to reduced warranty claims, enhanced customer satisfaction, and overall product safety.
Producing reliable products not only strengthens brand reputation but also strengthens customer trust, establishing the company as a reliable provider in the competitive electronics market.
Implementing Effective Failure Analysis
Failure analysis is a critical component of the reliability-building process in electronics.
After accelerated testing reveals potential weaknesses, failure analysis provides an in-depth investigation into the causes behind those failures.
Steps in Failure Analysis
The failure analysis process involves several key steps, each essential to understanding the root cause of a product’s weakness.
Failure Verification
The first step is to confirm and reproduce the failure that was detected during testing.
This is crucial for ensuring that the failure was not an isolated incident or an error during the testing process.
Fault Isolation
Once the failure is verified, the next step involves isolating the fault down to a specific component or assembly.
This often requires sophisticated diagnostic tools and techniques.
Root Cause Analysis
This step involves in-depth analysis to determine the fundamental reason for the failure.
Engineers may use techniques such as x-ray imaging, scanning electron microscopy, or chemical analysis to gain insight into the problem at a material level.
Corrective Action
After identifying the root cause, the next step is formulating a corrective action plan.
This could involve design changes, material substitution, altering manufacturing processes, or any combination of these to prevent future failures.
Combining Accelerated Testing and Failure Analysis
When utilized together, accelerated testing and failure analysis provide a comprehensive approach to building reliability in electronic devices.
Accelerated testing helps identify potential failure points quickly, while failure analysis delves into understanding and solving those failures.
The integration of these processes into the product development cycle ensures that products not only meet expected performance standards but also last longer and perform more reliably in the field.
Overcoming Challenges
Integrating these methodologies isn’t without its challenges.
Manufacturers may face issues like time and resource constraints or dealing with the complexity of advanced electronic designs.
However, technological advancements in testing equipment and analytical methods are making it easier to achieve accurate results and implement changes efficiently.
Investing in Skilled Personnel
Organizations must also invest in skilled personnel who can effectively operate testing equipment and interpret results.
The reliance on skilled engineers and technicians cannot be overstated, as their expertise is vital in drawing meaningful conclusions and executing corrective actions appropriately.
Conclusion
For companies striving to deliver reliable electronic equipment, effective accelerated testing and failure analysis are indispensable.
Together, these processes minimize risks associated with product failures, enhance customer satisfaction, and ultimately protect brand integrity.
As technology continues to evolve, so too will the methods for testing and analysis, offering new opportunities to build ever more dependable electronic devices.
資料ダウンロード
QCD管理受発注クラウド「newji」は、受発注部門で必要なQCD管理全てを備えた、現場特化型兼クラウド型の今世紀最高の受発注管理システムとなります。
ユーザー登録
受発注業務の効率化だけでなく、システムを導入することで、コスト削減や製品・資材のステータス可視化のほか、属人化していた受発注情報の共有化による内部不正防止や統制にも役立ちます。
NEWJI DX
製造業に特化したデジタルトランスフォーメーション(DX)の実現を目指す請負開発型のコンサルティングサービスです。AI、iPaaS、および先端の技術を駆使して、製造プロセスの効率化、業務効率化、チームワーク強化、コスト削減、品質向上を実現します。このサービスは、製造業の課題を深く理解し、それに対する最適なデジタルソリューションを提供することで、企業が持続的な成長とイノベーションを達成できるようサポートします。
製造業ニュース解説
製造業、主に購買・調達部門にお勤めの方々に向けた情報を配信しております。
新任の方やベテランの方、管理職を対象とした幅広いコンテンツをご用意しております。
お問い合わせ
コストダウンが利益に直結する術だと理解していても、なかなか前に進めることができない状況。そんな時は、newjiのコストダウン自動化機能で大きく利益貢献しよう!
(β版非公開)