- お役立ち記事
- How to proceed with FMEA/FTA and how to effectively utilize it to eliminate problems
月間77,185名の
製造業ご担当者様が閲覧しています*
*2025年2月28日現在のGoogle Analyticsのデータより
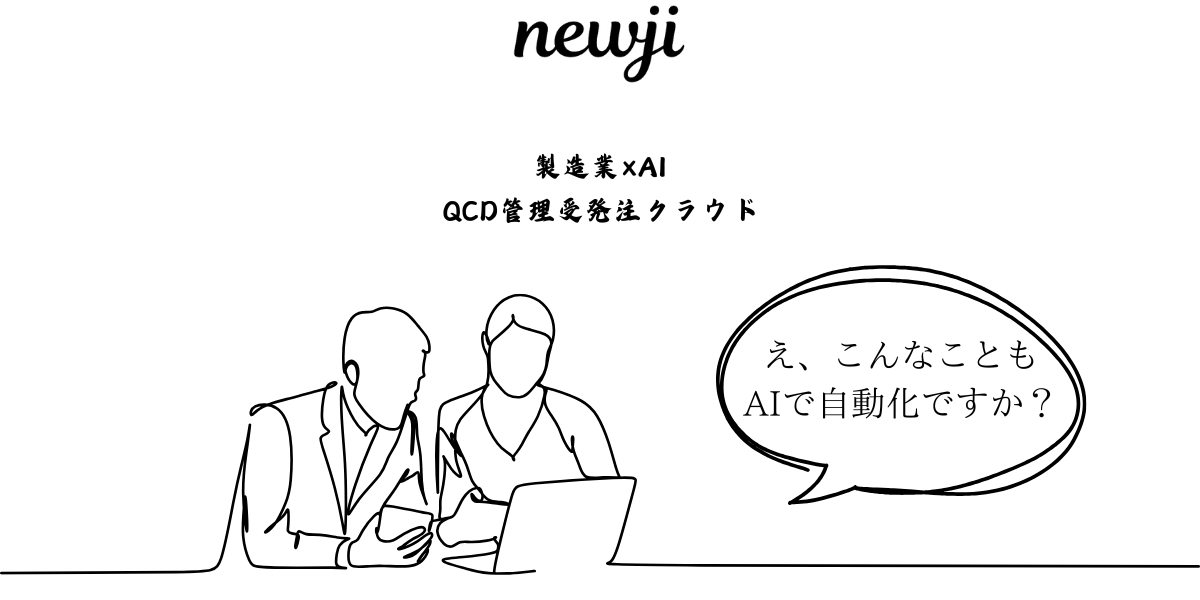
How to proceed with FMEA/FTA and how to effectively utilize it to eliminate problems
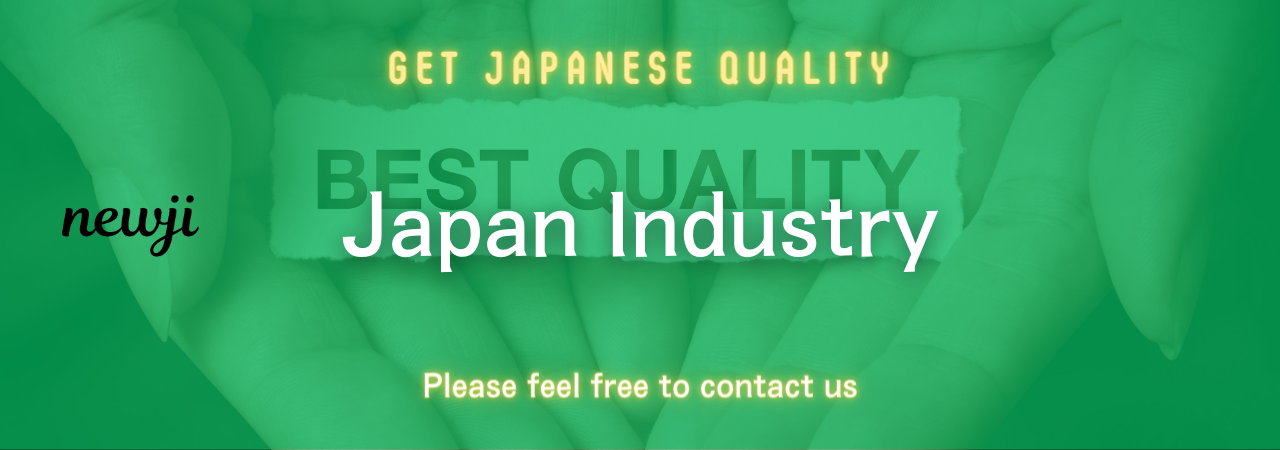
FMEA (Failure Modes and Effects Analysis) and FTA (Fault Tree Analysis) are powerful tools used in engineering and process management to identify and mitigate potential issues before they become real problems. These methodologies help ensure the reliability and safety of systems by analyzing potential failure modes and their impacts. Let’s explore how to proceed with FMEA and FTA, along with ways to effectively utilize these tools to eliminate problems.
目次
Understanding FMEA and Its Process
FMEA is a systematic approach used to identify potential failure modes within a system and assess their effects on the overall operation. The primary goal is to prioritize risks and implement corrective actions to minimize or eliminate failures.
Steps to Conduct FMEA
1. **Define the Scope**: Begin by clearly defining the scope of the FMEA. This includes identifying the system, subsystem, or process to analyze. Having a well-defined scope ensures that efforts are focused and effective.
2. **Assemble a Team**: Gather a multidisciplinary team with expertise in different areas relevant to the system. This team collaboration ensures diverse perspectives and expertise are included in the analysis.
3. **Identify Potential Failure Modes**: List all possible ways in which a component, system, or process might fail. This can include anything from hardware malfunctions to human errors.
4. **Analyze the Effects**: For each failure mode identified, assess the potential effects on the system. Consider factors like safety risks, operational impacts, and compliance with regulations.
5. **Prioritize Risks**: Use a risk priority number (RPN) to prioritize the failure modes. The RPN is calculated by multiplying the severity, occurrence, and detection ratings. Focus on the highest RPNs for corrective action.
6. **Develop and Implement Action Plans**: For high-priority risks, develop action plans to mitigate or eliminate the potential failure. This may involve redesigning components, implementing new controls, or enhancing training.
7. **Review and Update**: Regularly review and update the FMEA as systems change or new insights are gained. This ensures that the analysis remains relevant and effective in addressing potential failures.
Exploring the FTA Methodology
Fault Tree Analysis (FTA) is another methodical approach used to analyze potential causes of system failures. Unlike FMEA’s bottom-up approach, FTA uses a top-down method to identify root causes of system failures.
Steps to Perform FTA
1. **Define the Top Event**: Start by clearly defining the top event or the main failure condition that you want to prevent. This serves as the focus of the entire FTA.
2. **Develop the Fault Tree**: Using symbols and logical gates, construct the fault tree diagram. This involves breaking down the top event into more manageable causes and identifying contributing factors.
3. **Identify Basic Events**: At the lowest level of the fault tree, identify the basic events or root causes that, if occurred, would lead to the top event. These events form the basis for further analysis.
4. **Analyze the Fault Tree**: Evaluate which combinations of basic events can lead to the top event. Use qualitative and quantitative methods to determine the likelihood of failure scenarios.
5. **Implement Countermeasures**: Develop strategies and countermeasures to address the identified basic events. This can include preventive measures, design improvements, or implementing redundancies.
6. **Update and Review the Fault Tree**: Like FMEA, FTA should be a dynamic process subject to regular updates. As new data is collected or changes occur, update the fault tree to reflect the latest information.
Effective Utilization of FMEA and FTA
Successfully employing FMEA and FTA requires more than just their execution. It involves embedding these tools into an organization’s culture and processes to ensure maximum effectiveness.
Integrating FMEA and FTA into the Workflow
1. **Early Involvement**: Engage in FMEA and FTA at the early stages of system or process design. Identifying issues during the design phase prevents costly changes later in the development cycle.
2. **Continual Training and Awareness**: Train teams regularly on FMEA and FTA methodologies. Increasing awareness ensures that everyone understands their importance and responsibilities in maintaining system reliability.
3. **Use as a Communication Tool**: Leverage FMEA and FTA as communication tools between different departments. Sharing risk assessments can help align strategies and synchronize efforts to mitigate risks.
4. **Leverage Technology**: Utilize software and digital platforms to perform and manage FMEA and FTA processes efficiently. Automation can handle complex calculations, track changes, and store historical data for future reference.
Eliminating Problems with FMEA and FTA
When utilized effectively, FMEA and FTA can lead to significant improvements in system reliability and risk management.
Benefits of FMEA and FTA
1. **Proactive Problem Solving**: Both methodologies allow organizations to identify potential problems before they occur, leading to proactive rather than reactive responses.
2. **Enhanced Safety and Quality**: By systematically addressing potential failures, both tools contribute to heightened safety standards and improved product or service quality.
3. **Cost Savings**: Reducing the frequency and severity of failures can lead to substantial cost savings by avoiding downtime and minimizing rework or recalls.
4. **Increased Customer Satisfaction**: Reliable systems and products lead to higher customer satisfaction, as clients experience fewer disruptions and enhanced performance.
In conclusion, FMEA and FTA are indispensable tools in the arsenal of risk management and quality assurance. By following structured processes, regularly integrating these analyses, and fostering an organizational culture of continuous improvement, businesses can effectively identify, prioritize, and mitigate risks. This not only ensures the reliability and safety of products and processes but also builds stronger trust and satisfaction among stakeholders.
資料ダウンロード
QCD管理受発注クラウド「newji」は、受発注部門で必要なQCD管理全てを備えた、現場特化型兼クラウド型の今世紀最高の受発注管理システムとなります。
ユーザー登録
受発注業務の効率化だけでなく、システムを導入することで、コスト削減や製品・資材のステータス可視化のほか、属人化していた受発注情報の共有化による内部不正防止や統制にも役立ちます。
NEWJI DX
製造業に特化したデジタルトランスフォーメーション(DX)の実現を目指す請負開発型のコンサルティングサービスです。AI、iPaaS、および先端の技術を駆使して、製造プロセスの効率化、業務効率化、チームワーク強化、コスト削減、品質向上を実現します。このサービスは、製造業の課題を深く理解し、それに対する最適なデジタルソリューションを提供することで、企業が持続的な成長とイノベーションを達成できるようサポートします。
製造業ニュース解説
製造業、主に購買・調達部門にお勤めの方々に向けた情報を配信しております。
新任の方やベテランの方、管理職を対象とした幅広いコンテンツをご用意しております。
お問い合わせ
コストダウンが利益に直結する術だと理解していても、なかなか前に進めることができない状況。そんな時は、newjiのコストダウン自動化機能で大きく利益貢献しよう!
(β版非公開)